Introduction to PCA Electronics
PCA (Printed Circuit Assembly) electronics is a crucial aspect of modern electronics manufacturing. It involves the process of assembling various electronic components onto a printed circuit board (PCB) to create a functional electronic device. PCA electronics has revolutionized the electronics industry by enabling the production of compact, reliable, and cost-effective electronic devices.
In this comprehensive guide, we will delve into the world of PCA electronics, exploring its fundamental concepts, manufacturing processes, and best practices for utilizing this technology effectively.
Understanding the Basics of PCA Electronics
What is a Printed Circuit Board (PCB)?
A printed circuit board (PCB) is the foundation of PCA electronics. It is a flat, insulating substrate made of materials such as fiberglass, epoxy, or polyimide. The PCB serves as a platform for mounting and interconnecting electronic components, such as resistors, capacitors, integrated circuits (ICs), and connectors.
PCBs are designed using specialized software called PCB design tools or electronic design automation (EDA) software. These tools allow engineers to create schematic diagrams, layout the components on the board, and generate the necessary files for manufacturing.
Types of PCBs
There are several types of PCBs used in PCA electronics, each with its own characteristics and applications:
-
Single-layer PCBs: These PCBs have conductive tracks on only one side of the substrate. They are the simplest and most cost-effective type of PCB, suitable for basic electronic projects.
-
Double-layer PCBs: Double-layer PCBs have conductive tracks on both sides of the substrate, allowing for more complex circuit designs and higher component density compared to single-layer PCBs.
-
Multi-layer PCBs: Multi-layer PCBs consist of multiple layers of conductive tracks separated by insulating layers. They offer the highest level of complexity and density, enabling the creation of sophisticated electronic devices with compact form factors.
-
Flexible PCBs: Flexible PCBs are made of flexible substrates, such as polyimide, allowing them to bend and conform to various shapes. They are commonly used in applications where flexibility and space constraints are critical, such as wearable devices and medical equipment.
-
Rigid-Flex PCBs: Rigid-Flex PCBs combine the benefits of both rigid and flexible PCBs. They consist of rigid PCB sections connected by flexible PCB sections, providing the best of both worlds in terms of stability and flexibility.
PCB Manufacturing Process
The PCB manufacturing process involves several key steps:
-
Design: The PCB design is created using EDA software, where the schematic diagram is developed, and the components are laid out on the board.
-
Fabrication: The PCB fabrication process begins with the creation of a copper-clad laminate, which is a substrate covered with a thin layer of copper on one or both sides. The copper layer is then etched away, leaving only the desired conductive tracks based on the PCB design.
-
Drilling: Holes are drilled into the PCB to accommodate through-hole components and provide interconnections between layers in multi-layer PCBs.
-
Plating: The drilled holes are plated with a conductive material, typically copper, to ensure proper electrical connectivity between layers.
-
Solder Mask Application: A solder mask, usually green in color, is applied to the PCB surface to protect the conductive tracks from oxidation and prevent short circuits during soldering.
-
Silkscreen Printing: The silkscreen layer is printed on the PCB surface to add text, labels, and component identifiers, making it easier for assembly and troubleshooting.
-
Surface Finish: A surface finish, such as HASL (Hot Air Solder Leveling), ENIG (Electroless Nickel Immersion Gold), or OSP (Organic Solderability Preservative), is applied to the exposed copper areas to prevent oxidation and enhance solderability.
PCA Assembly Techniques
Once the PCB is manufactured, the next step is to assemble the electronic components onto the board. There are two primary techniques used in PCA assembly:
Through-Hole Assembly (THA)
Through-hole assembly involves inserting the leads of components through the drilled holes in the PCB and soldering them to the conductive tracks on the opposite side. This technique is suitable for larger components and provides a strong mechanical connection. However, it is more labor-intensive and requires more space on the PCB compared to surface-mount assembly.
Surface-Mount Assembly (SMA)
Surface-mount assembly involves placing components directly onto the surface of the PCB and soldering them to the conductive pads. Surface-mount components (SMCs) are smaller and have leads or terminations that are designed to be soldered directly to the PCB surface. SMA offers several advantages over THA, including:
- Higher component density: SMCs are smaller than through-hole components, allowing for more components to be placed on a given PCB area.
