What is PCB cloning?
PCB cloning involves reverse engineering an existing printed circuit board to create an identical copy or reproduction. The goal is to create a functional PCB that matches the original design in form, fit, and function.
There are several scenarios where PCB cloning may be necessary:
- The original PCB is no longer being manufactured
- Documentation and design files for the original PCB are missing
- Only a physical board is available with no accompanying information
- Modifications need to be made to an existing design
By cloning the PCB, a working replacement can be produced even without access to the original design documents and source files. The cloned PCB matches the mechanical dimensions and mounting holes to be a drop-in replacement for the original board.
PCB Cloning Process Overview
The basic steps in the PCB cloning process are:
-
Physical inspection and measurement – Examine the original PCB and document the physical dimensions, layer count, materials, and components used.
-
Schematic capture – Reverse engineer the circuit schematic by tracing the connections on the board. Create a schematic diagram in EDA (electronic design automation) software.
-
PCB layout – Recreate the physical layout of the board based on measurements and examination of the original PCB. Route the traces and place components to match the original design.
-
Bill of Materials (BOM) creation – Generate a parts list of all the components used on the cloned PCB.
-
Fabrication and assembly – Produce the cloned PCB and assemble it with the required components. Test and validate operation compared to the original board.
Each of these steps is covered in more detail in the following sections.
Physical Inspection and Measurement
The first step in PCB cloning is to closely examine the original board you want to copy. Some key things to check and document include:
-
Board dimensions – Measure the length, width, and thickness of the board as well as the sizes and locations of mounting holes and other mechanical features.
-
Number of layers – Determine how many copper layers are in the PCB stackup. This can often be seen by looking at the edges of the board.
-
Material – Identify the base material the PCB is made from, such as FR-4 glass epoxy.
-
Surface finish – Note the final finish on the copper, such as HASL (hot air solder leveling), lead-free HASL, ENIG (electroless nickel immersion gold), etc.
-
Copper weight – Estimate the thickness of the copper used for the outer layers and inner layers. This is typically specified in ounces per square foot.
-
Smallest features – Measure the smallest traces and gaps between traces to determine the minimum feature size that will need to be matched.
-
Components – Make a list of all the components on the board, including part numbers and values. Note any unusual or obsolete parts that may be difficult to source.
Document everything as completely as possible with clear photographs, notes, and measurements. This information will be essential when it comes time to recreate the schematic and board layout.
Inspection Tools and Equipment
To do a thorough inspection and collect the necessary details, some helpful tools and equipment include:
Tool | Purpose |
---|---|
Digital calipers | Precise measurements of board dimensions and component sizes |
Micrometer | Measuring board and copper thickness |
USB microscope | Close-up examination of PCB traces, markings, and components |
Magnifying glass | Viewing fine details and part markings |
Digital multimeter | Continuity checking and component testing |
Soldering iron and solder wick | Removing components for closer inspection or measurement |
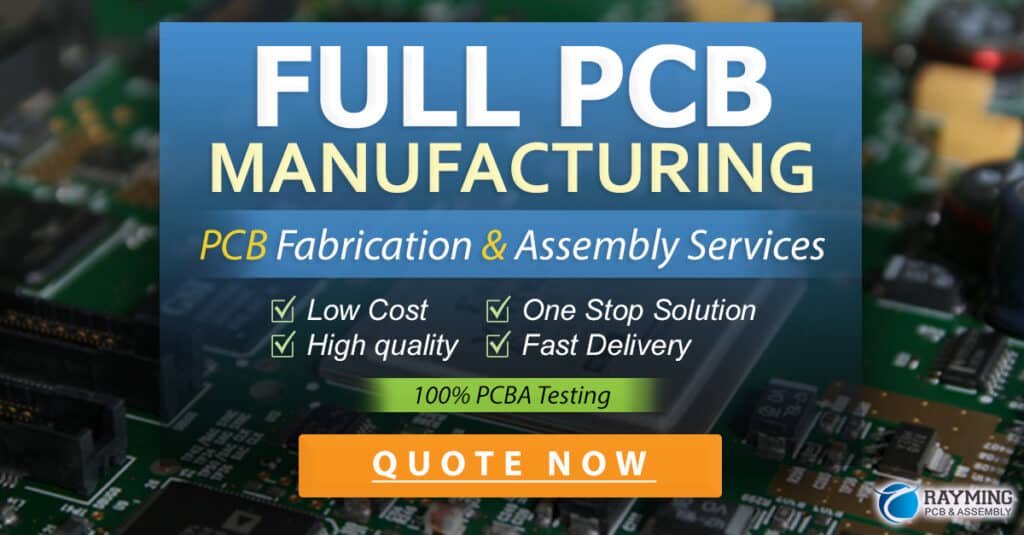
Schematic Capture
With the physical details of the board documented, the next step is to determine the schematic – the logical diagram of components and connections that defines the circuit’s operation. Unless you have the original schematic, this will require reverse engineering the circuit based on examination of the PCB.
