Introduction to PCB Classification
Printed Circuit Boards (PCBs) are essential components in modern electronic devices, providing a platform for mounting and interconnecting electronic components. The classification of PCBs is crucial for manufacturers, designers, and end-users to ensure that the boards meet the required specifications and performance standards. Two primary methods of classifying PCBs are based on their pattern class and drill class.
What is Pattern Class?
Pattern class refers to the level of complexity and precision required in the copper traces and spaces on a PCB. The pattern class is determined by the minimum trace width and spacing, as well as the overall density of the circuit layout. A higher pattern class indicates a more complex and precise board, while a lower pattern class signifies a simpler design.
What is Drill Class?
Drill class, on the other hand, relates to the size and accuracy of the holes drilled in a PCB. These holes are used for mounting components, vias, and other features. The drill class is determined by the smallest hole diameter and the tightest tolerance required on the board. A higher drill class indicates smaller, more precise holes, while a lower drill class allows for larger, less accurate holes.
Pattern Class Standards
The IPC (Association Connecting Electronics Industries) has established a set of standards for PCB pattern classes, known as the IPC-6012 standard. This standard defines three main pattern classes:
1. Class 1
Class 1 PCBs are the simplest and most basic level of boards. They are typically used in non-critical applications where cost is a primary concern, and the consequences of failure are minimal. Examples include consumer electronics, toys, and low-end appliances.
Characteristic | Requirement |
---|---|
Minimum trace width | 0.2 mm (8 mil) |
Minimum spacing | 0.2 mm (8 mil) |
Minimum annular ring | 0.05 mm (2 mil) |
2. Class 2
Class 2 PCBs are the most common type of boards used in the electronics industry. They strike a balance between cost and reliability, making them suitable for a wide range of applications, such as telecommunications, automotive systems, and industrial controls.
Characteristic | Requirement |
---|---|
Minimum trace width | 0.1 mm (4 mil) |
Minimum spacing | 0.1 mm (4 mil) |
Minimum annular ring | 0.025 mm (1 mil) |
3. Class 3
Class 3 PCBs are the most advanced and demanding type of boards, used in critical applications where reliability and performance are paramount. These include aerospace, military, and medical devices, where failure could result in significant financial losses or even loss of life.
Characteristic | Requirement |
---|---|
Minimum trace width | 0.075 mm (3 mil) |
Minimum spacing | 0.075 mm (3 mil) |
Minimum annular ring | 0.02 mm (0.8 mil) |
Drill Class Standards
The IPC-6012 standard also defines drill classes for PCBs, based on the Hole Size and accuracy requirements:
1. Drill Class 1
Drill Class 1 is the most relaxed standard, allowing for larger hole sizes and looser tolerances. This class is suitable for non-critical applications and larger components.
Characteristic | Requirement |
---|---|
Minimum hole diameter | 0.8 mm (31.5 mil) |
Hole size tolerance | ±0.1 mm (4 mil) |
2. Drill Class 2
Drill Class 2 is the most common standard, providing a balance between hole size, accuracy, and cost. This class is suitable for a wide range of applications and components.
Characteristic | Requirement |
---|---|
Minimum hole diameter | 0.5 mm (19.7 mil) |
Hole size tolerance | ±0.08 mm (3.1 mil) |
3. Drill Class 3
Drill Class 3 is the most stringent standard, requiring the smallest hole sizes and tightest tolerances. This class is necessary for high-density designs and critical applications.
Characteristic | Requirement |
---|---|
Minimum hole diameter | 0.2 mm (7.9 mil) |
Hole size tolerance | ±0.05 mm (2 mil) |
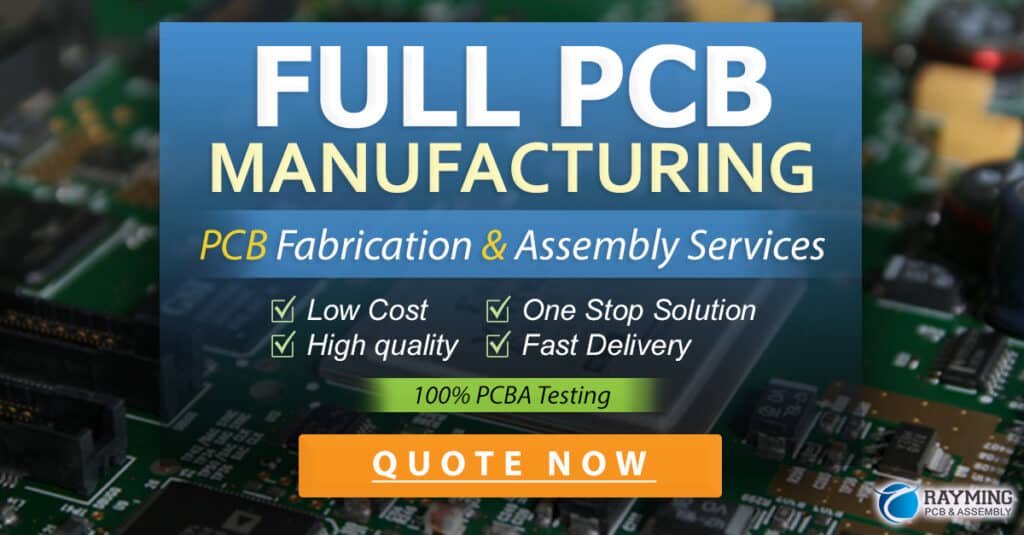
Factors Affecting PCB Classification
Several factors influence the classification of a PCB, including:
1. Application Requirements
The intended use of the PCB dictates the required pattern and drill classes. Critical applications demand higher classes to ensure reliability and performance, while non-critical applications can use lower classes to reduce costs.
