Introduction to DFM in PCB design
Design for Manufacturing (DFM) is a crucial aspect of the PCB design process that ensures the manufacturability, reliability, and cost-effectiveness of the final product. By incorporating DFM principles into the design phase, engineers can avoid potential issues during manufacturing and assembly, ultimately saving time and money.
Key Benefits of Implementing DFM in PCB Design
- Reduced manufacturing costs
- Improved product quality and reliability
- Shorter time-to-market
- Enhanced collaboration between design and manufacturing teams
Essential DFM Guidelines for PCB Design
1. Component Selection and Placement
Choosing the Right Components
When selecting components for your PCB design, consider the following factors:
- Availability and lead times
- Package size and pitch
- Thermal requirements
- Electrical characteristics
Optimal Component Placement
To ensure proper manufacturability and assembly, follow these guidelines:
- Place components on one side of the board whenever possible
- Maintain adequate spacing between components for soldering and inspection
- Orient components in the same direction to facilitate automated assembly
- Avoid placing components too close to the board edges or connectors
2. Trace Routing and Spacing
Trace Width and Thickness
Determine the appropriate trace width and thickness based on the following factors:
- Current carrying capacity
- Impedance requirements
- Manufacturing capabilities
Current (A) | Trace Width (mm) |
---|---|
0.5 | 0.2 |
1.0 | 0.3 |
2.0 | 0.5 |
3.0 | 0.8 |
Trace Spacing and Clearance
Maintain sufficient spacing between traces and components to prevent short circuits and ensure proper insulation. Consider the following guidelines:
- Minimum trace-to-trace spacing: 0.2 mm
- Minimum trace-to-pad spacing: 0.25 mm
- Minimum trace-to-edge spacing: 0.5 mm
3. Vias and Through-Hole Technology
Via Types and Sizes
Choose the appropriate via type and size based on your design requirements:
- Through-hole vias
- Blind vias
- Buried vias
Via Type | Minimum Diameter (mm) |
---|---|
Through-hole | 0.5 |
Blind | 0.3 |
Buried | 0.2 |
Via Placement and Drilling
Follow these guidelines for optimal via placement and drilling:
- Place vias on a grid to simplify manufacturing
- Avoid placing vias under components or in hard-to-reach areas
- Ensure proper via-to-via and via-to-trace spacing
- Specify the correct drill sizes and tolerances
4. Solder Mask and Silkscreen
Solder Mask Design
A well-designed solder mask layer helps prevent short circuits and improves the PCB’s aesthetic appearance. Consider the following:
- Minimum solder mask web thickness: 0.1 mm
- Solder Mask Expansion around pads: 0.05 mm
- Solder mask dam between pads: 0.1 mm
Silkscreen Legibility and Placement
The silkscreen layer provides essential information for assembly and debugging. Ensure proper legibility and placement:
- Minimum silkscreen line width: 0.15 mm
- Minimum silkscreen text size: 1 mm
- Place silkscreen text and symbols away from pads and vias
5. Panelization and Breakout Tabs
Panelization for Multiple PCBs
