Introduction to PCB Troubleshooting
Printed Circuit Boards (PCBs) are the backbone of modern electronics. They provide a platform for mounting and interconnecting electronic components to create complex circuits and systems. However, despite advancements in PCB design and manufacturing, problems can still arise during the production and operation of these boards. Effective PCB troubleshooting is essential for identifying and resolving these issues to ensure the proper functioning of electronic devices.
In this comprehensive guide, we will delve into the world of PCB troubleshooting, exploring common problems encountered in PCB electronics and providing practical solutions to address them. Whether you are an electronics enthusiast, a technician, or an engineer, understanding the fundamentals of PCB troubleshooting will empower you to diagnose and fix issues efficiently, saving time and resources.
Common PCB Problems and Their Causes
PCB problems can manifest in various forms, ranging from manufacturing defects to component failures. Let’s explore some of the most common PCB problems and their underlying causes:
Short Circuits
Short circuits occur when two or more points on a PCB that should not be connected electrically come into contact with each other. This can happen due to various reasons:
- Solder bridges: Excessive solder or improper soldering techniques can cause solder to bridge adjacent pads or traces.
- Conductive debris: Tiny metal particles or conductive contaminants on the PCB surface can create unintended connections.
- Damaged insulation: Cracks, scratches, or wear in the solder mask or other insulating materials can expose conductive layers, leading to shorts.
Open Circuits
Open circuits happen when there is a break in the electrical path, preventing current from flowing through the intended route. Common causes include:
- Broken traces: Physical damage, such as cracks or cuts in the copper traces, can disrupt the electrical continuity.
- Poor solder joints: Insufficient solder, cold solder joints, or lifted pads can result in open circuits.
- Damaged components: Faulty or improperly installed components can cause breaks in the circuit.
Component Failures
Component failures are another prevalent issue in PCB electronics. They can be caused by:
- Overheating: Excessive heat generated by components or inadequate heat dissipation can lead to premature failure.
- Electrostatic discharge (ESD): Uncontrolled static electricity can damage sensitive electronic components.
- Overcurrent: Excessive current flowing through components beyond their rated specifications can cause permanent damage.
- Manufacturing defects: Faulty components or improper assembly during the manufacturing process can result in failures.
Signal Integrity Issues
Signal integrity problems arise when the quality and timing of electrical signals are compromised. These issues can be attributed to:
- Crosstalk: Unwanted coupling of signals between adjacent traces or layers can introduce noise and distortion.
- Reflections: Impedance mismatches or improper termination can cause signal reflections, leading to signal degradation.
- Electromagnetic interference (EMI): External electromagnetic fields can induce noise and interfere with the proper functioning of the PCB.
PCB Troubleshooting Techniques and Tools
To effectively troubleshoot PCB problems, it is essential to have a systematic approach and the right tools at your disposal. Let’s explore some key techniques and tools used in PCB troubleshooting:
Visual Inspection
The first step in PCB troubleshooting is a thorough visual inspection of the board. Look for obvious defects such as:
- Solder bridges or cold solder joints
- Damaged traces or pads
- Misaligned or missing components
- Burnt or discolored components
- Foreign objects or contaminants on the PCB surface
A magnifying glass or microscope can aid in identifying small defects that may not be visible to the naked eye.
Continuity Testing
Continuity testing helps verify the electrical connection between two points on a PCB. It is particularly useful for identifying open circuits and short circuits. A multimeter set to the continuity or resistance mode can be used to perform this test. By placing the multimeter probes on the desired points, you can determine if there is a continuous path or a break in the circuit.
Power Supply Testing
Ensuring a stable and accurate power supply is crucial for the proper functioning of a PCB. Use a multimeter to measure the voltage levels at various points on the board, such as the power input, voltage regulator outputs, and ground points. Compare the measured values with the expected values specified in the schematic or datasheet. Any discrepancies may indicate power supply issues that need to be addressed.
Signal Tracing
Signal tracing involves following the path of a signal through the PCB to identify any anomalies or disruptions. An oscilloscope is a valuable tool for visualizing and analyzing electrical signals in real-time. By probing different points along the signal path, you can observe waveforms, measure signal levels, and detect any distortions or noise.
Thermal Imaging
Thermal imaging cameras can help identify hot spots on a PCB, indicating components that are generating excessive heat. Overheating can lead to component failures and potential damage to the board. By identifying the source of the heat, you can take corrective actions such as improving heat dissipation, replacing faulty components, or optimizing the PCB layout.
In-Circuit Testing (ICT)
In-circuit testing involves using specialized equipment to test individual components on a PCB while they are still connected to the board. ICT systems can perform various tests, including component value verification, open/short circuit detection, and functional testing. This technique is particularly useful for identifying faulty components or assembly issues in mass-produced PCBs.
