Introduction to PCB Performance-Enhancing Hardware
Printed Circuit Boards (PCBs) are the backbone of modern electronics. They provide a platform for components to be mounted and interconnected, enabling the creation of complex electronic systems. However, the performance of a PCB is not solely determined by its design and components. PCB performance-enhancing hardware can play a crucial role in optimizing the functionality, reliability, and efficiency of a circuit board.
In this article, we will explore various types of PCB performance-enhancing hardware and their applications. We will discuss how these hardware components can improve signal integrity, power delivery, thermal management, and mechanical stability of PCBs. Additionally, we will provide insights into the selection and implementation of these hardware components to achieve optimal performance in different PCB designs.
Types of PCB Performance-Enhancing Hardware
1. Decoupling Capacitors
Decoupling capacitors are essential components in PCB design that help to stabilize the power supply and reduce noise. They are placed close to the power pins of integrated circuits (ICs) to provide a local reservoir of charge, minimizing the effects of power supply fluctuations and high-frequency noise.
Capacitor Type | Capacitance Range | Frequency Range | Applications |
---|---|---|---|
Ceramic | 1 pF – 1 μF | High | Digital ICs, high-speed devices |
Tantalum | 0.1 μF – 1000 μF | Low to Medium | Analog ICs, power supply filtering |
Electrolytic | 1 μF – 10,000 μF | Low | Bulk capacitance, power supply filtering |
Proper selection and placement of decoupling capacitors are crucial for optimal performance. The capacitance value and frequency characteristics should be chosen based on the specific requirements of the IC and the expected noise spectrum. Placing the capacitors as close as possible to the power pins minimizes the inductance of the connection, enhancing the effectiveness of the decoupling.
2. Electromagnetic Interference (EMI) Shielding
EMI shielding is a technique used to protect PCBs from electromagnetic interference, both from external sources and internally generated noise. EMI can cause signal degradation, false triggering, and even permanent damage to components.
EMI shielding hardware includes:
– Metal enclosures
– Shielding gaskets
– Conductive adhesives
– Shielding tapes and fabrics
These components work by creating a barrier that attenuates electromagnetic waves, preventing them from entering or escaping the PCB. The effectiveness of EMI shielding depends on factors such as material properties, aperture size, and the frequency of the interference.
When implementing EMI shielding, it is important to consider the trade-offs between shielding effectiveness, cost, and manufacturability. Proper grounding and bonding techniques are also critical to ensure the integrity of the shielding.
3. Heat Sinks and Thermal Management
Heat generation is a common challenge in PCB design, especially with high-power components and dense layouts. Excessive heat can lead to component failure, reduced reliability, and degraded performance. Heat sinks and other thermal management hardware help to dissipate heat and maintain acceptable operating temperatures.
Heat sinks are passive components that provide a large surface area for heat dissipation. They are typically made of materials with high thermal conductivity, such as aluminum or copper. The design of a heat sink depends on factors such as the power dissipation of the component, available space, and airflow conditions.
Other thermal management hardware includes:
– Thermal interface materials (TIMs)
– Fans and blowers
– Peltier coolers
– Heat pipes and vapor chambers
Effective thermal management requires a holistic approach that considers the entire system, including component placement, PCB layout, and enclosure design. Thermal simulations and measurements can help optimize the thermal performance and identify potential hotspots.
4. Connectors and Interconnects
Connectors and interconnects are critical components that enable the transfer of signals and power between PCBs, modules, and external devices. The choice of connector and interconnect hardware can have a significant impact on the performance, reliability, and manufacturability of a PCB.
Common types of connectors and interconnects include:
– Board-to-board connectors
– Wire-to-board connectors
– Cable assemblies
– Sockets and headers
– Flex circuits
When selecting connectors and interconnects, factors such as signal integrity, current carrying capacity, mechanical stability, and environmental resistance must be considered. High-speed applications may require specialized connectors with controlled impedance and shielding to minimize signal degradation and crosstalk.