When designing panels containing multiple PCBs, consider the following:
- Include breakout tabs or mousebites for easy separation
- Maintain consistent spacing between individual PCBs
- Add Fiducial Markers for automated assembly alignment
Breakout Tab Design
Design breakout tabs to ensure clean and easy separation of individual PCBs:
- Minimum tab width: 2 mm
- Minimum tab spacing: 3 mm
- Use V-scored or perforated tabs for easy breaking
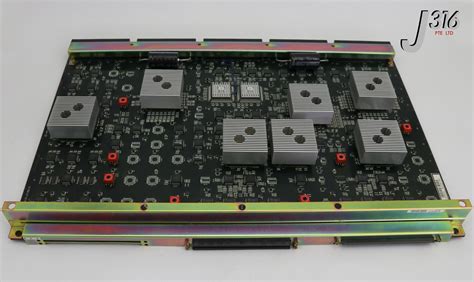
Collaborating with the Manufacturing Team
To ensure a smooth transition from design to manufacturing, maintain open communication with your manufacturing team. Share your DFM considerations and seek their input on the following aspects:
- Material selection and availability
- Manufacturing capabilities and limitations
- Assembly requirements and constraints
- Testing and quality control procedures
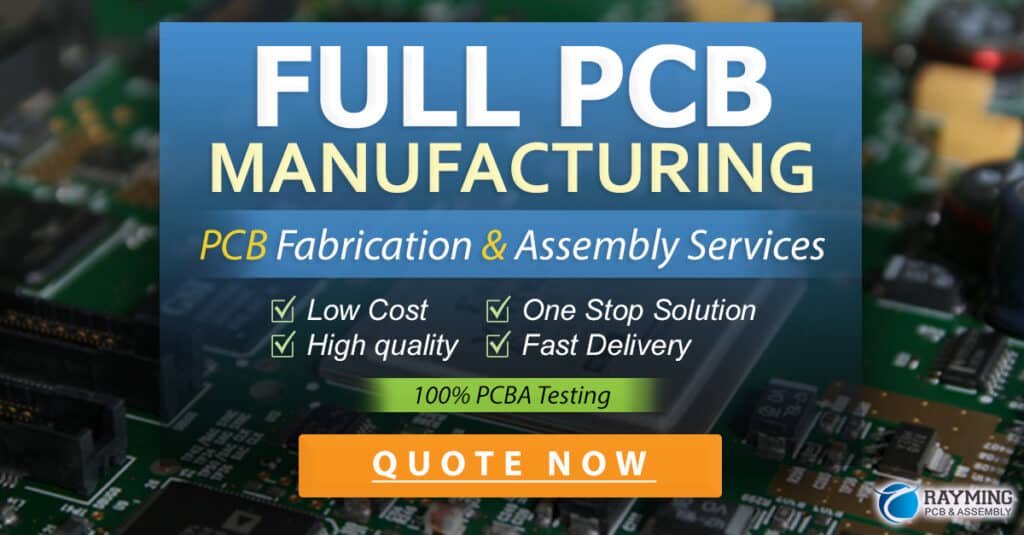
Frequently Asked Questions (FAQ)
-
Q: What is the importance of DFM in PCB design?
A: DFM helps ensure that your PCB design can be manufactured efficiently, reliably, and cost-effectively by considering the manufacturing process during the design phase. -
Q: How can I reduce manufacturing costs through DFM?
A: You can reduce manufacturing costs by selecting readily available components, optimizing component placement, and designing for automated assembly processes. -
Q: What are the key aspects to consider when choosing components for a DFM-optimized PCB?
A: When selecting components, consider their availability, package size and pitch, thermal requirements, and electrical characteristics to ensure compatibility with the manufacturing process. -
Q: How do I determine the appropriate trace width and spacing for my PCB design?
A: Trace width and spacing depend on factors such as current carrying capacity, impedance requirements, and manufacturing capabilities. Consult with your manufacturing team and refer to industry standards for guidance. -
Q: Why is collaborating with the manufacturing team important for successful DFM implementation?
A: Collaborating with the manufacturing team helps ensure that your PCB design is compatible with their capabilities, materials, and processes. Their input can help you optimize your design for manufacturability and avoid potential issues during production.
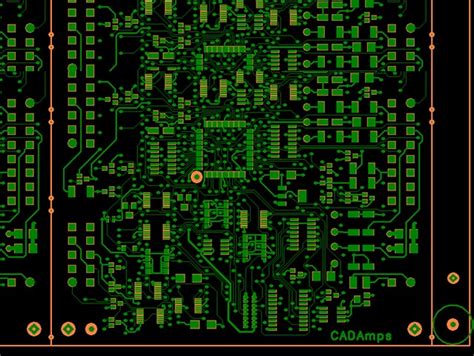
Conclusion
Incorporating DFM principles into your PCB design process is essential for creating manufacturable, reliable, and cost-effective products. By following the guidelines outlined in this article and collaborating closely with your manufacturing team, you can streamline the design-to-manufacturing transition and achieve optimal results.
Remember to consider factors such as component selection and placement, trace routing and spacing, vias and through-hole technology, solder mask and silkscreen design, and panelization and breakout tabs. By paying attention to these critical aspects and maintaining open communication with your manufacturing partners, you can ensure the success of your PCB design and manufacturing endeavors.
No responses yet