Introduction to PCB Cameras
A PCB camera, also known as a board camera, is a compact, lightweight, and highly integrated camera module designed for easy incorporation into various electronic devices and systems. These cameras are built on a printed circuit board (PCB) and typically include an image sensor, lens, and essential electronic components required for capturing images or videos. PCB cameras have gained popularity due to their versatility, affordability, and ease of integration, making them suitable for a wide range of applications, including surveillance, robotics, industrial inspection, and embedded systems.
Key Features of PCB Cameras
-
Compact Size: PCB cameras are designed to be small and lightweight, allowing for easy integration into space-constrained devices and systems.
-
High Integration: These cameras often include essential components such as an image sensor, lens, and basic image processing capabilities on a single board, simplifying the integration process.
-
Varied Resolutions: PCB cameras are available in a range of resolutions, from low-resolution VGA (640×480) to high-resolution 4K (3840×2160), catering to different application requirements.
-
Multiple Interfaces: Board cameras support various interface options, such as USB, HDMI, MIPI, and Ethernet, enabling easy connectivity with host systems.
-
Customizable: Many PCB camera manufacturers offer customization options, allowing customers to choose specific features, lenses, or form factors to suit their unique needs.
Types of PCB Cameras
Based on Image Sensor Technology
1. CCD (Charge-Coupled Device) PCB Cameras
CCD sensors have been widely used in digital imaging for decades due to their excellent image quality, low noise, and high sensitivity. CCD PCB cameras are known for their superior color reproduction and dynamic range, making them suitable for applications that require high-quality images, such as industrial inspection and scientific imaging.
2. CMOS (Complementary Metal-Oxide-Semiconductor) PCB Cameras
CMOS sensors have gained popularity in recent years due to their lower power consumption, higher integration capabilities, and lower manufacturing costs compared to CCD sensors. CMOS PCB cameras offer faster frame rates, making them ideal for applications that require real-time video capture, such as surveillance and robotics.
Based on Interface
1. USB PCB Cameras
USB PCB cameras are designed to connect directly to a host system using a USB interface, which provides both power and data transfer capabilities. These cameras are easy to install and use, making them popular for applications such as webcams, microscopy, and machine vision.
2. HDMI PCB Cameras
HDMI PCB cameras output digital video signals directly through an HDMI interface, allowing for easy connection to displays, monitors, or video capture devices. These cameras are commonly used in applications such as surveillance, drones, and automotive systems.
3. MIPI PCB Cameras
MIPI (Mobile Industry Processor Interface) PCB cameras are designed for mobile and embedded applications, offering high-speed serial interfaces for connecting to mobile processors and system-on-chips (SoCs). These cameras are commonly used in smartphones, tablets, and other portable devices.
4. Ethernet PCB Cameras
Ethernet PCB cameras feature an Ethernet interface, allowing for easy integration into IP-based networks. These cameras are ideal for applications that require remote access, such as IP surveillance systems and industrial automation.
