The History of PCBs
The concept of printed circuits dates back to the early 20th century, with the first patent for a printed wire circuit granted to Albert Hanson in 1903. However, it wasn’t until the 1930s that the technology began to gain traction. In 1936, Paul Eisler, an Austrian engineer, developed the first practical printed circuit board for a radio set.
During World War II, the United States military recognized the potential of PCBs and used them extensively in radio and radar equipment. This adoption accelerated the development and refinement of PCB technology. In the post-war era, PCBs became increasingly popular in consumer electronics, with the introduction of the first transistorized computer in 1956 and the first PCB-based calculator in 1961.
As electronic devices became more complex and compact, the demand for high-density, multi-layer PCBs grew. In the 1980s, surface-mount technology (SMT) emerged, allowing smaller components to be mounted directly onto the surface of the PCB, further increasing circuit density and reducing the size of electronic devices.
How PCBs are Manufactured
The PCB manufacturing process involves several steps, each requiring precision and adherence to strict quality control standards. The basic steps in PCB fabrication include:
-
Design: The PCB layout is designed using specialized software, such as Altium Designer or Eagle CAD. The design includes the placement of components, routing of traces, and creation of solder masks and silkscreen layers.
-
Printing: The designed circuit pattern is printed onto a transparent film or photomask, which will be used to transfer the pattern onto the copper-clad board.
-
Etching: The copper-clad board is coated with a light-sensitive photoresist. The photomask is then placed on top of the photoresist, and the board is exposed to ultraviolet light. The exposed photoresist hardens, while the unexposed areas remain soluble. The board is then placed in a chemical bath that removes the soluble photoresist and etches away the unwanted copper, leaving behind the desired circuit pattern.
-
Drilling: Holes are drilled into the board to accommodate through-hole components and provide connections between layers in multi-layer PCBs.
-
Plating: The drilled holes are plated with copper to ensure electrical continuity between layers.
-
Solder Mask and Silkscreen: A solder mask, typically green in color, is applied to the board to protect the copper traces from oxidation and prevent solder bridges. A silkscreen layer is then added to provide labels, logos, and other identifying marks on the board.
-
Surface Finish: A surface finish, such as HASL (Hot Air Solder Leveling), ENIG (Electroless Nickel Immersion Gold), or OSP (Organic Solderability Preservative), is applied to the exposed copper to prevent oxidation and enhance solderability.
-
Quality Control: The finished PCB undergoes a series of quality control tests, including visual inspection, electrical continuity testing, and functional testing, to ensure that it meets the required specifications.
Types of PCBs
PCBs can be classified based on various criteria, such as the number of layers, the type of substrate material, or the component mounting method. Some common types of PCBs include:
Single-Layer PCBs
Single-layer PCBs have conductive traces on only one side of the substrate. They are the simplest and most cost-effective type of PCB, suitable for low-complexity circuits and prototyping.
Double-Layer PCBs
Double-layer PCBs have conductive traces on both sides of the substrate, allowing for higher component density and more complex circuits compared to single-layer boards. The two layers are connected through plated through-holes (PTHs).
Multi-Layer PCBs
Multi-layer PCBs consist of three or more layers of conductive traces, separated by insulating layers. They offer the highest component density and are used in complex, high-performance electronic devices, such as smartphones, computers, and aerospace systems. Multi-layer PCBs can have up to 50 layers or more in some advanced applications.
Number of Layers | Typical Applications |
---|---|
1-2 | Simple circuits, prototypes, low-cost consumer electronics |
4-8 | Complex digital circuits, telecommunications equipment, automotive electronics |
10-12 | High-speed digital circuits, advanced telecommunications equipment, military and aerospace systems |
14+ | Highly complex, high-performance systems, such as supercomputers, satellites, and advanced medical equipment |
Rigid PCBs
Rigid PCBs are made from a solid, inflexible substrate material, typically fiberglass-reinforced epoxy resin (FR-4). They are the most common type of PCB and are used in a wide range of electronic devices.