Tracing the Circuit Board
To recreate the schematic, you’ll need to carefully trace out all the connections on the board. There are several techniques that can help with this:
- Follow traces visually or with a multimeter in continuity mode to see what pins are connected.
- Use a microscope to view small traces that are hard to see clearly.
- Look for power and ground planes that connect to multiple component pins.
- Identify components and research their pinouts in datasheets to understand their connections.
- Remove components from the board to better see the traces underneath and solder joints.
It can be very helpful to work methodically and document connections as you go along rather than trying to map out the whole board at once. Focus on one section of the board or one component at a time.
Schematic Capture Tools
To draw the schematic based on your tracing of the board, you’ll typically use an EDA tool. Some popular options for schematic capture include:
- KiCad
- Altium Designer
- OrCAD Capture
- Eagle
These tools provide schematic symbols for common components that you can place and wire together following the connections you determined from the original board. As you draw the schematic, you can associate components and nets with their physical locations on the board to help you stay organized.
PCB Layout
With a completed schematic, you’re ready to recreate the physical PCB layout. The goal is to match the original board as closely as possible in terms of component placement, routing, layer stackup, and mechanical features.
Board Outline and Mounting Holes
Begin by creating the overall board shape and size to match the original PCB. Include mounting holes and any cutouts or unusual outline features. Use the measurements you took during the initial physical inspection.
Layer Stackup
Set up the layer stackup in your EDA tool’s PCB editor to match what you determined about the original board – number of layers, thickness, material, and copper weights. Accurately reproducing the stackup is important for the board’s mechanical and electrical properties.
Component Placement
Place components on the board in the same physical locations as the original PCB. You can measure their positions or use a method like placing a printout of the original board overtop your working copy as a guide.
Pay attention to component orientations as well as positions. Make sure polarized components like electrolytic capacitors, diodes, and ICs are oriented the correct way.
Routing
Trace routing is one of the most time-consuming parts of the PCB cloning process. The goal is to recreate all the connections between components just like on the original board.
If you’re able to see the original trace routing clearly, you can route your board manually following the same pattern. Or the autorouter tool in your EDA software may be able to help recreate the routes, especially if you’re able to provide the original routes as a guide.
Trace widths are a key consideration when routing. You’ll want to match the original trace widths as closely as possible, or use standard widths for power, signal, and ground nets.
Be sure to route on the correct layers too. Inner layers are usually dedicated to power and ground planes, while signals should be routed on the outer layers just like the original design.
Copper Pours
Include copper pours for power and ground nets if they’re present on the original board. These large areas of copper help with power distribution and reducing electromagnetic interference.
Solder Mask and Silkscreen
To fully match the original PCB, you should also include solder mask and silkscreen layers. Copy any text markings, logos, and labels from the original silkscreen.
Layout Considerations
Given the complexity of PCB layouts, it’s very unlikely you’ll be able to create an exact replica of the original board. Some key things to keep in mind as you work on the layout:
- Prioritize matching critical elements like component placement, routing, and drill sizes over cosmetic details.
- If you can’t determine the exact trace routing, aim to create an electrically equivalent connection even if it doesn’t follow the same path.
- Ensure you leave enough clearance between traces, components, and board edges to meet manufacturing tolerances.
Bill of Materials
As part of the process of researching and identifying components on the original PCB, you should create a bill of materials or BOM. This is the complete list of parts needed to assemble the cloned board.
For each component, the BOM should include:
- Reference designator (e.g. R1, C2, U4)
- Part number
- Description
- Value or key specifications
- Quantity
- Manufacturer and supplier information
The BOM is a key document to check before getting boards made and assembled. Verify that all the parts are correct and available, and that you have accurate quantities to build the number of boards you need.
If any parts are obsolete or hard to find, you may need to find suitable replacements. This can involve looking for parts with the same specifications and package type that will fit the board.
Fabrication and Assembly
With the PCB layout finished and BOM complete, you’re ready to fabricate and assemble the cloned board.
Choosing a PCB Manufacturer
There are many PCB fabrication houses that can produce boards from your design files. For prototypes and small quantities, some popular options include:
- OSH Park
- JLCPCB
- PCBWay
- Seeed Studio
The manufacturer will need a set of Gerber files that describe your PCB design in a standard format they can use. Your EDA tool can export Gerbers that include all the necessary copper, drill, solder mask, and silkscreen layers.
Consider the manufacturer’s capabilities and tolerances to ensure they can reproduce your design accurately. You may need to adjust your design if it includes particularly small traces or clearances the fab house can’t do.
Assembly
After receiving the bare boards from the manufacturer, they need to be assembled with components according to the BOM. There are two main approaches to assembly:
Manual assembly involves hand soldering the components onto the board. This can be practical for simpler boards or small quantities.
Machine assembly uses a pick and place machine to automatically place components, followed by reflow soldering. This is usually outsourced to an assembly shop and makes sense for larger quantities or more complex boards.
