Introduction to PCB Finishes
Printed Circuit Boards (PCBs) are the backbone of modern electronics. They provide a platform for interconnecting electronic components and ensuring reliable performance. However, the choice of PCB finish can greatly impact the manufacturability, solderability, and long-term reliability of the board. Two popular PCB finishes are Organic Solderability Preservative (OSP) and Electroless Nickel Immersion Gold (ENIG). In this article, we will dive into the details of OSP and ENIG, exploring their characteristics, advantages, and differences.
What is OSP?
Definition and Composition
Organic Solderability Preservative (OSP) is a chemical coating applied to the exposed copper surfaces of a PCB. It is a thin, transparent layer that protects the copper from oxidation and contamination, ensuring excellent solderability. The OSP coating is typically composed of benzimidazole or benzotriazole compounds, which form a stable, organometallic complex with the copper surface.
Application Process
The OSP application process involves the following steps:
- Cleaning: The PCB is thoroughly cleaned to remove any contaminants or oxides from the copper surface.
- Microetching: A mild etching solution is used to remove a thin layer of copper, creating a uniform and active surface for OSP adhesion.
- OSP Application: The PCB is immersed in the OSP solution, allowing the organic compounds to form a protective layer on the copper surface.
- Drying: The PCB is dried using hot air or infrared heating to remove any excess moisture and ensure a uniform coating.
Advantages of OSP
OSP offers several advantages as a PCB finish:
- Cost-effectiveness: OSP is one of the most economical PCB finishes available, making it suitable for high-volume production and cost-sensitive applications.
- Flatness: The thin OSP coating does not significantly affect the flatness of the PCB, which is crucial for fine-pitch components and surface mount technology (SMT).
- Quick processing: The OSP application process is relatively fast, allowing for shorter lead times and faster production cycles.
- Excellent solderability: OSP provides excellent solderability, ensuring reliable solder joint formation during the assembly process.
Limitations of OSP
Despite its advantages, OSP has some limitations:
- Limited shelf life: The OSP coating has a limited shelf life, typically around 6-12 months, after which the solderability may degrade.
- Sensitivity to handling: The OSP coating is sensitive to handling and can be easily contaminated or damaged, requiring careful storage and transportation.
- Incompatibility with certain processes: OSP may not be suitable for certain assembly processes, such as wire bonding or press-fit connectors, due to its organic nature.
What is ENIG?
Definition and Composition
Electroless Nickel Immersion Gold (ENIG) is a popular PCB finish that consists of a thin layer of gold over a nickel underlayer. The nickel layer provides a barrier between the copper and gold, preventing diffusion and ensuring long-term reliability. The gold layer, on the other hand, offers excellent solderability and protection against oxidation.
Application Process
The ENIG application process involves the following steps:
- Cleaning: The PCB is cleaned to remove any contaminants or oxides from the copper surface.
- Microetching: A mild etching solution is used to remove a thin layer of copper, creating a uniform and active surface for nickel deposition.
- Electroless Nickel Plating: The PCB is immersed in an electroless nickel plating bath, where a thin layer of nickel is deposited on the copper surface through an autocatalytic chemical reaction.
- Immersion Gold Plating: The nickel-plated PCB is then immersed in an immersion gold plating bath, where a thin layer of gold is deposited on top of the nickel through a displacement reaction.
- Rinsing and Drying: The PCB is rinsed with deionized water and dried using hot air or infrared heating.
Advantages of ENIG
ENIG offers several advantages as a PCB finish:
- Excellent solderability: The gold layer provides excellent solderability, ensuring reliable solder joint formation during the assembly process.
- Long shelf life: ENIG has a long shelf life, typically exceeding 12 months, without significant degradation in solderability.
- Compatibility with various processes: ENIG is compatible with a wide range of assembly processes, including wire bonding, press-fit connectors, and surface mount technology (SMT).
- Corrosion resistance: The nickel layer acts as a barrier, preventing the diffusion of copper into the gold layer and providing excellent corrosion resistance.
Limitations of ENIG
ENIG also has some limitations:
- Higher cost: ENIG is more expensive compared to OSP due to the use of gold and the additional processing steps involved.
- Black pad phenomenon: In some cases, ENIG can be susceptible to the “black pad” phenomenon, where the nickel layer becomes brittle and separates from the copper surface, leading to solderability issues.
- Thickness control: Controlling the thickness of the nickel and gold layers in ENIG can be challenging, requiring strict process control and monitoring.
