Tip 1: Choose the Right PCB Design Software
Selecting the appropriate PCB design software is the first step towards ensuring a smooth PCB Assembly process. The software should be user-friendly, feature-rich, and compatible with your manufacturing requirements. Some popular PCB design software options include:
- Altium Designer
- Eagle
- KiCad
- OrCAD
- Mentor Graphics PADS
When choosing PCB design software, consider factors such as ease of use, library management, design rule checking (DRC), and integration with other tools in your workflow.
Tip 2: Optimize Your PCB Layout
An optimized PCB layout is crucial for a smooth assembly process. Here are some guidelines to follow:
- Keep component placement logical and organized
- Minimize the use of vias and through-holes
- Ensure adequate spacing between components
- Use appropriate trace widths and clearances
- Consider the manufacturing capabilities of your assembly partner
By optimizing your PCB layout, you can reduce the risk of manufacturing issues, improve signal integrity, and enhance the overall reliability of your product.
Tip 3: Select the Right Components
Component selection plays a significant role in the success of your PCB assembly process. When choosing components, consider the following factors:
- Availability and lead times
- Compatibility with your PCB design
- Quality and reliability
- Cost-effectiveness
- Packaging options (e.g., SMD, through-hole)
It’s essential to strike a balance between cost, performance, and availability to ensure a smooth assembly process and a high-quality final product.
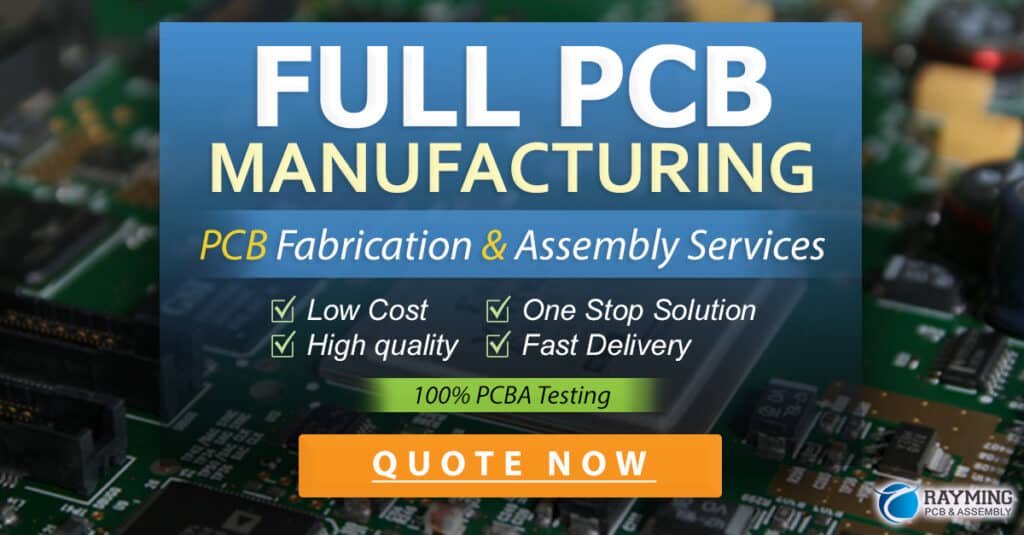
Tip 4: Create Comprehensive Documentation
Comprehensive documentation is essential for communicating your requirements to your assembly partner and ensuring a smooth PCB assembly process. Your documentation should include:
- Bill of Materials (BOM)
- Assembly drawings
- Gerber files
- Solder paste stencil files
- Test specifications
Ensure that your documentation is accurate, up-to-date, and clearly communicates your expectations to avoid misunderstandings and delays in the assembly process.
Tip 5: Choose a Reliable PCB Assembly Partner
Selecting a reliable PCB assembly partner is crucial for ensuring a smooth assembly process. When evaluating potential partners, consider the following factors:
- Experience and expertise in PCB assembly
- Quality control processes and certifications (e.g., ISO 9001, IPC standards)
- Manufacturing capabilities and capacity
- Communication and customer support
- Pricing and lead times
A reliable assembly partner will work closely with you to understand your requirements, provide valuable insights, and deliver high-quality results.
Tip 6: Implement Effective Communication Channels
Effective communication is key to ensuring a smooth PCB assembly process. Establish clear communication channels with your assembly partner, including:
- Regular status updates and progress reports
- Open lines of communication for questions and concerns
- Clearly defined points of contact
- Agreed-upon response times
By maintaining open and transparent communication, you can quickly address any issues that arise and ensure that your project stays on track.
