Introduction
The metal manufacturing industry is undergoing a significant transformation with the advent of Industry 4.0 technologies. One key aspect of this transformation is the adoption of Industrial Internet of Things (IIoT) solutions for digitalization and traceability. IIoT enables the collection, analysis, and sharing of data across the entire manufacturing process, from raw material procurement to finished product delivery. This case study explores how a leading metal manufacturing company implemented next-generation IIoT solutions to improve traceability, efficiency, and quality control.
The Challenge of Traceability in Metal Manufacturing
Metal manufacturing involves complex processes and supply chains, making traceability a significant challenge. Some key issues include:
- Tracking raw materials from multiple suppliers
- Monitoring production processes across different stages and locations
- Ensuring quality control and compliance with regulations
- Managing inventory and logistics for finished products
Without proper traceability, manufacturers face risks such as:
- Quality issues and product recalls
- Difficulty identifying the root cause of problems
- Inability to optimize processes and reduce waste
- Compliance violations and legal liabilities
The Promise of Industrial IoT Digitalization
Industrial IoT digitalization offers a solution to these challenges by enabling real-time data collection, analysis, and sharing across the entire manufacturing process. Some key benefits include:
- Improved visibility and control over the supply chain
- Real-time monitoring of production processes
- Predictive maintenance and quality control
- Optimized inventory management and logistics
To realize these benefits, manufacturers need to implement IIoT solutions that can:
- Connect and integrate data from various sources (sensors, machines, systems)
- Analyze data using advanced analytics and machine learning
- Provide real-time insights and actionable intelligence
- Enable collaboration and data sharing across the organization and with partners
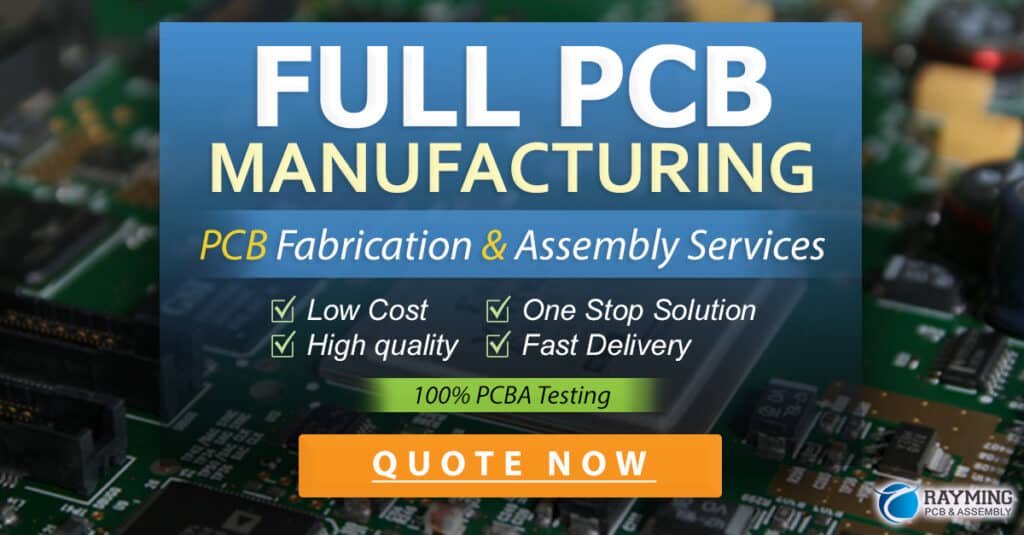
Case Study: Implementing Next-Gen IIoT at MetalCo
MetalCo is a leading global manufacturer of metal products for various industries, including automotive, aerospace, and construction. The company operates multiple production facilities across different countries and works with a complex network of suppliers and customers.
The Need for IIoT Digitalization
MetalCo recognized the need to improve traceability and efficiency in its manufacturing operations. Some key drivers included:
- Increasing customer demands for quality and compliance
- Pressure to reduce costs and optimize processes
- Need for better visibility and control over the supply chain
- Desire to leverage data for continuous improvement and innovation
The IIoT Implementation Journey
MetalCo embarked on a multi-year journey to implement next-generation IIoT solutions across its operations. The key steps included:
- Defining the vision and strategy
- Aligning IIoT initiatives with business goals
- Identifying key use cases and priorities
-
Developing a roadmap and implementation plan
-
Building the IIoT infrastructure
- Deploying sensors and connectivity across production lines
- Integrating data from various sources (machines, systems, suppliers)
-
Implementing a scalable and secure IIoT platform for data management and analysis
-
Developing analytics and insights
- Building machine learning models for predictive maintenance and quality control
- Creating real-time dashboards and alerts for monitoring and decision-making
-
Enabling self-service analytics for different roles and functions
-
Driving adoption and change management
- Educating and training employees on IIoT solutions
- Fostering a data-driven culture and mindset
- Collaborating with partners and customers to share data and insights
IIoT Architecture and Technologies
MetalCo implemented a scalable and flexible IIoT architecture based on industry standards and best practices. The key components included:
- Edge computing devices for data collection and processing
- Industrial protocols (OPC UA, MQTT) for machine connectivity
- Cloud-based IIoT platform for data storage, analysis, and sharing
- Big data technologies (Hadoop, Spark) for large-scale data processing
- Machine learning tools (TensorFlow, PyTorch) for predictive analytics
- Visualization and BI tools (PowerBI, Tableau) for reporting and dashboards
Component | Technologies |
---|---|
Edge Devices | IoT Gateways, Industrial PCs |
Connectivity | OPC UA, MQTT, Modbus, Profinet |
Cloud Platform | Microsoft Azure IoT, AWS IoT |
Big Data | Hadoop, Spark, Cassandra |
Machine Learning | TensorFlow, PyTorch, Scikit-learn |
Visualization | PowerBI, Tableau, Grafana |
Results and Benefits
The implementation of IIoT solutions has yielded significant benefits for MetalCo, including:
- 20% reduction in unplanned downtime through predictive maintenance
- 15% improvement in overall equipment effectiveness (OEE)
- 10% reduction in scrap and rework through real-time quality control
- 25% reduction in inventory costs through optimized supply chain management
- 30% faster time-to-market for new products through streamlined processes
Metric | Before IIoT | After IIoT | Improvement |
