Understanding PCB Panel Basics
Before diving into optimization strategies, it’s essential to grasp the fundamentals of PCB panels. A PCB panel, also known as a production panel or array, is a larger board that contains multiple identical or different PCB designs. The individual PCBs are arranged on the panel in a grid-like pattern, with spaces between each design called “rails” or “gutters.” These spaces accommodate the cutting process, which separates the individual boards from the panel.
Standard PCB Panel Sizes
PCB manufacturers offer a range of standard panel sizes to choose from. Some common panel sizes include:
Panel Size (mm) | Panel Size (inches) |
---|---|
229 x 305 | 9 x 12 |
457 x 610 | 18 x 24 |
508 x 610 | 20 x 24 |
610 x 915 | 24 x 36 |
It’s important to note that not all manufacturers support every panel size, so it’s crucial to check with your chosen manufacturer for their specific offerings.
Factors Affecting Panel Utilization
Several factors can impact the efficiency of your PCB panel utilization:
- PCB Design Size: The dimensions of your individual PCB designs play a significant role in how many boards can fit on a panel.
- Panelization Layout: The arrangement of the PCB designs on the panel affects the amount of waste material between boards.
- Manufacturing Constraints: Factors such as minimum spacing requirements, tooling holes, and other manufacturing considerations can limit the available space on the panel.
By understanding these factors, you can make informed decisions when optimizing your PCB panel utilization.
Strategies for Optimizing PCB Panel Utilization
Now that we’ve covered the basics, let’s explore some effective strategies for maximizing your PCB panel utilization.
1. Choose the Right Panel Size
Selecting an appropriate panel size is the first step in optimizing utilization. Consider the following:
- PCB Design Dimensions: Evaluate the size of your individual PCB designs and choose a panel size that accommodates multiple boards efficiently.
- Quantity Requirements: Take into account the number of PCBs you need to produce and select a panel size that aligns with your production volume.
- Manufacturing Capabilities: Ensure that your chosen panel size is supported by your PCB manufacturer and compatible with their equipment and processes.
2. Optimize PCB Design Layout
The layout of your PCB designs on the panel significantly impacts utilization. Here are some tips:
- Minimize Waste: Arrange the PCB designs on the panel in a way that minimizes the space between boards, reducing waste material.
- Consider Panelization Methods: Explore different panelization techniques, such as tab routing or perforated breakaways, to optimize the layout and facilitate easy separation of individual boards.
- Rotate and Mirror: If your PCB design allows, consider rotating or mirroring the designs to achieve a more compact and efficient arrangement on the panel.
3. Utilize Nested Panelization
Nested panelization involves placing smaller PCB designs within the cutouts of larger designs, maximizing the use of available panel space. This technique is particularly useful when you have a mix of PCB sizes or need to produce smaller quantities of certain designs.
To implement nested panelization:
- Identify the larger PCB designs that will serve as the base for nesting.
- Determine the smaller PCB designs that can fit within the cutouts of the larger designs.
- Arrange the smaller designs within the available spaces, ensuring proper spacing and manufacturing constraints are met.
4. Collaborate with Your PCB Manufacturer
Engaging in open communication with your PCB manufacturer can greatly benefit panel utilization optimization. Share your requirements, design files, and any specific considerations with them early in the process. Their expertise and experience can provide valuable insights and recommendations tailored to your project.
- Discuss panel size options and their impact on cost and lead time.
- Seek advice on panelization techniques and best practices specific to their manufacturing processes.
- Request a panelization proof or mockup to visualize and approve the proposed panel layout before production.
Balancing Panel Utilization with Other Factors
While optimizing panel utilization is important, it’s crucial to strike a balance with other manufacturing considerations. Keep the following in mind:
Manufacturing Constraints
Ensure that your panel optimization efforts align with the manufacturing constraints set by your PCB manufacturer. These constraints may include:
- Minimum spacing requirements between PCB designs
- Tooling hole placement and size
- Clearance for depanelization methods
- Specific design rules for copper pours, solder mask, and silkscreen
Cost Implications
Evaluate the cost implications of your panel utilization strategies. In some cases, using a larger panel size or implementing complex panelization techniques may increase manufacturing costs. Weigh the benefits of improved utilization against any potential cost increases to make an informed decision.
Lead Time Impact
Consider how your panel utilization choices affect the manufacturing lead time. Certain panel sizes or panelization methods may require additional setup time or specialized processes, which can impact the overall production schedule. Discuss lead time implications with your manufacturer and prioritize accordingly.
