What is a PCB Blank?
A PCB (Printed Circuit Board) blank is a bare circuit board without any components soldered onto it. It consists of a substrate material, typically FR-4 (a type of fiberglass), with copper traces etched onto one or both sides. These copper traces form the electrical connections between components that will be added later during the assembly process.
PCB blanks come in various sizes, thicknesses, and materials to suit different applications. They can be single-sided (copper on one side), double-sided (copper on both sides), or multi-layered (multiple layers of copper separated by insulating material).
Types of PCB Blanks
There are several types of PCB blanks available, each with its own characteristics and applications:
Type | Description | Applications |
---|---|---|
Single-sided | Copper on one side of the substrate | Simple, low-cost projects |
Double-sided | Copper on both sides of the substrate | More complex projects requiring more connections |
Multi-layer | Multiple layers of copper separated by insulating material | High-density, complex projects like computer motherboards |
Flexible | Made from flexible substrate materials like polyimide | Wearable electronics, compact devices |
Rigid-Flex | Combination of rigid and flexible sections | Devices requiring both stability and flexibility |
High-Frequency | Made with special materials for high-frequency signals | RF and microwave applications |
Choosing the Right PCB Blank
When selecting a PCB blank for your project, consider the following factors:
Size and Shape
PCB blanks come in various standard sizes, such as:
- 5×7 cm
- 7×10 cm
- 10×15 cm
- 20×30 cm
Choose a size that accommodates your components and provides enough space for routing traces. If your project requires a specific shape, you may need to use a custom-sized PCB blank or have it cut to size.
Thickness
The thickness of a PCB blank is measured in ounces (oz) of copper per square foot. Common thicknesses include:
- 0.5 oz (17.5 μm)
- 1 oz (35 μm)
- 2 oz (70 μm)
Thicker copper layers can carry more current and are better for high-power applications, while thinner layers are suitable for low-power, high-density designs.
Material
FR-4 is the most common substrate material for PCB blanks due to its good electrical insulation properties and mechanical stability. However, other materials like aluminum, ceramic, or polyimide may be used for specific applications:
Material | Properties | Applications |
---|---|---|
FR-4 | Good insulation, mechanical stability | General-purpose electronics |
Aluminum | Good heat dissipation | High-power, heat-sensitive applications |
Ceramic | Excellent insulation, thermal stability | High-temperature, high-frequency applications |
Polyimide | Flexible, high-temperature resistance | Flexible electronics, aerospace applications |
Designing Your PCB
Before you can use a PCB blank, you need to design your circuit and create the PCB layout. This process involves several steps:
Schematic Design
Create a schematic diagram of your circuit using electronic design automation (EDA) software like KiCad or EAGLE. This step involves placing component symbols (e.g., resistors, capacitors, ICs) on a canvas and connecting them with virtual wires based on their electrical connections. Carefully review your schematic for errors before proceeding to the next step.
Component Placement
Transfer your schematic to a PCB layout editor in your EDA software. Arrange the components on the board, taking into consideration factors like signal integrity, heat dissipation, and mechanical constraints. Aim for a logical, organized layout that minimizes the distance between connected components.
Routing
Connect the components using the copper traces on your PCB blank. This process can be done manually or with the help of autorouting algorithms in your EDA software. Consider the current-carrying capacity of your traces, as well as signal integrity issues like crosstalk and electromagnetic interference (EMI).
Design Rule Check (DRC)
Perform a DRC to ensure your PCB layout adheres to manufacturing and electrical constraints. This includes checking for minimum trace widths, clearances between traces, and drill hole sizes. Make necessary adjustments based on the DRC results.
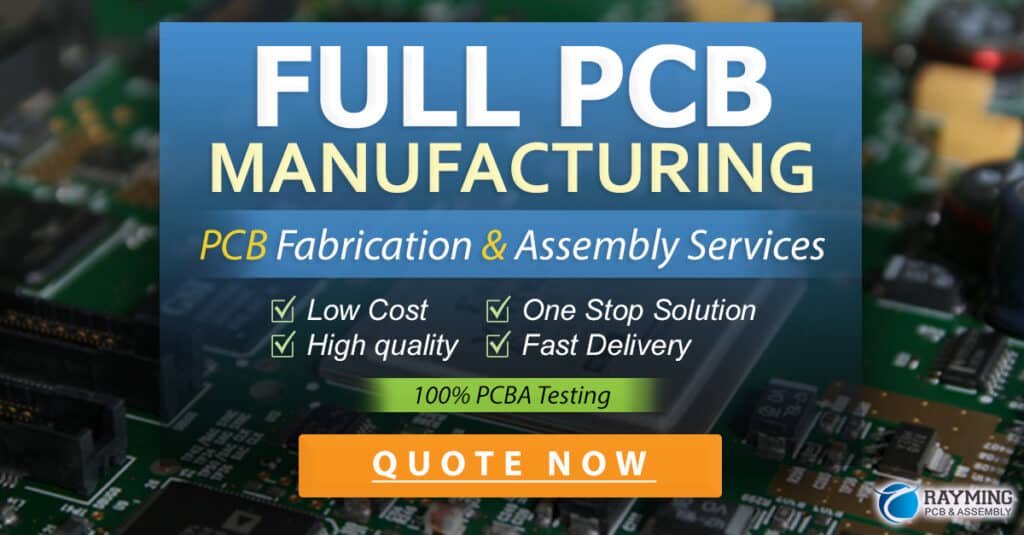
Manufacturing Your PCB
Once your PCB design is complete, you can proceed to manufacture your board using the PCB blank. There are two main methods for transferring your design onto the blank: etching and milling.
