Introduction to PCB Impedance Control
Printed Circuit Board (PCB) impedance control is a crucial aspect of modern electronics manufacturing, especially in high-speed and high-frequency applications. Impedance control ensures that the electrical signals propagate through the PCB traces with minimal distortion, reflection, and crosstalk, thereby maintaining signal integrity and overall system performance.
In this article, we will delve into the fundamentals of PCB impedance control, its importance in various applications, and how to effectively specify your requirements to achieve optimal results in PCB manufacturing.
Understanding PCB Impedance
What is PCB Impedance?
PCB impedance refers to the opposition to the flow of alternating current (AC) in a PCB trace. It is a combination of resistance, capacitance, and inductance, which together determine the characteristic impedance of a trace. The characteristic impedance is typically expressed in ohms (Ω) and is influenced by factors such as the trace width, thickness, spacing, and the dielectric constant of the PCB substrate material.
Why is PCB Impedance Control Important?
Proper PCB impedance control is essential for several reasons:
-
Signal Integrity: Impedance mismatches can cause signal reflections, leading to distortion, ringing, and overshoot, which can compromise signal integrity and cause errors in data transmission.
-
Electromagnetic Compatibility (EMC): Uncontrolled impedance can result in increased electromagnetic interference (EMI) and reduced electromagnetic compatibility, potentially causing issues with nearby electronic devices.
-
High-Speed Applications: As signal frequencies increase, the impact of impedance mismatches becomes more pronounced. Impedance control is crucial for high-speed applications such as high-speed digital interfaces, RF circuits, and high-bandwidth analog signals.
-
Reliability and Performance: Proper impedance control contributes to the overall reliability and performance of the electronic system by minimizing signal degradation and ensuring consistent signal propagation.
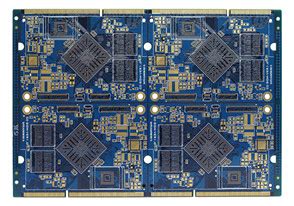
PCB Impedance Control Techniques
Trace Geometry
One of the primary methods for achieving impedance control is by adjusting the trace geometry. The width, thickness, and spacing of the traces can be modified to achieve the desired characteristic impedance. Wider traces have lower impedance, while narrower traces have higher impedance. The thickness of the trace and the spacing between traces also influence the impedance.
Dielectric Material Selection
The choice of dielectric material, which is the insulating layer between the conductive layers of the PCB, plays a significant role in impedance control. The dielectric constant (Dk) of the material determines the capacitance between the trace and the reference plane, affecting the characteristic impedance. Materials with lower Dk values, such as Rogers RO4000 series or Isola IS410, are often used for high-speed and RF applications.
Stackup Design
The PCB stackup, which refers to the arrangement of conductive and dielectric layers, is another crucial factor in impedance control. The stackup design determines the distance between the signal trace and the reference plane (e.g., ground or power plane), influencing the impedance. Symmetric stackups, where the signal layers are placed equidistant from the reference planes, help maintain consistent impedance across the board.
Termination and Matching
Proper termination and matching techniques are employed to minimize reflections and ensure efficient power transfer. Common termination methods include series termination, parallel termination, and differential termination. The choice of termination depends on factors such as the signal type, trace length, and driver/receiver characteristics.
