What is PCB Crosstalk?
PCB crosstalk is an electromagnetic phenomenon that occurs when a signal transmitted on one trace or wire unintentionally affects the signal on an adjacent trace or wire. This unwanted interaction between signals can cause distortion, noise, and other signal integrity issues, ultimately compromising the performance and reliability of the PCB.
There are two main types of crosstalk:
-
Inductive Crosstalk: This type of crosstalk occurs when the magnetic field generated by a current flowing through one trace induces a voltage in an adjacent trace.
-
Capacitive Crosstalk: This type of crosstalk occurs when the electric field between two adjacent traces causes a change in the voltage of the affected trace.
Causes of PCB Crosstalk
Several factors can contribute to the occurrence of PCB crosstalk:
1. Trace Proximity
The closer the traces are to each other, the higher the likelihood of crosstalk. When traces are placed too close together, the electromagnetic fields generated by the signals can interact, leading to crosstalk.
2. Signal Frequency
As signal frequencies increase, the risk of crosstalk also increases. Higher frequency signals have shorter wavelengths, making them more susceptible to coupling with adjacent traces.
3. Trace Length
Longer traces are more prone to crosstalk because they provide a greater opportunity for signals to interact with each other. As the trace length increases, the inductance and capacitance of the trace also increase, exacerbating the crosstalk effect.
4. Inadequate Ground Planes
Ground planes play a crucial role in mitigating crosstalk by providing a low-impedance return path for signals. Insufficient or improperly designed ground planes can lead to increased crosstalk.
5. Improper Termination
Improper termination of transmission lines can cause reflections and standing waves, which can contribute to crosstalk. Proper termination techniques, such as matching the impedance of the trace to the source and load impedances, can help reduce crosstalk.
Effects of PCB Crosstalk
PCB crosstalk can have several detrimental effects on the performance and functionality of a PCB:
1. Signal Integrity Degradation
Crosstalk can distort the shape and timing of signals, leading to signal integrity issues. This can cause bit errors, jitter, and other signal quality problems, which can affect the overall performance of the PCB.
2. Electromagnetic Interference (EMI)
Crosstalk can contribute to EMI, which is the unintentional emission of electromagnetic energy from a device. EMI can interfere with the operation of nearby electronic devices and can also violate regulatory standards.
3. Increased Noise
Crosstalk can introduce noise into the system, which can degrade the signal-to-noise ratio (SNR) and reduce the overall signal quality. This can lead to reduced system performance and reliability.
4. Timing Issues
Crosstalk can affect the timing of signals, causing delays or skews that can disrupt the synchronization of the system. This is particularly problematic in high-speed digital systems where precise timing is critical.
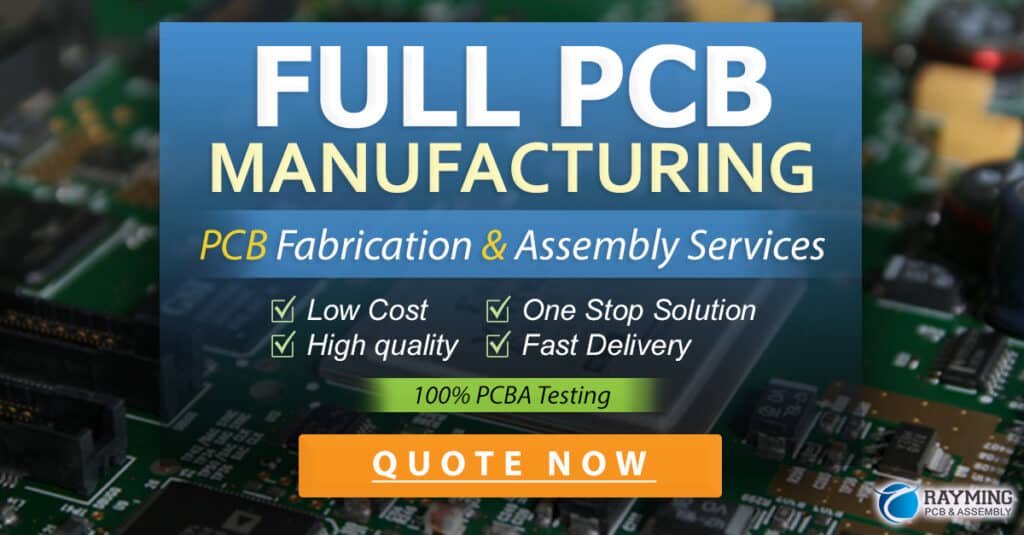
Techniques to Counter PCB Crosstalk
There are several design techniques and strategies that can be employed to minimize the impact of crosstalk on PCBs:
1. Increase Trace Spacing
One of the most effective ways to reduce crosstalk is to increase the spacing between traces. By keeping traces further apart, the electromagnetic interaction between them is reduced, leading to lower crosstalk. The following table provides general guidelines for trace spacing based on the signal rise time:
Signal Rise Time | Minimum Trace Spacing |
---|---|
> 1 ns | 3 × trace width |
500 ps – 1 ns | 5 × trace width |
< 500 ps | 10 × trace width |
2. Use Differential Signaling
Differential signaling involves using two complementary signals to transmit data, where the noise on one signal is cancelled out by the noise on the other signal. This technique is highly effective in reducing crosstalk, as any noise coupled onto the differential pair is common to both signals and can be easily filtered out at the receiver.
