The Importance of PCBs in Modern Electronics
PCBs are the backbone of modern electronics, providing a platform for the assembly and interconnection of electronic components. They are used in a wide range of applications, from consumer electronics and automotive systems to aerospace and medical devices. The PCB industry has experienced significant growth in recent years, driven by the increasing demand for electronic devices and the emergence of new technologies such as 5G, the Internet of Things (IoT), and artificial intelligence (AI).
Year | Global PCB Market Size (USD Billion) |
---|---|
2020 | 62.3 |
2021 | 65.2 |
2022 | 68.3 |
2023 | 71.6 |
2024 | 75.1 |
Source: Statista
The Role of PCBs in Various Industries
PCBs play a crucial role in numerous industries, enabling the development of innovative products and solutions. Some of the key industries that rely heavily on PCBs include:
- Consumer Electronics
- Smartphones
- Laptops
- Wearables
-
Smart Home Devices
-
Automotive
- In-vehicle Infotainment Systems
- Advanced Driver Assistance Systems (ADAS)
-
Electric Vehicle (EV) Powertrain Components
-
Aerospace and Defense
- Avionics Systems
- Radar and Communication Equipment
-
Satellite Components
-
Medical Devices
- Diagnostic Equipment
- Monitoring Systems
- Implantable Devices
Challenges Faced by the PCB Industry
As the demand for more advanced and compact electronic devices continues to grow, the PCB industry faces several significant challenges. These challenges include:
Miniaturization and High-Density Interconnect (HDI) PCBs
One of the primary challenges faced by the PCB industry is the increasing demand for miniaturization and high-density interconnect (HDI) PCBs. As electronic devices become smaller and more complex, PCBs must be designed to accommodate a larger number of components in a smaller space. This requires the use of advanced manufacturing techniques, such as micro-via drilling and fine-pitch component placement, which can be costly and time-consuming.
Solutions for Miniaturization and HDI PCBs
To overcome the challenges associated with miniaturization and HDI PCBs, the industry is adopting several strategies, including:
- Advanced Materials
- Using high-performance substrate materials, such as polyimide and liquid crystal polymer (LCP), which offer better electrical and thermal properties
-
Implementing low-loss dielectric materials to minimize signal integrity issues
-
Improved Manufacturing Processes
- Investing in advanced manufacturing equipment, such as laser drilling machines and high-precision pick-and-place systems
-
Optimizing the PCB design and layout to minimize the number of layers and reduce the overall board size
-
3D Packaging Technologies
- Utilizing 3D packaging technologies, such as package-on-package (PoP) and through-silicon via (TSV), to increase component density and reduce board size
- Integrating passive components, such as capacitors and resistors, into the PCB substrate to save space
High-Speed and High-Frequency PCB Design
Another significant challenge faced by the PCB industry is the increasing demand for high-speed and high-frequency PCBs. As data transmission rates continue to increase, PCBs must be designed to handle higher frequencies and minimize signal integrity issues, such as crosstalk and electromagnetic interference (EMI). This requires the use of advanced PCB design techniques and simulation tools to ensure optimal signal performance.
Solutions for High-Speed and High-Frequency PCB Design
To address the challenges associated with high-speed and high-frequency PCB design, the industry is implementing several strategies, including:
- Advanced PCB Design Tools
- Using advanced PCB design software with built-in simulation and analysis capabilities to optimize signal integrity and minimize EMI
-
Implementing automated design rule checks (DRCs) to ensure compliance with industry standards and manufacturing constraints
-
Controlled Impedance Design
- Designing PCBs with controlled impedance traces to minimize signal reflections and ensure consistent signal propagation
-
Using differential signaling techniques to reduce crosstalk and improve signal integrity
-
High-Performance Materials
- Selecting low-loss dielectric materials, such as Rogers RO4000 series, to minimize signal attenuation and improve high-frequency performance
- Using low-profile copper foils and smooth copper surfaces to reduce Skin Effect losses and improve signal quality
Thermal Management and Power Integrity
As electronic devices become more powerful and compact, thermal management and power integrity become increasingly critical challenges for the PCB industry. PCBs must be designed to efficiently dissipate heat generated by components and ensure stable power delivery to all parts of the board. Failure to address these issues can lead to reduced performance, reliability issues, and even device failure.