In either case, having an accurate BOM and clear reference designators on the board is important for successful assembly.
Testing and Validation
The final step of the PCB cloning process is testing the assembled boards to ensure they function like the original. Depending on the type of circuit, this may involve:
- Visual inspection
- Continuity testing
- Power up testing
- Functional testing
- Comparison of operation to the original board
If the cloned PCB doesn’t work as expected, you’ll need to troubleshoot and determine where the problem lies. This could be due to anything from incorrect component values to assembly errors to design mistakes.
Catching problems in the initial prototype run can save a lot of time and money before ordering larger quantities. It’s wise to build one or a few boards first and thoroughly validate them before doing a bigger production run.
Frequently Asked Questions
How long does it take to clone a PCB?
The time required to clone a PCB can vary widely depending on the complexity of the board and availability of information. Some rough estimates for each stage assuming a moderately complex board:
- Physical inspection and measurement: 2-4 hours
- Schematic capture: 8-16 hours
- PCB layout: 16-32 hours
- BOM creation: 4-8 hours
The turnaround time for fabrication and assembly depends on the manufacturer, but is typically 1-2 weeks for prototypes.
So in total, cloning a PCB can easily be a 30-60 hour process spread over a few weeks to a couple months.
How much does it cost to clone a PCB?
The main costs involved in PCB cloning are:
- Labor for the design and engineering work
- Fabrication of bare PCBs
- Components to assemble the boards
- Assembly labor or service
Fabrication costs depend on the size and complexity of the board, but can range from $10-25 per board for small prototypes to a few dollars each in larger volumes.
Component and assembly costs are highly variable based on the parts used and assembly method. A basic parts kit could be $20-50 for common components, or far more if it includes specialized ICs or large quantities. Manual assembly might cost $30-100 per board, while machine assembly could be a few dollars each in volume.
Design and engineering labor is often the biggest cost. Depending on the hourly rate, 30-60 hours of engineering work could easily cost a few to several thousand dollars.
So in total, the cost to clone a simple PCB might be a few hundred dollars, while a complex board could be tens of thousands. Generally the non-recurring engineering costs dominate for one-off projects or small volumes.
Is it legal to clone a PCB?
The legality of cloning a PCB depends on copyright and intellectual property considerations. In general, PCB layouts are considered copyrightable works, so copying a layout directly without permission would be copyright infringement.
However, copyright doesn’t protect functionality. So if you reverse engineer a PCB and reproduce the same schematic and function but with a different physical layout, that is less likely to be infringement.
Trademarks or patents on the original product could also come into play. It’s safest to clone PCBs you have the rights to or that are no longer protected by intellectual property.
When in doubt, it’s best to consult an intellectual property attorney for advice on the legality of cloning a specific PCB design.
What are some challenges of PCB cloning?
Some of the key challenges that can come up when cloning a PCB include:
- Incomplete or missing information about the original board
- Obsolete or hard-to-find components
- Very high density boards with small traces that are hard to reverse engineer
- Highly complex boards with a lot of connections to trace
- Damaged original boards that are hard to measure or inspect
- Specialized materials or manufacturing processes used on the original that are hard to replicate
- No access to original design files
- Nondisclosure agreements or IP rights that restrict copying
Cloning is most straightforward for simpler boards that use readily available components and standard manufacturing specs. The more specialized or proprietary the original design, the more difficult it will be to duplicate.
What if I can’t find an exact match for a component?
When you can’t find an exact replacement for a component used on the original board, you’ll need to find a suitable substitute. There are a few things to look for:
- Same functionality and specs (e.g. passive component values, IC functionality)
- Same package size and pinout
- Ideally the same manufacturer or product line for consistency
- Similar electrical characteristics like voltage rating, power dissipation, slew rate, etc.
You may need to consult the component manufacturer’s datasheet or application notes to determine compatibility, or seek out a cross-reference guide that suggests equivalents.
In some cases substituting a different component will require adjusting the pad size or layout to accommodate it. Or if it has a different pinout you may need to reroute connections.
If you absolutely can’t find a suitable through-hole part, you might need to adapt to a surface mount equivalent or even a different circuit design. At that point it’s becoming more of a redesign than a true clone.
Conclusion
PCB cloning is a complex process that involves reverse engineering all aspects of a circuit board from the schematic to the physical layout. It requires a combination of component research, circuit tracing, and PCB design skills.
When done properly, PCB cloning can be an effective way to resurrect an obsolete design, create a drop-in replacement, or reproduce a board when the original design documents are lost.
However, the time and cost to clone a board scales rapidly with the complexity of the original design. And there are intellectual property risks to consider before copying someone else’s layout.
Despite the challenges, PCB cloning remains a valuable skill in industries like aerospace, medical devices, and industrial controls where long product lifecycles mean a constant need for replacement PCBs. As boards continue to get more complex and customized, the ability to recreate them faithfully will only become more important over time.
No responses yet