Schematic Capture
Component Selection
- [ ] Select components based on the project requirements, including functionality, performance, and cost
- [ ] Ensure component availability and lead times align with the project timeline
- [ ] Consider using standardized components to simplify sourcing and reduce costs
- [ ] Review component datasheets and application notes for proper usage and implementation
Schematic Design
- [ ] Create a clear and organized schematic layout
- [ ] Use consistent naming conventions for components, nets, and labels
- [ ] Assign appropriate component values and tolerances
- [ ] Include necessary power supply decoupling capacitors and filtering
- [ ] Implement proper grounding techniques, such as star grounding or ground planes
- [ ] Add test points and debugging interfaces for easier troubleshooting
- [ ] Include necessary protection circuitry, such as ESD protection and reverse polarity protection
Schematic Review
- [ ] Verify the schematic against the project requirements and specifications
- [ ] Check for correct component connections and pinouts
- [ ] Ensure proper power supply connections and decoupling
- [ ] Review the schematic for any missing or incorrect components
- [ ] Perform a design rule check (DRC) to identify any errors or warnings
- [ ] Collaborate with team members and stakeholders for a peer review of the schematic
PCB Layout
Component Placement
- [ ] Group related components together for optimal signal integrity and functionality
- [ ] Consider component orientation for ease of assembly and manufacturing
- [ ] Ensure adequate clearance between components for soldering and inspection
- [ ] Place sensitive components away from sources of interference, such as power supplies or high-speed signals
- [ ] Optimize component placement for thermal management and heat dissipation
Routing and Traces
- [ ] Define appropriate trace widths based on signal requirements and current carrying capacity
- [ ] Maintain consistent trace spacing to minimize crosstalk and interference
- [ ] Route critical signals first, such as clocks, high-speed signals, and sensitive analog traces
- [ ] Minimize trace lengths to reduce signal degradation and parasitic effects
- [ ] Implement proper trace corners and angles to avoid signal reflections
- [ ] Use ground planes or ground pours to provide a low-impedance return path for signals
- [ ] Consider using differential pair routing for high-speed signals
- [ ] Avoid routing traces under components or through vias whenever possible
Power and Ground
- [ ] Create separate power and ground planes for different voltage levels
- [ ] Use appropriate plane layer stacking for optimal signal integrity and EMI reduction
- [ ] Implement proper power supply decoupling and bulk capacitance
- [ ] Ensure adequate copper pour for power and ground nets to minimize voltage drops
- [ ] Use star grounding techniques to minimize ground loops and noise
Signal Integrity and EMC
- [ ] Analyze critical signals for impedance matching and termination requirements
- [ ] Implement appropriate termination strategies, such as series termination or parallel termination
- [ ] Consider using guard rings or shielding for sensitive analog or RF signals
- [ ] Minimize the loop area of high-speed signals to reduce electromagnetic interference (EMI)
- [ ] Follow proper layout techniques for high-speed interfaces, such as USB, PCIe, or Ethernet
Manufacturing Considerations
- [ ] Define the PCB stackup and layer arrangement based on the manufacturing capabilities and project requirements
- [ ] Specify the appropriate PCB material, thickness, and copper weight
- [ ] Include necessary fiducials, tooling holes, and alignment marks for manufacturing
- [ ] Define the soldermask and silkscreen requirements, including component outlines and reference designators
- [ ] Consider the assembly process, such as component placement and soldering methods
