Why is Power Supply Optimization Important?
Before diving into the specific guidelines, it’s essential to understand why power supply optimization is crucial. A well-designed power supply ensures:
- Efficiency: Optimal power supply design minimizes power losses, resulting in lower heat generation and improved overall system efficiency.
- Stability: A stable power supply provides consistent voltage and current to the connected components, ensuring reliable operation.
- EMC Compliance: Proper power supply layout helps minimize electromagnetic interference (EMI) and ensures compliance with EMC regulations.
Key Considerations for Power Supply PCB Layout
Component Placement
One of the most critical aspects of power supply PCB layout is component placement. Here are some guidelines to follow:
- Place the power components close to the input and output connectors to minimize the length of high-current traces.
- Position the switching devices (e.g., MOSFETs, IGBTs) close to the transformer or inductor to reduce the loop area and minimize parasitic inductance.
- Keep the sensitive analog circuitry, such as feedback and control components, away from high-current and high-frequency switching paths to avoid interference.
Grounding and Ground Planes
Proper grounding is essential for power supply performance and EMC. Consider the following guidelines:
- Use a solid ground plane to provide a low-impedance return path for currents and minimize ground bounce.
- Implement a star ground topology, where all ground connections meet at a single point, to avoid ground loops and minimize noise coupling.
- Separate the analog and digital ground planes, connecting them at a single point near the power supply to prevent digital noise from affecting analog circuitry.
Trace Routing and Widths
The trace routing and widths play a significant role in power supply performance. Keep these points in mind:
- Use wide traces for high-current paths to minimize resistance and voltage drop.
- Keep the high-current traces as short as possible to reduce parasitic inductance and improve transient response.
- Route the sensitive traces, such as feedback and control signals, away from high-current and high-frequency paths to minimize crosstalk and noise pickup.
Decoupling and Bypass Capacitors
Decoupling and bypass capacitors are crucial for power supply stability and noise reduction. Follow these guidelines:
- Place decoupling capacitors close to the power pins of ICs to minimize the loop area and provide a low-impedance path for high-frequency currents.
- Use a combination of bulk capacitors (e.g., electrolytic or tantalum) and ceramic capacitors to provide both low-frequency and high-frequency decoupling.
- Choose capacitors with low equivalent series resistance (ESR) and equivalent series inductance (ESL) to ensure effective decoupling and minimize parasitic effects.
Shielding and EMI Reduction
To minimize EMI and ensure EMC compliance, consider the following shielding techniques:
- Use shielding cans or enclosures to contain high-frequency noise sources, such as switching devices and transformers.
- Implement proper grounding of the shields, ensuring a low-impedance connection to the ground plane.
- Use ferrite beads or common-mode chokes on power lines to suppress high-frequency noise and prevent EMI propagation.
Thermal Management
Proper thermal management is essential for power supply reliability and longevity. Consider these guidelines:
- Provide adequate copper area for power components to dissipate heat effectively.
- Use thermal vias to transfer heat from the components to the ground plane or dedicated thermal layers.
- Implement proper airflow and ventilation in the enclosure to prevent heat buildup and ensure optimal operating temperatures.
PCB Layout Techniques for Specific Power Supply Topologies
Different power supply topologies may require specific PCB layout techniques to optimize performance. Let’s discuss a few common topologies:
Buck Converter Layout
When laying out a buck converter, consider the following:
- Place the input capacitor close to the switching device to minimize the loop area and reduce input ripple.
- Use a ground plane to provide a low-impedance return path for the high-frequency switching currents.
- Route the output inductor and capacitor traces to minimize the loop area and reduce output ripple.
Boost Converter Layout
For a boost converter layout, keep these points in mind:
- Place the input capacitor close to the switching device to reduce input ripple and provide a low-impedance path for the switch current.
- Route the inductor and diode traces to minimize the loop area and reduce parasitic inductance.
- Use a ground plane to provide a low-impedance return path for the high-frequency currents.
Flyback Converter Layout
When designing a flyback converter layout, consider the following:
- Place the primary-side components (e.g., switching device, transformer) close together to minimize the primary loop area.
- Use a ground plane on the primary side to provide a low-impedance return path for the switching currents.
- Separate the primary and secondary grounds, connecting them only at a single point (usually the transformer’s core) to maintain isolation and prevent noise coupling.