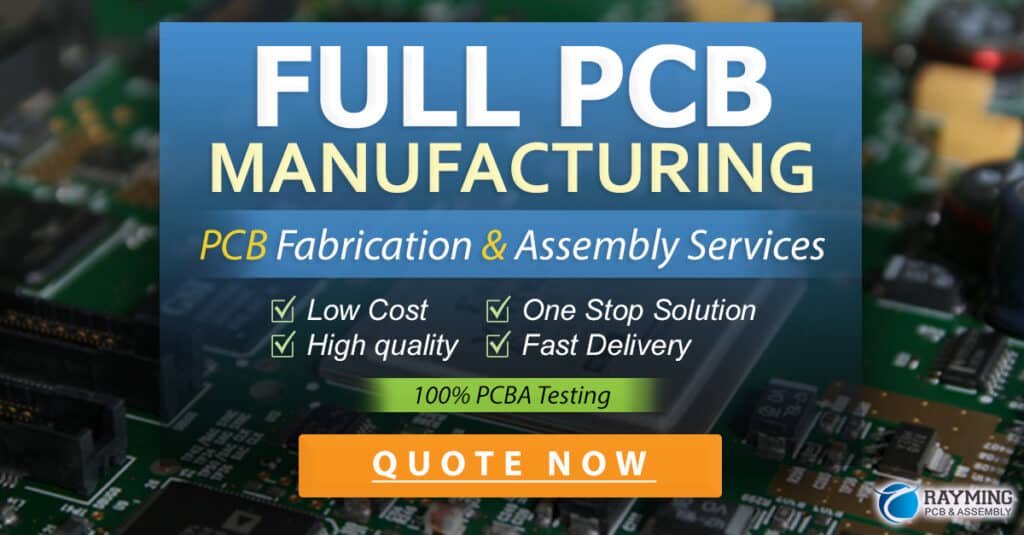
Specifying PCB Impedance Control Requirements
When outsourcing PCB manufacturing, it is essential to clearly communicate your impedance control requirements to the manufacturer. Here are some key points to consider:
-
Impedance Value: Specify the target characteristic impedance value for your traces, typically 50Ω for single-ended signals and 100Ω for differential pairs, unless your application requires different values.
-
Tolerance: Indicate the acceptable tolerance for the impedance value, such as ±10% or ±5%. Tighter tolerances may increase manufacturing costs but provide better control over impedance variations.
-
Trace Geometry: Provide the desired trace width, thickness, and spacing for each impedance-controlled layer. If you have specific requirements or constraints, communicate them clearly to the manufacturer.
-
Dielectric Material: Specify the preferred dielectric material for your application, considering factors such as the dielectric constant, dissipation factor, and thermal properties. If you have specific material requirements, provide the manufacturer with the material name or specifications.
-
Stackup: Define the desired stackup configuration, including the number of layers, layer order, and dielectric thicknesses. If you have a specific stackup in mind, provide a detailed diagram or work with the manufacturer to optimize the stackup for your application.
-
Controlled Impedance Layers: Clearly identify which layers in the stackup require impedance control. Specify whether you need single-ended or differential impedance control, or both.
-
Trace Routing: Provide guidelines for trace routing, such as minimum trace length, maximum uncoupled length, and any specific routing requirements for critical signals.
-
Test Coupons: Request the inclusion of impedance test coupons on the production panel. Test coupons allow for impedance measurement and verification during the manufacturing process.
-
Testing and Reporting: Specify the required impedance testing methods, such as Time Domain Reflectometry (TDR) or Insertion Loss testing, and the desired reporting format for the impedance measurements.
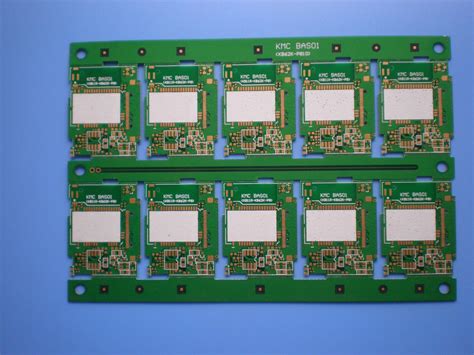
PCB Impedance Control Application Examples
High-Speed Digital Interfaces
High-speed digital interfaces, such as USB, PCIe, SATA, and HDMI, require strict impedance control to maintain signal integrity and minimize reflections. These interfaces typically use differential signaling, where impedance control is critical for maintaining signal balance and reducing crosstalk.
For example, USB 3.0 specifications require a differential impedance of 90Ω ±10% for the transmit and receive pairs. Failure to meet these requirements can lead to signal degradation, increased bit error rates, and potential device malfunctions.
RF and Microwave Circuits
RF and microwave circuits, used in wireless communication systems, radar, and satellite applications, heavily rely on impedance control for efficient power transfer and minimizing signal reflections. These circuits often utilize controlled impedance transmission lines, such as microstrip or stripline, to interconnect components.
Impedance mismatches in RF circuits can cause signal reflections, leading to reduced power transfer, distortion, and unwanted radiation. Proper impedance control, along with techniques like impedance matching networks and careful component placement, ensures optimal performance in RF and microwave applications.