- [ ] Communicate any special requirements or considerations to the manufacturing partner
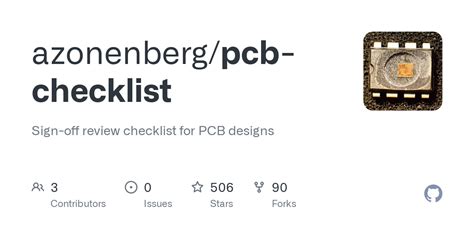
PCB Review and Verification
Design Rule Check (DRC)
- [ ] Run a comprehensive DRC to identify any design rule violations
- [ ] Verify trace width and spacing, minimum hole size, and clearance requirements
- [ ] Check for any unconnected or shorted nets
- [ ] Ensure proper copper pour connections and isolation
- [ ] Review the DRC report and address any issues or warnings
Electrical Rule Check (ERC)
- [ ] Perform an ERC to detect any electrical errors or inconsistencies
- [ ] Check for proper component connections and pinouts
- [ ] Verify power supply nets and connections
- [ ] Ensure appropriate net naming and labeling
- [ ] Address any ERC warnings or errors
Mechanical Review
- [ ] Verify the PCB dimensions and mounting hole locations
- [ ] Check for any mechanical clearance issues or interferences
- [ ] Ensure proper component placement and orientation for mechanical fitment
- [ ] Review the PCB outline and any cutouts or special features
- [ ] Confirm the PCB thickness and material specifications
Manufacturing Review
- [ ] Generate the necessary manufacturing files, such as Gerber files, drill files, and assembly drawings
- [ ] Review the manufacturing files for accuracy and completeness
- [ ] Verify the layer stackup and any special requirements with the manufacturing partner
- [ ] Confirm the soldermask and silkscreen artwork
- [ ] Provide clear instructions for any special handling or assembly requirements
Prototype and Testing
- [ ] Order prototype PCBs for initial testing and validation
- [ ] Assemble the prototype boards and perform functional testing
- [ ] Verify the PCB functionality against the project requirements and specifications
- [ ] Conduct any necessary environmental or reliability testing
- [ ] Document any issues or improvements identified during the prototype phase
- [ ] Update the PCB design based on the prototype feedback and retest as needed
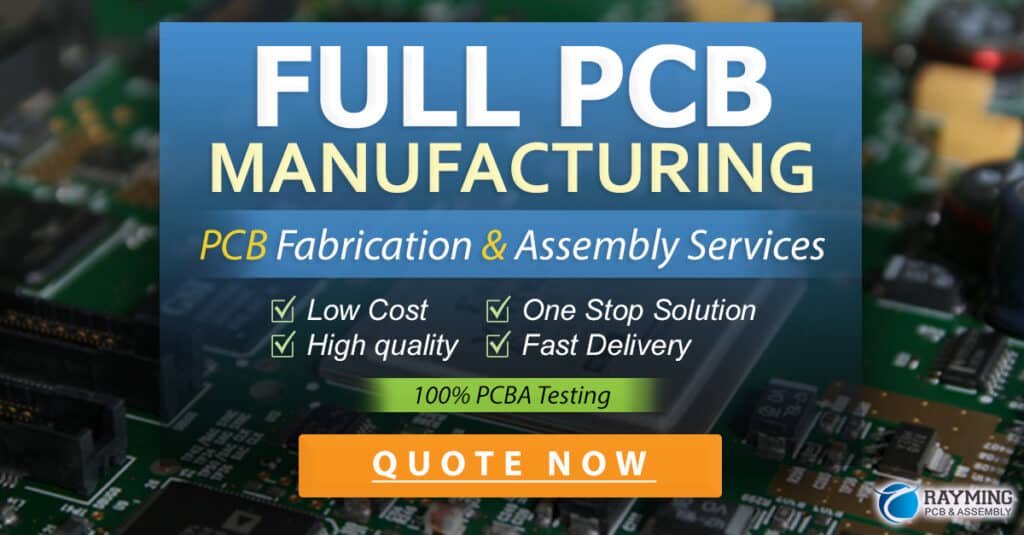
Documentation and Version Control
Schematic and Layout Files
- [ ] Maintain accurate and up-to-date schematic and layout files
- [ ] Use version control software to track changes and revisions
- [ ] Include relevant notes, comments, and annotations within the design files
- [ ] Regularly backup the design files to prevent data loss
Bill of Materials (BOM)
- [ ] Generate a comprehensive BOM listing all components and their specifications
- [ ] Include manufacturer part numbers, quantities, and any special notes
- [ ] Verify the BOM against the schematic and layout for accuracy
- [ ] Update the BOM as needed throughout the design process
Assembly and Fabrication Drawings
- [ ] Create clear and detailed assembly drawings for manufacturing
- [ ] Include component placement, orientation, and any special assembly instructions
- [ ] Provide fabrication drawings specifying the PCB stackup, materials, and any special requirements
- [ ] Ensure the drawings are properly labeled and versioned
Design Documentation
- [ ] Maintain a design document outlining the project requirements, specifications, and any design decisions
- [ ] Include relevant calculations, simulations, and test results
- [ ] Document any design trade-offs or compromises made during the development process
- [ ] Update the design documentation as the project progresses
Collaboration and Review
- [ ] Share the design files, documentation, and BOM with relevant team members and stakeholders
- [ ] Collaborate with mechanical, firmware, and software teams to ensure proper integration
- [ ] Conduct regular design reviews to gather feedback and identify any issues or improvements
- [ ] Document and address any action items or changes resulting from the design reviews
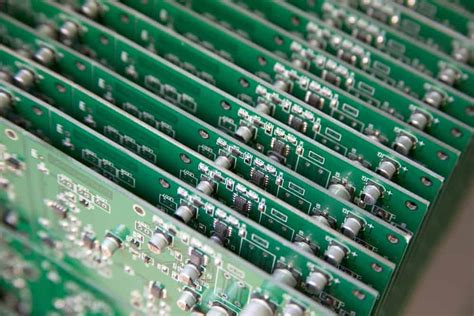
Frequently Asked Questions (FAQ)
