Table of Contents
- Introduction to PCB Adhesives
- Key Applications of PCB Glue
- Component Bonding
- Conformal Coating
- Encapsulation and Potting
- Thermal Management
- Types of PCB Adhesives
- Epoxy Adhesives
- Silicone Adhesives
- Acrylic Adhesives
- Polyurethane Adhesives
- Factors to Consider When Selecting PCB Glue
- Application Methods for PCB Adhesives
- Curing Process of PCB Glue
- Advantages of Using PCB Adhesives
- Challenges and Limitations of PCB Glue
- Future Trends in PCB Adhesive Technology
- Frequently Asked Questions (FAQ)
- Conclusion
Introduction to PCB Adhesives
PCB adhesives are specially formulated materials that offer strong bonding, insulation, and protection for electronic components and circuits on printed circuit boards. These adhesives play a crucial role in ensuring the reliability, durability, and performance of electronic devices across various industries, including consumer electronics, automotive, aerospace, and medical devices.
PCB glue is available in different formulations, each with unique properties and benefits tailored to specific applications. The selection of the appropriate PCB adhesive depends on factors such as the type of components, environmental conditions, and performance requirements.
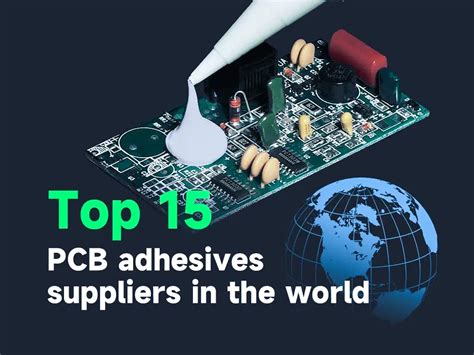
Key Applications of PCB Glue
Component Bonding
One of the primary applications of PCB adhesives is component bonding. PCB glue is used to secure electronic components, such as resistors, capacitors, and integrated circuits (ICs), to the printed circuit board. The adhesive provides a strong mechanical bond, preventing components from shifting or detaching due to vibrations, shocks, or thermal stresses.
Component bonding adhesives are available in various forms, including epoxies, silicones, and acrylics. These adhesives are chosen based on their compatibility with the components and the PCB substrate, as well as their ability to withstand the operating conditions of the device.
Conformal Coating
Conformal coating is another important application of PCB glue. In this process, a thin layer of adhesive is applied over the entire surface of the PCB, covering the components and the board itself. The primary purpose of conformal coating is to protect the PCB from environmental factors, such as moisture, dust, and chemicals, which can lead to corrosion, short circuits, and other failures.
PCB adhesives used for conformal coating are typically transparent or translucent, allowing for easy inspection of the board and components. These adhesives also have excellent dielectric properties, providing electrical insulation between components and traces.
Encapsulation and Potting
Encapsulation and potting are techniques used to provide additional protection and support for sensitive electronic components on a PCB. In these applications, PCB glue is used to completely encapsulate or “pot” the components, creating a protective barrier against environmental factors and physical damage.
Encapsulation and potting adhesives are usually two-part systems, consisting of a resin and a hardener that are mixed together before application. These adhesives have high viscosity and can fill cavities and gaps around components, providing a secure and stable enclosure.
Thermal Management
PCB adhesives also play a role in thermal management, helping to dissipate heat generated by electronic components. Thermal management is critical for maintaining the performance and longevity of electronic devices, as excessive heat can lead to component failure and reduced reliability.
Thermally conductive PCB adhesives are specifically formulated to enhance heat transfer from components to heat sinks or other cooling solutions. These adhesives often contain fillers, such as aluminum oxide or boron nitride, which improve their thermal conductivity while maintaining electrical insulation.
