Introduction to PCB Classification
Printed Circuit Boards (PCBs) are essential components in modern electronics, providing a platform for mounting and interconnecting electronic components. The classification of PCBs is crucial for manufacturers, designers, and end-users to ensure that the boards meet specific requirements and standards. Two primary aspects of PCB classification are the Pattern Class and Drill Class, which define the level of complexity and precision required in the manufacturing process.
In this article, we will delve into the details of PCB classification, focusing on the Pattern Class and Drill Class. We will explore the various categories within each class, their characteristics, and the applications they are best suited for. Additionally, we will discuss the importance of adhering to these classifications and the benefits they offer in terms of quality, reliability, and cost-effectiveness.
What is PCB Pattern Class?
PCB Pattern Class refers to the level of complexity and precision required in the design and fabrication of the conductive traces on a PCB. The pattern class is determined by factors such as the minimum line width, minimum spacing between traces, and the overall density of the circuit layout. The IPC (Association Connecting Electronics Industries) has defined three main categories of PCB Pattern Class:
1. Class 1 (General)
Class 1 PCBs are the most basic and least complex category. They are typically used in applications where the primary focus is on functionality rather than miniaturization or high performance. The minimum line width and spacing requirements for Class 1 PCBs are relatively relaxed, allowing for larger traces and greater clearances between components.
Characteristics of Class 1 PCBs:
– Minimum line width: 0.2 mm (8 mil)
– Minimum spacing: 0.2 mm (8 mil)
– Suitable for general-purpose applications
– Lower manufacturing costs compared to higher classes
2. Class 2 (Dedicated Service)
Class 2 PCBs are designed for applications that require a higher level of reliability and performance than Class 1 boards. These PCBs have tighter tolerances for line width and spacing, enabling more compact and dense circuit layouts. Class 2 PCBs are commonly used in industrial, automotive, and medical devices where consistent performance and durability are essential.
Characteristics of Class 2 PCBs:
– Minimum line width: 0.1 mm (4 mil)
– Minimum spacing: 0.1 mm (4 mil)
– Suitable for applications requiring higher reliability and performance
– Increased manufacturing costs compared to Class 1
3. Class 3 (High Performance)
Class 3 PCBs represent the highest level of complexity and precision in PCB manufacturing. These boards are designed for demanding applications that require the utmost reliability, performance, and miniaturization. Class 3 PCBs have the tightest tolerances for line width and spacing, allowing for extremely dense and compact circuit layouts.
Characteristics of Class 3 PCBs:
– Minimum line width: 0.075 mm (3 mil) or smaller
– Minimum spacing: 0.075 mm (3 mil) or smaller
– Suitable for high-performance applications, such as aerospace, military, and advanced medical devices
– Highest manufacturing costs due to stringent requirements and specialized processes
Pattern Class | Minimum Line Width | Minimum Spacing | Applications |
---|---|---|---|
Class 1 | 0.2 mm (8 mil) | 0.2 mm (8 mil) | General-purpose |
Class 2 | 0.1 mm (4 mil) | 0.1 mm (4 mil) | Industrial, automotive, medical |
Class 3 | 0.075 mm (3 mil) or smaller | 0.075 mm (3 mil) or smaller | Aerospace, military, advanced medical |
What is PCB Drill Class?
PCB Drill Class refers to the level of precision and accuracy required in the drilling of holes on a PCB. These holes serve various purposes, such as mounting components, providing electrical connections between layers (vias), and facilitating the attachment of connectors or mechanical parts. The drill class is determined by factors such as the minimum hole size, hole position tolerance, and the overall hole density on the board. The IPC has defined three main categories of PCB Drill Class:
1. Class 1 (Standard)
Class 1 drill requirements are the most lenient among the three classes. PCBs with Class 1 drilling are suitable for applications where hole size and position accuracy are not critical. The minimum hole size for Class 1 is relatively large, and the tolerance for hole position is more relaxed compared to higher classes.
Characteristics of Class 1 drilling:
– Minimum hole size: 0.5 mm (20 mil)
– Hole position tolerance: ±0.25 mm (±10 mil)
– Suitable for general-purpose applications
– Lower manufacturing costs compared to higher classes
2. Class 2 (Advanced)
Class 2 drilling offers a higher level of precision and accuracy than Class 1. PCBs with Class 2 drilling are used in applications where hole size and position are more critical, such as in high-density designs or boards with fine-pitch components. The minimum hole size is smaller, and the hole position tolerance is tighter compared to Class 1.
Characteristics of Class 2 drilling:
– Minimum hole size: 0.3 mm (12 mil)
– Hole position tolerance: ±0.1 mm (±4 mil)
– Suitable for high-density designs and fine-pitch components
– Increased manufacturing costs compared to Class 1
3. Class 3 (Precision)
Class 3 drilling represents the highest level of precision and accuracy in PCB manufacturing. PCBs with Class 3 drilling are used in the most demanding applications, where hole size and position are critical to the overall performance and reliability of the device. The minimum hole size is the smallest among the three classes, and the hole position tolerance is extremely tight.
