What is a PCB+Panel”>PCB Panel?
A PCB panel, also known as a multi-panel or an array, is a larger board that contains multiple identical or different PCB Designs. The individual PCBs are arranged in a grid-like pattern, with a small amount of space between each board, called the “rail” or “web.” These rails provide structural support and allow for easy separation of the individual PCBs after the manufacturing and assembly processes are complete.
Advantages of Using PCB Panels
Using PCB panels offers several advantages over manufacturing individual PCBs:
- Cost reduction: By producing multiple PCBs on a single panel, manufacturers can reduce material costs, setup times, and labor costs.
- Increased efficiency: Panels allow for simultaneous processing of multiple boards, reducing overall production time.
- Improved consistency: Manufacturing PCBs in a panel ensures consistent quality across all boards, as they undergo the same processes together.
- Simplified handling: Panels are easier to handle and transport than individual PCBs, reducing the risk of damage during manufacturing and assembly.
Designing PCBs for Panel Manufacturing
When designing PCBs that will be manufactured in a panel, several factors must be considered to ensure optimal results.
Board Orientation and Placement
The orientation and placement of the individual PCBs on the panel play a crucial role in the manufacturing process. Consider the following guidelines:
- Orientation: Ensure that all PCBs on the panel have the same orientation. This simplifies the assembly process and reduces the risk of errors.
- Spacing: Provide adequate spacing between individual PCBs to allow for the rails and tooling holes. The rail width typically ranges from 3mm to 5mm, depending on the panel size and the number of boards.
- Symmetry: If possible, arrange the PCBs symmetrically on the panel. This helps to balance the panel during manufacturing and assembly, reducing the risk of warping or distortion.
Tooling Holes and Fiducial Marks
Tooling holes and fiducial marks are essential features that help to align and secure the panel during the manufacturing and assembly processes.
- Tooling holes: These are small holes drilled in the rails of the panel, used to pin the panel in place during manufacturing. Ensure that the tooling holes are correctly sized and positioned according to the manufacturer’s specifications.
- Fiducial marks: Fiducial marks are small, copper-defined shapes placed on the panel that serve as reference points for automated assembly equipment. Place fiducial marks on the outer corners of the panel and, if necessary, near each individual PCB.
Panelization Methods
There are two primary methods for panelizing PCBs:
- V-Scoring: V-scoring involves milling a V-shaped groove along the rails between the individual PCBs. This method allows for easy separation of the boards after assembly, but it can slightly weaken the structural integrity of the panel.
- Tab Routing: Tab routing uses small, unrouted tabs to connect the individual PCBs to the rails. This method provides better structural support but requires manual separation of the boards after assembly.
Choose the panelization method that best suits your project’s requirements, considering factors such as the PCB size, thickness, and the intended application.
Assembly Considerations for PCB Panels
When assembling PCBs that are delivered in a panel, there are several factors to keep in mind to ensure a smooth and efficient process.
Component Placement
When placing components on panelized PCBs, consider the following:
- Clearance: Ensure that there is sufficient clearance between components and the edges of the individual PCBs to avoid interference with the rails or adjacent boards.
- Orientation: Place components in the same orientation across all PCBs on the panel to simplify the assembly process and reduce the risk of errors.
- Symmetry: If possible, arrange components symmetrically on each PCB to balance the panel and reduce the risk of warping or distortion during reflow.
Solder Paste Application
When applying solder paste to panelized PCBs, consider the following:
- Stencil design: Ensure that the stencil apertures are correctly sized and positioned for each component on the PCBs. If necessary, modify the stencil design to accommodate the panel layout.
- Paste volume: Adjust the solder paste volume to account for the increased surface area of the panel. This may require increasing the stencil thickness or modifying the print parameters.
- Print alignment: Use the fiducial marks on the panel to ensure accurate alignment of the stencil and the panel during the print process.
Reflow Soldering
When reflow soldering panelized PCBs, consider the following:
- Thermal profile: Adjust the reflow profile to account for the increased thermal mass of the panel. This may require longer soak times or higher peak temperatures to ensure proper solder joint formation.
- Support: Use appropriate support fixtures to prevent warping or distortion of the panel during reflow. This is particularly important for larger panels or thinner PCBs.