Flexible PCBs
Flexible PCBs, or flex circuits, are made from a thin, flexible plastic substrate, such as polyimide or polyester. They can bend and twist without damaging the conductive traces, making them ideal for applications where space is limited, or the circuit needs to conform to a specific shape, such as in wearable electronics or automotive applications.
Rigid-Flex PCBs
Rigid-flex PCBs combine the benefits of both rigid and flexible PCBs. They consist of rigid PCB sections connected by flexible PCB sections, allowing for three-dimensional circuit designs and improved reliability in applications that require both stability and flexibility, such as aerospace and military equipment.
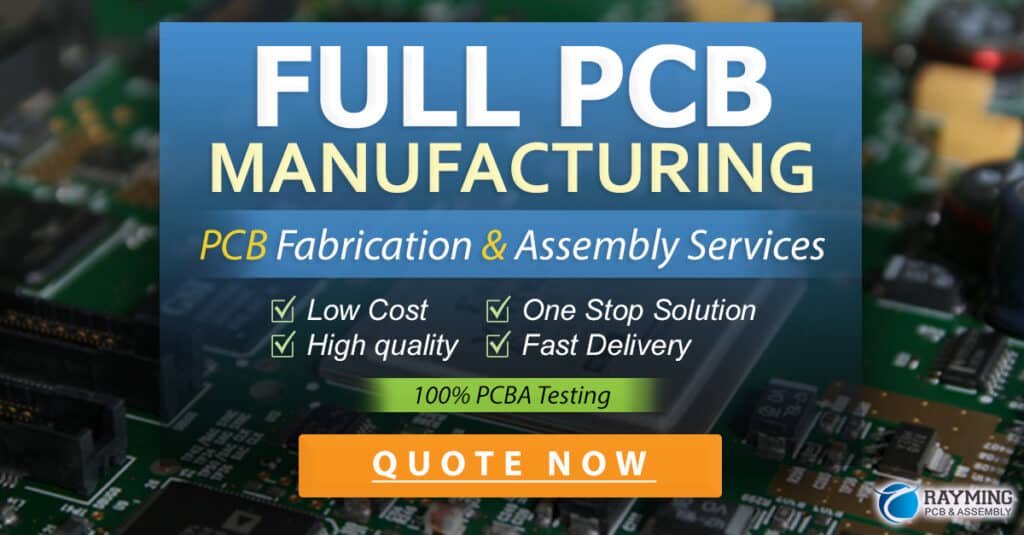
PCB Design Considerations
Designing a PCB involves several key considerations to ensure optimal performance, reliability, and manufacturability. Some of these considerations include:
Component Placement
Components should be placed strategically on the PCB to minimize signal interference, reduce trace lengths, and facilitate efficient routing. Components should also be grouped based on their function and placed in a way that promotes easy assembly and maintenance.
Trace Routing
Traces should be routed to minimize signal reflections, crosstalk, and electromagnetic interference (EMI). This involves using appropriate trace widths, spacing, and angles, as well as implementing techniques such as ground planes and shielding.
Power Distribution
A well-designed power distribution network is crucial for ensuring stable and clean power delivery to all components on the PCB. This involves using appropriate trace widths, placing decoupling capacitors close to power-hungry components, and implementing proper grounding techniques.
Signal Integrity
Signal integrity refers to the quality of the electrical signals transmitted through the PCB. To maintain signal integrity, designers must consider factors such as impedance matching, termination, and the use of differential pairs for high-speed signals.
Thermal Management
Proper thermal management is essential for preventing component overheating and ensuring long-term reliability. This involves using appropriate trace widths for high-current paths, providing adequate copper coverage for heat dissipation, and incorporating thermal relief pads for components with high heat generation.
