Introduction to PCB Material Selection
Printed Circuit Board (PCB) material selection is a critical aspect of designing high-frequency circuits for RF, microwave, and millimeter-wave applications. The choice of PCB material directly impacts the electrical performance, signal integrity, and manufacturability of the final product. With the increasing demand for higher bandwidth, lower latency, and miniaturization in modern communication systems, it is essential to understand the key factors that influence PCB material selection and their effects on circuit performance.
In this article, we will delve into the world of PCB materials, exploring their properties, characteristics, and suitability for various high-frequency applications. We will discuss the challenges faced by designers and provide insights into making informed decisions when selecting PCB materials for RF, microwave, and millimeter-wave designs.
Factors Affecting PCB Material Selection
Several factors come into play when selecting PCB materials for high-frequency applications. These factors can be broadly categorized into electrical, mechanical, and environmental considerations. Let’s examine each of these factors in detail.
Electrical Properties
The electrical properties of PCB materials are of utmost importance in high-frequency designs. The key electrical properties to consider include:
-
Dielectric Constant (Dk): The dielectric constant, also known as relative permittivity, is a measure of a material’s ability to store electrical energy. It determines the speed at which signals propagate through the material. A lower dielectric constant is generally preferred for high-frequency applications to minimize signal delay and reduce the wavelength of the signal.
-
Dissipation Factor (Df): The dissipation factor, or loss tangent, represents the amount of energy lost as heat when an alternating electric field is applied to the material. A lower dissipation factor is desirable to minimize signal loss and maintain signal integrity. Materials with low dissipation factors are particularly important for applications that require low insertion loss and high Q-factors.
-
Dielectric Thickness and Uniformity: The thickness and uniformity of the dielectric material affect the characteristic impedance and signal propagation. Consistent dielectric thickness is crucial for maintaining controlled impedance and reducing signal reflections. Variations in thickness can lead to impedance mismatches and signal degradation.
-
Copper Foil Roughness: The surface roughness of the copper foil used in PCBs impacts the high-frequency performance. Rough copper surfaces can increase conductor losses and affect signal integrity. Smooth copper foils, such as rolled or electrodeposited copper, are preferred for high-frequency applications to minimize skin effect losses.
Mechanical Properties
The mechanical properties of PCB materials play a vital role in the manufacturing process and the overall reliability of the final product. Some key mechanical properties to consider include:
-
Coefficient of Thermal Expansion (CTE): The CTE describes how much a material expands or contracts with changes in temperature. A mismatch in CTE between the PCB material and components can lead to mechanical stress, warpage, and reliability issues. It is important to select materials with CTEs that closely match the components and minimize thermal stresses.
-
Glass Transition Temperature (Tg): The glass transition temperature is the point at which a material transitions from a rigid, glassy state to a softer, rubbery state. It is crucial to choose materials with a high Tg to ensure the PCB remains stable and maintains its mechanical integrity during manufacturing processes, such as soldering, and throughout its operating life.
-
Mechanical Strength and Stiffness: The mechanical strength and stiffness of the PCB material affect its ability to withstand handling, vibration, and mechanical shocks. Materials with high strength and stiffness are preferred for applications that require robustness and long-term reliability.
Environmental Factors
Environmental factors play a significant role in the performance and reliability of PCBs in high-frequency applications. Some key environmental factors to consider include:
-
Operating Temperature Range: The operating temperature range of the PCB material should be compatible with the intended application. Materials with a wide temperature range are preferred for applications that experience extreme temperatures, such as aerospace and automotive systems.
-
Moisture Absorption: Moisture absorption can significantly impact the electrical properties of PCB materials, especially at high frequencies. Materials with low moisture absorption, such as hydrocarbon ceramics and PTFE-based laminates, are preferred for applications exposed to humid environments.
-
Outgassing: Outgassing refers to the release of gases from the PCB material when exposed to heat or vacuum. It can lead to contamination and affect the performance of sensitive components. Low-outgassing materials are essential for space and vacuum applications.
Common PCB Materials for High-Frequency Applications
There are several PCB materials commonly used in high-frequency applications. Each material has its own set of characteristics and trade-offs. Let’s explore some of the most popular PCB materials:
PTFE (Polytetrafluoroethylene)
PTFE, also known as Teflon, is a popular choice for high-frequency PCBs due to its excellent electrical properties. It offers a low dielectric constant (Dk) and a low dissipation factor (Df), making it suitable for applications that require low loss and high signal integrity. PTFE-based laminates, such as Rogers RT/duroid® and Taconic TLY, are widely used in RF and microwave designs.