Solutions for Thermal Management and Power Integrity
To overcome the challenges associated with thermal management and power integrity, the PCB industry is adopting several strategies, including:
- Advanced Thermal Management Techniques
- Incorporating thermal vias and heat spreaders into the PCB design to improve heat dissipation
-
Using thermally conductive materials, such as metal-core PCBs and thermal interface materials (TIMs), to enhance heat transfer
-
Optimized Power Distribution Networks (PDNs)
- Designing robust power distribution networks with adequate copper thickness and low-impedance power planes to ensure stable power delivery
-
Implementing decoupling capacitors and power integrity simulations to minimize voltage fluctuations and reduce electromagnetic interference (EMI)
-
Embedded Components and 3D Packaging
- Embedding passive components, such as capacitors and resistors, into the PCB substrate to reduce component count and improve power integrity
- Utilizing 3D packaging technologies, such as package-on-package (PoP) and through-silicon via (TSV), to optimize power delivery and reduce interconnect lengths
Environmental Sustainability and Regulatory Compliance
As environmental concerns continue to grow, the PCB industry faces increasing pressure to adopt sustainable manufacturing practices and comply with stringent regulations. This includes the use of environmentally friendly materials, the reduction of hazardous substances, and the implementation of effective waste management strategies. Additionally, the industry must stay abreast of evolving regulations, such as the Restriction of Hazardous Substances (RoHS) and the Registration, Evaluation, Authorization, and Restriction of Chemicals (REACH), to ensure compliance and avoid potential legal and financial consequences.
Solutions for Environmental Sustainability and Regulatory Compliance
To address the challenges associated with environmental sustainability and regulatory compliance, the PCB industry is implementing several strategies, including:
- Eco-Friendly Materials and Processes
- Adopting halogen-free and lead-free materials to reduce the use of hazardous substances
-
Implementing green manufacturing processes, such as water-based cleaning and low-VOC (volatile organic compound) coatings, to minimize environmental impact
-
Waste Reduction and Recycling
- Optimizing PCB design and manufacturing processes to minimize material waste and improve resource efficiency
-
Implementing effective waste management and recycling programs to reduce the environmental footprint of PCB manufacturing
-
Regulatory Compliance and Monitoring
- Staying informed about the latest environmental regulations and industry standards to ensure compliance
- Implementing robust quality control and testing procedures to verify the absence of restricted substances and ensure product safety
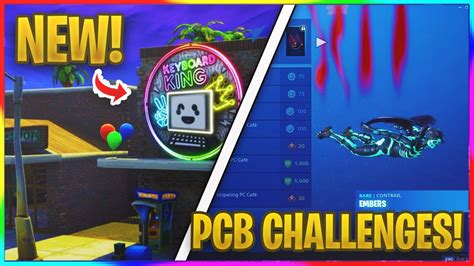
FAQ
-
What are the main technological challenges faced by the PCB industry?
The main technological challenges faced by the PCB industry include miniaturization and high-density interconnect (HDI) PCBs, high-speed and high-frequency PCB design, thermal management and power integrity, and environmental sustainability and regulatory compliance. -
How is the PCB industry addressing the challenge of miniaturization and HDI PCBs?
The PCB industry is addressing the challenge of miniaturization and HDI PCBs by using advanced materials, improving manufacturing processes, and implementing 3D packaging technologies. -
What strategies are being used to overcome the challenges associated with high-speed and high-frequency PCB design?