- Improved electrical performance: SMCs have shorter lead lengths, reducing parasitic inductance and capacitance, resulting in better high-frequency performance.
- Automated assembly: SMA is well-suited for automated assembly processes, such as pick-and-place machines, which can place components quickly and accurately.
PCA Assembly Process
The PCA assembly process typically involves the following steps:
-
Solder Paste Application: Solder paste, a mixture of tiny solder particles and flux, is applied to the PCB pads using a stencil or syringe. The solder paste holds the components in place during the reflow soldering process.
-
Component Placement: Components are placed onto the PCB, either manually or using automated pick-and-place machines. Proper alignment and orientation of components are crucial for a successful assembly.
-
Reflow Soldering: The PCB with the placed components is subjected to a controlled heating process called reflow soldering. The PCB passes through a reflow oven, where the solder paste melts and forms a strong electrical and mechanical bond between the components and the PCB pads.
-
Inspection and Testing: After the reflow soldering process, the assembled PCB undergoes visual inspection and various testing procedures to ensure proper functionality and quality. Common testing methods include automated optical inspection (AOI), in-circuit testing (ICT), and functional testing.
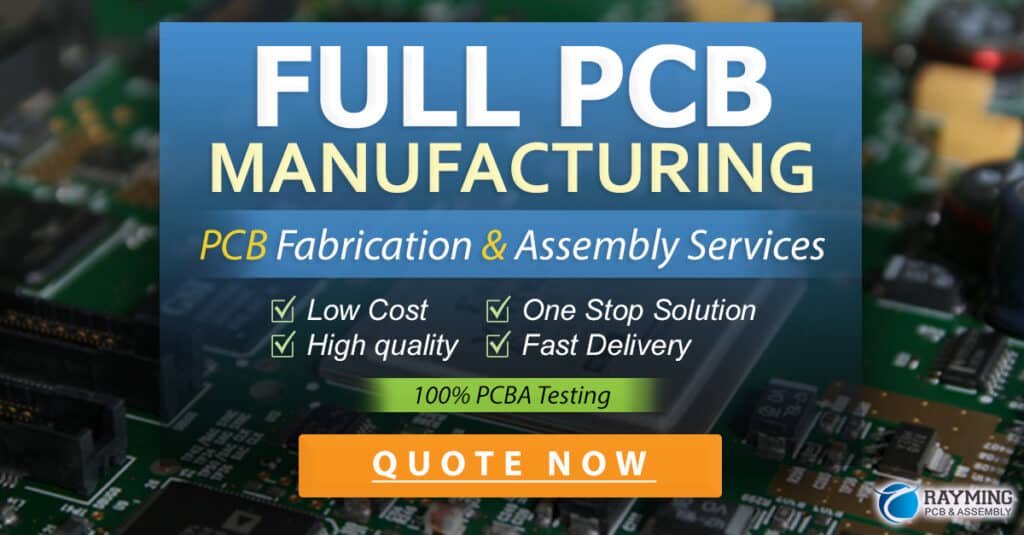
Best Practices for PCA Electronics Design and Assembly
To ensure the success of your PCA electronics projects, consider the following best practices:
Design for Manufacturability (DFM)
When designing PCBs, it is essential to consider the manufacturability aspects to avoid potential issues during fabrication and assembly. Some DFM guidelines include:
- Adhere to the manufacturer’s design rules and guidelines, such as minimum trace widths, clearances, and drill sizes.
- Avoid sharp corners and angles in the PCB layout to prevent stress concentrations and improve reliability.
- Provide adequate spacing between components to facilitate assembly and avoid interference.
- Use standard component sizes and packages whenever possible to simplify sourcing and assembly.
Component Selection and Sourcing
Careful component selection and sourcing are crucial for the success of your PCA electronics project. Consider the following factors:
- Choose components that meet the electrical, mechanical, and environmental requirements of your application.
- Verify the availability and lead times of components to avoid potential supply chain disruptions.
- Consider using components with multiple sources or alternate part numbers to mitigate the risk of obsolescence or shortages.
- Ensure compatibility between components and the chosen assembly techniques (THA or SMA).
Assembly Process Control
Implementing proper process control measures during PCA assembly can help minimize defects and improve overall quality. Some key considerations include:
- Maintain a clean and controlled environment to prevent contamination and electrostatic discharge (ESD) damage.