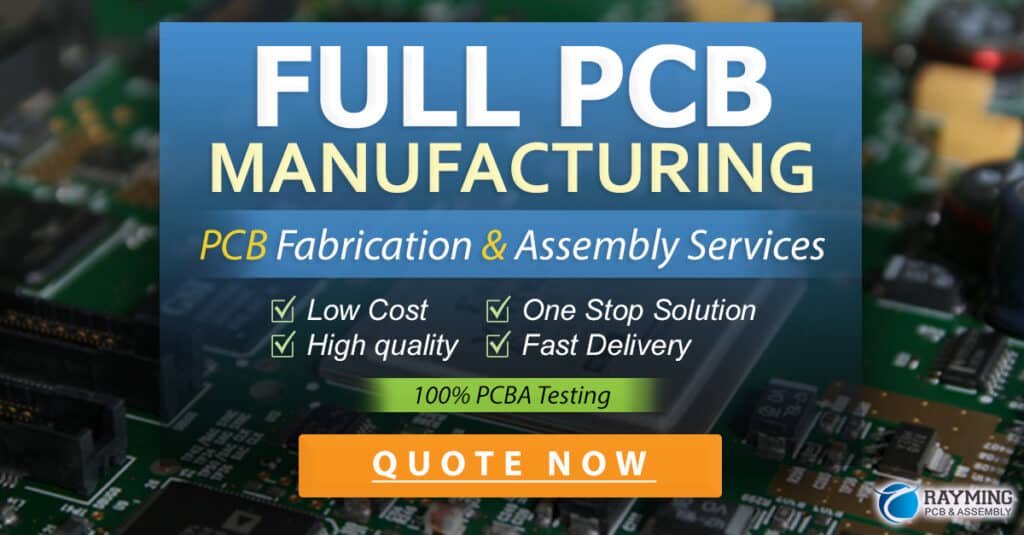
Troubleshooting Specific PCB Problems
Now that we have covered the common PCB problems and general troubleshooting techniques, let’s dive into specific scenarios and their solutions:
Short Circuit Troubleshooting
When dealing with short circuits, follow these steps:
- Identify the affected area: Use visual inspection and continuity testing to locate the short circuit.
- Isolate the short: Disconnect power and any connected components to prevent further damage.
- Clean the area: Remove any solder bridges, conductive debris, or contaminants using solder wick, a solder sucker, or appropriate cleaning solutions.
- Repair the damage: If traces or pads are damaged, use jumper wires or perform trace repair using conductive ink or copper tape.
- Retest: Verify the continuity and functionality of the repaired area.
Open Circuit Troubleshooting
To troubleshoot open circuits:
- Locate the break: Use visual inspection and continuity testing to identify the location of the open circuit.
- Check solder joints: Inspect solder joints for insufficient solder, cold joints, or lifted pads. Resolder if necessary.
- Repair traces: If traces are broken, use jumper wires or perform trace repair using conductive ink or copper tape.
- Replace components: If a component is causing the open circuit, replace it with a known good component.
- Retest: Verify the continuity and functionality of the repaired area.
Component Failure Troubleshooting
When troubleshooting component failures:
- Identify the faulty component: Use visual inspection, thermal imaging, or in-circuit testing to locate the failed component.
- Check component specifications: Verify that the component is within its rated operating conditions (voltage, current, temperature).
- Replace the component: Desolder the faulty component and replace it with a known good one, ensuring proper orientation and soldering.
- Investigate the root cause: Determine what caused the component failure (e.g., overheating, ESD, overcurrent) and take preventive measures.
- Retest: Verify the functionality of the replaced component and the overall PCB.
Signal Integrity Troubleshooting
To address signal integrity issues:
- Identify the affected signals: Use an oscilloscope to observe and analyze the problematic signals.
- Check for crosstalk: Ensure adequate spacing between sensitive traces and use ground planes or shielding techniques to minimize crosstalk.
- Verify impedance matching: Ensure proper termination and impedance matching to reduce reflections and signal distortions.
- Minimize EMI: Use proper grounding, shielding, and filtering techniques to reduce the impact of electromagnetic interference.
- Optimize PCB layout: Review and optimize the PCB layout to minimize signal integrity issues, considering factors such as trace routing, layer stackup, and component placement.
Preventive Measures and Best Practices
While troubleshooting is essential, preventing PCB problems from occurring in the first place is equally important. Here are some preventive measures and best practices to minimize the likelihood of PCB issues:
Robust PCB Design
- Follow PCB design guidelines and industry standards to ensure proper signal integrity, power distribution, and thermal management.
- Use appropriate trace widths, spacing, and impedance control techniques to minimize crosstalk and reflections.
- Incorporate necessary protection circuitry, such as ESD protection and overcurrent protection, to safeguard sensitive components.
