Introduction to PCB Analog Design
Designing printed circuit boards (PCBs) for analog circuits requires a different approach compared to digital circuits. Analog signals are sensitive to noise, crosstalk, and other disturbances that can affect the overall performance of the system. Therefore, it is crucial to follow specific design rules and guidelines to ensure the integrity of the analog signals and minimize the impact of unwanted effects.
In this article, we will explore the key considerations and best practices for designing PCBs for analog circuits. We will cover topics such as component placement, signal routing, power distribution, grounding, shielding, and more. By understanding and applying these design rules, you can create robust and reliable analog PCBs that meet your performance requirements.
Importance of Proper PCB Layout in Analog Design
The layout of a PCB plays a critical role in the performance of analog circuits. Unlike digital circuits, which are more tolerant to noise and disturbances, analog circuits are highly sensitive to these factors. Poor PCB layout can introduce unwanted coupling between signals, create ground loops, and degrade the signal-to-noise ratio (SNR) of the system.
Proper PCB layout involves careful consideration of component placement, signal routing, power distribution, and grounding. By optimizing these aspects, you can minimize the impact of noise, crosstalk, and other disturbances on the analog signals. This, in turn, leads to improved system performance, higher accuracy, and better overall reliability.
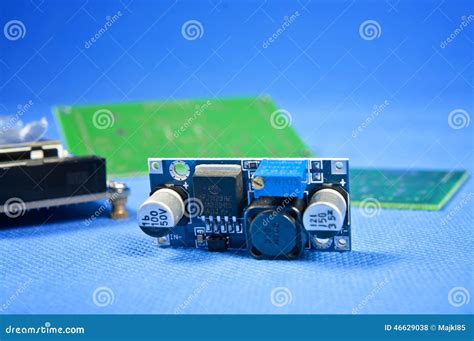
Key Considerations for Analog PCB Design
When designing PCBs for analog circuits, there are several key considerations to keep in mind. These include:
-
Component Placement: The placement of components on the PCB is crucial for minimizing the impact of noise and crosstalk. It is important to group related components together and keep sensitive analog components away from noisy digital components.
-
Signal Routing: Proper signal routing is essential for maintaining signal integrity and minimizing crosstalk. Analog signals should be routed away from noisy digital traces, and sensitive traces should be kept as short as possible.
-
Power Distribution: A clean and stable power supply is critical for analog circuits. It is important to provide separate power and ground planes for analog and digital sections of the PCB and use appropriate decoupling capacitors to minimize power supply noise.
-
Grounding: Proper grounding is essential for minimizing ground loops and reducing noise in analog circuits. It is important to use a single-point ground scheme and avoid creating ground loops between different sections of the PCB.
-
Shielding: Shielding sensitive analog components and traces can help reduce the impact of external noise and interference. This can be achieved through the use of grounded copper pours, shielding cans, or other shielding techniques.
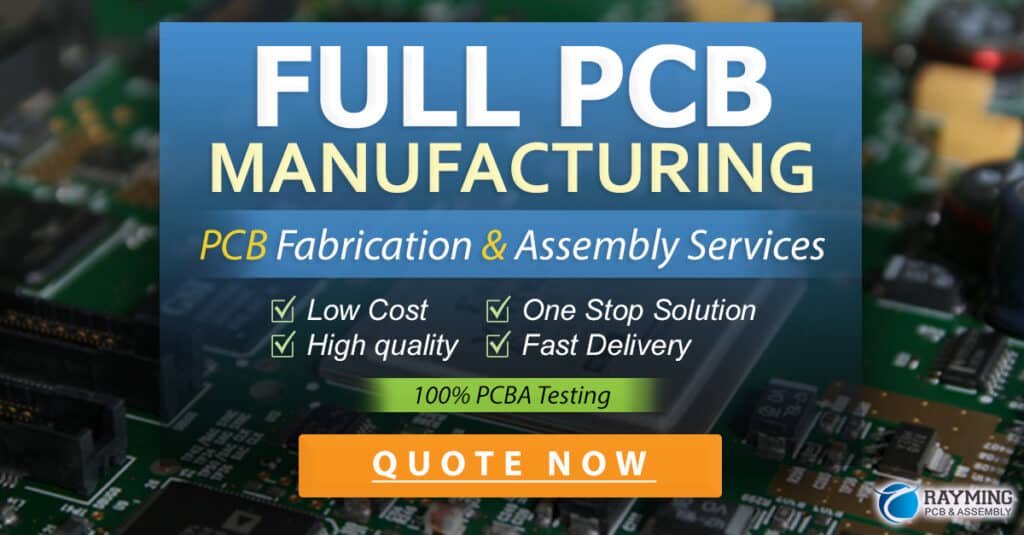
Best Practices for Component Placement
Proper component placement is critical for minimizing noise and crosstalk in analog circuits. Here are some best practices to follow:
-
Group Related Components: Place related components, such as amplifiers, filters, and ADCs/DACs, close together to minimize the length of sensitive traces and reduce the impact of noise and crosstalk.
