What are PCB Drill Sizes?
PCB (Printed Circuit Board) drill sizes refer to the diameters of the holes drilled into a PCB to accommodate components, vias, and mounting points. These holes are essential for creating electrical connections and securing components to the board. Understanding PCB drill sizes is crucial for designing and manufacturing reliable and functional PCBs.
Common PCB Drill Sizes
PCB drill sizes are typically measured in inches or millimeters. Some of the most common PCB drill sizes include:
Drill Size (Inch) | Drill Size (mm) | Application |
---|---|---|
0.0135″ | 0.343 mm | Small vias, fine-pitch components |
0.020″ | 0.508 mm | Standard vias, small component leads |
0.031″ | 0.787 mm | Larger vias, component leads |
0.040″ | 1.016 mm | Power vias, connectors, mounting holes |
0.125″ | 3.175 mm | Large mounting holes, high-current vias |
These drill sizes are just a small sample of the available options. The specific drill sizes used in a PCB design will depend on the components, desired electrical characteristics, and manufacturing capabilities.
Factors Affecting PCB Drill Size Selection
When selecting PCB drill sizes, several factors must be considered to ensure proper functionality and manufacturability of the PCB.
Component Requirements
The drill sizes used in a PCB design are primarily determined by the components that will be mounted on the board. Each component has specific lead or pin sizes that require corresponding hole diameters. For example, a through-hole resistor may require a 0.8 mm drill size, while a power connector may need a larger 3.0 mm hole.
Via Size and Spacing
Vias are small holes drilled in a PCB to create electrical connections between layers. The size of the vias depends on the current carrying requirements and the available space on the board. Smaller vias allow for higher density designs but may have limitations in terms of current carrying capacity and manufacturability.
Manufacturing Capabilities
The manufacturing capabilities of the PCB fabricator also play a role in drill size selection. Some manufacturers may have limitations on the minimum drill size they can produce reliably. It is essential to consult with the fabricator to ensure that the selected drill sizes are within their capabilities.
Cost Considerations
Smaller drill sizes and higher hole densities can increase the manufacturing cost of a PCB. This is because smaller drill bits are more prone to wear and breakage, requiring more frequent replacement. Additionally, higher hole densities may require more precise and expensive drilling equipment.
PCB Drill Size Standards
To ensure compatibility and reliability, the PCB industry has established standards for drill sizes. These standards provide guidelines for selecting appropriate drill sizes based on the specific requirements of the PCB design.
IPC Standards
The IPC (Association Connecting Electronics Industries) is a global trade association that develops standards for the electronic interconnection industry. The IPC-6012 standard, “Qualification and Performance Specification for Rigid Printed Boards,” provides guidelines for PCB drill sizes and tolerances.
According to IPC-6012, the minimum drill size for plated through holes is 0.20 mm (0.008 in), and the minimum drill size for non-plated through holes is 0.35 mm (0.014 in). The standard also specifies the tolerances for drill sizes based on the hole diameter and the PCB thickness.
Metric vs. Imperial Drill Sizes
PCB drill sizes can be expressed in either metric (mm) or imperial (inch) units. While metric sizes are more common in Europe and Asia, imperial sizes are still widely used in North America.
When working with drill sizes, it is essential to ensure consistency in the units used throughout the design and manufacturing process to avoid confusion and errors.
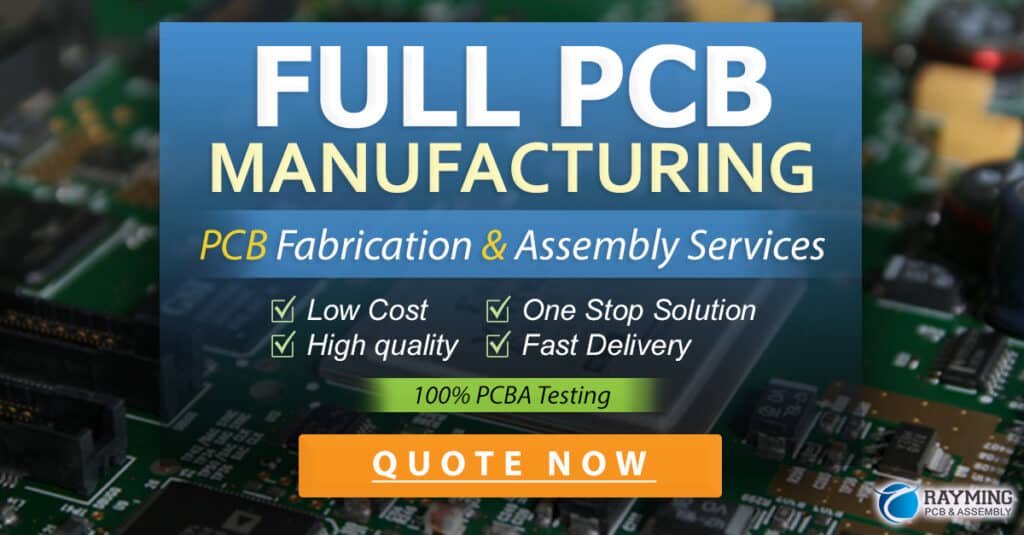
PCB Drill Size Tolerances
In addition to selecting the appropriate drill sizes, it is crucial to consider the tolerances associated with each size. Drill size tolerances specify the acceptable range of variation in the hole diameter.
