What are PCB Laminates?
PCB laminates are the base material used to manufacture printed circuit boards (PCBs). They provide the insulating layer and mechanical support for the copper traces and components that make up the circuit. PCB laminates typically consist of a reinforcement material, such as glass fiber, impregnated with a thermosetting resin, usually epoxy.
Composition of PCB Laminates
PCB laminates are composite materials made up of two main components:
-
Reinforcement material: This is usually a woven glass fiber fabric, which provides mechanical strength and dimensional stability to the laminate. Other reinforcement materials, such as aramid fiber or paper, may also be used in specific applications.
-
Resin system: The most common resin used in PCB laminates is epoxy, a thermosetting polymer that provides excellent electrical insulation, chemical resistance, and thermal stability. Other resins, such as polyimide or PTFE, may be used for high-performance applications.
The combination of the reinforcement material and resin system determines the electrical, mechanical, and thermal properties of the PCB laminate.
Types of PCB Laminates
There are several types of PCB laminates available, each with its own unique properties and applications. Some of the most common types include:
FR-4 Laminates
FR-4 (Flame Retardant 4) is the most widely used PCB laminate material. It is made of woven glass fabric impregnated with an epoxy resin. FR-4 offers a good balance of electrical, mechanical, and thermal properties at a reasonable cost, making it suitable for a wide range of applications.
High Tg Laminates
High Tg laminates are similar to FR-4 but use a modified epoxy resin with a higher glass transition temperature (Tg). This makes the laminate more resistant to thermal stress and suitable for applications that require higher operating temperatures or lead-free soldering processes.
Polyimide Laminates
Polyimide laminates use a polyimide resin instead of epoxy, which provides excellent thermal stability, chemical resistance, and electrical properties. These laminates are often used in high-reliability applications, such as aerospace, military, and automotive electronics.
PTFE Laminates
PTFE (polytetrafluoroethylene) laminates, also known as Teflon laminates, offer the lowest dielectric constant and loss tangent among PCB laminates. They are ideal for high-frequency applications, such as RF and microwave circuits, where signal integrity is critical.
Ceramic-based Laminates
Ceramic-based laminates use a ceramic material, such as aluminum oxide or aluminum nitride, as the reinforcement instead of glass fiber. These laminates provide excellent thermal conductivity and are often used in high-power applications or for thermal management purposes.
Properties of PCB Laminates
When selecting a PCB laminate, several key properties must be considered to ensure the material is suitable for the intended application. These properties include:
Electrical Properties
-
Dielectric constant (Dk): The ratio of the electric field strength in a vacuum to that in the material. A lower Dk is desirable for high-frequency applications to minimize signal delay and distortion.
-
Dissipation factor (Df) or loss tangent: A measure of the energy lost in the material due to dielectric relaxation. A lower Df is preferred to minimize signal attenuation and heat generation.
-
Dielectric strength: The maximum electric field strength the material can withstand before breakdown occurs. A higher dielectric strength is necessary for high-voltage applications.
Mechanical Properties
-
Tensile strength: The maximum stress the material can withstand before breaking. A higher tensile strength is desirable for improved durability and reliability.
-
Flexural strength: The ability of the material to resist bending forces. A higher flexural strength is important for applications where the PCB may be subjected to mechanical stress.
-
Dimensional stability: The ability of the material to maintain its dimensions under varying environmental conditions, such as temperature and humidity changes. Good dimensional stability is critical for maintaining the integrity of the copper traces and preventing warpage.
Thermal Properties
-
Glass transition temperature (Tg): The temperature at which the material transitions from a glassy to a rubbery state. A higher Tg is necessary for applications that require higher operating temperatures or lead-free soldering processes.
-
Coefficient of thermal expansion (CTE): The rate at which the material expands or contracts with temperature changes. A lower CTE is desirable to minimize thermal stress and improve reliability.
-
Thermal conductivity: The ability of the material to conduct heat. A higher thermal conductivity is beneficial for applications that generate significant heat, as it helps to dissipate the heat and prevent hot spots.
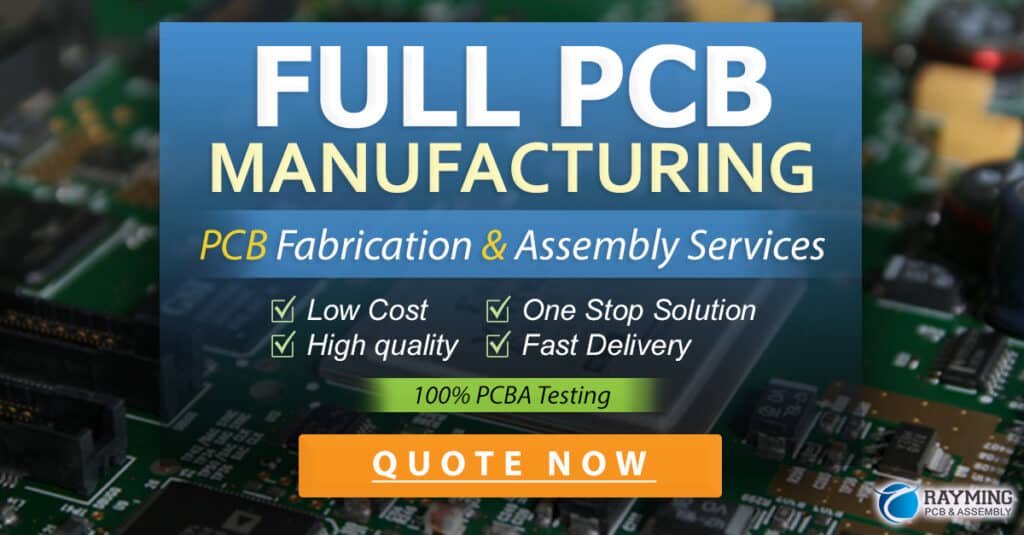
Selecting the Right PCB Laminate
Choosing the appropriate PCB laminate for a given application involves considering the electrical, mechanical, and thermal requirements of the circuit, as well as the environmental conditions it will be exposed to. The following table provides a general guide for selecting PCB laminates based on common applications:
Application | Recommended PCB Laminates |
---|---|
General-purpose electronics | FR-4, High Tg FR-4 |
High-frequency circuits | PTFE, Low-loss ceramic-based |
High-reliability applications | Polyimide, High Tg FR-4 |
High-power electronics | Ceramic-based, High Tg FR-4 |
Automotive electronics | Polyimide, High Tg FR-4 |
Aerospace and military | Polyimide, PTFE, Ceramic-based |
It is essential to work closely with the PCB manufacturer and laminate supplier to ensure that the selected material meets the specific requirements of the application and is compatible with the manufacturing process.
