Introduction to Pad Ring Copper Specification
In the world of printed circuit board (PCB) design and manufacturing, pad hole ring copper specification plays a crucial role in ensuring the reliability and functionality of the final product. This comprehensive guide will delve into the intricacies of Pad ring specification, covering various aspects such as design considerations, manufacturing processes, and industry standards.
What is a Pad Hole Ring?
A pad hole ring, also known as an annular ring, is the copper area surrounding a drilled hole on a PCB. The primary purpose of the pad hole ring is to provide a reliable electrical connection between the component lead and the copper trace on the board. The size and shape of the pad hole ring are critical factors in determining the overall performance and durability of the PCB.
Importance of Pad Ring Specification
Proper pad ring specification is essential for several reasons:
-
Electrical Connectivity: A well-designed pad hole ring ensures a robust electrical connection between the component lead and the copper trace, minimizing the risk of open circuits or intermittent connections.
-
Mechanical Strength: The pad hole ring provides mechanical support to the component lead, preventing it from being pulled out or damaged during the assembly process or in use.
-
Manufacturing Feasibility: Adhering to industry-standard pad ring specifications ensures that the PCB can be manufactured consistently and reliably, reducing the likelihood of production issues or defects.
Pad Ring Design Considerations
When designing a PCB, several factors must be considered to determine the appropriate pad ring specification for each component. These factors include:
Hole Size and Tolerance
The hole size is determined by the diameter of the component lead that will be inserted into the hole. It is essential to consider the tolerance of the hole size to ensure a proper fit between the lead and the hole. The tolerance should be specified based on the manufacturing capabilities of the PCB fabricator and the requirements of the component manufacturer.
Component Lead Diameter (mm) | Recommended Hole Size (mm) | Tolerance (mm) |
---|---|---|
0.5 | 0.8 | ±0.1 |
0.8 | 1.1 | ±0.1 |
1.0 | 1.3 | ±0.1 |
1.2 | 1.5 | ±0.1 |
Pad Size and Shape
The size and shape of the pad hole ring are determined by several factors, including the hole size, the thickness of the copper layer, and the spacing between adjacent pads. The pad size should be large enough to provide adequate electrical connectivity and mechanical support, while also allowing for sufficient spacing between adjacent pads to prevent short circuits.
Common pad shapes include circular, rectangular, and oval. The choice of pad shape depends on the specific requirements of the component and the available space on the PCB.
Pad Shape | Advantages | Disadvantages |
---|---|---|
Circular | – Easy to manufacture – Provides uniform electrical contact |
– May require more space than other shapes |
Rectangular | – Allows for closer spacing between pads – Saves space |
– More difficult to manufacture than circular pads |
Oval | – Combines advantages of circular and rectangular pads | – More complex to design and manufacture than other shapes |
Copper Thickness
The thickness of the copper layer on the PCB is another critical factor in determining the appropriate pad ring specification. Thicker copper layers provide better electrical conductivity and mechanical strength, but they also increase the overall cost of the PCB.
Typical copper thicknesses for PCBs range from 0.5 oz/ft² (17 µm) to 4 oz/ft² (140 µm). The choice of copper thickness depends on the specific requirements of the application, such as current-carrying capacity, thermal management, and mechanical durability.
Copper Thickness (oz/ft²) | Thickness (µm) | Typical Applications |
---|---|---|
0.5 | 17 | – Low-power electronics – Small-signal applications |
1.0 | 35 | – General-purpose electronics – Moderate-power applications |
2.0 | 70 | – High-power electronics – Automotive applications |
4.0 | 140 | – Very high-power electronics – Aerospace applications |
Soldermask and Silkscreen
Soldermask and silkscreen are additional layers applied to the PCB that serve important functions in the pad ring specification.
Soldermask is a protective coating applied over the copper layer, leaving only the pad hole rings and other exposed areas uncovered. The soldermask helps to prevent solder bridging between adjacent pads and protects the copper from oxidation and damage.
Silkscreen is a layer of text and symbols printed on the PCB that provides information about component placement, orientation, and identification. The silkscreen should be designed to ensure that the pad hole rings remain clearly visible and accessible for soldering.
Manufacturing Processes
Once the pad ring specification has been determined, the PCB undergoes several manufacturing processes to create the final product.
Drilling
The first step in the manufacturing process is drilling the holes in the PCB. The holes are typically drilled using a computer-controlled drill machine, which ensures precise hole placement and size. The drill bit size is selected based on the specified hole size and tolerance.
Copper Plating
After drilling, the holes are plated with copper to create the pad hole rings. This process involves depositing a thin layer of copper onto the walls of the drilled holes using an electroplating process. The copper plating provides the electrical connection between the component lead and the copper trace on the PCB.
Soldermask and Silkscreen Application
Once the copper plating is complete, the soldermask and silkscreen layers are applied to the PCB. The soldermask is typically applied using a photoimaging process, while the silkscreen is applied using a screen printing process.