3. Implement Ground Planes
Incorporating solid ground planes in the PCB design can significantly reduce crosstalk. Ground planes provide a low-impedance return path for signals and help to shield traces from each other. By placing ground planes between signal layers, the coupling between traces is minimized.
4. Optimize Signal Routing
Careful signal routing can help minimize crosstalk. Some tips for optimizing signal routing include:
- Route critical signals on separate layers to minimize interaction with other signals.
- Avoid running parallel traces for long distances, as this increases the coupling between them.
- Use via fences or guard traces to isolate sensitive signals from other traces.
- Keep high-speed traces as short as possible to reduce the opportunity for crosstalk.
5. Employ Proper Termination Techniques
Proper termination of transmission lines is crucial for reducing reflections and minimizing crosstalk. Some common termination techniques include:
- Series Termination: A resistor is placed in series with the signal source to match the impedance of the trace to the source impedance.
- Parallel Termination: A resistor is placed in parallel with the load to match the impedance of the trace to the load impedance.
- Differential Termination: Resistors are placed at both ends of a differential pair to match the impedance of the traces to the source and load impedances.
6. Use Shielding Techniques
Shielding techniques can be employed to reduce crosstalk between traces. Some shielding methods include:
- Using shielded cables or connectors for sensitive signals.
- Placing grounded guard traces between sensitive signals and other traces.
- Using conductive foil or tape to shield critical areas of the PCB.
Simulation and Analysis Tools
To predict and analyze crosstalk in PCB designs, several simulation and analysis tools are available:
-
SPICE (Simulation Program with Integrated Circuit Emphasis): SPICE is a widely used circuit simulation tool that can be used to simulate and analyze crosstalk in PCBs.
-
Electromagnetic Field Solvers: Tools like Ansys HFSS, Keysight ADS, and Altium Designer’s Power Integrity Simulation can perform electromagnetic field simulations to predict crosstalk in PCB designs.
-
Signal Integrity Analysis Tools: Tools like Cadence Sigrity, Mentor Graphics HyperLynx, and Synopsys PCB SI can analyze signal integrity issues, including crosstalk, in PCB designs.
By using these simulation and analysis tools, designers can identify potential crosstalk issues early in the design process and take appropriate measures to mitigate them.
Frequently Asked Questions (FAQ)
1. What is the difference between inductive and capacitive crosstalk?
Inductive crosstalk occurs when the magnetic field generated by a current flowing through one trace induces a voltage in an adjacent trace. Capacitive crosstalk, on the other hand, occurs when the electric field between two adjacent traces causes a change in the voltage of the affected trace.
2. How does increasing the spacing between traces reduce crosstalk?
Increasing the spacing between traces reduces the electromagnetic interaction between them. As the distance between traces increases, the coupling capacitance and mutual inductance decrease, leading to lower crosstalk.
3. What is the role of ground planes in mitigating crosstalk?
Ground planes provide a low-impedance return path for signals and help to shield traces from each other. By placing ground planes between signal layers, the coupling between traces is minimized, reducing crosstalk.
4. How does differential signaling help in reducing crosstalk?
Differential signaling uses two complementary signals to transmit data, where the noise on one signal is cancelled out by the noise on the other signal. Any noise coupled onto the differential pair is common to both signals and can be easily filtered out at the receiver, effectively reducing crosstalk.
5. What are some common termination techniques used to reduce crosstalk?
Common termination techniques used to reduce crosstalk include series termination, parallel termination, and differential termination. These techniques involve placing resistors at the source or load end of the traces to match the impedance of the traces to the source and load impedances, minimizing reflections and crosstalk.
Conclusion
PCB crosstalk is a significant challenge faced by electronics designers and engineers in the pursuit of high-performance and reliable PCBs. Understanding the causes, effects, and techniques to counter crosstalk is essential for designing robust and efficient PCBs.
By implementing design strategies such as increasing trace spacing, using differential signaling, incorporating ground planes, optimizing signal routing, employing proper termination techniques, and utilizing shielding methods, designers can effectively mitigate the impact of crosstalk on PCB performance.
Furthermore, the use of simulation and analysis tools can greatly assist in predicting and analyzing crosstalk issues early in the design process, enabling designers to make informed decisions and optimize their PCB designs for minimal crosstalk.
As technology continues to advance and the demand for high-speed, high-density PCBs grows, addressing PCB crosstalk will remain a critical aspect of electronics design. By staying informed about the latest techniques and best practices for countering crosstalk, designers can ensure the development of robust, reliable, and high-performance PCBs that meet the ever-increasing demands of modern electronic systems.
No responses yet