- Cooling: Allow sufficient time for the panel to cool after reflow to prevent thermal shock and minimize the risk of component damage.
Depaneling
After assembly, the individual PCBs must be separated from the panel. The depaneling process depends on the panelization method used:
- V-Scored panels: V-scored panels can be separated by applying gentle pressure along the V-grooves until the boards snap apart. Use a specialized depaneling tool or a sharp blade to ensure a clean break.
- Tab-routed panels: Tab-routed panels require manual cutting of the tabs using a sharp blade or a specialized depaneling tool. Take care not to damage the components or the PCB edges during the process.
After depaneling, inspect the individual PCBs for any signs of damage or stress, and clean any remaining debris from the edges.
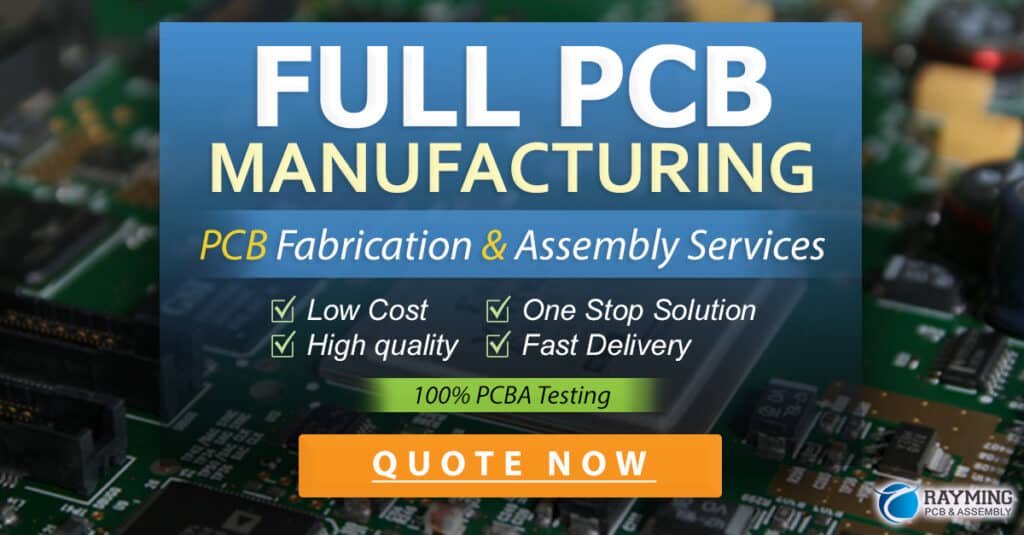
Frequently Asked Questions (FAQ)
-
Q: What is the minimum rail width for a PCB panel?
A: The minimum rail width for a PCB panel typically ranges from 3mm to 5mm, depending on the panel size and the number of boards. Consult with your manufacturer for specific guidelines. -
Q: Can I mix different PCB designs on the same panel?
A: Yes, it is possible to mix different PCB designs on the same panel, provided they have similar specifications (e.g., thickness, material, and copper weight). However, it is generally more efficient to group identical PCBs together. -
Q: How do I determine the optimal panel size for my PCBs?
A: The optimal panel size depends on several factors, including the size and number of PCBs, the manufacturing capabilities of your supplier, and the assembly requirements. Consult with your manufacturer to determine the most suitable panel size for your project. -
Q: Can I use a V-scored panel for high-density PCBs?
A: V-scoring may not be suitable for high-density PCBs, as the grooves can weaken the structural integrity of the board and increase the risk of damage during depaneling. Tab routing is generally preferred for high-density designs. -
Q: What is the purpose of fiducial marks on a PCB panel?
A: Fiducial marks serve as reference points for automated assembly equipment, ensuring accurate alignment and positioning of the panel during the pick-and-place and solder paste printing processes. They help to improve the overall accuracy and consistency of the assembly process.
Conclusion
Delivering PCBs in a panel offers numerous benefits, including cost reduction, increased efficiency, and improved consistency. By following the guidelines outlined in this article, you can ensure that your panelized PCBs are designed, manufactured, and assembled to the highest standards, resulting in a successful and cost-effective project. Remember to consider factors such as board orientation, tooling holes, fiducial marks, and assembly requirements when working with PCB panels, and always consult with your manufacturer for specific guidance and support.
No responses yet