---|---|---|---|
Unplanned Downtime | 10% | 8% | 20% |
OEE | 70% | 80.5% | 15% |
Scrap/Rework | 5% | 4.5% | 10% |
Inventory Costs | $10M | $7.5M | 25% |
Time-to-Market | 12 months | 8 months | 30% |
Beyond these quantitative benefits, MetalCo has also achieved qualitative improvements such as:
- Enhanced traceability and compliance with regulations
- Improved collaboration and data sharing across the organization
- Faster problem identification and resolution through root cause analysis
- Better decision-making through data-driven insights and intelligence
Key Lessons and Best Practices
Based on MetalCo’s experience, some key lessons and best practices for successful IIoT implementation include:
- Start with a clear vision and strategy aligned with business goals
- Focus on high-impact use cases that deliver tangible value
- Build a scalable and flexible IIoT architecture based on standards
- Invest in data quality, security, and governance
- Foster a data-driven culture and mindset across the organization
- Collaborate with partners and customers to share data and insights
- Continuously measure and optimize performance based on KPIs
Future Outlook and Opportunities
Looking ahead, MetalCo sees several opportunities to further leverage IIoT and Industry 4.0 technologies, such as:
- Expanding IIoT solutions to other areas (e.g. energy management, worker safety)
- Implementing advanced analytics and AI for autonomous decision-making
- Exploring new business models and services based on data (e.g. predictive maintenance as a service)
- Collaborating with ecosystem partners to create new value propositions
- Driving digital transformation across the entire value chain
As the metal manufacturing industry continues to evolve, companies like MetalCo that embrace IIoT and digitalization will be well-positioned to compete and thrive in the future.
Frequently Asked Questions (FAQ)
- What is Industrial IoT (IIoT) digitalization?
-
IIoT digitalization refers to the use of IoT technologies to collect, analyze, and share data across industrial processes and supply chains. It enables real-time monitoring, predictive maintenance, quality control, and optimization of manufacturing operations.
-
Why is traceability important in metal manufacturing?
-
Traceability is critical in metal manufacturing to ensure quality, compliance, and efficiency. It allows manufacturers to track raw materials, monitor production processes, identify issues, and manage finished products across the supply chain. Lack of traceability can lead to quality problems, recalls, and legal liabilities.
-
What are the key components of an IIoT architecture?
-
The key components of an IIoT architecture include edge devices for data collection, industrial protocols for machine connectivity, cloud platforms for data storage and analysis, big data technologies for large-scale processing, machine learning tools for predictive analytics, and visualization tools for reporting and dashboards.
-
How can IIoT benefit metal manufacturers?
-
IIoT can benefit metal manufacturers in several ways, such as reducing unplanned downtime through predictive maintenance, improving overall equipment effectiveness (OEE), reducing scrap and rework through real-time quality control, optimizing inventory and supply chain management, and accelerating time-to-market for new products.
-
What are some best practices for successful IIoT implementation?
- Some best practices for successful IIoT implementation include starting with a clear vision and strategy, focusing on high-impact use cases, building a scalable and flexible architecture, investing in data quality and security, fostering a data-driven culture, collaborating with partners and customers, and continuously measuring and optimizing performance based on KPIs.
Conclusion
The case study of MetalCo demonstrates the transformative potential of Industrial IoT digitalization for traceability and efficiency in the metal manufacturing industry. By implementing next-generation IIoT solutions, MetalCo was able to achieve significant improvements in key metrics such as unplanned downtime, OEE, scrap/rework, inventory costs, and time-to-market. The company’s experience also highlights key lessons and best practices for successful IIoT implementation, such as starting with a clear strategy, focusing on high-impact use cases, building a scalable architecture, fostering a data-driven culture, and collaborating with partners and customers.
As the metal manufacturing industry continues to evolve in the era of Industry 4.0, IIoT digitalization will become increasingly critical for companies to stay competitive and meet the growing demands for quality, compliance, and efficiency. By embracing IIoT and other advanced technologies, manufacturers can not only improve their existing operations but also explore new business models and value propositions based on data and insights.
Looking ahead, the future of metal manufacturing will be shaped by the continued adoption and evolution of IIoT and related technologies such as artificial intelligence, 5G, and edge computing. Companies that can successfully navigate this digital transformation journey will be well-positioned to thrive in the Industry 4.0 era and beyond.
No responses yet