Introduction to PCB Insulation
Printed Circuit Boards (PCBs) are essential components in modern electronics, providing a platform for interconnecting electronic components and facilitating the flow of electrical signals. To ensure proper functionality and prevent short circuits, PCBs require adequate insulation between conductive layers and traces. PCB insulation plays a crucial role in maintaining the integrity of electrical pathways and protecting the board from external factors such as moisture, dust, and mechanical stress.
In this article, we will explore the various aspects of PCB insulation, including the materials used, their properties, and the techniques employed to achieve effective insulation. We will also discuss the importance of proper insulation in different applications and the challenges faced in designing and manufacturing insulated PCBs.
Types of PCB Insulation Materials
PCB insulation materials come in various forms, each with its own set of properties and advantages. The choice of insulation material depends on factors such as the intended application, operating environment, and required performance characteristics. Here are some of the commonly used PCB insulation materials:
1. FR-4
FR-4 (Flame Retardant 4) is the most widely used PCB insulation material. It is a composite material made of woven fiberglass cloth impregnated with an epoxy resin. FR-4 offers excellent mechanical strength, good dielectric properties, and high resistance to moisture and chemicals. It is suitable for a wide range of applications, including consumer electronics, industrial control systems, and telecommunications equipment.
2. Polyimide
Polyimide is a high-performance polymer known for its exceptional thermal stability, mechanical strength, and chemical resistance. It is often used in applications that require operation at high temperatures or exposure to harsh environments. Polyimide-based PCBs are commonly found in aerospace, automotive, and military applications.
3. Teflon (PTFE)
Teflon, or polytetrafluoroethylene (PTFE), is a fluoropolymer with excellent dielectric properties and low dielectric constant. It offers superior electrical insulation, low moisture absorption, and high thermal stability. Teflon-based PCBs are commonly used in high-frequency applications, such as radar systems and wireless communication devices.
4. Ceramic
Ceramic PCB insulation materials, such as alumina and beryllia, are known for their excellent thermal conductivity, high dielectric strength, and low dielectric loss. They are often used in high-power applications that generate significant heat, such as power electronics and LED lighting.
5. Polyethylene Terephthalate (PET)
PET is a thermoplastic polymer that offers good electrical insulation properties, dimensional stability, and resistance to moisture and chemicals. It is commonly used as a substrate material for flexible PCBs and in applications that require high flexibility and durability.
Properties of PCB Insulation Materials
When selecting a PCB insulation material, several key properties need to be considered to ensure optimal performance and reliability. These properties include:
1. Dielectric Constant
The dielectric constant, also known as relative permittivity, is a measure of a material’s ability to store electrical energy. A lower dielectric constant indicates better insulation properties and reduces signal propagation delays. Materials with low dielectric constants, such as Teflon and certain ceramics, are preferred for high-frequency applications.
2. Dielectric Strength
Dielectric strength refers to the maximum electric field that an insulating material can withstand before breakdown occurs. Higher dielectric strength ensures better insulation and prevents electrical breakdown between conductive layers. Materials with high dielectric strength, such as polyimide and ceramic, are suitable for high-voltage applications.
3. Thermal Conductivity
Thermal conductivity measures a material’s ability to conduct heat. In PCB insulation, materials with high thermal conductivity are desirable for applications that generate significant heat, as they help dissipate heat more effectively and prevent thermal damage to components. Ceramic materials, such as alumina and beryllia, excel in thermal conductivity.
4. Moisture Absorption
Moisture absorption refers to a material’s tendency to absorb moisture from the environment. High moisture absorption can lead to degradation of insulation properties, corrosion of conductive traces, and reduced reliability. Materials with low moisture absorption, such as FR-4 and polyimide, are preferred for applications exposed to humid environments.
5. Mechanical Strength
Mechanical strength is an important consideration in PCB insulation, especially for applications subject to mechanical stress or vibration. Materials with high mechanical strength, such as FR-4 and polyimide, provide better support and durability to the PCB assembly.