1. What are the most common PCB design mistakes to avoid?
Some common PCB design mistakes include:
– Improper component placement and orientation
– Incorrect trace widths and spacing
– Insufficient power supply decoupling and filtering
– Lack of proper grounding techniques
– Neglecting signal integrity and EMI considerations
– Inadequate documentation and version control
To avoid these mistakes, follow the PCB design checklist and best practices, conduct thorough design reviews, and collaborate with experienced PCB designers.
2. How do I select the appropriate PCB material and stackup?
The choice of PCB material and stackup depends on several factors, including:
– Signal frequency and speed requirements
– Dielectric constant and loss tangent of the material
– Thermal management and heat dissipation needs
– Manufacturing capabilities and cost considerations
Consider the project requirements and consult with your PCB manufacturer to determine the most suitable material and stackup for your design. Common PCB materials include FR-4, Rogers, and Isola, and the stackup can vary from simple two-layer boards to complex multi-layer designs.
3. What are the key considerations for high-speed PCB design?
When designing high-speed PCBs, consider the following:
– Impedance matching and termination techniques
– Proper routing and trace geometry for signal integrity
– Minimizing crosstalk and electromagnetic interference (EMI)
– Power supply decoupling and bypassing
– Grounding strategies, such as ground planes and stitching vias
– Material selection for low dielectric loss and high-frequency performance
It’s essential to follow best practices for high-speed design, such as minimizing trace lengths, avoiding sharp corners, and using appropriate simulation tools to analyze signal integrity.
4. How can I ensure proper power supply decoupling and filtering?
To ensure proper power supply decoupling and filtering:
– Place decoupling capacitors close to the power pins of ICs
– Use a combination of bulk, ceramic, and tantalum capacitors for effective decoupling
– Implement power supply filtering, such as ferrite beads or LC filters, to reduce noise
– Use separate power planes for different voltage levels
– Optimize the placement and routing of power traces to minimize inductance and resistance
Regularly review the power supply design and conduct simulations or measurements to verify the effectiveness of the decoupling and filtering techniques.
5. What are the benefits of using a PCB design checklist?
Using a PCB design checklist offers several benefits:
– Ensures a systematic and thorough approach to PCB design
– Reduces the risk of overlooking critical design aspects
– Helps maintain consistency and quality across different projects
– Facilitates collaboration and communication among team members
– Serves as a reference for best practices and design guidelines
– Minimizes the likelihood of design errors and costly redesigns
By following a comprehensive PCB design checklist, you can streamline your design process, improve the reliability and performance of your PCBs, and ultimately save time and resources in the long run.
PCB Design Stage | Key Considerations |
---|---|
Schematic Capture | – Component selection – Schematic design – Schematic review |
PCB Layout | – Component placement – Routing and traces – Power and ground – Signal integrity and EMC – Manufacturing considerations |
PCB Review and Verification | – Design rule check (DRC) – Electrical rule check (ERC) – Mechanical review – Manufacturing review – Prototype and testing |
Documentation and Version Control | – Schematic and layout files – Bill of materials (BOM) – Assembly and fabrication drawings – Design documentation – Collaboration and review |
By following this comprehensive PCB design and review checklist, you can ensure a systematic and thorough approach to developing high-quality and reliable printed circuit boards. Regular design reviews, collaboration with experienced professionals, and continuous improvement based on feedback and testing results will help you refine your PCB design skills and deliver successful projects.
No responses yet