Manufacturing Considerations
When designing a PCB using a specific laminate, it is important to consider the manufacturing process and any limitations or guidelines associated with the material. Some key manufacturing considerations include:
-
Drilling: Different laminates may require specific drill bit types, speeds, and feed rates to minimize damage and ensure hole quality. The laminate’s hardness and abrasiveness should be taken into account when selecting drilling parameters.
-
Etching: The etchability of the copper foil on the laminate can vary depending on the material and the copper foil type (e.g., electrodeposited or rolled annealed). The etching process parameters may need to be adjusted to achieve the desired trace geometries and avoid over- or under-etching.
-
Lamination: The lamination process, which involves bonding the copper foil to the base material under heat and pressure, must be optimized for the specific laminate to ensure proper adhesion and minimize defects such as delamination or blistering.
-
Soldering: The laminate’s thermal properties, particularly its Tg and CTE, should be considered when selecting soldering processes and parameters. Lead-free soldering, which requires higher temperatures, may necessitate the use of high Tg laminates to prevent thermal damage.
Collaborating closely with the PCB manufacturer and providing detailed material specifications and design files can help ensure that the PCB is manufactured to the required quality standards and performs as intended.
Future Trends in PCB Laminates
As electronics continue to advance, there is a growing demand for PCB laminates that can support higher frequencies, greater bandwidths, and more challenging environmental conditions. Some of the future trends in PCB laminates include:
-
Low-loss materials: The development of laminates with even lower dielectric constants and loss tangents to support the ever-increasing frequencies used in modern communication systems, such as 5G networks and millimeter-wave applications.
-
High-speed materials: The creation of laminates with improved signal integrity properties, such as lower skew and jitter, to enable faster data transmission rates in high-speed digital circuits.
-
Thermally conductive materials: The incorporation of thermally conductive fillers, such as boron nitride or aluminum nitride, into laminates to enhance thermal management capabilities and address the increasing power densities in modern electronics.
-
Environmentally friendly materials: The development of halogen-free, low-toxicity, and recyclable laminates to meet growing environmental concerns and comply with evolving regulations, such as the Restriction of Hazardous Substances (RoHS) directive.
As these new materials emerge, designers and manufacturers will need to stay informed about their properties and potential applications to take full advantage of their capabilities and ensure the continued advancement of electronic systems.
Frequently Asked Questions (FAQ)
- What is the difference between FR-4 and high Tg FR-4 laminates?
-
FR-4 is the standard laminate material used in most general-purpose PCBs. High Tg FR-4 laminates use a modified epoxy resin with a higher glass transition temperature (Tg), making them more suitable for applications that require higher operating temperatures or lead-free soldering processes.
-
Can I use a standard FR-4 laminate for high-frequency applications?
-
While FR-4 can be used for some high-frequency applications, it may not be the best choice for very high frequencies or applications that require exceptional signal integrity. For these cases, laminates with lower dielectric constants and loss tangents, such as PTFE or low-loss ceramic-based materials, are recommended.
-
What are the advantages of using polyimide laminates?
-
Polyimide laminates offer excellent thermal stability, chemical resistance, and electrical properties. They are often used in high-reliability applications, such as aerospace, military, and automotive electronics, where the PCB must withstand harsh environmental conditions and maintain long-term performance.
-
How do I select the right laminate thickness for my PCB?
-
The choice of laminate thickness depends on several factors, including the number of layers in the PCB, the required mechanical strength, and the desired impedance of the traces. Thinner laminates are typically used for high-density, multi-layer designs, while thicker laminates provide greater mechanical stability and are often used in single-layer or double-sided PCBs. It is best to consult with the PCB manufacturer and use PCB design software to determine the optimal laminate thickness for your specific application.
-
Are there any special considerations when soldering PCBs with high Tg laminates?
- High Tg laminates are designed to withstand higher soldering temperatures associated with lead-free soldering processes. However, it is still essential to control the soldering temperature and duration to prevent thermal damage to the PCB and components. Following the laminate manufacturer’s guidelines and using appropriate soldering techniques, such as controlled-temperature soldering or selective soldering, can help ensure reliable solder joints and minimize the risk of thermal stress.
Conclusion
PCB laminates play a critical role in the performance and reliability of electronic circuits. Understanding the different types of laminates, their properties, and their applications is essential for designing and manufacturing high-quality PCBs. By carefully considering the electrical, mechanical, and thermal requirements of the application and working closely with PCB manufacturers and laminate suppliers, designers can select the most suitable laminate material and ensure the optimal performance of their electronic devices.
As technology continues to advance, new laminate materials with improved properties will emerge to meet the ever-growing demands of modern electronics. Staying informed about these developments and adapting designs accordingly will be crucial for staying competitive in the rapidly evolving world of PCBs.
No responses yet