Proper design and layout techniques, such as minimizing stub lengths, matching impedances, and providing adequate clearances, are essential for optimal performance. Simulation tools can help analyze the signal integrity and identify potential issues before fabrication.
5. Mechanical Supports and Vibration Damping
Mechanical stability is an important consideration in PCB design, particularly in applications exposed to vibration, shock, or physical stress. Mechanical supports and vibration damping hardware help to protect components and maintain the integrity of the PCB.
Examples of mechanical support hardware include:
– Standoffs and spacers
– Stiffeners and brackets
– Mounting holes and fasteners
– Conformal coatings and potting compounds
Vibration damping hardware, such as elastomeric mounts and damping materials, helps to absorb and dissipate vibrational energy, reducing the stress on components and solder joints.
The selection and placement of mechanical support and vibration damping hardware should be based on the expected environmental conditions and the sensitivity of the components. Finite element analysis (FEA) can be used to simulate the mechanical behavior of the PCB and optimize the design for robustness.
Implementing PCB Performance-Enhancing Hardware
1. Design Considerations
When incorporating performance-enhancing hardware into a PCB design, several factors must be considered:
- Electrical requirements: Ensure that the selected hardware is compatible with the electrical specifications of the PCB, such as voltage ratings, current handling capacity, and signal frequencies.
- Mechanical constraints: Consider the available space, component heights, and mounting requirements when selecting and placing hardware components.
- Thermal management: Evaluate the heat generation and dissipation requirements of the PCB and choose appropriate thermal management hardware.
- Manufacturing feasibility: Assess the impact of the hardware on the manufacturability of the PCB, including aspects such as assembly processes, testing, and rework.
2. Layout Techniques
Proper layout techniques are crucial for the effective implementation of PCB performance-enhancing hardware. Some key considerations include:
- Component placement: Position hardware components close to their associated devices to minimize interconnect lengths and reduce parasitic effects.
- Grounding and shielding: Provide adequate grounding and shielding for EMI-sensitive components and signals, using techniques such as ground planes, shielding cans, and stitching vias.
- Thermal management: Optimize the placement of heat-generating components and thermal management hardware to ensure efficient heat dissipation and avoid thermal coupling between components.
- Signal integrity: Route high-speed signals with controlled impedance, minimize crosstalk, and provide appropriate terminations to maintain signal integrity.
3. Simulation and Analysis
Simulation and analysis tools play a vital role in the design and optimization of PCBs with performance-enhancing hardware. These tools allow engineers to predict the behavior of the PCB and identify potential issues before fabrication, saving time and cost.
Some common simulation and analysis techniques include:
– Signal integrity analysis: Simulate the propagation of high-speed signals through the PCB, considering factors such as impedance matching, crosstalk, and reflections.
– Power integrity analysis: Analyze the power delivery network to ensure stable and clean power supply to all components, considering factors such as voltage drop, decoupling, and power plane resonances.
– Thermal analysis: Simulate the thermal behavior of the PCB, identifying hotspots and evaluating the effectiveness of thermal management hardware.
– Mechanical analysis: Perform FEA to assess the mechanical strength and vibrational behavior of the PCB, optimizing the placement of mechanical support and damping hardware.