Advantages:
– Low dielectric constant (Dk)
– Low dissipation factor (Df)
– Wide operating temperature range
– Low moisture absorption
Disadvantages:
– Higher cost compared to other materials
– Challenging to process and fabricate
– Lower mechanical strength and stiffness
Ceramic-Filled PTFE
Ceramic-filled PTFE laminates, such as Rogers RO3000® and Taconic RF-35, combine the advantages of PTFE with the improved mechanical properties of ceramic fillers. These materials offer a good balance between electrical performance and mechanical stability.
Advantages:
– Improved mechanical strength and stiffness compared to pure PTFE
– Good thermal conductivity
– Suitable for high-frequency applications
Disadvantages:
– Higher dielectric constant compared to pure PTFE
– Increased dissipation factor compared to pure PTFE
– Higher cost compared to FR-4
Hydrocarbon Ceramics
Hydrocarbon ceramic laminates, such as Rogers RO4000® and Taconic CER-10, are engineered for high-frequency applications that require low loss and stable performance over a wide temperature range. These materials offer a combination of low dielectric constant, low dissipation factor, and good mechanical properties.
Advantages:
– Low dielectric constant (Dk)
– Low dissipation factor (Df)
– Stable electrical properties over a wide temperature range
– Good mechanical strength and stiffness
Disadvantages:
– Higher cost compared to FR-4
– Requires specialized processing techniques
Low-Loss FR-4
Low-loss FR-4 laminates, such as Isola IS400 and Panasonic Megtron, are designed to provide improved electrical performance compared to standard FR-4 while maintaining the cost-effectiveness and ease of processing. These materials are suitable for applications that require a balance between performance and cost.
Advantages:
– Lower cost compared to PTFE and ceramic-filled materials
– Easier to process and fabricate compared to PTFE
– Improved electrical properties compared to standard FR-4
Disadvantages:
– Higher dielectric constant and dissipation factor compared to PTFE and ceramic-filled materials
– Limited operating temperature range compared to PTFE and ceramic-filled materials
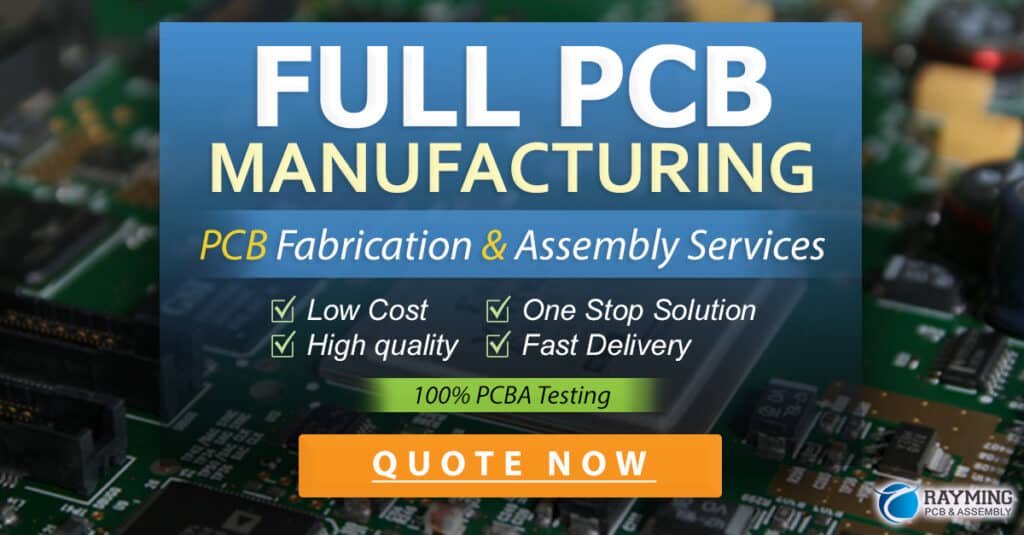
PCB Material Selection Guidelines
When selecting PCB materials for high-frequency applications, consider the following guidelines:
-
Prioritize Electrical Performance: Give priority to the electrical properties that are critical for your application. Consider the required dielectric constant, dissipation factor, and dielectric thickness to meet your design goals.
