Introduction to PCB Manufacturing
Printed Circuit Board (PCB) manufacturing is a crucial process in the electronics industry. PCBs are the backbone of most electronic devices, providing a platform for components to be mounted and interconnected. PCB manufacturing involves various steps, from design to fabrication, to ensure that the final product meets the required specifications and functions as intended.
In this article, we will dive deep into the world of PCB manufacturing, exploring the various aspects of the process, including design, materials, fabrication techniques, and quality control. We will also discuss the importance of choosing the right PCB manufacturing service provider and the factors to consider when making that decision.
The PCB Manufacturing Process
PCB Design
The first step in PCB manufacturing is the design phase. This involves creating a schematic diagram and a layout of the PCB using specialized software. The schematic diagram represents the electrical connections between components, while the layout shows the physical placement of those components on the board.
During the design phase, several factors must be considered, such as:
- Component selection and placement
- Signal integrity and power distribution
- Electromagnetic compatibility (EMC)
- Thermal management
- Manufacturability and testability
Once the design is finalized, it is sent to the PCB manufacturer for fabrication.
PCB Materials
PCBs are typically made from a composite material consisting of a non-conductive substrate, such as FR-4, and a conductive layer, usually copper. The choice of materials depends on the specific requirements of the application, such as:
- Electrical properties (dielectric constant, loss tangent)
- Thermal properties (glass transition temperature, thermal conductivity)
- Mechanical properties (tensile strength, flexural strength)
- Environmental resistance (moisture absorption, chemical resistance)
Other materials used in PCB manufacturing include solder mask, silkscreen, and surface finishes, which serve to protect the copper traces, provide insulation, and enhance solderability.
PCB Fabrication Techniques
There are several techniques used in PCB fabrication, depending on the complexity and requirements of the design. The most common techniques include:
-
Subtractive Process: This involves starting with a copper-clad substrate and selectively removing (etching) unwanted copper to create the desired circuit pattern.
-
Additive Process: This involves depositing copper onto a non-conductive substrate to create the desired circuit pattern. This technique is often used for high-density interconnect (HDI) PCBs.
-
Semi-Additive Process: This is a combination of the subtractive and additive processes, where a thin layer of copper is deposited onto the substrate, followed by selective etching to create the circuit pattern.
-
PCB Lamination: This involves bonding multiple layers of PCB material together using heat and pressure to create a multi-layer PCB.
Quality Control
Quality control is an essential aspect of PCB manufacturing, as it ensures that the final product meets the required specifications and functions as intended. Quality control measures are implemented at various stages of the manufacturing process, including:
- Incoming material inspection
- In-process inspection
- Electrical testing
- Visual inspection
- Functional testing
Automated optical inspection (AOI) and X-ray inspection are also used to detect defects such as shorts, opens, and missing components.
Choosing a PCB Manufacturing Service Provider
Choosing the right PCB manufacturing service provider is crucial to ensuring the success of your project. Here are some factors to consider when making that decision:
Technical Capabilities
Ensure that the PCB manufacturer has the technical capabilities to meet your specific requirements, such as:
- Board size and thickness
- Layer count
- Material selection
- Surface finish options
- Hole sizes and tolerances
Quality Management System
Look for a PCB manufacturer that has a robust quality management system in place, such as ISO 9001 certification. This ensures that the manufacturer adheres to strict quality control standards and continuously improves their processes.
Lead Time and Pricing
Consider the lead time and pricing offered by the PCB manufacturer. While it may be tempting to choose the lowest-priced option, keep in mind that quality and reliability should not be compromised.
Customer Support and Communication
Choose a PCB manufacturer that provides excellent customer support and communication. This includes responsive and knowledgeable sales and technical support teams, as well as regular updates on the status of your project.
Experience and Reputation
Research the PCB manufacturer’s experience and reputation in the industry. Look for customer testimonials, case studies, and industry certifications to gauge their expertise and track record.
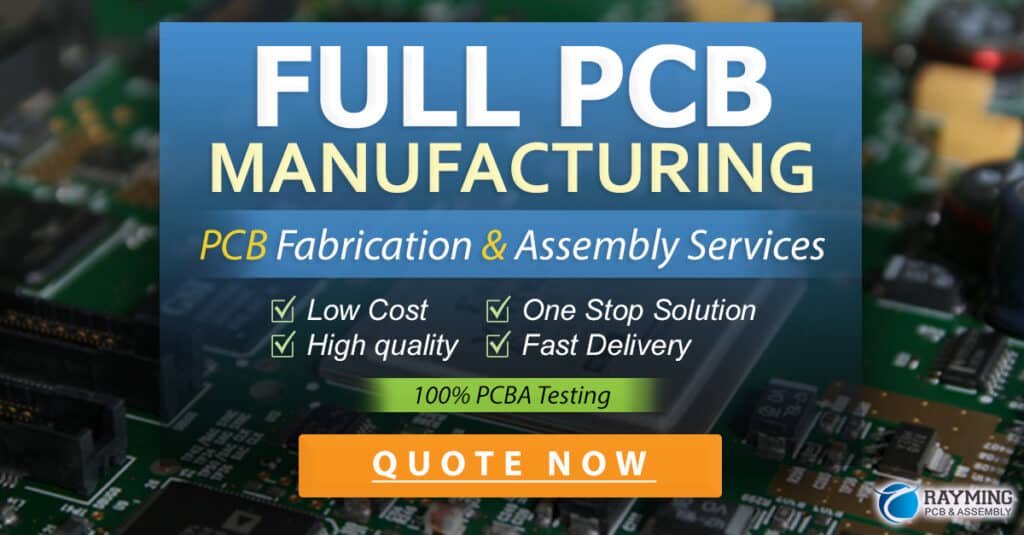
Advantages of Using a PCB Manufacturing Service
Using a PCB manufacturing service offers several advantages over in-house PCB fabrication, including:
-
Access to Specialized Equipment: PCB manufacturers have access to specialized equipment and technologies that may not be feasible for in-house fabrication, such as high-speed drilling machines, laser direct imaging (LDI), and automated inspection systems.