Tip 7: Conduct Thorough Testing and Inspection
Thorough testing and inspection are essential for ensuring the quality and reliability of your assembled PCBs. Implement a comprehensive testing and inspection plan that includes:
- Visual inspection
- Automated Optical Inspection (AOI)
- X-ray inspection
- Functional testing
- Burn-in testing
By catching defects and issues early in the assembly process, you can minimize rework, delays, and additional costs.
Tip 8: Plan for Manufacturing Scalability
As your product evolves and demand grows, it’s essential to plan for manufacturing scalability. Consider the following factors when planning for scalability:
- Modular PCB design
- Flexible manufacturing processes
- Robust supply chain management
- Inventory management and forecasting
By designing your PCB and assembly process with scalability in mind, you can ensure a smooth transition from prototype to mass production.
Tip 9: Continuously Monitor and Improve the Process
Continuously monitoring and improving your PCB assembly process is crucial for maintaining quality, efficiency, and cost-effectiveness. Implement a continuous improvement program that includes:
- Regular process audits and reviews
- Data collection and analysis
- Identification of improvement opportunities
- Implementation of corrective and preventive actions
By continuously refining your PCB assembly process, you can stay ahead of the competition and deliver high-quality products to your customers.
PCB Assembly Process Improvement Techniques
Technique | Description | Benefits |
---|---|---|
Lean Manufacturing | Focuses on eliminating waste and optimizing efficiency | Reduces costs, improves quality, and increases productivity |
Six Sigma | A data-driven approach to reducing defects and variability | Enhances product quality and customer satisfaction |
Kaizen | A philosophy of continuous improvement through small, incremental changes | Fosters a culture of innovation and employee engagement |
5S | A workplace organization method that emphasizes cleanliness, order, and standardization | Improves safety, productivity, and morale |
Total Productive Maintenance (TPM) | A proactive approach to equipment maintenance and optimization | Reduces downtime, increases equipment reliability, and improves overall equipment effectiveness (OEE) |
By implementing these improvement techniques, you can continuously enhance your PCB assembly process and stay competitive in the ever-evolving electronics industry.
Frequently Asked Questions (FAQ)
-
Q: What is the difference between SMD and through-hole components?
A: Surface Mount Device (SMD) components are mounted directly onto the surface of the PCB, while through-hole components have leads that are inserted into holes drilled in the PCB and soldered on the opposite side. SMD components are smaller and more suitable for high-density designs, while through-hole components offer stronger mechanical connections and are easier to work with for hand soldering. -
Q: What is the purpose of a solder paste stencil in the PCB assembly process?
A: A solder paste stencil is a thin metal sheet with apertures that correspond to the pads on the PCB. It is used to apply solder paste to the pads before component placement. The stencil ensures that the correct amount of solder paste is deposited on each pad, which is crucial for achieving reliable solder joints during the reflow soldering process. -
Q: What is the difference between reflow soldering and wave soldering?
A: Reflow soldering is used for SMD components and involves applying solder paste to the PCB, placing components, and then heating the entire assembly in a reflow oven to melt the solder and form connections. Wave soldering is used for through-hole components and involves passing the PCB over a molten solder wave, which coats the component leads and pads to form solder joints. -
Q: What is the purpose of Automated Optical Inspection (AOI) in the PCB assembly process?
A: AOI is a machine vision technique used to automatically inspect assembled PCBs for defects such as missing components, incorrect component placement, solder bridges, and insufficient solder. AOI systems compare the assembled PCB to a reference image or CAD data to identify any discrepancies. This helps to catch defects early in the assembly process, reducing rework and improving overall quality. -
Q: What are some common certifications that PCB assembly partners should have?
A: Some common certifications that PCB assembly partners should have include ISO 9001 (Quality Management System), IPC-A-610 (Acceptability of Electronic Assemblies), IPC-J-STD-001 (Requirements for Soldered Electrical and Electronic Assemblies), and IPC-A-600 (Acceptability of Printed Boards). These certifications demonstrate a commitment to quality, reliability, and adherence to industry standards.
In conclusion, ensuring a smooth PCB assembly process requires careful planning, attention to detail, and a commitment to continuous improvement. By following the 9 tips outlined in this article and working closely with a reliable assembly partner, you can minimize risks, improve efficiency, and deliver high-quality products to your customers.
No responses yet