Mistake 1: Neglecting DFM (Design for Manufacturability) Principles
One of the most significant oversights in PCB design is failing to consider Design for Manufacturability (DFM) principles. DFM is a set of guidelines that ensure your PCB can be manufactured efficiently, reliably, and cost-effectively. By neglecting DFM, you risk encountering issues during the manufacturing process, leading to delays, increased costs, and potential product failures.
How to Avoid This Mistake
- Familiarize yourself with DFM guidelines provided by your PCB manufacturer.
- Consider the limitations and capabilities of the manufacturing process when designing your PCB.
- Pay attention to minimum trace widths, clearances, and drill sizes.
- Use standard component sizes and packages whenever possible.
- Incorporate testability features, such as test points and boundary scan, to facilitate testing and debugging.
DFM Guideline | Recommendation |
---|---|
Minimum Trace Width | 0.006″ (0.15mm) for standard PCBs |
Minimum Clearance | 0.006″ (0.15mm) between traces and pads |
Minimum Drill Size | 0.020″ (0.50mm) for through-hole components |
Standard Component Sizes | 0402, 0603, 0805, 1206 for SMD components |
Mistake 2: Poor Component Placement and Routing
Improper component placement and inefficient routing can lead to a host of issues, including signal integrity problems, electromagnetic interference (EMI), and thermal management challenges. These issues can compromise the performance and reliability of your PCB, resulting in costly rework or redesigns.
How to Avoid This Mistake
- Group components logically based on their function and connectivity.
- Place sensitive components, such as high-speed devices and analog circuits, away from potential sources of interference.
- Use ground planes and power planes to provide a low-impedance return path and minimize EMI.
- Route critical signals first, ensuring they have the shortest and most direct path possible.
- Avoid routing traces under components or through vias whenever possible.
Component Group | Placement Guidelines |
---|---|
Power Supply | Place near the edge of the board, close to power input |
Digital Logic | Group based on functionality and connectivity |
Analog Circuits | Place away from digital components and potential noise sources |
High-Speed Devices | Place close to connectors and route signals with controlled impedance |
Mistake 3: Ignoring Signal Integrity and EMI Considerations
Signal integrity and EMI are critical aspects of PCB design that are often overlooked. Poor signal integrity can lead to data corruption, timing issues, and intermittent failures, while EMI can cause interference with other electronic devices and violate regulatory requirements.
How to Avoid This Mistake
- Use appropriate termination techniques, such as series termination and parallel termination, to minimize reflections and improve signal quality.
- Implement differential pairs for high-speed signals to reduce crosstalk and EMI.
- Provide adequate ground plane coverage and use ground stitching vias to create a low-impedance return path.
- Follow proper grounding and shielding techniques, such as separating analog and digital grounds and using shielded connectors or enclosures.
- Perform signal integrity simulations and EMI analysis to identify and address potential issues early in the design process.
Termination Technique | Application |
---|---|
Series Termination | For point-to-point connections and short traces |
Parallel Termination | For multi-drop buses and long traces |
Differential Pairs | For high-speed signals (e.g., USB, PCIe, HDMI) |
Ground Stitching Vias | To provide a low-impedance return path and minimize ground bounce |
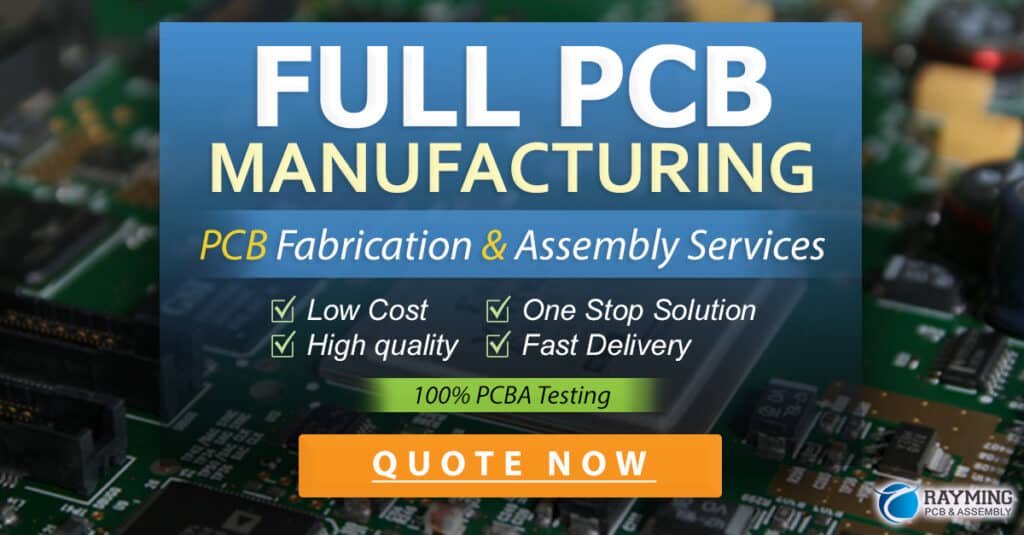
Mistake 4: Neglecting Thermal Management
Thermal management is a critical aspect of PCB design that is often overlooked. Overheating components can lead to reduced performance, reliability issues, and even complete failure. Proper thermal management ensures that your PCB operates within safe temperature limits, extending its lifespan and maintaining optimal performance.
