Understanding the Factors That Affect PCB Price
Several key factors contribute to the overall cost of a PCB. By understanding these elements, you can make informed decisions when designing and sourcing your boards.
PCB Size and Complexity
The physical dimensions and complexity of your PCB design play a significant role in determining its price. Larger boards require more raw materials and longer processing times, while complex designs with intricate traces, multiple layers, and high component density demand more advanced manufacturing techniques.
PCB Size | Relative Cost |
---|---|
Small (< 50 cm²) | Low |
Medium (50-200 cm²) | Moderate |
Large (> 200 cm²) | High |
Material Selection
The choice of substrate material directly impacts PCB cost. Standard FR-4 is the most common and economical option, while high-performance materials like Rogers or Isola can significantly increase expenses. Consider your application’s requirements and choose materials that balance performance and cost.
Material | Relative Cost |
---|---|
FR-4 | Low |
High-Tg FR-4 | Moderate |
Rogers | High |
Isola | High |
Layer Count
Multi-layer PCBs offer increased routing density and improved signal integrity but come at a higher cost compared to single or double-layer boards. Each additional layer requires more processing steps and materials, driving up the overall price.
Layers | Relative Cost |
---|---|
1-2 | Low |
4 | Moderate |
6-8 | High |
10+ | Very High |
Surface Finish
The choice of surface finish affects both the cost and the performance of your PCB. While cheaper options like HASL (Hot Air Solder Leveling) are suitable for many applications, advanced finishes like ENIG (Electroless Nickel Immersion Gold) or ENEPIG (Electroless Nickel Electroless Palladium Immersion Gold) offer improved solderability and durability at a higher price point.
Finish | Relative Cost |
---|---|
HASL | Low |
Lead-Free HASL | Moderate |
ENIG | High |
ENEPIG | Very High |
Order Quantity
As with most manufacturing processes, ordering PCBs in larger quantities generally results in lower per-unit costs. This is due to the fixed setup costs associated with each production run, which are spread across more boards in high-volume orders.
Quantity | Relative Cost per Unit |
---|---|
1-10 | Very High |
11-100 | High |
101-500 | Moderate |
501-1000 | Low |
1000+ | Very Low |
Strategies for Controlling PCB Costs
Now that we understand the factors influencing PCB pricing, let’s explore some strategies for keeping costs under control.
Optimize Your Design
Efficient PCB design is crucial for minimizing manufacturing costs. Consider the following best practices:
- Keep your board size as small as possible while maintaining functionality.
- Use standard materials and finishes whenever feasible.
- Minimize the number of layers required by optimizing component placement and routing.
- Adhere to your manufacturer’s design guidelines to avoid unnecessary complications or rework.
Choose the Right Manufacturer
Selecting a reputable PCB manufacturer with experience in your specific industry or application can help ensure high-quality boards at competitive prices. Consider factors such as:
- Manufacturing capabilities and technology
- Quality control processes and certifications
- Turnaround times and delivery options
- Customer support and communication
Leverage Economies of Scale
Whenever possible, consolidate your PCB orders to take advantage of volume discounts. If your production schedule allows, consider combining multiple designs into a single panel to reduce setup costs and improve efficiency.
Implement Design for Manufacturing (DFM)
Collaborating with your PCB manufacturer during the design phase can help identify potential issues early on and reduce the risk of costly revisions or production delays. Implement Design for Manufacturing (DFM) principles to ensure your boards are optimized for the manufacturing process, minimizing the chances of defects or assembly problems.
Regularly Review and Negotiate Pricing
Establish a regular review process to assess your PCB costs and identify opportunities for savings. Stay up-to-date with market trends and periodically negotiate pricing with your manufacturer to ensure you’re getting the best value for your investment.
FAQ
-
Q: How can I estimate the cost of my PCB design before placing an order?
A: Most PCB manufacturers offer online quoting tools that allow you to input your design specifications and receive an instant price estimate. Additionally, you can request quotes from multiple suppliers to compare prices and lead times. -
Q: Are there any hidden costs I should be aware of when ordering PCBs?
A: Some manufacturers may charge additional fees for services like design review, tooling, or expedited shipping. Be sure to clarify all costs upfront and factor them into your budget to avoid surprises. -
Q: How can I balance cost and quality when sourcing PCBs?
A: Focus on finding a reputable manufacturer with a proven track record of producing high-quality boards. While it may be tempting to choose the lowest-priced option, inferior quality can lead to costly rework or product failures down the line. -
Q: What are some common mistakes that can drive up PCB costs?
A: Common mistakes include overdesigning boards with unnecessary features, failing to optimize component placement and routing, and not adhering to the manufacturer’s design guidelines. These issues can result in higher production costs and potential delays. -
Q: How can I stay informed about PCB pricing trends and cost-saving opportunities?
A: Regularly engage with your PCB manufacturer and stay updated on industry news and trends. Attend trade shows, participate in online forums, and subscribe to relevant publications to gain insights into new technologies and best practices that can help you optimize your PCB costs.
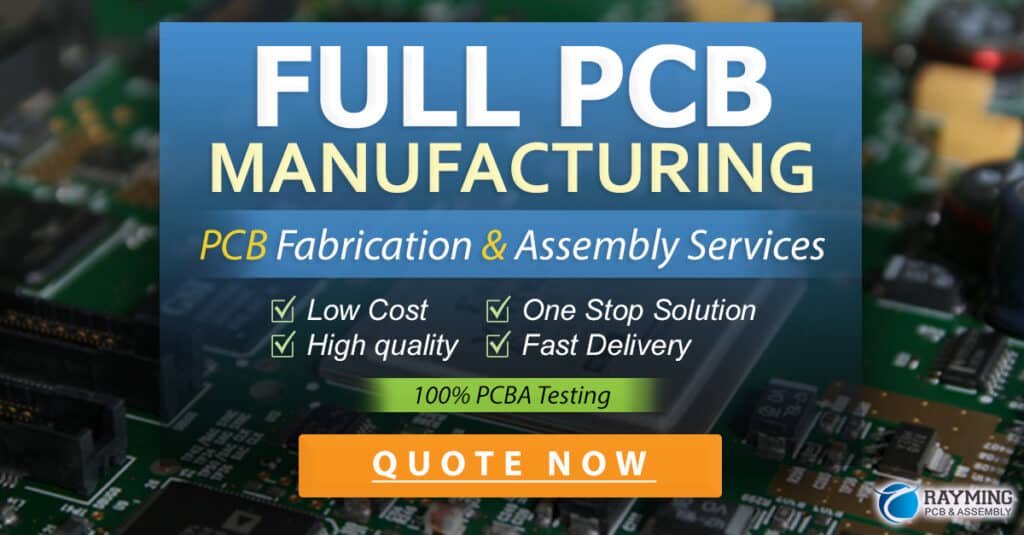
Conclusion
Controlling PCB costs is essential for maintaining a competitive edge in today’s fast-paced electronics industry. By understanding the factors that influence pricing and implementing smart design and sourcing strategies, you can effectively manage your PCB expenses without sacrificing quality or performance.
Remember to collaborate closely with your PCB manufacturer, stay informed about industry trends, and continuously refine your processes to achieve the best possible balance of cost, quality, and lead time for your specific applications. With a proactive approach to PCB cost management, you can position your company for long-term success in an increasingly demanding market.
No responses yet