Introduction to PCB Colors
Printed Circuit Boards (PCBs) are the foundation of modern electronics. They provide a platform for mounting and connecting electronic components to create functional circuits. While the primary focus is usually on the electrical properties and layout of the PCB, the color of the PCB can also play a significant role in the overall design and functionality.
PCB color is not just an aesthetic choice; it can serve various purposes, such as improving visibility, enhancing inspection capabilities, or even providing functional benefits. In this article, we will explore the different aspects of PCB color selection, including the available color options, their purposes, and how to choose the right color for your specific needs.
Common PCB Color Options
PCBs come in a variety of colors, each with its own characteristics and applications. Here are some of the most common PCB color options:
Green
Green is the most popular and widely used PCB color. It is the default color for most PCB manufacturers due to its cost-effectiveness and good contrast with copper traces and white silkscreen. Green PCBs are suitable for a wide range of applications, from consumer electronics to industrial devices.
Blue
Blue PCBs are another popular choice, particularly in the aerospace and military industries. They offer good contrast and visibility, making them suitable for high-reliability applications. Blue PCBs are also known for their durability and resistance to harsh environmental conditions.
Red
Red PCBs are less common but can be used for specific applications, such as in the automotive industry. They provide good visibility and can be used to indicate high-voltage or power-related circuits. Red PCBs can also be used for aesthetic purposes in consumer electronics.
Black
Black PCBs have gained popularity in recent years, particularly in high-end consumer electronics and IoT devices. They offer a sleek and modern appearance, making them attractive for products where aesthetics are important. Black PCBs can also provide good contrast with white silkscreen and component markings.
White
White PCBs are relatively uncommon but can be used for specific applications, such as LED lighting or reflective surfaces. They provide excellent contrast with dark-colored components and can enhance the overall appearance of the product.
Yellow
Yellow PCBs are rarely used but can be helpful in applications where high visibility is required, such as in safety-critical systems. They provide excellent contrast with dark-colored components and can be easily spotted during inspection or troubleshooting.
PCB Color Selection Factors
When choosing the color of your PCB, several factors should be considered to ensure the best performance and functionality. Some of these factors include:
Contrast and Visibility
One of the primary reasons for selecting a specific PCB color is to improve contrast and visibility. The color of the PCB should provide good contrast with the copper traces, components, and silkscreen markings. This enhances the readability of the PCB, making it easier to inspect, assemble, and troubleshoot.
For example, green and blue PCBs offer good contrast with white silkscreen and copper traces, while black PCBs provide excellent contrast with white silkscreen and component markings.
Application and Environment
The intended application and operating environment of the PCB should also be considered when selecting the color. Different industries may have specific color preferences or requirements based on their unique needs.
For instance, the aerospace and military industries often prefer blue PCBs due to their durability and resistance to harsh environmental conditions. In the automotive industry, red PCBs may be used to indicate high-voltage or power-related circuits.
Aesthetics and Branding
In some cases, the color of the PCB may be chosen for aesthetic or branding purposes. This is particularly relevant in consumer electronics, where the appearance of the product can significantly influence consumer perception and market success.
Black PCBs, for example, have become increasingly popular in high-end consumer electronics due to their sleek and modern appearance. White PCBs can be used to enhance the overall look of LED lighting products or to create a clean and minimalistic design.
Cost and Availability
The cost and availability of different PCB colors should also be taken into account. Green PCBs are the most cost-effective and readily available option, as they are the default color for most PCB manufacturers. Other colors, such as blue, red, or black, may come at a higher cost or have longer lead times due to lower demand or specialized manufacturing processes.
It is essential to balance the desired color with the cost and availability constraints of your project to ensure timely and cost-effective production.
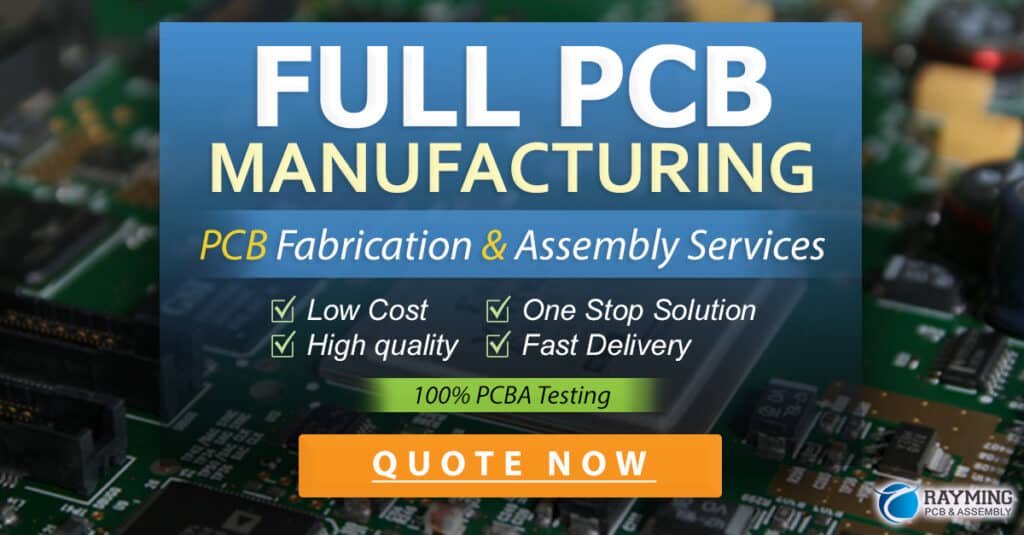
PCB Color and Solder Mask
The color of a PCB is determined by the solder mask, which is a protective layer applied over the copper traces to prevent oxidation and provide electrical insulation. Solder masks are available in various colors, with green being the most common.