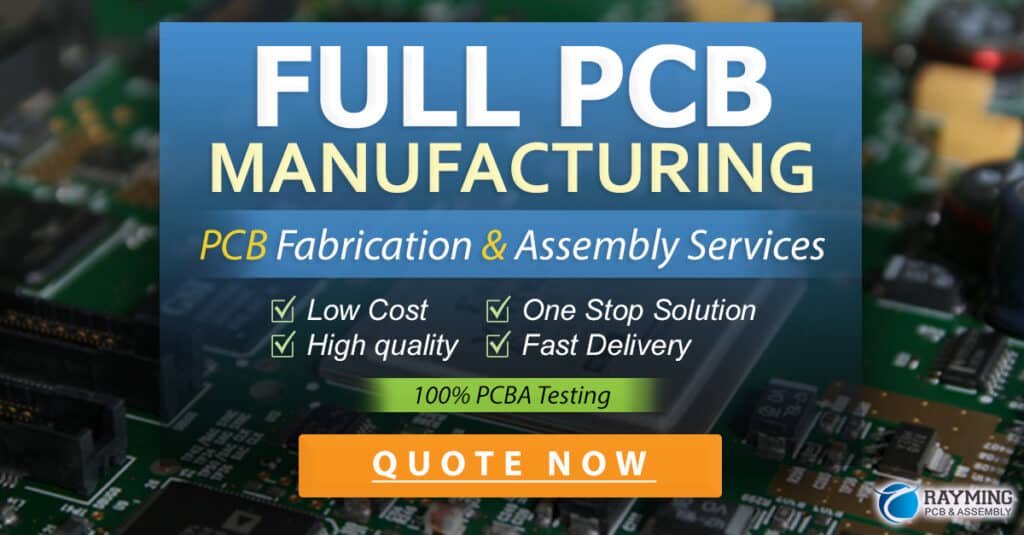
Types of PCB Adhesives
There are several types of PCB adhesives available, each with distinct properties and benefits. The choice of adhesive depends on the specific application, performance requirements, and compatibility with the PCB materials and components. Here are some of the most common types of PCB glue:
Epoxy Adhesives
Epoxy adhesives are widely used in PCB assembly due to their excellent mechanical strength, chemical resistance, and thermal stability. These adhesives are available in one-part or two-part systems, with the latter offering better performance and durability.
Epoxy adhesives cure through a polymerization reaction, forming a strong and rigid bond between the components and the PCB substrate. They are suitable for various applications, including component bonding, conformal coating, and encapsulation.
Property | Description |
---|---|
Composition | Resin and hardener |
Curing | Heat or room temperature |
Strength | High |
Thermal stability | Excellent |
Chemical resistance | Excellent |
Silicone Adhesives
Silicone adhesives are known for their flexibility, thermal stability, and resistance to moisture and chemicals. These properties make them ideal for applications that require a more flexible bond or exposure to harsh environments.
Silicone adhesives are available in various forms, including room temperature vulcanizing (RTV) and heat-curable systems. They are commonly used for conformal coating, encapsulation, and bonding of temperature-sensitive components.
Property | Description |
---|---|
Composition | Silicone polymer |
Curing | Room temperature or heat |
Flexibility | High |
Thermal stability | Excellent |
Moisture resistance | Excellent |
Acrylic Adhesives
Acrylic adhesives offer fast curing, good adhesion to various substrates, and resistance to thermal cycling. These adhesives are often used for component bonding and conformal coating applications that require quick processing times.
Acrylic adhesives cure through solvent evaporation or UV exposure, forming a strong and flexible bond. They are available in both liquid and film forms, allowing for different application methods and thicknesses.
Property | Description |
---|---|
Composition | Acrylic polymer |
Curing | Solvent evaporation or UV |
Adhesion | Good |
Thermal cycling resistance | Good |
Processing speed | Fast |
Polyurethane Adhesives
Polyurethane adhesives are known for their toughness, flexibility, and resistance to vibrations and impacts. These properties make them suitable for applications that require a durable and resilient bond, such as in automotive and aerospace electronics.
Polyurethane adhesives are available in one-part or two-part systems, with the latter offering better performance and chemical resistance. They cure through a reaction between the isocyanate and polyol components, forming a strong and flexible bond.
