What is a PCB antipad?
A PCB antipad, also known as a thermal relief or thermal spoke, is a design feature used in printed circuit boards (PCBs) to improve the solderability and reliability of through-hole components. It is a small, non-conductive area surrounding a hole or via on a PCB, which reduces the amount of copper connected to the hole or via.
How Does a PCB Antipad Work?
When a through-hole component is soldered to a PCB, the copper surrounding the hole acts as a heat sink, drawing heat away from the solder joint. This can lead to insufficient heat reaching the solder, resulting in poor solder joint formation and potential reliability issues.
By incorporating an antipad around the hole, the amount of copper connected to the hole is reduced, allowing more heat to be concentrated on the solder joint during the soldering process. This improves the flow of solder and ensures a better connection between the component lead and the PCB.
Benefits of Using PCB Antipads
1. Improved Solderability
The primary benefit of using PCB antipads is improved solderability. By reducing the heat-sinking effect of the copper surrounding the hole, more heat is available to melt the solder and create a strong, reliable connection between the component lead and the PCB.
2. Enhanced Reliability
With better solder joint formation, the overall reliability of the PCB Assembly is enhanced. Well-formed solder joints are less likely to fail due to thermal stress, vibration, or other environmental factors, leading to a longer product lifespan and reduced risk of field failures.
3. Faster Soldering Process
PCB antipads can also contribute to a faster soldering process. As the solder melts more easily and flows better into the joint, the time required for soldering each component is reduced. This can lead to increased production efficiency and lower manufacturing costs.
4. Better Compatibility with Lead-Free Solder
Lead-free solder alloys, which have become more common due to environmental regulations, typically have higher melting temperatures than traditional lead-based solders. PCB antipads can help ensure that sufficient heat is available to melt lead-free solder, promoting better compatibility with these materials.
Designing PCB Antipads
When designing PCB antipads, several factors should be considered to ensure optimal performance:
1. Antipad Size
The size of the antipad should be carefully chosen based on the hole size, component lead diameter, and the desired level of thermal relief. A larger antipad provides greater thermal isolation but may reduce the mechanical strength of the connection. Conversely, a smaller antipad may not provide sufficient thermal relief.
Hole Size (mm) | Antipad Size (mm) |
---|---|
0.8 | 1.2 |
1.0 | 1.4 |
1.2 | 1.6 |
1.5 | 1.9 |
2. Number of Thermal Spokes
Thermal spokes are the narrow copper connections that extend from the pad to the surrounding copper area. The number of thermal spokes can vary, typically ranging from 2 to 4. More thermal spokes provide a stronger mechanical connection but may reduce the effectiveness of the thermal relief.
Number of Spokes | Thermal Relief | Mechanical Strength |
---|---|---|
2 | High | Low |
3 | Medium | Medium |
4 | Low | High |
3. Spoke Width
The width of the thermal spokes should be chosen based on the desired balance between thermal relief and mechanical strength. Wider spokes provide a stronger connection but may reduce the effectiveness of the antipad. Narrower spokes offer better thermal isolation but may be more susceptible to mechanical stress.
4. Copper Thickness
The thickness of the copper on the PCB can also influence the design of PCB antipads. Thicker copper layers may require larger antipads or more thermal spokes to achieve the desired level of thermal relief.
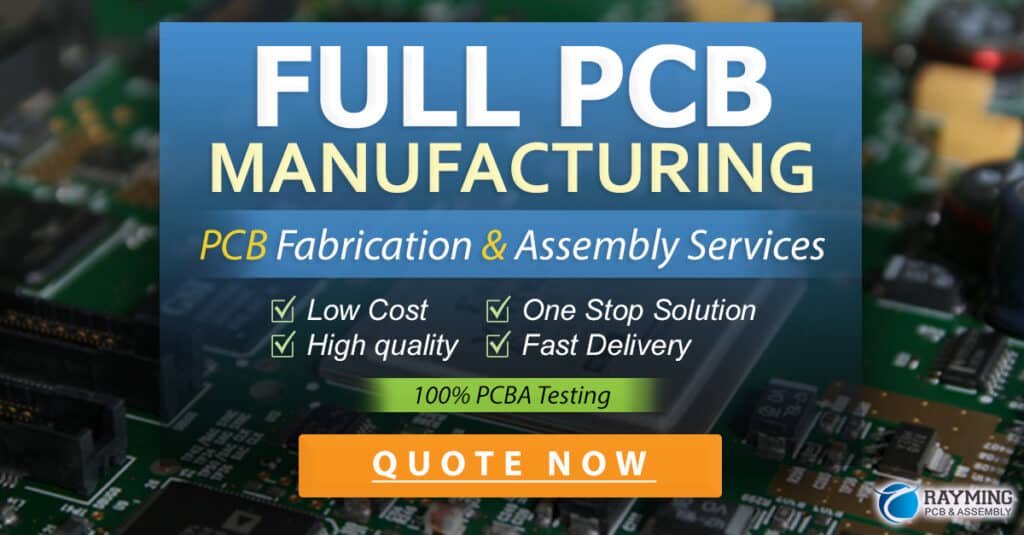
When to Use PCB Antipads
PCB antipads are particularly useful in certain situations:
1. High-Density Designs
In high-density PCB designs with many through-hole components, the use of antipads can significantly improve solderability and reliability. The thermal relief provided by the antipads helps ensure consistent solder joint formation across the board.