2. Component Density
Higher component densities require more precise trace routing and smaller hole sizes, necessitating higher pattern and drill classes.
3. Manufacturing Capabilities
The manufacturing capabilities of the PCB fabricator determine the achievable pattern and drill classes. Advanced equipment and processes are necessary to produce high-class boards.
4. Cost Considerations
Higher pattern and drill classes generally result in increased manufacturing costs due to the need for more precise equipment, materials, and processes. Balancing cost and performance is essential when selecting the appropriate classes for a given application.
Benefits of Proper PCB Classification
Properly classifying PCBs according to their pattern and drill classes offers several benefits:
1. Improved Reliability
Selecting the appropriate classes ensures that the PCB meets the required performance and reliability standards for its intended application.
2. Optimized Manufacturing
Accurate classification allows manufacturers to optimize their processes and resources, reducing waste and improving efficiency.
3. Cost Savings
By choosing the appropriate classes for a given application, designers can minimize costs while still meeting performance requirements.
4. Simplified Communication
Using standardized classification systems, such as the IPC-6012 standard, simplifies communication between designers, manufacturers, and end-users, reducing the potential for errors and misunderstandings.
Challenges in PCB Classification
Despite the benefits of proper PCB classification, several challenges can arise:
1. Complexity
As PCB Designs become more complex and component densities increase, it can be difficult to determine the appropriate pattern and drill classes.
2. Evolving Standards
PCB classification standards, such as IPC-6012, are periodically updated to reflect advances in technology and manufacturing capabilities. Staying current with these changes can be challenging for designers and manufacturers.
3. Balancing Cost and Performance
Finding the right balance between cost and performance when selecting pattern and drill classes can be difficult, particularly for applications with tight budgets or strict performance requirements.
4. Manufacturing Limitations
Not all PCB fabricators have the capabilities to produce boards with the highest pattern and drill classes, which can limit design options or increase costs.
Best Practices for PCB Classification
To ensure the proper classification of PCBs and optimize their performance and cost, designers and manufacturers should follow these best practices:
1. Understand Application Requirements
Thoroughly assess the performance, reliability, and cost requirements of the intended application to determine the appropriate pattern and drill classes.
2. Collaborate with Manufacturers
Work closely with PCB fabricators to understand their capabilities and limitations, ensuring that the selected classes are achievable and cost-effective.
3. Stay Current with Standards
Regularly review and update knowledge of PCB classification standards, such as IPC-6012, to ensure compliance and take advantage of new technologies and processes.
4. Use Design for Manufacturing (DFM) Principles
Incorporate DFM principles into the PCB design process to optimize manufacturability, reliability, and cost, while meeting the required pattern and drill classes.
5. Consider Alternative Materials and Processes
Explore the use of alternative materials and manufacturing processes, such as high-density interconnect (HDI) technology, to achieve higher pattern and drill classes without significantly increasing costs.
Frequently Asked Questions (FAQ)
1. What is the difference between pattern class and drill class in PCB classification?
Pattern class refers to the complexity and precision of the copper traces and spaces on a PCB, while drill class relates to the size and accuracy of the holes drilled in the board.
2. What are the main pattern classes defined by the IPC-6012 standard?
The IPC-6012 standard defines three main pattern classes: Class 1 (simplest), Class 2 (most common), and Class 3 (most advanced).
3. How do the application requirements influence the selection of pattern and drill classes?
The intended use of the PCB dictates the required pattern and drill classes. Critical applications demand higher classes to ensure reliability and performance, while non-critical applications can use lower classes to reduce costs.
4. What are some of the challenges in PCB classification?
Some of the challenges in PCB classification include increasing complexity of designs, evolving standards, balancing cost and performance, and manufacturing limitations.
5. How can designers and manufacturers ensure proper PCB classification?
To ensure proper PCB classification, designers and manufacturers should understand application requirements, collaborate with each other, stay current with standards, use Design for Manufacturing (DFM) principles, and consider alternative materials and processes.
Conclusion
PCB classification based on pattern class and drill class is essential for ensuring that boards meet the required specifications and performance standards for their intended applications. By understanding the IPC-6012 standard, the factors affecting classification, and the benefits and challenges involved, designers and manufacturers can make informed decisions and optimize the performance, reliability, and cost of their PCBs. Adopting best practices, such as collaborating with manufacturers, staying current with standards, and using DFM principles, can further enhance the success of PCB projects and contribute to the advancement of the electronics industry as a whole.
No responses yet