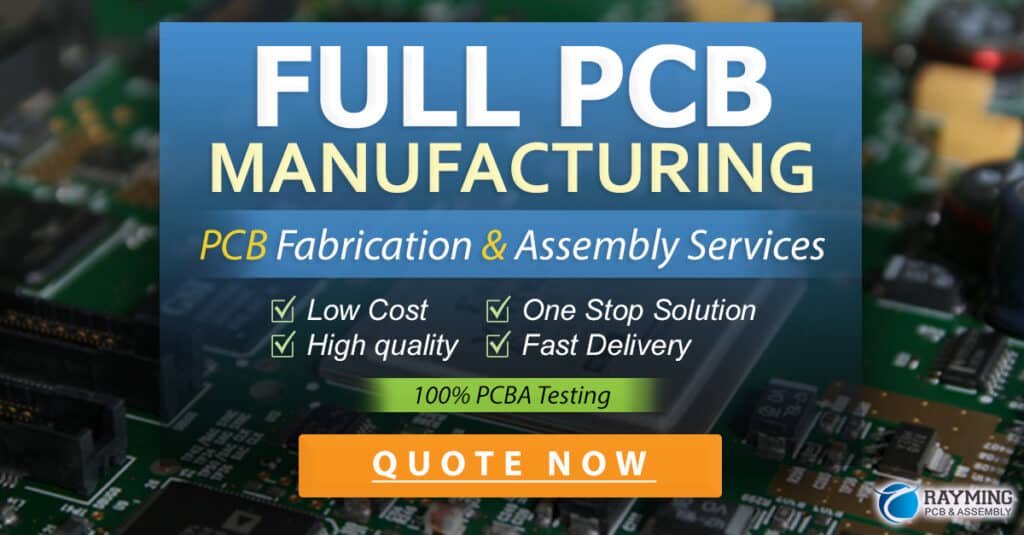
PCB Panel Utilization FAQs
-
Q: What is the minimum spacing required between PCB designs on a panel?
A: The minimum spacing requirements vary depending on the manufacturer and the specific manufacturing processes used. Typically, a minimum spacing of 2-3 mm is recommended, but it’s best to consult your PCB manufacturer for their specific guidelines. -
Q: Can I mix different PCB designs on the same panel?
A: Yes, it is possible to include different PCB designs on the same panel, known as a mixed panel or multi-design panel. This can be useful for producing smaller quantities of various designs simultaneously. However, keep in mind that mixed panels may require additional setup time and coordination with your manufacturer. -
Q: How does the choice of depanelization method affect panel utilization?
A: The depanelization method, such as tab routing or perforated breakaways, can impact the amount of space required between PCB designs on the panel. Some methods may require larger spacing or specific design considerations. Discuss the most suitable depanelization method with your manufacturer based on your project requirements and panel utilization goals. -
Q: Can optimal panel utilization lead to cost savings?
A: Yes, optimizing panel utilization can result in cost savings by reducing waste material, increasing production efficiency, and potentially allowing for higher manufacturing volumes per panel. However, it’s essential to consider the balance between panel utilization and other factors like manufacturing constraints and lead time impact. -
Q: How can I ensure my PCB design is compatible with efficient panel utilization?
A: To ensure your PCB design is compatible with efficient panel utilization, follow these guidelines: - Keep your PCB design dimensions consistent and within standard sizes when possible.
- Minimize irregularly shaped or non-rectangular designs that can lead to wasted panel space.
- Adhere to the manufacturer’s design rules and constraints regarding spacing, copper pours, and other aspects.
- Engage with your PCB manufacturer early in the design process to get their input on optimizing your design for panel utilization.
Conclusion
Optimizing PCB panel utilization is a critical aspect of efficient and cost-effective PCB manufacturing. By understanding the basics of PCB panels, implementing smart design strategies, collaborating with your manufacturer, and balancing utilization with other manufacturing factors, you can significantly improve your panel utilization and streamline your PCB production process.
Remember to consider factors such as panel size selection, PCB design layout optimization, nested panelization, and manufacturing constraints when developing your panel utilization strategy. Open communication with your PCB manufacturer is key to ensuring your approach aligns with their capabilities and leads to the best possible results.
By following the guidelines and best practices outlined in this article, you can unlock the benefits of optimal PCB panel utilization, including reduced waste, increased efficiency, and potential cost savings. Stay proactive in your approach, continually assess and refine your strategies, and leverage the expertise of your manufacturing partners to achieve success in your PCB projects.
No responses yet