What is PCB Milling?
PCB milling is a subtractive manufacturing process that involves using a computer-controlled milling machine to remove copper from a blank PCB board. The milling machine uses a rotating cutting tool, called an end mill, to remove the unwanted copper, leaving behind the desired circuit pattern. This process is similar to CNC machining, where a computer-controlled machine is used to cut and shape materials based on a digital design.
PCB milling offers several advantages over traditional PCB fabrication methods, such as:
- Rapid prototyping: PCB milling allows for quick and easy creation of prototype PCBs, enabling faster iteration and testing of designs.
- Cost-effective for small batches: For small-scale production or one-off projects, PCB milling is more cost-effective than traditional PCB fabrication methods.
- Customization: PCB milling enables the creation of custom PCB designs with unique shapes, sizes, and features.
Equipment Needed for PCB Milling
To get started with PCB milling, you will need the following equipment:
-
PCB Milling Machine: A computer-controlled milling machine specifically designed for creating PCBs. Some popular options include the Bantam Tools Desktop PCB Milling Machine and the Prometheus PCB Milling Machine.
-
Blank PCB Boards: Copper-clad boards that serve as the base material for your PCBs. These boards are available in various sizes and materials, such as FR-4 and Rogers.
-
End Mills: Cutting tools used by the milling machine to remove copper from the PCB board. End mills come in different sizes and shapes, depending on the desired trace width and depth.
-
Computer with CAD/CAM Software: A computer equipped with CAD (Computer-Aided Design) and CAM (Computer-Aided Manufacturing) software is necessary to design the PCB layout and generate the toolpaths for the milling machine.
-
Safety Equipment: Protective gear such as safety glasses, gloves, and a dust mask to ensure your safety during the milling process.
Step-by-Step Guide to PCB Milling
Step 1: Design your PCB Layout
Using CAD software, design your PCB layout according to your circuit requirements. Some popular CAD software options for PCB design include KiCad, Eagle, and Altium Designer. When designing your PCB, consider factors such as component placement, trace width, and clearance between traces.
Step 2: Generate Toolpaths
Once your PCB layout is complete, use CAM software to generate the toolpaths for the milling machine. The CAM software will convert your PCB design into a set of instructions that the milling machine can follow to remove the unwanted copper. Some CAD software, like KiCad, have built-in CAM functionality, while others may require separate CAM software.
Step 3: Prepare the PCB Milling Machine
Set up your PCB milling machine according to the manufacturer’s instructions. This may involve installing the appropriate end mill, adjusting the spindle speed, and setting the origin point for the milling process.
Step 4: Secure the Blank PCB Board
Place the blank PCB board on the milling machine’s bed and secure it in place. Ensure that the board is firmly held down to prevent any movement during the milling process.
Step 5: Run the Milling Process
Load the generated toolpaths into the milling machine’s control software and start the milling process. The machine will follow the toolpaths, removing copper from the PCB board to create the desired circuit pattern. Monitor the process closely to ensure that the machine is operating correctly and there are no issues, such as broken end mills or excessive vibration.
Step 6: Clean and Inspect the PCB
Once the milling process is complete, remove the PCB from the machine and clean it using a brush or compressed air to remove any debris. Inspect the PCB closely to ensure that all traces are properly milled and there are no shorts or open circuits. If necessary, use a multimeter to test the continuity of the traces.
Step 7: Drill Holes and Add Components
If your PCB requires through-hole components, use a drill or the milling machine to create the necessary holes. Once the holes are drilled, you can add your components and solder them in place.
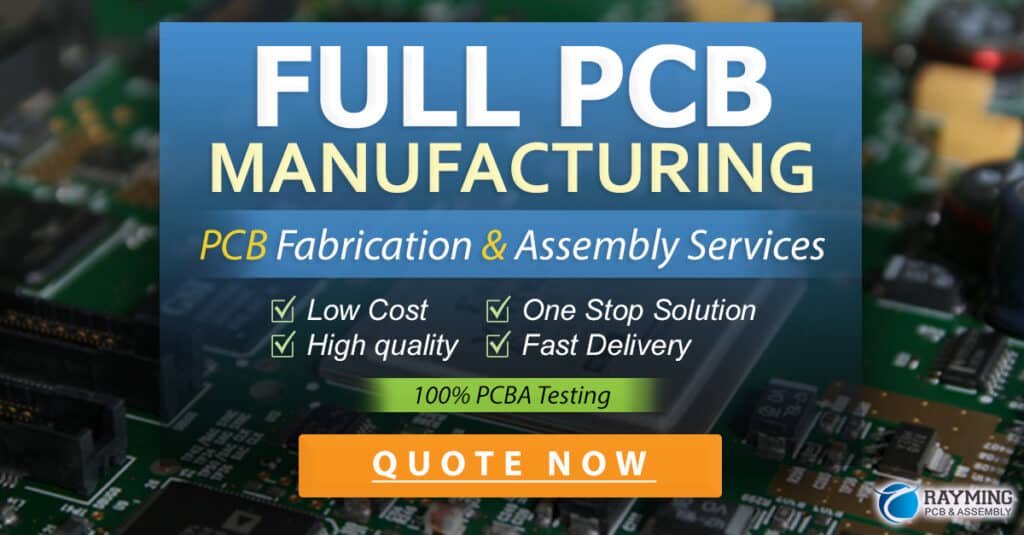
Troubleshooting Common Issues
-
Broken End Mills: If an end mill breaks during the milling process, stop the machine immediately and replace the end mill. Ensure that the new end mill is properly installed and the milling process can resume from where it left off.
-
Inaccurate Milling: If the milled PCB does not match your design, double-check your CAD and CAM files for any errors. Ensure that the milling machine is properly calibrated and the origin point is set correctly.
-
Overheating: If the end mill or the PCB board becomes excessively hot during the milling process, reduce the spindle speed or the feed rate. Overheating can lead to damaged end mills or melted PCB material.
Frequently Asked Questions (FAQ)
- What is the minimum trace width that can be achieved with PCB milling?
-
The minimum trace width depends on the size of the end mill used. Typically, PCB milling machines can achieve trace widths as small as 0.1mm (4 mil) with the appropriate end mill.
-
Can PCB milling be used for multi-layer PCBs?
-
Yes, PCB milling can be used to create multi-layer PCBs. However, the process is more complex and requires precise alignment of the layers during the milling process.
-
How long does it take to mill a PCB?
-
The milling time depends on the complexity of the PCB design and the size of the board. Simple designs can be milled in a matter of minutes, while more complex designs may take several hours.
-
What is the cost of setting up a PCB milling machine?
-
The cost of a PCB milling machine varies depending on the model and features. Entry-level machines can cost around $1,000, while high-end machines can cost upwards of $10,000.
-
Can PCB milling be used for high-volume production?
- PCB milling is generally not suitable for high-volume production due to the slower speed compared to traditional PCB fabrication methods. It is best suited for prototyping and small-scale production.
Advantage | PCB Milling | Traditional PCB Fabrication |
---|---|---|
Rapid Prototyping | Yes | No |
Cost-effective for Small Batches | Yes | No |
Customization | High | Low |
High-volume Production | No | Yes |
Minimum Trace Width | 0.1mm (4 mil) | 0.075mm (3 mil) |
In conclusion, PCB milling is a versatile and cost-effective method for creating custom PCBs, especially for prototyping and small-scale production. With the right equipment and a step-by-step approach, anyone can learn to mill their own PCBs and bring their electronic projects to life.
No responses yet