Manufacturing Constraints
PCB designers must also consider the limitations and capabilities of the manufacturing process. This includes adhering to minimum trace widths and spacings, hole sizes, and annular ring requirements, as well as ensuring proper clearances for solder masks and silkscreen layers.
PCB Testing and Inspection
To ensure the quality and reliability of PCBs, several testing and inspection methods are employed during and after the manufacturing process. Some common methods include:
Visual Inspection
Visual inspection is the first line of defense in identifying defects such as poor soldering, component misalignment, or damage to the PCB. This can be done manually or using automated optical inspection (AOI) systems.
Automated Optical Inspection (AOI)
AOI systems use high-resolution cameras and advanced image processing algorithms to detect surface-level defects, such as missing or misaligned components, solder bridges, or incorrect component polarity.
X-Ray Inspection
X-ray inspection is used to detect defects that are not visible on the surface, such as voids in solder joints, broken traces, or internal delamination. This is particularly useful for inspecting multi-layer PCBs and ball grid array (BGA) components.
In-Circuit Testing (ICT)
ICT involves using a bed-of-nails fixture to make electrical contact with specific points on the PCB and test the functionality of individual components and circuits. This helps identify defects such as open or short circuits, incorrect component values, or faulty components.
Functional Testing
Functional testing involves powering up the PCB and testing its overall functionality and performance. This can include testing various input and output signals, measuring power consumption, and verifying the PCB’s compliance with the design specifications.
Applications of PCBs
PCBs are used in virtually every electronic device, from simple consumer gadgets to complex industrial and military systems. Some common applications include:
- Consumer electronics: Smartphones, tablets, laptops, televisions, gaming consoles, and wearable devices.
- Automotive electronics: Engine control units, infotainment systems, driver assistance systems, and electric vehicle power management.
- Industrial automation: Programmable logic controllers (PLCs), sensors, actuators, and human-machine interfaces (HMIs).
- Medical devices: Diagnostic equipment, patient monitoring systems, implantable devices, and prosthetics.
- Aerospace and defense: Avionics, communication systems, radar, and satellite electronics.
- Internet of Things (IoT): Smart home devices, industrial IoT sensors, and connected wearables.
As technology continues to advance, the demand for high-performance, compact, and reliable PCBs will only continue to grow, driving innovation in PCB design and manufacturing processes.
Frequently Asked Questions (FAQ)
1. What is the difference between a PCB and a PCBA?
A PCB is the bare board with the etched conductive traces, while a PCBA (Printed Circuit Board Assembly) is a PCB populated with electronic components, ready to be used in an electronic device.
2. What materials are PCBs typically made from?
The most common substrate material for rigid PCBs is FR-4, a fiberglass-reinforced epoxy resin. Flexible PCBs are typically made from polyimide or polyester materials.
3. How small can the traces on a PCB be?
The minimum trace width depends on the PCB manufacturer’s capabilities and the specific application. In general, modern PCB manufacturing processes can produce trace widths as small as 3-4 mils (0.003-0.004 inches or 0.0762-0.1016 mm).
4. Can PCBs be recycled?
Yes, PCBs can be recycled to recover valuable materials, such as copper, gold, and palladium. However, the recycling process is complex and requires specialized facilities to ensure proper handling of the hazardous materials found in some PCBs.
5. How long do PCBs typically last?
The lifespan of a PCB depends on various factors, such as the quality of the materials, the manufacturing process, and the operating environment. In general, a well-designed and manufactured PCB can last for several decades under normal use conditions. However, PCBs in harsh environments or those subjected to frequent thermal cycling may have shorter lifespans.
In conclusion, PCBs are the backbone of modern electronics, providing a compact, reliable, and efficient means of assembling electronic circuits. Understanding the PCB Meaning, its manufacturing process, design considerations, and testing methods is essential for anyone involved in the development or production of electronic devices. As technology continues to evolve, PCBs will remain a crucial component in driving innovation across a wide range of industries.
No responses yet