- Conduct thorough design reviews and simulations to identify and address potential issues before manufacturing.
Quality Manufacturing Processes
- Choose reputable PCB manufacturers with strict quality control processes and certifications.
- Ensure proper handling, storage, and transportation of PCBs to prevent physical damage or contamination.
- Implement automated optical inspection (AOI) and X-ray inspection to detect manufacturing defects early in the process.
- Perform rigorous testing and burn-in procedures to identify and weed out faulty boards before they reach the end-user.
Proper Handling and Assembly
- Follow electrostatic discharge (ESD) precautions when handling PCBs and components to prevent static damage.
- Use appropriate soldering techniques and materials to ensure reliable solder joints and avoid solder bridges or cold joints.
- Implement proper component placement and orientation procedures to prevent misaligned or reversed components.
- Conduct visual inspections and functional tests after assembly to catch any issues before final integration.
Regular Maintenance and Monitoring
- Establish regular maintenance schedules to inspect and clean PCBs, ensuring they are free from dust, debris, or contaminants.
- Monitor operating conditions such as temperature, humidity, and vibration to ensure they are within acceptable ranges.
- Implement diagnostic and self-test routines in the firmware to detect and report any anomalies or failures during operation.
- Keep detailed records of maintenance activities, failures, and repairs to identify patterns and implement proactive measures.
Frequently Asked Questions (FAQ)
1. What are the most common causes of short circuits on a PCB?
The most common causes of short circuits on a PCB include solder bridges, conductive debris, and damaged insulation. Solder bridges occur when excessive solder connects adjacent pads or traces unintentionally. Conductive debris, such as tiny metal particles, can create unintended connections. Damaged insulation, like cracks or scratches in the solder mask, can expose conductive layers and lead to shorts.
2. How can I identify a faulty component on a PCB?
To identify a faulty component on a PCB, you can use various techniques such as visual inspection, thermal imaging, and in-circuit testing. Visual inspection involves looking for signs of damage, discoloration, or deformation on the component. Thermal imaging can help identify components that are generating excessive heat, indicating potential failure. In-circuit testing allows you to test individual components while they are still connected to the board, helping pinpoint faulty components.
3. What tools do I need for PCB troubleshooting?
Essential tools for PCB troubleshooting include a multimeter for continuity and voltage testing, an oscilloscope for signal analysis, a soldering iron and solder wick for repairs, tweezers and magnifying glass for handling small components, and a thermal imaging camera for detecting hot spots. Additionally, having access to the PCB schematic, layout files, and component datasheets can greatly aid in the troubleshooting process.
4. How can I prevent signal integrity issues on a PCB?
To prevent signal integrity issues on a PCB, consider the following best practices:
– Ensure proper trace routing and spacing to minimize crosstalk.
– Use appropriate impedance matching and termination techniques to reduce reflections.
– Implement ground planes and shielding to minimize electromagnetic interference (EMI).
– Follow PCB design guidelines for signal integrity, considering factors such as trace width, layer stackup, and component placement.
– Conduct thorough simulations and analysis to identify and address potential signal integrity problems early in the design phase.
5. What are some preventive measures to minimize PCB failures?
Preventive measures to minimize PCB failures include:
– Following robust PCB design practices, such as proper signal integrity, power distribution, and thermal management.
– Choosing reputable PCB manufacturers with strict quality control processes.
– Implementing automated optical inspection (AOI) and X-ray inspection to detect manufacturing defects.
– Following proper handling and assembly procedures, including ESD precautions and soldering techniques.
– Establishing regular maintenance schedules to inspect and clean PCBs.
– Monitoring operating conditions and implementing diagnostic routines to detect anomalies early.
– Keeping detailed records of failures and repairs to identify patterns and implement proactive measures.
Conclusion
PCB troubleshooting is an essential skill for anyone involved in electronics design, manufacturing, or maintenance. By understanding common PCB problems, their causes, and employing effective troubleshooting techniques, you can quickly identify and resolve issues, minimizing downtime and ensuring the reliable operation of electronic systems.
Remember to approach PCB troubleshooting systematically, using visual inspection, continuity testing, power supply testing, signal tracing, thermal imaging, and in-circuit testing as necessary. Utilize the right tools and follow best practices to isolate and repair faults efficiently.
Prevention is equally important, so prioritize robust PCB design, quality manufacturing processes, proper handling and assembly, and regular maintenance to minimize the occurrence of PCB problems. By combining proactive measures with effective troubleshooting skills, you can ensure the long-term reliability and performance of your PCB-based electronic devices.
Embrace the art of PCB troubleshooting, continually expand your knowledge, and stay updated with the latest techniques and technologies in the field. With practice and perseverance, you will become proficient in diagnosing and resolving PCB issues, contributing to the success of your electronic projects.
No responses yet