Characteristics of Class 3 drilling:
– Minimum hole size: 0.2 mm (8 mil) or smaller
– Hole position tolerance: ±0.05 mm (±2 mil) or tighter
– Suitable for high-performance applications, such as aerospace, military, and advanced medical devices
– Highest manufacturing costs due to stringent requirements and specialized processes
Drill Class | Minimum Hole Size | Hole Position Tolerance | Applications |
---|---|---|---|
Class 1 | 0.5 mm (20 mil) | ±0.25 mm (±10 mil) | General-purpose |
Class 2 | 0.3 mm (12 mil) | ±0.1 mm (±4 mil) | High-density designs, fine-pitch components |
Class 3 | 0.2 mm (8 mil) or smaller | ±0.05 mm (±2 mil) or tighter | Aerospace, military, advanced medical |
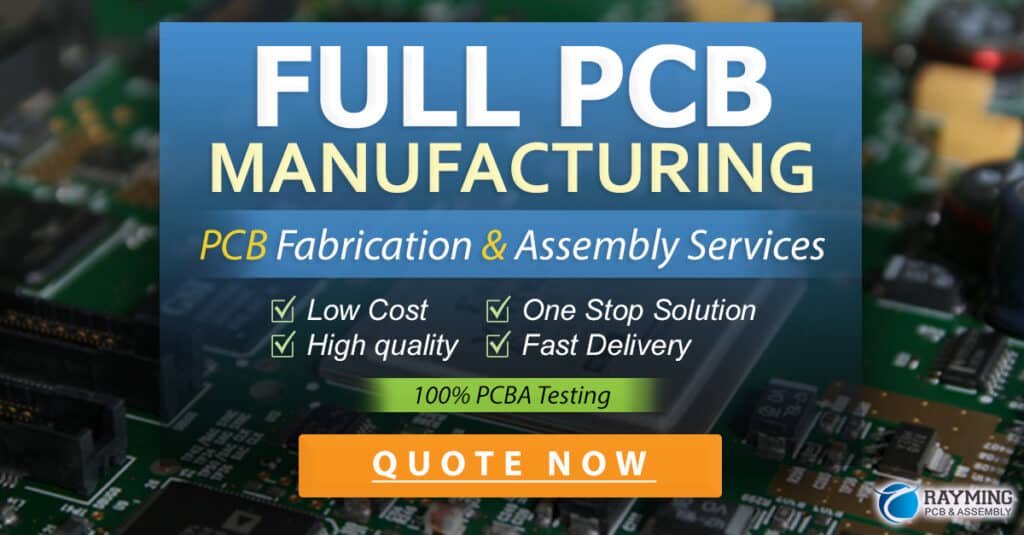
Importance of Adhering to PCB Classification Standards
Adhering to PCB classification standards, such as the Pattern Class and Drill Class, is crucial for several reasons:
-
Quality and Reliability: By following the guidelines set by the IPC for each class, manufacturers can ensure that the PCBs they produce meet the necessary quality and reliability standards. This helps to minimize the risk of failures, malfunctions, or performance issues in the end-product.
-
Consistency: Classification standards provide a common language and set of expectations for PCB manufacturers, designers, and end-users. This ensures that all parties involved in the PCB supply chain have a clear understanding of the requirements and can work together seamlessly.
-
Cost-effectiveness: Choosing the appropriate class for a given application helps to optimize costs. Overspecifying a PCB with a higher class than necessary can lead to increased manufacturing costs, while underspecifying may result in poor performance or reliability issues. By selecting the right class, manufacturers can strike a balance between cost and performance.
-
Simplified Communication: PCB classification standards simplify communication between stakeholders. Designers can specify the required class in their design files, and manufacturers can quickly understand the level of complexity and precision needed for the project. This streamlines the quoting, planning, and production processes.
-
Regulatory Compliance: In some industries, such as aerospace, military, or medical, adherence to specific PCB classification standards may be mandatory for regulatory compliance. Meeting these standards ensures that the PCBs are suitable for use in critical applications and have undergone the necessary quality control processes.
Frequently Asked Questions (FAQ)
-
Q: How do I determine the appropriate PCB Pattern Class for my application?
A: The choice of PCB Pattern Class depends on factors such as the required level of miniaturization, performance, and reliability. Class 1 is suitable for general-purpose applications, Class 2 for applications requiring higher reliability and performance, and Class 3 for the most demanding high-performance applications. -
Q: Can I use a higher PCB Pattern Class than required for my application?
A: Yes, you can use a higher PCB Pattern Class than required, but it will likely result in increased manufacturing costs. It is generally recommended to choose the class that meets your application’s requirements without overspecifying. -
Q: What is the difference between PCB Pattern Class and Drill Class?
A: PCB Pattern Class refers to the level of complexity and precision required in the design and fabrication of the conductive traces on a PCB, while Drill Class refers to the level of precision and accuracy required in the drilling of holes on a PCB. -
Q: Are there any specific industries that require adherence to certain PCB classification standards?
A: Yes, industries such as aerospace, military, and medical often have specific requirements for PCB classification standards. In these industries, adherence to the required standards may be mandatory for regulatory compliance. -
Q: How does the choice of PCB Drill Class affect the manufacturing process?
A: The choice of PCB Drill Class determines the level of precision and accuracy required in the drilling process. Higher drill classes (Class 2 and Class 3) require more advanced equipment, tighter tolerances, and specialized processes, which can increase manufacturing costs compared to lower classes (Class 1).
Conclusion
PCB classification, particularly the Pattern Class and Drill Class, plays a vital role in ensuring that PCBs meet the necessary requirements for quality, reliability, and performance. By understanding the different classes and their characteristics, designers and manufacturers can make informed decisions when selecting the appropriate class for a given application.
Adhering to PCB classification standards offers numerous benefits, including improved quality and reliability, consistency, cost-effectiveness, simplified communication, and regulatory compliance. By working together and following these standards, all stakeholders in the PCB supply chain can contribute to the production of high-quality, reliable, and cost-effective PCBs that meet the demands of modern electronics.
As technology continues to advance and new applications emerge, the importance of PCB classification will only continue to grow. Staying up-to-date with the latest standards and best practices in PCB design and manufacturing will be essential for companies looking to remain competitive and deliver cutting-edge products to their customers.
No responses yet