Insulation Material | Dielectric Constant | Dielectric Strength (kV/mm) | Thermal Conductivity (W/mK) | Moisture Absorption (%) |
---|---|---|---|---|
FR-4 | 4.2-4.9 | 20-50 | 0.3-0.4 | 0.1-0.2 |
Polyimide | 3.2-3.5 | 150-300 | 0.1-0.4 | 0.2-0.4 |
Teflon (PTFE) | 2.0-2.1 | 60-173 | 0.2-0.3 | <0.01 |
Alumina (Ceramic) | 9.0-10.0 | 10-35 | 20-30 | <0.01 |
PET | 3.0-3.2 | 17-21 | 0.1-0.2 | 0.1-0.3 |
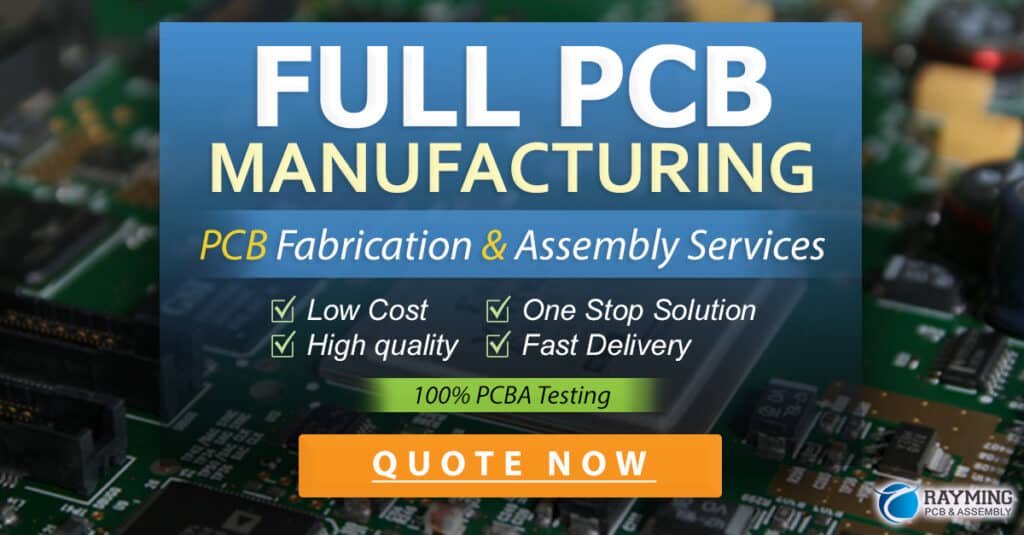
PCB Insulation Techniques
To achieve effective insulation between conductive layers and traces on a PCB, various techniques are employed during the manufacturing process. These techniques ensure proper separation and prevent electrical shorts. Here are some commonly used PCB insulation techniques:
1. Solder Mask
Solder mask is a thin layer of polymer applied over the copper traces on a PCB. It serves as an insulating barrier, protecting the copper from oxidation and preventing accidental short circuits during soldering. Solder mask also provides a surface for applying component labels and other markings.
2. Conformal Coating
Conformal coating is a protective layer applied over the assembled PCB to provide additional insulation and environmental protection. It conforms to the contours of the board and components, creating a seamless barrier against moisture, dust, and other contaminants. Common conformal coating materials include acrylic, silicone, and urethane.
3. Potting and Encapsulation
Potting and encapsulation involve filling the spaces between components and the PCB with a solid or gelatinous compound, such as epoxy or silicone. This technique provides enhanced insulation, mechanical support, and protection against vibration and shock. It is commonly used in harsh environments or applications requiring high reliability.
4. Insulating Washers and Spacers
Insulating washers and spacers are used to provide physical separation and insulation between conductive components or layers. They are typically made of non-conductive materials, such as nylon, Teflon, or ceramic, and are placed between components or mounting points to prevent electrical contact.
5. Multilayer PCBs
Multilayer PCBs consist of multiple layers of conductive and insulating materials laminated together. The insulating layers, typically made of FR-4 or similar materials, provide separation between the conductive layers. Multilayer PCBs allow for higher component density and more complex routing while maintaining adequate insulation.
Importance of Proper PCB Insulation
Proper PCB insulation is critical for several reasons:
1. Preventing Short Circuits
Adequate insulation prevents unintended electrical contact between conductive traces and layers, eliminating the risk of short circuits. Short circuits can cause device malfunction, damage components, and even pose safety hazards.
2. Ensuring Signal Integrity
Proper insulation helps maintain signal integrity by reducing crosstalk and electromagnetic interference (EMI) between adjacent traces. This is particularly important in high-speed and high-frequency applications where signal integrity is crucial.