Property | Description |
---|---|
Composition | Isocyanate and polyol |
Curing | Room temperature or heat |
Toughness | High |
Flexibility | Good |
Vibration resistance | Excellent |
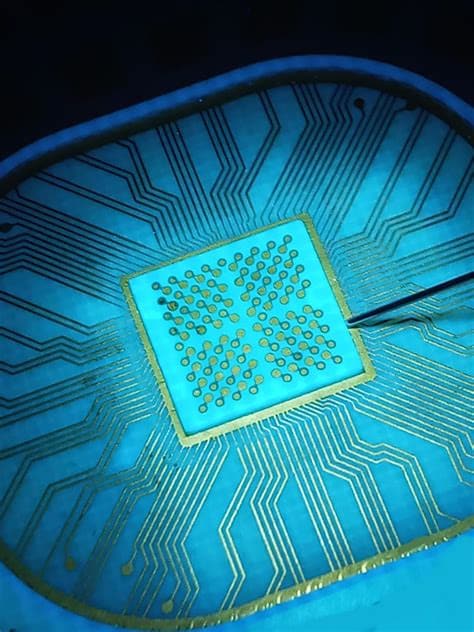
Factors to Consider When Selecting PCB Glue
When choosing a PCB adhesive for a specific application, several factors need to be considered to ensure optimal performance and reliability. These factors include:
- Compatibility with PCB materials and components
- Environmental conditions (temperature, humidity, chemicals)
- Performance requirements (strength, flexibility, thermal conductivity)
- Curing method and processing time
- Viscosity and application method
- Electrical properties (insulation, dielectric strength)
- Regulatory compliance (RoHS, REACH, UL)
By carefully evaluating these factors, engineers and manufacturers can select the most appropriate PCB glue for their specific needs, ensuring the long-term reliability and performance of the electronic device.
Application Methods for PCB Adhesives
PCB adhesives can be applied using various methods, depending on the adhesive type, viscosity, and the specific application requirements. Some common application methods include:
-
Dispensing: Adhesives are applied using automated or manual dispensing equipment, such as syringe dispensers or valve dispensers. This method allows for precise control over the amount and placement of the adhesive.
-
Screen printing: A stencil or screen is used to apply a uniform layer of adhesive onto the PCB surface. This method is suitable for conformal coating and solder mask applications.
-
Spraying: Adhesives with low viscosity can be applied using spray equipment, which atomizes the material and deposits a thin, even layer onto the PCB. This method is often used for conformal coating.
-
Dipping: The PCB is dipped into a tank containing the adhesive, coating the entire surface. This method is suitable for conformal coating and encapsulation applications.
-
Brushing: A brush or applicator is used to manually apply the adhesive onto the PCB surface. This method is suitable for small-scale or repair applications.
The choice of application method depends on factors such as the adhesive viscosity, the desired thickness, the level of automation, and the production volume.
Curing Process of PCB Glue
After application, PCB adhesives need to undergo a curing process to achieve their final properties and form a strong bond. The curing process varies depending on the type of adhesive and the specific formulation. Common curing methods include:
-
Room temperature curing: Some adhesives, such as RTV silicones and certain epoxies, can cure at room temperature through a chemical reaction or solvent evaporation.
-
Heat curing: Many PCB adhesives require elevated temperatures to initiate and complete the curing process. Heat curing can be achieved using ovens, hot plates, or inline heating systems.
-
UV curing: Adhesives formulated with UV-sensitive compounds can be cured by exposure to ultraviolet light. This method allows for fast curing and is suitable for applications that require quick processing times.
-
Moisture curing: Some adhesives, particularly polyurethanes, cure through a reaction with ambient moisture. This curing method is suitable for applications where heat or UV curing is not feasible.
The curing process is critical for achieving the desired mechanical, thermal, and electrical properties of the PCB adhesive. Proper curing conditions, such as temperature, duration, and humidity, must be maintained to ensure optimal performance and reliability.
Advantages of Using PCB Adhesives
The use of PCB adhesives offers several advantages over traditional assembly methods, such as mechanical fastening or soldering. Some of the key benefits include:
-
Strong and durable bonding: PCB adhesives provide excellent adhesion to various substrates, ensuring a secure and reliable bond between components and the PCB.
-
Improved reliability: Adhesives protect components and circuits from environmental factors, such as moisture, dust, and chemicals, enhancing the overall reliability of the electronic device.
-
Reduced mechanical stress: Flexible adhesives, such as silicones and polyurethanes, can absorb vibrations and shocks, reducing mechanical stress on components and solder joints.
-
Enhanced thermal management: Thermally conductive adhesives facilitate heat dissipation from components, improving the thermal performance and longevity of the device.
-
Simplified assembly process: Adhesives can be easily applied using automated or manual methods, streamlining the PCB assembly process and reducing labor costs.
-
Miniaturization: Adhesives enable the use of smaller components and tighter packaging, allowing for the design of more compact and lightweight electronic devices.
-
Insulation and protection: PCB adhesives provide electrical insulation and protection against short circuits, ensuring the proper functioning of the electronic device.