-
Separate Analog and Digital Sections: Physically separate the analog and digital sections of the PCB to minimize the coupling of digital noise into sensitive analog circuits. Use separate power and ground planes for each section.
-
Keep Sensitive Components Away from Noisy Components: Place sensitive analog components, such as high-gain amplifiers and precision references, away from noisy digital components, such as microcontrollers and switching regulators.
-
Minimize Component Height: Use low-profile components whenever possible to reduce the height of the PCB and minimize the impact of electromagnetic interference (EMI).
-
Consider Thermal Management: Place power-dissipating components, such as voltage regulators and power amplifiers, away from temperature-sensitive components to minimize thermal gradients across the PCB.
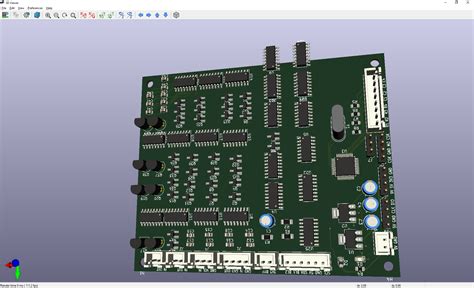
Signal Routing Techniques for Analog PCBs
Proper signal routing is essential for maintaining signal integrity and minimizing crosstalk in analog circuits. Here are some techniques to follow:
-
Keep Traces Short: Keep sensitive analog traces as short as possible to minimize the impact of noise and crosstalk. Use direct routing paths whenever possible.
-
Avoid Routing Analog Traces Near Digital Traces: Route analog traces away from noisy digital traces to minimize coupling. If crossing is unavoidable, use perpendicular crossings to minimize the coupling area.
-
Use Differential Signaling: Use differential signaling for sensitive analog signals to improve noise immunity and reduce the impact of ground noise.
-
Provide Adequate Spacing: Provide adequate spacing between analog traces and other traces to minimize crosstalk. The spacing should be based on the signal frequency and the dielectric constant of the PCB material.
-
Use Ground Planes: Use continuous ground planes beneath sensitive analog traces to provide a low-impedance return path and minimize the impact of ground noise.
Power Distribution and Decoupling
A clean and stable power supply is critical for analog circuits. Here are some best practices for power distribution and decoupling:
-
Use Separate Power and Ground Planes: Use separate power and ground planes for analog and digital sections of the PCB to minimize the coupling of digital noise into sensitive analog circuits.
-
Provide Adequate Decoupling: Use appropriate decoupling capacitors near power pins of analog components to minimize power supply noise. Use a combination of bulk and ceramic capacitors to provide low-impedance paths for high-frequency noise.
-
Use Power Supply Filtering: Use power supply filtering, such as LC filters or ferrite beads, to reduce high-frequency noise on the power supply lines.
-
Minimize Power Supply Impedance: Minimize the impedance of the power supply traces by using wide traces and multiple vias to connect to the power planes.
-
Consider Voltage Regulation: Use voltage regulators to provide a clean and stable power supply for sensitive analog components. Place the regulators close to the components they are powering.
Grounding Techniques for Analog PCBs
Proper grounding is essential for minimizing ground loops and reducing noise in analog circuits. Here are some grounding techniques to follow:
-
Use a Single-Point Ground: Use a single-point ground scheme, where all ground connections are made to a single point on the PCB. This helps minimize ground loops and reduces the impact of ground noise.
-
Separate Analog and Digital Grounds: Use separate ground planes for analog and digital sections of the PCB and connect them at a single point, preferably near the power supply.
-
Use Star Grounding: Use a star grounding scheme, where each ground connection is made to a central point, such as a ground plane or a ground bus.
-
Minimize Ground Impedance: Minimize the impedance of the ground connections by using wide traces and multiple vias to connect to the ground planes.
-
Avoid Ground Loops: Avoid creating ground loops between different sections of the PCB by ensuring that there is only one path for ground currents to flow.
Shielding Techniques for Analog PCBs
Shielding sensitive analog components and traces can help reduce the impact of external noise and interference. Here are some shielding techniques to consider:
-
Use Grounded Copper Pours: Use grounded copper pours around sensitive analog components and traces to provide a low-impedance path for high-frequency noise and reduce the impact of EMI.
-
Use Shielding Cans: Use shielding cans or enclosures to completely enclose sensitive analog components and provide additional shielding against external noise and interference.
-
Use Guard Rings: Use guard rings around sensitive analog traces to provide a low-impedance path for noise currents and reduce the impact of crosstalk.
-
Use Shielded Cables: Use shielded cables for off-board connections to sensitive analog components to reduce the impact of external noise and interference.