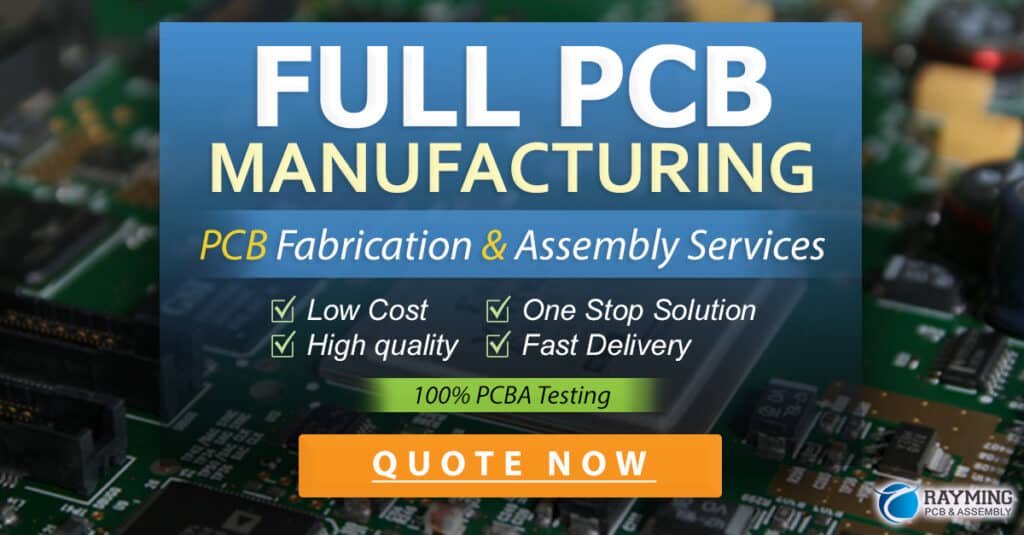
PCB Layout Verification and Testing
After completing the PCB layout, it’s crucial to verify and test the design to ensure optimal power supply performance. Here are some steps to follow:
- Perform a design rule check (DRC) to verify that the layout meets the manufacturing constraints and design rules specified by the PCB fabricator.
- Conduct a thorough visual inspection of the PCB layout to identify any potential issues, such as unintended short circuits or missing connections.
- Use simulation tools to analyze the power supply’s performance, including transient response, stability, and EMC.
- Perform physical testing on the manufactured PCB to validate the power supply’s functionality, efficiency, and compliance with specifications.
Frequently Asked Questions (FAQ)
-
Q: What is the importance of component placement in power supply PCB layout?
A: Component placement is crucial in power supply PCB layout as it directly impacts the performance and reliability of the power supply. Proper component placement minimizes parasitic inductance, reduces noise coupling, and improves overall efficiency. -
Q: Why is grounding important in power supply PCB layout?
A: Proper grounding is essential in power supply PCB layout to provide a low-impedance return path for currents, minimize ground bounce, and reduce noise coupling. A well-designed grounding scheme, such as a star ground topology, helps ensure power supply stability and EMC compliance. -
Q: How do decoupling and bypass capacitors contribute to power supply performance?
A: Decoupling and bypass capacitors play a vital role in power supply performance by providing a low-impedance path for high-frequency currents, reducing noise, and improving power supply stability. They should be placed close to the power pins of ICs to minimize the loop area and ensure effective decoupling. -
Q: What are some shielding techniques used in power supply PCB layout?
A: Shielding techniques in power supply PCB layout include using shielding cans or enclosures to contain high-frequency noise sources, implementing proper grounding of the shields, and using ferrite beads or common-mode chokes on power lines to suppress EMI. -
Q: Why is thermal management important in power supply PCB layout?
A: Thermal management is crucial in power supply PCB layout to ensure reliable operation and longevity of the components. Proper thermal management techniques, such as providing adequate copper area for power components, using thermal vias, and implementing proper airflow and ventilation, help dissipate heat effectively and prevent component overheating.
Conclusion
Optimizing power supply performance through proper PCB layout is a critical aspect of electronic design. By following the guidelines discussed in this article, such as strategic component placement, proper grounding, trace routing, decoupling techniques, shielding, and thermal management, designers can create power supplies that are efficient, stable, and EMC compliant. Additionally, considering specific layout techniques for different power supply topologies and conducting thorough verification and testing ensures the power supply meets the desired performance requirements. By prioritizing power supply optimization in PCB layout, designers can develop robust and reliable electronic systems that deliver optimal performance in various applications.
References
-
“Power Supply Design Guide,” Texas Instruments, 2018. [Online]. Available: https://www.ti.com/seclit/ml/slup263/slup263.pdf
-
“PCB Layout Considerations for Non-Isolated Switching Power Supplies,” Maxim Integrated, 2007. [Online]. Available: https://pdfserv.maximintegrated.com/en/an/AN1149.pdf
-
“PCB Layout Techniques for EMC Compliance,” Altium, 2021. [Online]. Available: https://resources.altium.com/p/pcb-layout-techniques-emc-compliance
-
“Power Supply Layout and EMI,” Analog Devices, 2012. [Online]. Available: https://www.analog.com/media/en/technical-documentation/application-notes/AN-1368.pdf
-
“Thermal Management in Power Supply Design,” ON Semiconductor, 2020. [Online]. Available: https://www.onsemi.com/pub/Collateral/AND9788-D.PDF
No responses yet