Etching
Etching involves removing unwanted copper from the PCB blank to leave behind the desired traces. The process typically follows these steps:
- Print your PCB layout onto a transparent film using a laser printer.
- Clean the copper surface of your PCB blank with steel wool or fine sandpaper.
- Apply a light-sensitive photoresist coating to the copper surface.
- Place the transparent film onto the photoresist and expose it to UV light.
- Develop the photoresist using a sodium hydroxide solution, which removes the unexposed areas.
- Etch away the exposed copper using ferric chloride or ammonium persulfate solution.
- Remove the remaining photoresist using acetone or a specialized stripping solution.
Milling
Milling uses a computer-controlled rotary tool to remove copper from the PCB blank directly. This process is often faster and more precise than etching, but it requires specialized equipment. Milling follows these general steps:
- Export your PCB layout from your EDA software in a format compatible with your milling machine’s software (e.g., Gerber, G-code).
- Load your PCB blank into the milling machine.
- Set up the milling parameters (e.g., tool size, feed rate, spindle speed) based on your design and the capabilities of your machine.
- Start the milling process and monitor it for any issues.
Assembling Your PCB
After manufacturing your PCB, you can proceed to assemble the components onto the board. This process involves several steps:
Soldering
Soldering is the process of joining two metal surfaces (component leads and PCB pads) using a molten filler metal (solder). To solder components onto your PCB:
- Apply a small amount of solder paste or flux to the PCB pads.
- Place the component leads through the corresponding holes in the PCB.
- Heat the connection with a soldering iron until the solder melts and forms a strong bond between the lead and pad.
- Repeat this process for all components.
Inspection
After soldering, inspect your PCB for any issues like cold joints, bridged connections, or misaligned components. Use a magnifying glass or microscope to visually inspect the solder joints, and use a multimeter to check for continuity and short circuits.
Testing
Once your PCB is assembled and inspected, it’s time to test its functionality. Power on the board and use test equipment like oscilloscopes, logic analyzers, or specialized testing jigs to verify that it performs as expected. If you encounter any issues, troubleshoot the problem by checking for faulty components, poor solder joints, or design errors.
Frequently Asked Questions (FAQ)
1. Can I use any type of printer to print my PCB layout onto a transparent film?
No, you should use a laser printer for this purpose. Inkjet printers do not produce the required opacity and resolution for the photoresist exposure process.
2. What safety precautions should I take when etching or milling my PCB?
Always wear protective gloves, goggles, and a face mask when handling etching or milling chemicals. Work in a well-ventilated area and dispose of any waste materials according to local regulations.
3. How do I choose the right solder for my PCB assembly?
Consider factors like melting temperature, alloy composition, and the type of components you are soldering. Lead-free solder (e.g., Sn99.3Cu0.7) is commonly used due to environmental regulations, but leaded solder (e.g., Sn63Pb37) may be required for certain applications.
4. What should I do if my PCB doesn’t work after assembly?
Systematically troubleshoot the problem by checking for poor solder joints, damaged components, or design errors. Use a multimeter to check for continuity and short circuits, and refer to your schematic and layout to identify potential issues.
5. Can I reuse a PCB blank after etching or milling?
No, once a PCB blank has been etched or milled, it cannot be reused for another design. However, you may be able to salvage certain areas of the board for smaller projects if the copper is still intact.
Conclusion
PCB blanks are the foundation of any electronic project, providing the base for components and connections. By understanding the different types of PCB blanks, designing your circuit carefully, and following proper manufacturing and assembly techniques, you can create functional, reliable PCBs for a wide range of applications.
Remember to always prioritize safety when working with chemicals and high temperatures, and take the time to thoroughly test and troubleshoot your PCB before using it in your final project. With practice and attention to detail, you can master the art of PCB design and assembly using PCB blanks.
No responses yet