-
Consider Faraday Cages: Consider using Faraday cages to completely enclose sensitive analog sections of the PCB and provide the ultimate protection against external noise and interference.
PCB Material Selection for Analog Circuits
The choice of PCB material can have a significant impact on the performance of analog circuits. Here are some considerations for PCB material selection:
-
Choose Low-Loss Materials: Choose low-loss PCB materials, such as Rogers or Isola, for high-frequency analog circuits to minimize dielectric losses and improve signal integrity.
-
Consider Dielectric Constant: Consider the dielectric constant of the PCB material when designing high-frequency analog circuits. Materials with lower dielectric constants, such as PTFE or Rogers, can help reduce the impact of capacitive coupling and improve signal integrity.
-
Use High-Quality Copper: Use high-quality copper for the PCB traces to minimize resistive losses and improve signal integrity. Consider using thicker copper layers for power and ground planes to minimize impedance.
-
Consider Thermal Properties: Consider the thermal properties of the PCB material when designing power-dissipating analog circuits. Materials with higher thermal conductivity, such as aluminum or copper-clad laminates, can help dissipate heat more effectively.
-
Use Multilayer PCBs: Use multilayer PCBs for complex analog circuits to provide additional layers for power and ground planes, as well as for signal routing. This can help improve signal integrity and reduce the impact of noise and crosstalk.
Testing and Validation of Analog PCBs
Testing and validation are critical steps in the design of analog PCBs. Here are some techniques to consider:
-
Perform Signal Integrity Simulations: Perform signal integrity simulations using tools such as Hyperlynx or ADS to predict the performance of the PCB and identify potential issues before fabrication.
-
Use Power Integrity Analysis: Use power integrity analysis tools to predict the performance of the power distribution network and identify potential issues such as voltage drops or resonances.
-
Perform EMC Testing: Perform electromagnetic compatibility (EMC) testing to ensure that the PCB meets regulatory requirements and does not cause interference with other electronic devices.
-
Use Thermal Imaging: Use thermal imaging techniques to identify hot spots on the PCB and ensure that the thermal design is adequate for the power dissipation of the components.
-
Perform Functional Testing: Perform functional testing of the assembled PCB to ensure that it meets the performance requirements and functions as intended.
FAQs
-
What is the difference between analog and digital PCB design?
Analog PCB design focuses on maintaining signal integrity and minimizing noise and distortion, while digital PCB design focuses on maintaining signal integrity and minimizing crosstalk and reflections. Analog circuits are more sensitive to noise and require more careful design techniques, such as proper grounding and shielding. -
What are some common mistakes in analog PCB design?
Common mistakes in analog PCB design include improper grounding, inadequate decoupling, poor component placement, and inadequate shielding. These mistakes can lead to increased noise, distortion, and other performance issues. -
How can I minimize crosstalk in analog PCB design?
To minimize crosstalk in analog PCB design, use proper signal routing techniques, such as keeping sensitive traces away from noisy traces, using guard traces or ground planes, and providing adequate spacing between traces. Additionally, use differential signaling for sensitive analog signals and consider using shielding techniques such as grounded copper pours or shielding cans. -
What is the importance of power supply decoupling in analog PCB design?
Power supply decoupling is critical in analog PCB design to provide a clean and stable power supply for sensitive analog components. Decoupling capacitors help to minimize power supply noise and provide a low-impedance path for high-frequency noise. Inadequate decoupling can lead to increased noise and distortion in the analog signals. -
What are some common PCB materials used for analog circuits?
Common PCB materials used for analog circuits include FR-4, Rogers, Isola, and PTFE. The choice of material depends on the specific requirements of the circuit, such as the frequency range, power dissipation, and thermal properties. Low-loss materials such as Rogers or Isola are often used for high-frequency analog circuits to minimize dielectric losses and improve signal integrity.
Conclusion
Designing PCBs for analog circuits requires careful consideration of many factors, including component placement, signal routing, power distribution, grounding, and shielding. By following best practices and guidelines for each of these areas, designers can create PCBs that provide high performance, low noise, and reliable operation for analog circuits.
Some key takeaways include:
- Use separate power and ground planes for analog and digital sections of the PCB
- Use appropriate decoupling capacitors and power supply filtering to minimize power supply noise
- Use a single-point ground scheme and avoid creating ground loops
- Use shielding techniques such as grounded copper pours or shielding cans to minimize the impact of external noise and interference
- Choose low-loss PCB materials for high-frequency analog circuits to minimize dielectric losses and improve signal integrity
By following these guidelines and best practices, designers can create PCBs that provide the best possible performance for analog circuits, while minimizing noise, distortion, and other performance issues. Proper testing and validation are also critical to ensure that the PCB meets the required specifications and functions as intended.
No responses yet