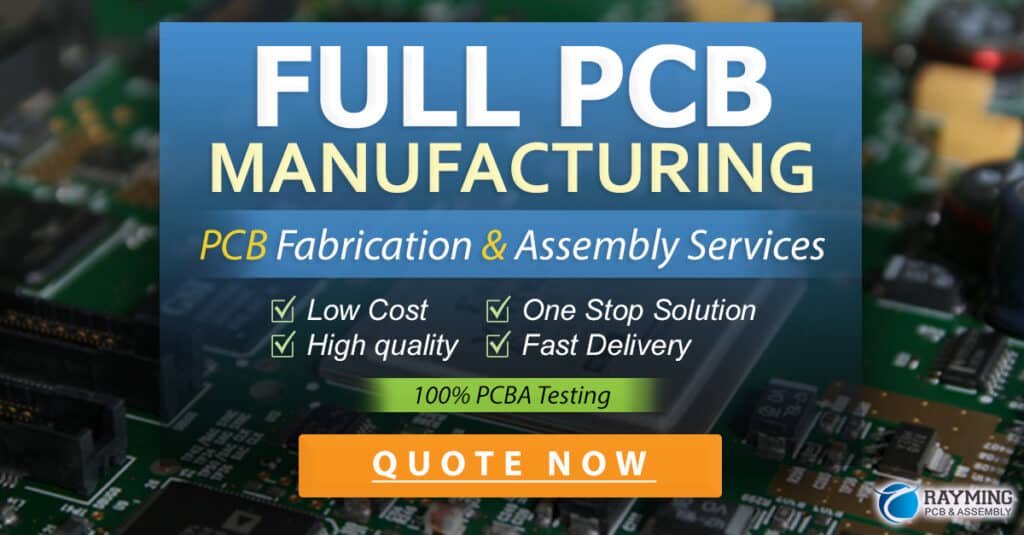
OSP vs ENIG: A Comparison
Now that we have explored the characteristics of OSP and ENIG, let’s compare them side by side:
Characteristic | OSP | ENIG |
---|---|---|
Composition | Organic compounds (benzimidazole or benzotriazole) | Nickel underlayer with gold coating |
Application | Immersion in OSP solution | Electroless nickel plating followed by immersion gold plating |
Shelf Life | Limited (6-12 months) | Long (>12 months) |
Solderability | Excellent | Excellent |
Flatness | Excellent (thin coating) | Good |
Cost | Low | High |
Process Compatibility | Limited (not suitable for wire bonding or press-fit) | Wide range (compatible with wire bonding, press-fit, SMT) |
Corrosion Resistance | Good | Excellent |
Thickness Control | Not applicable | Challenging |
Potential Issues | Contamination, degradation over time | Black pad phenomenon |
Choosing Between OSP and ENIG
When deciding between OSP and ENIG for your PCB finish, consider the following factors:
- Application requirements: Evaluate the specific requirements of your application, such as the need for wire bonding, press-fit connectors, or long shelf life.
- Budget: Consider the cost implications of each finish. OSP is generally more cost-effective, while ENIG is more expensive.
- Production volume: For high-volume production, OSP may be more suitable due to its lower cost and faster processing time.
- Reliability: If long-term reliability is a critical factor, ENIG may be the better choice due to its excellent corrosion resistance and longer shelf life.
- Assembly process: Consider the compatibility of the finish with your assembly process. ENIG is more versatile and compatible with a wider range of processes compared to OSP.
Frequently Asked Questions (FAQ)
-
What is the typical shelf life of OSP?
The typical shelf life of OSP is around 6-12 months, after which the solderability may degrade. -
Is ENIG suitable for wire bonding?
Yes, ENIG is suitable for wire bonding due to its compatibility with a wide range of assembly processes. -
Can OSP be used for press-fit connectors?
No, OSP is not recommended for press-fit connectors due to its organic nature and potential for contamination. -
What is the “black pad” phenomenon in ENIG?
The “black pad” phenomenon in ENIG refers to the brittle nickel layer that separates from the copper surface, leading to solderability issues. -
Is OSP more cost-effective than ENIG?
Yes, OSP is generally more cost-effective compared to ENIG due to its simpler application process and lower material costs.
Conclusion
Choosing the right PCB finish is crucial for ensuring the manufacturability, solderability, and reliability of your electronic products. OSP and ENIG are two popular finishes, each with its own advantages and limitations. OSP offers cost-effectiveness, excellent flatness, and quick processing, making it suitable for high-volume production and cost-sensitive applications. ENIG, on the other hand, provides excellent solderability, long shelf life, and compatibility with various assembly processes, making it ideal for applications requiring long-term reliability and versatility.
When selecting between OSP and ENIG, consider factors such as application requirements, budget, production volume, reliability, and assembly process compatibility. By understanding the characteristics and differences between these two finishes, you can make an informed decision that aligns with your specific needs and ensures the success of your PCB Assembly.
Remember, the choice of PCB finish is just one aspect of the overall PCB design and manufacturing process. It is essential to work closely with your PCB manufacturer and assembly partner to ensure that all aspects of your design are optimized for manufacturability, reliability, and cost-effectiveness.
No responses yet