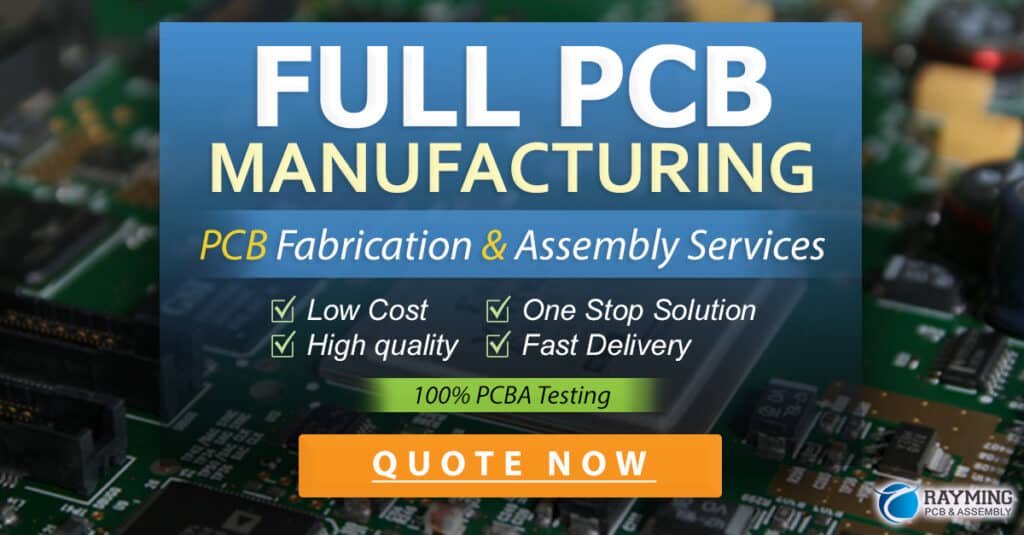
Frequently Asked Questions (FAQ)
- What are the benefits of using decoupling capacitors in a PCB design?
Decoupling capacitors help to stabilize the power supply and reduce high-frequency noise in a PCB. They act as local charge reservoirs, providing a low-impedance path for high-frequency currents and minimizing voltage fluctuations at the power pins of ICs. This improves the overall signal integrity and reliability of the PCB.
- How do I select the appropriate EMI shielding hardware for my PCB?
The selection of EMI shielding hardware depends on factors such as the frequency range of the interference, the required attenuation level, and the physical constraints of the PCB. Consider the shielding effectiveness, cost, and manufacturability of the available options. Conduct EMI simulations and measurements to validate the shielding performance and ensure compliance with relevant EMC standards.
- What are the key considerations for implementing thermal management hardware in a PCB?
When implementing thermal management hardware, consider the power dissipation of the components, the available space, and the operating environment of the PCB. Select heat sinks and other hardware based on their thermal performance, compatibility with the components, and ease of assembly. Optimize the placement of thermal management hardware to ensure efficient heat dissipation and avoid thermal coupling between components.
- How can I ensure signal integrity when using connectors and interconnects in my PCB design?
To ensure signal integrity, choose connectors and interconnects with suitable electrical characteristics, such as impedance matching and shielding, for the required signal frequencies. Minimize stub lengths and provide appropriate terminations to reduce reflections and ringing. Use simulation tools to analyze the signal integrity and identify potential issues, such as crosstalk and signal degradation.
- What are the benefits of using simulation and analysis tools in PCB design with performance-enhancing hardware?
Simulation and analysis tools allow engineers to predict the behavior of the PCB and optimize the design before fabrication. They can help identify potential issues related to signal integrity, power delivery, thermal management, and mechanical stability. By using these tools, designers can make informed decisions about the selection and placement of performance-enhancing hardware, reducing the risk of costly redesigns and improving the overall performance and reliability of the PCB.
Conclusion
PCB performance-enhancing hardware plays a crucial role in optimizing the functionality, reliability, and efficiency of circuit boards. By selecting and implementing appropriate hardware components, such as decoupling capacitors, EMI shielding, thermal management solutions, connectors, and mechanical supports, designers can significantly improve the performance of their PCBs.
Effective implementation of performance-enhancing hardware requires careful consideration of electrical, mechanical, thermal, and manufacturing aspects. Proper layout techniques, simulation, and analysis tools are essential for optimizing the design and ensuring the desired performance.
As PCB designs continue to evolve, with increasing complexity and higher performance requirements, the role of performance-enhancing hardware becomes even more critical. By staying informed about the latest advancements in PCB hardware technologies and best practices, engineers can create robust, reliable, and high-performance electronic systems that meet the demanding needs of today’s applications.
No responses yet