Automotive and Industrial Electronics
Automotive and industrial electronics operate in harsh environments with stringent reliability and EMC requirements. Proper PCB impedance control helps mitigate issues related to signal integrity, crosstalk, and electromagnetic interference in these applications.
For example, in automotive infotainment systems or advanced driver assistance systems (ADAS), high-speed data buses like CAN, LIN, or FlexRay require controlled impedance to ensure reliable communication between electronic control units (ECUs). Similarly, in industrial automation systems, controlled impedance PCBs are essential for maintaining signal integrity in high-speed communication protocols like EtherCAT or PROFINET.
Frequently Asked Questions (FAQ)
- What is the impact of improper PCB impedance control?
Improper PCB impedance control can lead to signal integrity issues, such as reflections, ringing, overshoot, and crosstalk. These issues can cause data corruption, increased bit error rates, and potential device malfunctions. Additionally, poor impedance control can result in increased electromagnetic interference (EMI) and reduced electromagnetic compatibility (EMC).
- How does the dielectric constant affect PCB impedance?
The dielectric constant (Dk) of the PCB substrate material influences the capacitance between the trace and the reference plane, which in turn affects the characteristic impedance. A higher Dk value results in lower impedance, while a lower Dk value leads to higher impedance. Therefore, the choice of dielectric material is crucial for achieving the desired impedance in PCB design.
- What is the difference between single-ended and differential impedance control?
Single-ended impedance control refers to the control of impedance for individual traces with respect to a common reference plane, such as ground or power. Differential impedance control, on the other hand, focuses on the impedance of a pair of traces with respect to each other, commonly used in high-speed differential signaling. Differential impedance control is crucial for maintaining signal balance and reducing crosstalk in differential pairs.
- How can I verify the impedance of my PCB?
PCB impedance can be verified through various testing methods, such as Time Domain Reflectometry (TDR) or Insertion Loss testing. TDR measures the impedance along the trace by sending a fast rise time pulse and analyzing the reflections, while Insertion Loss testing measures the attenuation of a signal as it propagates through the trace. Impedance test coupons, which are dedicated traces designed for impedance measurement, are often included on the production panel for verification purposes.
- What are the common impedance values used in PCB design?
The most common impedance values used in PCB design are 50Ω for single-ended signals and 100Ω for differential pairs. These values are widely used in various applications, such as high-speed digital interfaces, RF circuits, and telecommunications. However, depending on the specific application and requirements, other impedance values like 75Ω or 90Ω may be used. It is essential to consult the relevant standards, specifications, or application notes to determine the appropriate impedance value for your design.
Conclusion
PCB impedance control is a critical aspect of modern electronics manufacturing, ensuring signal integrity, reliability, and overall system performance. By understanding the fundamentals of impedance control, employing appropriate design techniques, and clearly specifying requirements to the manufacturer, designers can achieve optimal results in their PCB designs.
Effective communication between the designer and the PCB manufacturer is vital for successful impedance control implementation. Providing comprehensive and accurate information about impedance requirements, trace geometry, dielectric material, stackup, and testing expectations enables the manufacturer to deliver high-quality, impedance-controlled PCBs that meet the specific needs of the application.
As technology advances and signal speeds continue to increase, the importance of PCB impedance control will only grow. Designers must stay updated with the latest techniques, materials, and best practices to ensure their designs can keep pace with the ever-evolving demands of the electronics industry.
Impedance Control Parameter | Description | Common Values |
---|---|---|
Characteristic Impedance | The target impedance value for the traces | 50Ω (single-ended), 100Ω (differential) |
Tolerance | Acceptable deviation from the target impedance | ±10%, ±5% |
Trace Width | The width of the impedance-controlled traces | Depends on the impedance value and dielectric material |
Trace Spacing | The spacing between adjacent traces | Depends on the impedance value and crosstalk requirements |
Dielectric Constant (Dk) | The dielectric constant of the PCB substrate material | 4.0 (FR-4), 3.0-3.5 (Rogers RO4000 series) |
Dielectric Thickness | The thickness of the dielectric layer between the trace and reference plane | Depends on the desired impedance and stackup design |
By carefully considering and specifying these impedance control parameters, designers can ensure that their PCBs meet the required impedance targets and perform optimally in their intended applications.
No responses yet