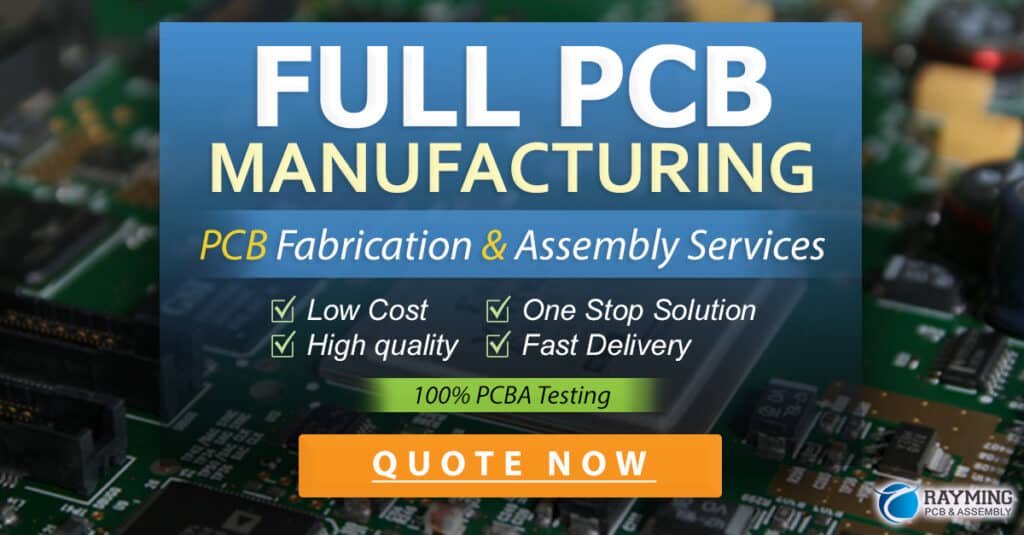
Industry Standards
To ensure consistency and reliability in PCB manufacturing, several industry standards have been established for pad ring specification. These standards provide guidelines for design, manufacturing, and testing of PCBs.
IPC Standards
The Association Connecting Electronics Industries (IPC) is a global trade association that develops standards for the electronic interconnection industry. Some of the key IPC standards related to pad ring specification include:
- IPC-2221: Generic Standard on Printed Board Design
- IPC-6012: Qualification and Performance Specification for Rigid Printed Boards
- IPC-A-600: Acceptability of Printed Boards
These standards provide detailed requirements for pad ring design, manufacturing tolerances, and acceptance criteria.
Military and Aerospace Standards
In addition to the IPC standards, there are also military and aerospace standards that apply to PCBs used in these industries. These standards, such as MIL-PRF-31032 and MIL-PRF-55110, have more stringent requirements for pad ring specification and other aspects of PCB design and manufacturing.
Frequently Asked Questions (FAQ)
-
What is the minimum pad hole ring size required for a given component lead diameter?
The minimum pad hole ring size depends on several factors, including the lead diameter, the copper thickness, and the manufacturing capabilities of the PCB fabricator. As a general rule, the pad hole ring should be at least 0.2 mm larger than the lead diameter to ensure a reliable electrical connection and mechanical support. -
Can I use different pad shapes for different components on the same PCB?
Yes, it is possible to use different pad shapes for different components on the same PCB. However, it is important to ensure that the chosen pad shapes are compatible with the manufacturing process and do not compromise the overall reliability of the PCB. -
How does the copper thickness affect the pad ring specification?
Thicker copper layers provide better electrical conductivity and mechanical strength, which can allow for smaller pad hole ring sizes. However, thicker copper also increases the overall cost of the PCB and may require more advanced manufacturing capabilities. -
What are the consequences of not following industry standards for pad ring specification?
Not following industry standards for pad ring specification can lead to several issues, including poor electrical connectivity, mechanical instability, and manufacturing defects. This can result in reduced reliability, increased costs, and potential product failures. -
How can I ensure that my PCB design meets the required pad ring specifications?
To ensure that your PCB design meets the required pad ring specifications, it is important to work closely with your PCB fabricator and follow the relevant industry standards. Use design tools that incorporate the latest design rules and guidelines, and consider using automated design rule checks (DRCs) to verify that your design meets the required specifications.
Conclusion
Pad hole ring copper specification is a critical aspect of PCB design and manufacturing that directly impacts the reliability, functionality, and cost of the final product. By understanding the key design considerations, manufacturing processes, and industry standards related to pad ring specification, PCB designers and manufacturers can ensure that their products meet the highest quality and performance standards.
As technology continues to advance and new applications emerge, it is essential to stay up-to-date with the latest developments in pad ring specification and related areas of PCB design and manufacturing. By doing so, we can continue to push the boundaries of what is possible with electronic interconnection and create innovative, reliable, and cost-effective solutions for a wide range of industries and applications.
No responses yet