How to Avoid This Mistake
- Identify components with high power dissipation and place them in areas with good airflow.
- Use thermal relief pads for through-hole components to improve solderability and heat dissipation.
- Incorporate thermal vias to transfer heat from components to the ground plane or dedicated thermal layers.
- Consider using heatsinks, fans, or other cooling solutions for high-power components.
- Perform thermal simulations to identify hot spots and optimize the placement of components and cooling solutions.
Component | Thermal Management Techniques |
---|---|
Power MOSFETs | Use thermal vias, heatsinks, and place in areas with good airflow |
Voltage Regulators | Use thermal relief pads, place away from heat-sensitive components |
High-Power Resistors | Use large pads, thermal vias, and place in areas with good airflow |
CPUs and FPGAs | Use heatsinks, fans, and thermal interface materials (TIMs) |
Mistake 5: Failing to Document and Version Control Your Design
Proper documentation and version control are essential for maintaining the integrity and traceability of your PCB design. Failing to document your design decisions, component selections, and layout guidelines can lead to confusion, errors, and delays in future revisions or troubleshooting efforts.
How to Avoid This Mistake
- Use a version control system, such as Git or SVN, to track changes and collaborate with team members.
- Maintain a comprehensive design document that includes component selections, design decisions, and layout guidelines.
- Use descriptive naming conventions for files, components, and nets to improve clarity and searchability.
- Generate and archive fabrication files, such as Gerber files and drill files, for each revision of your PCB.
- Keep a record of any design changes, issues, and resolutions for future reference.
Documentation | Best Practices |
---|---|
Design Document | Include component selections, design decisions, and layout guidelines |
Naming Conventions | Use descriptive names for files, components, and nets |
Version Control | Use Git or SVN to track changes and collaborate with team members |
Fabrication Files | Generate and archive Gerber files and drill files for each revision |
Frequently Asked Questions (FAQ)
Q1: What are the most common PCB design mistakes?
A1: The most common PCB design mistakes include neglecting DFM principles, poor component placement and routing, ignoring signal integrity and EMI considerations, neglecting thermal management, and failing to document and version control your design.
Q2: How can I ensure my PCB design is manufacturable?
A2: To ensure your PCB design is manufacturable, familiarize yourself with DFM guidelines provided by your PCB manufacturer, consider the limitations and capabilities of the manufacturing process, and use standard component sizes and packages whenever possible.
Q3: What are some techniques for improving signal integrity in PCB design?
A3: Some techniques for improving signal integrity in PCB design include using appropriate termination techniques, implementing differential pairs for high-speed signals, providing adequate ground plane coverage, and performing signal integrity simulations to identify and address potential issues early in the design process.
Q4: How can I manage thermal issues in my PCB design?
A4: To manage thermal issues in your PCB design, identify components with high power dissipation and place them in areas with good airflow, use thermal relief pads and thermal vias, consider using heatsinks or fans for high-power components, and perform thermal simulations to optimize the placement of components and cooling solutions.
Q5: Why is documentation and version control important in PCB design?
A5: Documentation and version control are important in PCB design because they help maintain the integrity and traceability of your design, reduce confusion and errors, and facilitate collaboration among team members. Proper documentation and version control also make it easier to troubleshoot issues and implement future revisions.
By understanding and avoiding these common PCB design mistakes, you can create more reliable, efficient, and cost-effective PCBs. Implementing best practices for DFM, component placement and routing, signal integrity, thermal management, and documentation will help ensure the success of your PCB projects and minimize the risk of costly errors or delays.
No responses yet