Importance of Drill Size Tolerances
Drill size tolerances are important for several reasons:
-
Ensuring proper fit of components: If the hole diameter is too small, the component leads may not fit, causing assembly issues. If the hole diameter is too large, the component may not be securely attached to the board.
-
Maintaining electrical integrity: Hole diameters that are too large can result in reduced electrical contact between the component lead and the plated hole wall, leading to poor electrical performance.
-
Facilitating reliable manufacturing: Tight tolerances help ensure consistent and repeatable manufacturing processes, reducing the likelihood of defects and improving overall PCB Quality.
Typical Drill Size Tolerances
The typical drill size tolerances for PCBs depend on the hole diameter and the PCB thickness. The IPC-6012 standard provides guidance on drill size tolerances for various hole sizes and board thicknesses.
For example, for a hole diameter of 0.5 mm (0.020 in) and a PCB thickness of 1.6 mm (0.063 in), the acceptable drill size tolerance is ±0.075 mm (±0.003 in).
It is essential to work closely with the PCB fabricator to ensure that the specified drill size tolerances are achievable and align with their manufacturing capabilities.
Advanced PCB Drilling Techniques
As PCB designs become more complex and miniaturized, advanced drilling techniques have been developed to accommodate smaller drill sizes and higher hole densities.
Laser Drilling
Laser drilling uses a focused laser beam to create micro-vias and small holes in PCBs. This technique allows for the creation of holes as small as 0.05 mm (0.002 in) in diameter, enabling higher density designs and finer pitch components.
Laser drilling offers several advantages over traditional mechanical drilling:
- Higher precision and accuracy
- Ability to create smaller holes
- Reduced damage to surrounding material
- Faster drilling speeds for small holes
However, laser drilling is generally more expensive than mechanical drilling and may not be suitable for all PCB materials.
Controlled Depth Drilling
Controlled depth drilling is a technique used to create blind vias, which are vias that do not extend through the entire thickness of the PCB. This technique involves using specialized drill bits and depth control systems to accurately control the depth of the drilled hole.
Controlled depth drilling allows for the creation of complex multi-layer PCB designs with improved signal integrity and reduced electromagnetic interference (EMI).
FAQ
1. What is the most common PCB drill size?
The most common PCB drill size is 0.8 mm (0.031 in), which is suitable for a wide range of through-hole components and vias.
2. Can I use any drill size for my PCB design?
While there is a wide range of drill sizes available, it is essential to select drill sizes that are appropriate for your specific components and design requirements. Consult with your PCB fabricator to ensure that your selected drill sizes are within their manufacturing capabilities.
3. What is the smallest drill size that can be used in PCB manufacturing?
The smallest drill size that can be reliably used in PCB manufacturing depends on the capabilities of the fabricator. Some advanced fabricators can produce holes as small as 0.05 mm (0.002 in) using laser drilling techniques.
4. How do I specify drill sizes in my PCB design files?
When creating PCB design files, drill sizes are typically specified in the drill file or drill table. This file contains information about the location, size, and type of each drilled hole in the PCB. It is important to use consistent units (metric or imperial) and to communicate clearly with your PCB fabricator regarding drill size requirements.
5. What are the consequences of using incorrect drill sizes in a PCB design?
Using incorrect drill sizes in a PCB design can lead to several issues, including:
- Difficulty in assembling components
- Poor electrical connections and signal integrity
- Reduced mechanical strength and reliability of the PCB
- Increased manufacturing costs and delays due to rework or scrap
To avoid these issues, it is crucial to carefully select and specify drill sizes based on the requirements of your components, design, and manufacturing process.
Conclusion
PCB drill sizes play a critical role in the design and manufacturing of reliable and high-quality printed circuit boards. By understanding the factors that influence drill size selection, industry standards, and advanced drilling techniques, PCB designers and engineers can create designs that are both functional and manufacturable.
When selecting PCB drill sizes, it is essential to consider the requirements of the components, the desired electrical characteristics, and the manufacturing capabilities of the PCB fabricator. Adhering to industry standards and communicating clearly with the fabricator can help ensure a smooth and successful PCB manufacturing process.
As PCB technology continues to evolve, staying up-to-date with the latest drilling techniques and best practices will be crucial for designing and manufacturing cutting-edge electronic devices.
No responses yet