- Use appropriate tools and equipment, such as ESD-safe workstations, soldering irons, and handling devices.
- Establish and follow standard operating procedures (SOPs) for each assembly step to ensure consistency and repeatability.
- Implement quality control measures, such as visual inspection, automated testing, and statistical process control (SPC), to identify and address potential issues promptly.
Documentation and Version Control
Proper documentation and version control are essential for effective collaboration, troubleshooting, and future reference. Consider the following practices:
- Maintain accurate and up-to-date schematic diagrams, PCB layouts, and bill of materials (BOM) for each project.
- Use a version control system to track changes and revisions to the design files and documents.
- Provide clear and concise assembly instructions, including component placement, orientation, and any special handling requirements.
- Document any modifications, rework, or repairs made during the assembly process for traceability and future reference.
Frequently Asked Questions (FAQ)
1. What is the difference between PCB and PCA?
A printed circuit board (PCB) is the bare board without any components attached to it, while a printed circuit assembly (PCA) refers to the PCB with electronic components assembled onto it. In other words, a PCA is the complete assembly of a PCB and its components.
2. Can PCA electronics be repaired if a component fails?
Yes, PCA electronics can be repaired if a component fails, but the complexity of the repair depends on various factors, such as the type of component, the assembly technique used (THA or SMA), and the accessibility of the component on the board. Rework and repair techniques, such as desoldering and soldering, can be employed to replace faulty components.
3. How can I ensure the reliability of my PCA electronics?
To ensure the reliability of your PCA electronics, consider the following practices:
– Use high-quality components from reputable suppliers
– Follow best practices for PCB design and assembly
– Implement proper process control measures during manufacturing
– Conduct thorough testing and inspection to identify and address potential issues
– Use appropriate packaging and protection measures to prevent damage during storage and transportation
4. What are the advantages of using surface-mount assembly (SMA) over through-hole assembly (THA)?
Surface-mount assembly offers several advantages over through-hole assembly, including:
– Higher component density, allowing for smaller and more compact PCBs
– Improved electrical performance due to shorter lead lengths and reduced parasitic effects
– Faster and more efficient automated assembly processes
– Lower overall manufacturing costs for high-volume production
5. How can I choose the right PCB manufacturer for my PCA electronics project?
When choosing a PCB manufacturer for your PCA electronics project, consider the following factors:
– Technical capabilities and experience in manufacturing PCBs similar to your design
– Quality certifications and standards, such as ISO 9001 and IPC standards
– Turnaround time and pricing
– Customer support and communication
– Reputation and references from previous clients
PCB Type | Layers | Typical Applications |
---|---|---|
Single-layer PCB | 1 | Simple electronic projects, low-cost devices |
Double-layer PCB | 2 | More complex circuits, medium-density designs |
Multi-layer PCB | 4, 6, 8, or more | High-density designs, advanced electronic devices |
Flexible PCB | 1 or more | Wearable devices, medical equipment, space-constrained applications |
Rigid-Flex PCB | Combination of rigid and flexible layers | Applications requiring both stability and flexibility |
Assembly Technique | Characteristics | Advantages | Disadvantages |
---|---|---|---|
Through-Hole Assembly (THA) | Components inserted through holes in PCB | Strong mechanical connection, suitable for larger components | More space required, labor-intensive, slower assembly |
Surface-Mount Assembly (SMA) | Components placed directly on PCB surface | Higher component density, improved electrical performance, automated assembly | Smaller components, more sensitive to thermal stress |
Conclusion
PCA electronics has revolutionized the electronics industry by enabling the production of compact, reliable, and cost-effective electronic devices. By understanding the fundamental concepts, manufacturing processes, and best practices associated with PCA electronics, you can effectively design and manufacture electronic devices that meet your specific requirements.
Remember to consider factors such as PCB design, component selection, assembly techniques, process control, and documentation throughout your PCA electronics projects. By following best practices and working with reputable manufacturers, you can ensure the success and reliability of your electronic devices.
As technology continues to advance, PCA electronics will play an increasingly important role in shaping the future of the electronics industry. By staying informed and adapting to new technologies and techniques, you can remain at the forefront of this exciting field and create innovative electronic solutions that meet the evolving needs of the market.
No responses yet