3. Protecting Against Environmental Factors
Insulation materials protect the PCB and its components from environmental factors such as moisture, dust, and chemical exposure. This protection enhances the reliability and longevity of the electronic device.
4. Meeting Safety Standards
Adequate PCB insulation is necessary to meet safety standards and regulations, such as those set by UL (Underwriters Laboratories) and IPC (Association Connecting Electronics Industries). Compliance with these standards ensures the safety and reliability of the end product.
Challenges in PCB Insulation Design and Manufacturing
Designing and manufacturing insulated PCBs can present several challenges:
1. Material Selection
Selecting the appropriate insulation material based on the specific application requirements, such as operating temperature, dielectric properties, and environmental conditions, can be complex. Balancing cost, performance, and manufacturability is crucial in material selection.
2. Dimensional Constraints
As electronic devices become smaller and more compact, PCB designers face the challenge of maintaining adequate insulation while accommodating tight dimensional constraints. Ensuring sufficient clearance and creepage distances between conductive traces and components becomes increasingly difficult in high-density designs.
3. Manufacturing Processes
Implementing effective insulation techniques during the PCB manufacturing process requires precise control and adherence to strict quality standards. Inconsistencies in the application of solder mask, conformal coating, or other insulation methods can lead to insulation failures and reduced reliability.
4. Cost Considerations
Balancing the cost of insulation materials and manufacturing techniques with the desired performance and reliability is a significant challenge. Higher-performance insulation materials and advanced manufacturing processes often come at a higher cost, which needs to be justified based on the specific application requirements.
5. Thermal Management
Insulation materials can impact the thermal management of a PCB. Some insulation materials, such as ceramics, have high thermal conductivity and can aid in heat dissipation, while others may act as thermal barriers. Careful consideration of the thermal properties of insulation materials is necessary to ensure proper thermal management and prevent overheating.
Frequently Asked Questions (FAQ)
1. What is the most commonly used PCB insulation material?
FR-4 (Flame Retardant 4) is the most widely used PCB insulation material. It offers a good balance of mechanical, electrical, and thermal properties, making it suitable for a wide range of applications.
2. How does PCB insulation prevent short circuits?
PCB insulation provides a non-conductive barrier between conductive traces and layers, preventing unintended electrical contact and short circuits. Techniques such as solder mask, conformal coating, and the use of insulating materials like FR-4 help maintain the separation between conductive paths.
3. What is the purpose of solder mask on a PCB?
Solder mask is a thin layer of polymer applied over the copper traces on a PCB. It serves as an insulating barrier, protecting the copper from oxidation and preventing accidental short circuits during soldering. Solder mask also provides a surface for applying component labels and other markings.
4. How do I choose the right insulation material for my PCB?
The choice of insulation material depends on several factors, including the intended application, operating environment, required performance characteristics, and cost considerations. Consider properties such as dielectric constant, dielectric strength, thermal conductivity, and moisture absorption when selecting an insulation material. Consult with PCB manufacturers or material suppliers for guidance based on your specific requirements.
5. Can improper PCB insulation affect signal integrity?
Yes, improper PCB insulation can affect signal integrity. Inadequate insulation can lead to crosstalk and electromagnetic interference (EMI) between adjacent traces, compromising signal quality. Proper insulation techniques, such as maintaining sufficient clearance and using appropriate insulation materials, help maintain signal integrity and reduce interference.
Conclusion
PCB insulation plays a vital role in ensuring the proper functioning, reliability, and safety of electronic devices. By providing non-conductive layers between electrical pathways, insulation prevents short circuits, maintains signal integrity, and protects against environmental factors.
Understanding the various insulation materials, their properties, and the techniques used in PCB manufacturing is essential for designing and producing high-quality insulated PCBs. Careful consideration of application requirements, material selection, and manufacturing processes is necessary to overcome the challenges associated with PCB insulation.
As electronic devices continue to advance and become more compact, the importance of effective PCB insulation will only grow. Designers and manufacturers must stay updated with the latest insulation technologies and best practices to meet the evolving demands of the electronics industry.
By prioritizing proper PCB insulation, manufacturers can deliver reliable, safe, and high-performance electronic products that meet the needs of customers across various industries.
No responses yet