Strategies used to overcome the challenges associated with high-speed and high-frequency PCB design include using advanced PCB design tools, implementing controlled impedance design, and selecting high-performance materials. -
How is the PCB industry addressing the issues of thermal management and power integrity?
The PCB industry is addressing the issues of thermal management and power integrity by incorporating advanced thermal management techniques, optimizing power distribution networks (PDNs), and utilizing embedded components and 3D packaging technologies. -
What steps is the PCB industry taking to ensure environmental sustainability and regulatory compliance?
The PCB industry is taking steps to ensure environmental sustainability and regulatory compliance by adopting eco-friendly materials and processes, implementing waste reduction and recycling programs, and staying informed about the latest environmental regulations and industry standards.
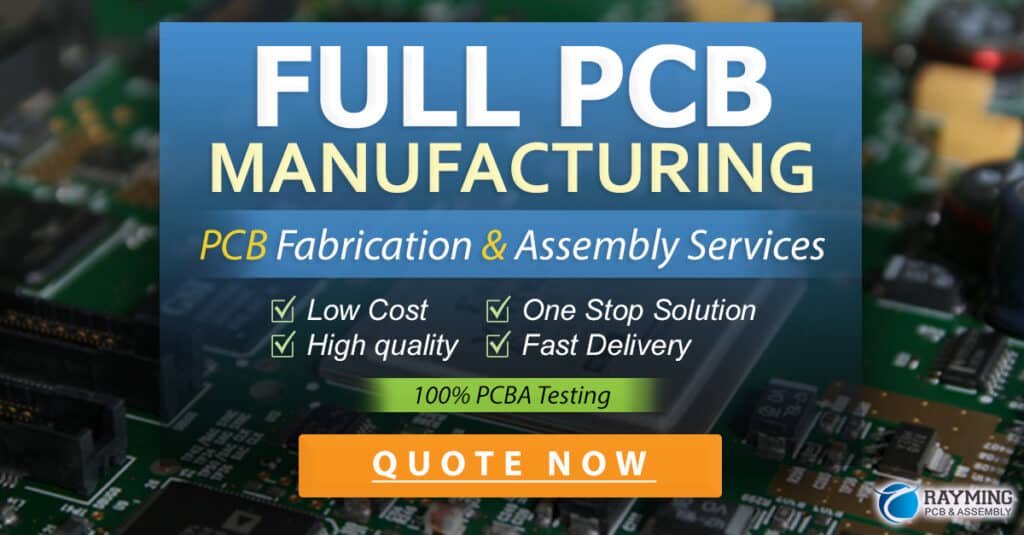
Conclusion
The PCB industry faces numerous technological challenges as it strives to meet the ever-increasing demands for smaller, faster, and more reliable PCBs. These challenges include miniaturization and high-density interconnect (HDI) PCBs, high-speed and high-frequency PCB design, thermal management and power integrity, and environmental sustainability and regulatory compliance.
To overcome these challenges, the industry is adopting a range of strategies, such as using advanced materials and manufacturing processes, implementing 3D packaging technologies, utilizing advanced PCB design tools and techniques, and incorporating eco-friendly materials and practices.
By addressing these challenges head-on and investing in innovative solutions, the PCB industry can continue to drive the development of cutting-edge electronic devices and systems, while also ensuring environmental sustainability and regulatory compliance. As technology continues to advance, the PCB industry will undoubtedly face new challenges, but with a commitment to innovation and collaboration, it is well-positioned to overcome these obstacles and shape the future of electronics.
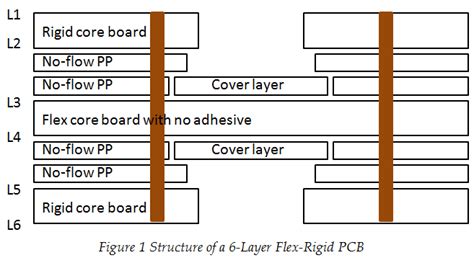
No responses yet