Challenges and Limitations of PCB Glue
Despite the numerous advantages of PCB adhesives, there are also some challenges and limitations to consider:
-
Material compatibility: Not all adhesives are compatible with every PCB material or component. Careful selection is required to ensure proper adhesion and avoid adverse reactions.
-
Curing requirements: Some adhesives require specific curing conditions, such as elevated temperatures or UV exposure, which may not be feasible for all applications or manufacturing processes.
-
Rework and repair: Bonded components can be difficult to remove or replace without damaging the PCB or adjacent components. Specialized techniques and tools may be required for rework and repair.
-
Shelf life and storage: PCB adhesives have a limited shelf life and may require specific storage conditions to maintain their performance and usability.
-
Cost: Specialized PCB adhesives can be more expensive than traditional assembly methods, such as soldering or mechanical fastening.
-
Skill and training: Proper application and curing of PCB adhesives require skilled operators and appropriate training to ensure consistent and reliable results.
Addressing these challenges and limitations requires careful planning, material selection, and process optimization to ensure the successful implementation of PCB adhesives in electronic device manufacturing.
Future Trends in PCB Adhesive Technology
As electronic devices continue to evolve and become more complex, the demand for advanced PCB adhesive solutions is expected to grow. Some of the future trends in PCB adhesive technology include:
-
Eco-friendly and sustainable adhesives: The development of adhesives with reduced environmental impact, such as bio-based or recyclable materials, will become increasingly important to meet regulatory requirements and customer demands.
-
High-performance adhesives: Adhesives with enhanced thermal, electrical, and mechanical properties will be needed to support the growing demands of advanced electronic applications, such as 5G, IoT, and electric vehicles.
-
Nanomaterial-based adhesives: The incorporation of nanomaterials, such as carbon nanotubes or graphene, into PCB adhesives can offer improved thermal conductivity, electrical conductivity, and mechanical strength.
-
Flexible and stretchable adhesives: The rise of flexible and wearable electronics will drive the development of adhesives that can accommodate bending, stretching, and twisting without compromising performance or reliability.
-
Automated application and curing processes: Advancements in dispensing, printing, and curing technologies will enable faster, more precise, and cost-effective application of PCB adhesives, improving manufacturing efficiency and quality.
As PCB adhesive technology continues to advance, collaboration between adhesive manufacturers, PCB designers, and electronic device manufacturers will be essential to address the evolving challenges and opportunities in the industry.
Frequently Asked Questions (FAQ)
- What is the difference between a one-part and two-part PCB adhesive?
-
One-part adhesives consist of a single component that cures through exposure to heat, moisture, or UV light. Two-part adhesives consist of a resin and a hardener that are mixed together before application, offering better performance and durability.
-
How do I select the right PCB adhesive for my application?
-
When selecting a PCB adhesive, consider factors such as the PCB materials, components, environmental conditions, performance requirements, curing method, and processing time. Consult with adhesive manufacturers or experienced engineers to determine the most suitable adhesive for your specific application.
-
Can PCB adhesives be used for rework or repair?
-
Rework and repair of bonded components can be challenging, as the adhesive bond may be difficult to break without damaging the PCB or adjacent components. Specialized techniques, such as localized heating or solvent application, may be required for successful rework or repair.
-
Are PCB adhesives electrically conductive?
-
Most PCB adhesives are designed to be electrically insulating to prevent short circuits and ensure proper functioning of the electronic device. However, some specialized adhesives, such as conductive epoxies, are formulated to provide electrical conductivity for specific applications.
-
How long do PCB adhesives take to cure?
- The curing time of PCB adhesives varies depending on the type of adhesive and the curing method employed. Some adhesives, such as UV-curable or snap-cure epoxies, can cure within seconds or minutes, while others, such as room temperature vulcanizing (RTV) silicones, may take several hours or days to fully cure.
Conclusion
PCB adhesives play a crucial role in the assembly and reliability of modern electronic devices. With a wide range of applications, from component bonding and conformal coating to encapsulation and thermal management, PCB glue offers numerous advantages over traditional assembly methods.
The selection of the appropriate PCB adhesive depends on various factors, including material compatibility, environmental conditions, performance requirements, and processing constraints. As electronic devices continue to advance, the development of new and improved PCB adhesive solutions will be essential to meet the evolving challenges and opportunities in the industry.
By
No responses yet