2. Power-Hungry Components
Components that generate or dissipate significant amounts of heat, such as power transistors or voltage regulators, can benefit from the use of PCB antipads. The thermal isolation provided by the antipads helps prevent heat from spreading to nearby components and reduces the risk of thermal damage.
3. Lead-Free Soldering
As mentioned earlier, PCB antipads can improve compatibility with lead-free solder alloys. The higher melting temperatures of these materials make thermal relief even more important for achieving reliable solder joints.
Limitations and Alternatives
While PCB antipads offer several benefits, they also have some limitations:
1. Reduced Mechanical Strength
The presence of antipads reduces the amount of copper connected to the hole, which can weaken the mechanical strength of the connection. In applications subject to high mechanical stress or vibration, alternative methods may be necessary to ensure robust connections.
2. Increased PCB Complexity
Incorporating PCB antipads adds complexity to the PCB design process. Designers must carefully consider the size, number, and placement of antipads to achieve the desired thermal relief while maintaining the overall integrity of the board.
3. Alternative Methods
In some cases, other methods may be used to improve solderability and reliability without the need for PCB antipads. These include:
- Increasing the hole size to accommodate more solder
- Using thermal vias to transfer heat away from the solder joint
- Employing selective soldering techniques to apply heat more precisely
Frequently Asked Questions (FAQ)
1. What is the difference between a PCB antipad and a thermal relief?
A PCB antipad and a thermal relief are essentially the same things. Both terms refer to the non-conductive area surrounding a hole or via on a PCB, which reduces the amount of copper connected to the hole to improve solderability.
2. How do I determine the appropriate size for a PCB antipad?
The appropriate size for a PCB antipad depends on several factors, including the hole size, component lead diameter, and the desired level of thermal relief. Generally, larger holes require larger antipads. It’s essential to strike a balance between thermal relief and mechanical strength when choosing the antipad size.
3. Can PCB antipads be used with surface-mount components?
PCB antipads are primarily used with through-hole components, as surface-mount components do not require holes in the PCB. However, similar concepts, such as thermal relief pads, can be applied to surface-mount components to improve solderability and heat dissipation.
4. Do PCB antipads affect the electrical properties of the circuit?
PCB antipads do not directly affect the electrical properties of the circuit, as they are non-conductive areas. However, the presence of antipads can indirectly influence the circuit’s performance by improving the quality and reliability of solder joints.
5. Are there any industry standards for PCB antipad design?
While there are no strict industry standards for PCB antipad design, various guidelines and best practices have been established based on experience and empirical data. Designers should consult with their PCB manufacturers and refer to relevant technical resources to determine the most appropriate antipad design for their specific application.
Conclusion
PCB antipads are a valuable design feature that can significantly improve the solderability and reliability of through-hole components in PCB assemblies. By providing thermal relief around holes and vias, antipads help ensure consistent solder joint formation, enhance product lifespan, and reduce the risk of field failures.
When incorporating PCB antipads into your designs, it’s essential to carefully consider factors such as antipad size, the number of thermal spokes, spoke width, and copper thickness. By striking the right balance between thermal relief and mechanical strength, you can optimize the performance and reliability of your PCB assemblies.
While PCB antipads may not be necessary for every design, they are particularly beneficial in high-density layouts, power-hungry applications, and when using lead-free solder alloys. By understanding the benefits, limitations, and design considerations associated with PCB antipads, you can make informed decisions about whether to incorporate them into your PCB designs.
[Word count: 1309 words]
No responses yet