PCB Camera Specifications
When selecting a PCB camera for a specific application, it is essential to consider the following key specifications:
Specification | Description |
---|---|
Resolution | The number of pixels in the image sensor, determining the level of detail captured (e.g., VGA, 720p, 1080p, 4K). |
Frame Rate | The number of frames the camera can capture per second (fps), important for applications requiring smooth video or high-speed imaging. |
Sensor Size | The physical dimensions of the image sensor, affecting low-light performance and depth of field. |
Lens Mount | The type of lens mount compatible with the camera (e.g., M12, CS, C). |
Focal Length | The distance between the lens and the image sensor, determining the camera’s field of view and magnification. |
Interface | The type of interface used to connect the camera to the host system (e.g., USB, HDMI, MIPI, Ethernet). |
Power Requirements | The voltage and current required to power the camera, which can be supplied through the interface or external power connectors. |
Operating Temperature | The temperature range within which the camera can operate reliably, important for outdoor or industrial applications. |
Dimensions and Weight | The physical size and weight of the camera module, crucial for integration into space-constrained devices or weight-sensitive applications. |
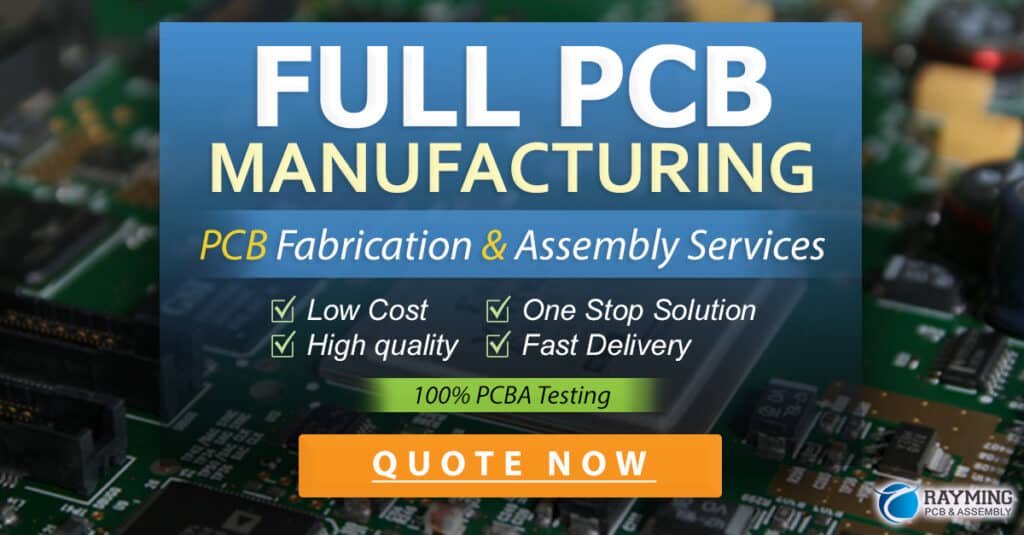
Applications of PCB Cameras
PCB cameras find applications in a wide range of industries and sectors, including:
1. Surveillance and Security
Compact and easily integrated PCB cameras are widely used in surveillance and security systems, such as IP cameras, dome cameras, and body-worn cameras. These cameras help monitor premises, detect intrusions, and ensure public safety.
2. Industrial Inspection and Machine Vision
PCB cameras play a crucial role in industrial inspection and machine vision applications, enabling automated quality control, defect detection, and process monitoring. High-resolution cameras with fast frame rates and specialized lenses are used to capture detailed images of products and components for analysis.
3. Robotics and Drones
Board cameras are essential components in robotics and drone applications, providing visual input for navigation, obstacle avoidance, and object recognition. Lightweight and low-power consumption cameras are preferred for these applications to maximize battery life and maneuverability.
4. Medical and Scientific Imaging
PCB cameras are used in various medical and scientific imaging applications, such as microscopy, endoscopy, and dental imaging. High-quality cameras with specialized lenses and lighting are employed to capture detailed images for diagnosis, research, and documentation purposes.
5. Automotive and Transportation
PCB cameras are increasingly being integrated into automotive and transportation systems for applications such as backup cameras, driver monitoring, and autonomous vehicle perception. Rugged and reliable cameras with wide operating temperature ranges are essential for these applications.
6. Consumer Electronics
Board cameras are widely used in consumer electronic devices, such as smartphones, tablets, laptops, and smart home devices. These cameras enable features like video conferencing, facial recognition, and augmented reality applications.
Choosing the Right PCB Camera
When selecting a PCB camera for a specific application, consider the following factors:
-
Resolution and Image Quality: Choose a camera with a resolution and image quality suitable for your application’s requirements. Higher resolutions may be necessary for applications like industrial inspection, while lower resolutions may suffice for basic surveillance or consumer applications.
-
Frame Rate: Consider the required frame rate for your application. Higher frame rates are essential for applications involving fast-moving objects or real-time video processing, while lower frame rates may be adequate for static or slow-moving scenes.
-
Interface: Select a camera with an interface compatible with your host system and application requirements. USB and HDMI interfaces are common for general-purpose applications, while MIPI and Ethernet interfaces are more specialized for mobile and networked applications, respectively.
-
Lens and Optical Characteristics: Choose a camera with the appropriate lens mount and focal length for your application. Wide-angle lenses are suitable for applications requiring a large field of view, while telephoto lenses are ideal for long-distance imaging or surveillance.