-
Consider Mechanical and Environmental Factors: Evaluate the mechanical and environmental requirements of your application. Consider the operating temperature range, moisture exposure, and mechanical stresses that the PCB will encounter.
-
Balance Cost and Performance: Weigh the cost of the PCB material against the required performance. Higher-performance materials often come with a higher price tag. Determine the appropriate balance between cost and performance for your specific application.
-
Consult with PCB Manufacturers: Engage with PCB manufacturers early in the design process. They can provide valuable insights into material availability, manufacturing capabilities, and cost considerations.
-
Conduct Simulations and Prototyping: Perform simulations and prototyping to validate the performance of the selected PCB material. This helps identify potential issues and optimize the design before moving to full-scale production.
Frequently Asked Questions (FAQs)
- What is the difference between Dk and Df in PCB materials?
-
Dk (Dielectric Constant) represents a material’s ability to store electrical energy, while Df (Dissipation Factor) represents the amount of energy lost as heat when an alternating electric field is applied. A lower Dk is preferred for high-speed signal propagation, and a lower Df is desired for minimizing signal loss.
-
Why is the glass transition temperature (Tg) important for PCB materials?
-
The glass transition temperature (Tg) is the point at which a material transitions from a rigid, glassy state to a softer, rubbery state. A high Tg ensures that the PCB remains stable and maintains its mechanical integrity during manufacturing processes and throughout its operating life.
-
What are the advantages of using PTFE-based materials for high-frequency PCBs?
-
PTFE-based materials offer low dielectric constant (Dk) and low dissipation factor (Df), making them suitable for applications that require low loss and high signal integrity. They also have a wide operating temperature range and low moisture absorption.
-
How does the copper foil roughness affect high-frequency performance?
-
Rough copper surfaces can increase conductor losses and affect signal integrity at high frequencies. Smooth copper foils, such as rolled or electrodeposited copper, are preferred to minimize skin effect losses and maintain signal integrity.
-
What factors should I consider when balancing cost and performance in PCB material selection?
- When balancing cost and performance, consider the specific requirements of your application. Determine the minimum acceptable performance criteria and evaluate the cost implications of different PCB materials. Engage with PCB manufacturers to understand material availability, manufacturing capabilities, and cost trade-offs.
Conclusion
PCB material selection is a critical aspect of designing high-frequency circuits for RF, microwave, and millimeter-wave applications. Understanding the electrical, mechanical, and environmental properties of PCB materials is essential for making informed decisions that optimize performance, reliability, and cost.
By considering factors such as dielectric constant, dissipation factor, glass transition temperature, and copper foil roughness, designers can select the most suitable PCB material for their specific application. PTFE, ceramic-filled PTFE, hydrocarbon ceramics, and low-loss FR-4 are among the commonly used materials for high-frequency PCBs, each offering its own set of advantages and trade-offs.
Engaging with PCB manufacturers, conducting simulations, and prototyping are important steps in validating the performance of the selected PCB material and optimizing the design. By following the guidelines and considering the FAQs discussed in this article, designers can navigate the complexities of PCB material selection and create high-performance, reliable, and cost-effective solutions for RF, microwave, and millimeter-wave applications.
PCB Material | Dielectric Constant (Dk) | Dissipation Factor (Df) | Key Characteristics |
---|---|---|---|
PTFE (Teflon) | 2.1 – 2.5 | 0.0002 – 0.0010 | Low Dk, low Df, wide temperature range, low moisture absorption |
Ceramic-Filled PTFE | 2.5 – 3.5 | 0.0010 – 0.0030 | Improved mechanical strength, good thermal conductivity |
Hydrocarbon Ceramics | 3.2 – 3.7 | 0.0020 – 0.0040 | Low Dk, low Df, stable over wide temperature range |
Low-Loss FR-4 | 3.8 – 4.2 | 0.0100 – 0.0200 | Lower cost, easier processing, improved electrical properties compared to standard FR-4 |
Table: Comparison of common PCB materials for high-frequency applications
As the demand for higher bandwidth, lower latency, and miniaturization continues to grow in the world of RF, microwave, and millimeter-wave technology, the importance of proper PCB material selection cannot be overstated. By carefully considering the electrical, mechanical, and environmental factors, and leveraging the expertise of PCB manufacturers, designers can create high-performance, reliable, and cost-effective solutions that push the boundaries of what is possible in high-frequency electronics.
No responses yet