Introduction to mmWave and PCB Design
Millimeter wave (mmWave) frequencies, spanning from 30 GHz to 300 GHz, have gained significant attention in recent years due to their potential for high-speed wireless communications, radar applications, and imaging systems. As the demand for higher data rates and increased bandwidth continues to grow, mmWave technology has emerged as a promising solution. However, designing printed circuit boards (PCBs) for mmWave applications presents unique challenges that require careful consideration.
In this article, we will explore the key PCB design considerations for mmWave frequencies, including material selection, Transmission Line Design, signal integrity, power integrity, and manufacturing techniques. By understanding and addressing these critical aspects, engineers can optimize their PCB designs to ensure reliable and efficient operation at mmWave frequencies.
Advantages of mmWave Technology
- Higher bandwidth and data rates
- Smaller antenna sizes
- Increased spectrum availability
- Improved spatial resolution for radar and imaging
Challenges in mmWave PCB Design
- Higher losses and attenuation
- Increased sensitivity to manufacturing tolerances
- Greater impact of parasitic effects
- Stringent signal and power integrity requirements
Material Selection for mmWave PCBs
Substrate Materials
When designing PCBs for mmWave frequencies, the choice of substrate material is crucial. The substrate must exhibit low dielectric losses, stable properties over temperature, and consistent performance at high frequencies. Some commonly used substrate materials for mmWave PCBs include:
Material | Dielectric Constant (Dk) | Loss Tangent (Df) |
---|---|---|
Rogers RO3003 | 3.0 | 0.0013 @ 10 GHz |
Rogers RO4350B | 3.48 | 0.0037 @ 10 GHz |
Isola Astra MT77 | 3.0 | 0.0017 @ 10 GHz |
PTFE (Teflon) | 2.1 | 0.0002 @ 10 GHz |
It is essential to consider the dielectric constant (Dk) and loss tangent (Df) of the substrate material when making a selection. A lower Dk value results in faster signal propagation, while a lower Df value indicates lower dielectric losses. PTFE (Teflon) is an excellent choice for mmWave PCBs due to its low loss tangent, but it can be more expensive and challenging to manufacture compared to other materials.
Copper Foil Thickness
The thickness of the copper foil used in mmWave PCBs is another important consideration. Thinner copper foils are preferred to minimize conductor losses and improve high-frequency performance. Typical copper foil thicknesses for mmWave PCBs range from 0.5 oz to 1 oz (17 μm to 35 μm). However, thinner copper foils can increase manufacturing complexity and cost.
Transmission Line Design for mmWave
Microstrip and Stripline
Microstrip and stripline are two common transmission line structures used in mmWave PCB design. Microstrip consists of a conductive trace on the top layer of the substrate, with a ground plane on the bottom layer. Stripline, on the other hand, has a conductive trace embedded between two ground planes.
Microstrip is easier to fabricate and provides better heat dissipation, but it is more susceptible to radiation losses and external interference. Stripline offers better isolation and lower radiation losses, but it requires more complex fabrication and has limited heat dissipation capabilities.
Impedance Matching
Proper impedance matching is crucial in mmWave PCB design to minimize reflections and ensure efficient power transfer. The characteristic impedance of the transmission line should match the impedance of the connected components, typically 50 ohms. Impedance matching can be achieved by adjusting the width and thickness of the conductive trace, as well as the substrate thickness and dielectric constant.
Bends and Discontinuities
At mmWave frequencies, bends and discontinuities in transmission lines can introduce significant reflections and losses. To minimize these effects, it is recommended to use smooth, gradual bends instead of sharp corners. Mitered bends and chamfered corners can help reduce reflections and maintain signal integrity.
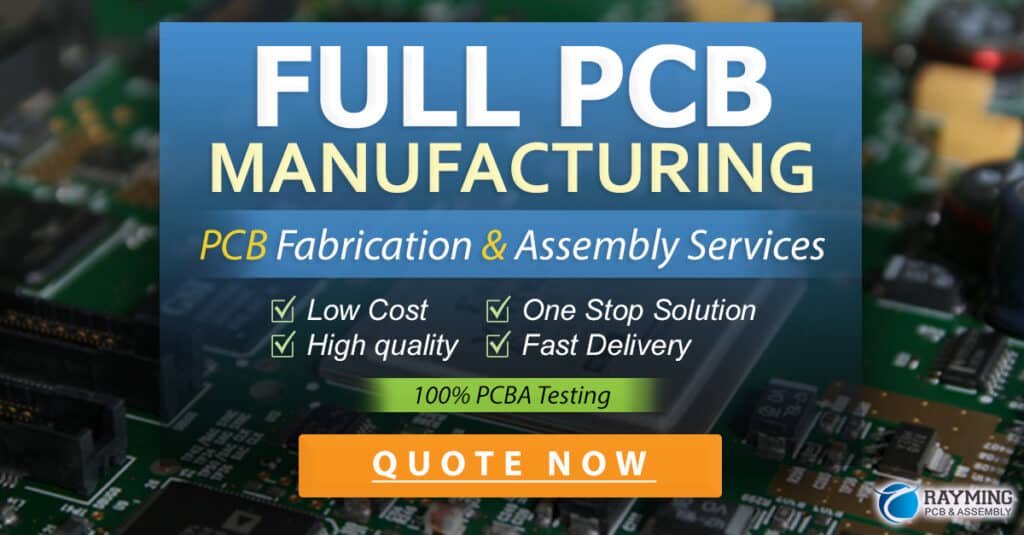
Signal Integrity Considerations
Losses and Attenuation
At mmWave frequencies, losses and attenuation become more pronounced, limiting the maximum transmission distance and signal quality. Conductor losses, dielectric losses, and radiation losses all contribute to the overall attenuation. To mitigate these losses, it is essential to choose low-loss materials, minimize transmission line lengths, and optimize the PCB layout.