-
Environmental Factors: Consider the operating environment of your application and choose a camera with suitable environmental ratings, such as temperature range, humidity resistance, and ingress protection (IP) ratings for outdoor or industrial use.
-
Integration and Software Support: Ensure that the selected camera has adequate documentation, software development kits (SDKs), and technical support from the manufacturer to facilitate seamless integration into your application.
-
Cost and Availability: Consider the cost and availability of the camera, as well as any associated development costs, such as lenses, cables, and software licenses. Evaluate the long-term availability and support for the camera model to ensure a reliable supply for your application’s lifecycle.
By carefully considering these factors and understanding the specific requirements of your application, you can select the most suitable PCB camera to meet your needs.
Conclusion
PCB cameras have revolutionized the way imaging technology is integrated into various devices and systems, offering compact, versatile, and cost-effective solutions for a wide range of applications. By understanding the key features, types, specifications, and application areas of PCB cameras, engineers and developers can make informed decisions when selecting and integrating these cameras into their projects. As technology continues to advance, PCB cameras are expected to become even more capable, efficient, and accessible, driving innovation across industries and enabling new possibilities in imaging and machine vision.
Frequently Asked Questions (FAQ)
1. What is the difference between CCD and CMOS PCB cameras?
CCD (Charge-Coupled Device) and CMOS (Complementary Metal-Oxide-Semiconductor) are two main types of image sensor technologies used in PCB cameras. CCD sensors are known for their excellent image quality, low noise, and high sensitivity, making them suitable for applications requiring high-quality images. On the other hand, CMOS sensors offer lower power consumption, higher integration capabilities, and faster frame rates, making them ideal for applications that require real-time video capture or have power constraints.
2. Can I customize a PCB camera for my specific application?
Yes, many PCB camera manufacturers offer customization options to cater to specific application requirements. Customization options may include choosing specific resolutions, lenses, interfaces, or form factors. Some manufacturers also provide custom firmware development and integration support to ensure the camera meets your application’s unique needs.
3. What is the typical power consumption of a PCB camera?
The power consumption of a PCB camera varies depending on factors such as the image sensor technology, resolution, frame rate, and interface. Generally, CMOS cameras consume less power than CCD cameras. A typical low-resolution (VGA) USB camera may consume around 0.5W, while a high-resolution (1080p) Ethernet camera may consume around 2-3W. It is essential to consider the power requirements of the camera when designing your system and ensure that the power supply can meet the camera’s demand.
4. How do I integrate a PCB camera into my embedded system?
Integrating a PCB camera into an embedded system typically involves the following steps:
- Choose a camera with an interface compatible with your embedded platform (e.g., USB, MIPI, Ethernet).
- Connect the camera to your embedded board using the appropriate cables and connectors.
- Install the necessary drivers and software development kits (SDKs) provided by the camera manufacturer.
- Develop your application software using the provided APIs and libraries to control the camera and process the captured images or video.
Many camera manufacturers provide detailed documentation, sample code, and technical support to assist with the integration process.
5. What are the key considerations when selecting a lens for a PCB camera?
When selecting a lens for a PCB camera, consider the following factors:
-
Focal Length: Choose a focal length that provides the desired field of view for your application. Shorter focal lengths offer wider fields of view, while longer focal lengths provide narrower fields of view and higher magnification.
-
Aperture: The lens aperture determines the amount of light that reaches the image sensor. A larger aperture (lower f-number) allows more light to enter the camera, which is beneficial for low-light conditions. However, larger apertures also result in a shallower depth of field.
-
Image Circle: Ensure that the lens’s image circle is large enough to cover the camera’s image sensor size to avoid vignetting or dark corners in the captured image.
-
Lens Mount: Select a lens with a mount compatible with your PCB camera. Common lens mounts for board cameras include M12, CS, and C-mount.
-
Optical Quality: Consider the optical quality of the lens, including factors such as sharpness, distortion, and chromatic aberration, which can affect the overall image quality.
By carefully considering these factors and the specific requirements of your application, you can select the most suitable lens for your PCB camera to achieve the desired imaging performance.
No responses yet