The choice of solder mask color can affect the performance and functionality of the PCB in several ways:
Thermal Properties
Different colored solder masks can have varying thermal properties, which can impact the heat dissipation and thermal management of the PCB. For example, black solder masks are known to have better heat absorption properties compared to lighter colors, making them suitable for applications with high heat generation.
UV Resistance
The color of the solder mask can also influence its resistance to ultraviolet (UV) light. Some colors, such as green and blue, are more resistant to UV degradation compared to lighter colors like white or yellow. This is particularly important for PCBs that will be exposed to direct sunlight or used in outdoor applications.
Electrical Properties
While the color of the solder mask does not directly affect the electrical properties of the PCB, it can indirectly influence the performance through factors such as thermal management and UV resistance. Proper selection of solder mask color can help ensure the long-term reliability and functionality of the PCB.
PCB Color and Silkscreen
Silkscreen is the text and graphics printed on the surface of the PCB to provide information about component placement, orientation, and identification. The color of the silkscreen is typically chosen to provide good contrast against the PCB color for enhanced readability.
PCB Color | Recommended Silkscreen Color |
---|---|
Green | White |
Blue | White |
Red | White |
Black | White |
White | Black |
Yellow | Black |
Choosing the right silkscreen color based on the PCB color ensures that the information is clearly visible and easy to read, which is crucial for accurate assembly and troubleshooting.
PCB Color and Inspection
The color of the PCB can also play a role in the inspection process, both during manufacturing and post-assembly. Different colors can affect the visibility of defects, such as solder bridges, component misalignment, or hairline cracks.
PCB Color | Inspection Considerations |
---|---|
Green | Good contrast with copper traces and white silkscreen |
Blue | Good contrast with copper traces and white silkscreen |
Red | May require special lighting for accurate inspection |
Black | Excellent contrast with white silkscreen and components |
White | May require special lighting for accurate inspection |
Yellow | Excellent contrast with dark-colored components |
Choosing a PCB color that enhances the visibility of defects can improve the efficiency and accuracy of the inspection process, ultimately leading to higher quality and reliability of the final product.
FAQ
1. What is the most common PCB color?
The most common PCB color is green. Green PCBs are widely used due to their cost-effectiveness and good contrast with copper traces and white silkscreen.
2. Can PCB color affect the electrical performance of the board?
The color of the PCB itself does not directly affect the electrical performance. However, the color of the solder mask can indirectly influence the performance through factors such as thermal management and UV resistance.
3. Are there any industry-specific preferences for PCB colors?
Yes, some industries have specific preferences or requirements for PCB colors. For example, the aerospace and military industries often prefer blue PCBs for their durability and resistance to harsh environments, while the automotive industry may use red PCBs to indicate high-voltage or power-related circuits.
4. How does PCB color impact the inspection process?
The color of the PCB can affect the visibility of defects during inspection. Choosing a color that provides good contrast with the copper traces, components, and silkscreen can enhance the efficiency and accuracy of the inspection process.
5. Are there any limitations on the availability of different PCB colors?
Some PCB colors, such as green, are more readily available and cost-effective due to high demand. Other colors, like blue, red, or black, may come at a higher cost or have longer lead times due to specialized manufacturing processes or lower demand.
Conclusion
PCB color selection is an important aspect of the overall PCB design process. It goes beyond mere aesthetics and can serve various purposes, such as improving visibility, enhancing inspection capabilities, and providing functional benefits specific to certain industries or applications.
When choosing the color of your PCB, consider factors such as contrast and visibility, application and environment, aesthetics and branding, and cost and availability. The color of the solder mask and silkscreen should also be taken into account to ensure optimal performance and readability.
By understanding the different PCB color options and their characteristics, you can make an informed decision that best suits your specific needs and requirements. Whether you opt for the classic green, the durable blue, the sleek black, or any other color, the right choice can contribute to the success and reliability of your electronic product.
No responses yet