-
Cost Savings: Outsourcing PCB manufacturing can be more cost-effective than setting up and maintaining an in-house fabrication facility, especially for low-volume production runs.
-
Faster Turnaround Times: PCB manufacturers have streamlined processes and dedicated resources to ensure faster turnaround times compared to in-house fabrication.
-
Expertise and Experience: PCB manufacturers have a wealth of expertise and experience in PCB design and fabrication, which can help optimize your design for manufacturability and reliability.
-
Scalability: PCB manufacturers can easily scale up production to meet increasing demand, without the need for additional capital investment in equipment and personnel.
Future Trends in PCB Manufacturing
The PCB manufacturing industry is constantly evolving, driven by advances in technology and changing market demands. Here are some future trends to watch out for:
Miniaturization and High-Density Interconnect (HDI)
The trend towards miniaturization and increased functionality in electronic devices is driving the demand for HDI PCBs. HDI PCBs feature smaller trace widths, via sizes, and pad sizes, allowing for higher component density and improved signal integrity.
Flexible and Rigid-Flex PCBs
Flexible and rigid-flex PCBs are gaining popularity in applications that require flexibility, such as wearable devices and automotive electronics. These PCBs consist of flexible substrates that can be bent or folded to fit into tight spaces or conform to irregular shapes.
Embedded Components
Embedded components, such as resistors, capacitors, and inductors, are increasingly being integrated into the PCB substrate itself, rather than being mounted on the surface. This allows for smaller board sizes, improved signal integrity, and reduced assembly costs.
Green and Sustainable Manufacturing
There is a growing emphasis on green and sustainable manufacturing practices in the PCB industry, driven by environmental regulations and consumer demand. This includes the use of lead-free and halogen-free materials, as well as the adoption of energy-efficient and waste-reducing processes.
Frequently Asked Questions (FAQ)
-
What is the typical turnaround time for PCB manufacturing?
The turnaround time for PCB manufacturing depends on various factors, such as the complexity of the design, the board size and layer count, and the manufacturing process used. Typical turnaround times range from 2-3 days for simple designs to 2-3 weeks for complex, multi-layer boards. -
What is the minimum order quantity (MOQ) for PCB manufacturing?
The minimum order quantity (MOQ) for PCB manufacturing varies among manufacturers. Some manufacturers offer low MOQs of 5-10 pieces for prototype runs, while others may require a minimum of 100 pieces or more for production runs. -
What file formats are required for PCB manufacturing?
The most common file formats required for PCB manufacturing are Gerber files (RS-274X) and drill files (Excellon). These files contain the necessary information for the PCB manufacturer to fabricate the board, including the copper layer artwork, solder mask and silkscreen layers, and drill hole locations and sizes. -
What surface finish options are available for PCBs?
There are several surface finish options available for PCBs, each with their own advantages and disadvantages. The most common surface finishes include: - Hot Air Solder Leveling (HASL)
- Organic Solderability Preservative (OSP)
- Electroless Nickel Immersion Gold (ENIG)
- Immersion Silver (IAg)
-
Immersion Tin (ISn)
-
How do I choose the right PCB material for my application?
Choosing the right PCB material depends on the specific requirements of your application, such as the operating environment, electrical and thermal properties, and mechanical stresses. Common PCB materials include: - FR-4: A versatile, glass-reinforced epoxy laminate suitable for most applications.
- High-Tg FR-4: A variant of FR-4 with improved thermal stability for high-temperature applications.
- Polyimide: A high-performance material with excellent thermal and chemical resistance, suitable for aerospace and military applications.
- Aluminum: A metal-core PCB material with high thermal conductivity, suitable for high-power LED lighting and automotive applications.
Consult with your PCB manufacturer or materials supplier to determine the best material for your specific application.
Conclusion
PCB manufacturing is a complex and multi-faceted process that requires a combination of technical expertise, state-of-the-art equipment, and strict quality control measures. By understanding the various aspects of PCB manufacturing, from design to fabrication to quality control, you can make informed decisions when choosing a PCB manufacturing service provider and ensure the success of your project.
As the electronics industry continues to evolve, so too will the PCB manufacturing industry, with new technologies and trends emerging to meet the changing demands of the market. By staying up-to-date with these developments and partnering with a reliable PCB manufacturer, you can stay ahead of the curve and bring your innovative ideas to life.
No responses yet