Crosstalk and Interference
Crosstalk and interference can severely impact signal integrity in mmWave PCBs. To minimize crosstalk, it is crucial to maintain adequate spacing between signal traces, use proper shielding techniques, and employ ground planes to provide isolation. Differential signaling can also help reduce crosstalk and improve noise immunity.
Vias and Transitions
Vias and transitions between layers in mmWave PCBs can introduce discontinuities and reflections. To minimize these effects, it is recommended to use small-diameter vias, keep via stubs short, and employ impedance-matched transitions. Blind and buried vias can also be used to reduce the impact of via stubs on signal integrity.
Power Integrity Considerations
Power Distribution Network (PDN)
Designing a robust power distribution network (PDN) is crucial for maintaining power integrity in mmWave PCBs. The PDN should provide a low-impedance path for power delivery while minimizing voltage fluctuations and noise. Decoupling capacitors should be placed close to the power pins of active components to suppress high-frequency noise and maintain a stable power supply.
Thermal Management
Thermal management is a critical aspect of mmWave PCB design, as high-frequency components generate significant heat. Proper thermal management techniques, such as the use of heatsinks, thermal vias, and adequate copper pour, can help dissipate heat and prevent performance degradation. It is also important to consider the thermal properties of the substrate material and the placement of components to optimize heat dissipation.
Manufacturing Considerations for mmWave PCBs
Tolerances and Precision
Manufacturing tolerances and precision become increasingly critical at mmWave frequencies. Small variations in trace width, substrate thickness, and via placement can significantly impact performance. It is essential to work closely with the PCB manufacturer to ensure tight tolerances and high-precision fabrication techniques are employed.
Surface Finish
The choice of surface finish for mmWave PCBs is important for ensuring reliable connections and minimizing losses. Immersion silver (IAg) and electroless nickel immersion gold (ENIG) are common surface finishes used in mmWave applications. IAg provides good solderability and low insertion loss, while ENIG offers better durability and corrosion resistance.
Testing and Validation
Thorough testing and validation are critical for ensuring the performance and reliability of mmWave PCBs. High-frequency measurements, such as S-parameter characterization and time-domain reflectometry (TDR), can help evaluate signal integrity and identify potential issues. It is also important to perform environmental testing, including temperature cycling and vibration tests, to assess the robustness of the PCB design.
FAQ
What is the main challenge in designing PCBs for mmWave frequencies?
The main challenge in designing PCBs for mmWave frequencies is managing the increased losses, attenuation, and sensitivity to manufacturing tolerances. At higher frequencies, the impact of parasitic effects, impedance mismatches, and signal integrity issues becomes more pronounced, requiring careful consideration and optimization of the PCB design.
What substrate materials are commonly used for mmWave PCBs?
Common substrate materials for mmWave PCBs include Rogers RO3003, Rogers RO4350B, Isola Astra MT77, and PTFE (Teflon). These materials are chosen for their low dielectric losses, stable properties over temperature, and consistent performance at high frequencies.
How can crosstalk and interference be minimized in mmWave PCBs?
To minimize crosstalk and interference in mmWave PCBs, designers can maintain adequate spacing between signal traces, use proper shielding techniques, employ ground planes for isolation, and utilize differential signaling. These techniques help reduce the coupling between signals and improve overall signal integrity.
Why is thermal management important in mmWave PCB design?
Thermal management is crucial in mmWave PCB design because high-frequency components generate significant heat. If not properly managed, excessive heat can lead to performance degradation and reliability issues. Effective thermal management techniques, such as the use of heatsinks, thermal vias, and adequate copper pour, help dissipate heat and maintain optimal performance.
What testing and validation methods are used for mmWave PCBs?
Testing and validation of mmWave PCBs typically involve high-frequency measurements, such as S-parameter characterization and time-domain reflectometry (TDR), to evaluate signal integrity and identify potential issues. Environmental testing, including temperature cycling and vibration tests, is also performed to assess the robustness and reliability of the PCB design.
Conclusion
Designing PCBs for mmWave frequencies presents unique challenges that require careful consideration of material selection, transmission line design, signal integrity, power integrity, and manufacturing techniques. By understanding and addressing these critical aspects, engineers can optimize their PCB designs to ensure reliable and efficient operation at mmWave frequencies.
As the demand for high-speed wireless communications, radar applications, and imaging systems continues to grow, mmWave technology will play an increasingly important role. By following the guidelines and best practices outlined in this article, designers can effectively navigate the complexities of mmWave PCB design and unlock the full potential of this exciting technology.
No responses yet