Introduction to PCB Architectures
Printed Circuit Board (PCB) architecture refers to the layout and design of the various layers, components, and interconnections that make up a PCB. As technology advances and electronic devices become more compact and sophisticated, the demand for high-density PCB construction increases. This article explores new PCB architectures that enable the creation of high-density PCBs, their advantages, challenges, and future trends.
What is High Density PCB Construction?
High-density PCB construction involves the design and fabrication of PCBs with a higher number of components and interconnections per unit area compared to traditional PCBs. This is achieved by utilizing smaller component sizes, finer trace widths, and reduced spacing between components and traces. High-density PCBs allow for more functionality to be packed into a smaller space, which is crucial for modern electronic devices such as smartphones, wearables, and IoT devices.
Multilayer PCB Architecture
Overview of Multilayer PCBs
Multilayer PCBs consist of multiple layers of conductive material, typically copper, separated by insulating layers. This architecture allows for a higher density of interconnections and components compared to single or double-layer PCBs. By utilizing the vertical space, multilayer PCBs can accommodate more complex circuits and reduce the overall PCB size.
Advantages of Multilayer PCBs
- Increased circuit density: Multilayer PCBs allow for a higher number of components and interconnections per unit area, enabling more functionality in a smaller space.
- Improved signal integrity: By carefully designing the layer stack-up and utilizing proper grounding and shielding techniques, multilayer PCBs can minimize crosstalk and electromagnetic interference (EMI), resulting in better signal integrity.
- Enhanced thermal management: The multiple layers in a multilayer PCB can be used to create dedicated power and ground planes, which help distribute heat more evenly across the board, improving thermal management.
Challenges in Multilayer PCB Design
- Complexity: Designing multilayer PCBs requires careful consideration of layer stack-up, via placement, and signal routing to ensure proper functionality and minimize signal integrity issues.
- Manufacturing cost: The increased complexity and number of layers in multilayer PCBs can result in higher manufacturing costs compared to simpler PCB designs.
- Reliability concerns: With a higher number of layers and interconnections, there is an increased risk of manufacturing defects and reliability issues, requiring stringent quality control measures.
HDI (High Density Interconnect) PCB Architecture
What is HDI PCB?
HDI (High Density Interconnect) PCBs are a type of PCB architecture that utilizes advanced design and manufacturing techniques to achieve even higher component and interconnection densities compared to traditional multilayer PCBs. HDI PCBs typically feature smaller via sizes, finer trace widths, and reduced spacing between components and traces.
Microvias and Buried Vias
One of the key features of HDI PCBs is the use of microvias and buried vias. Microvias are small-diameter vias that connect adjacent layers in the PCB, while buried vias are used to connect inner layers without penetrating the top or bottom layers. These types of vias allow for more efficient use of board space and enable higher interconnection densities.
Sequential Lamination Process
HDI PCBs are often manufactured using a sequential lamination process, where the PCB is built up layer by layer. This process allows for the creation of complex multilayer structures with a high number of interconnections between layers. Sequential lamination enables the use of microvias and buried vias, which are essential for achieving high-density interconnects.
Benefits of HDI PCB Architecture
- Ultra-high density: HDI PCBs can accommodate a significantly higher number of components and interconnections per unit area compared to traditional multilayer PCBs.
- Improved signal integrity: The smaller via sizes and reduced trace lengths in HDI PCBs result in lower signal distortion and crosstalk, leading to better signal integrity.
- Miniaturization: HDI PCBs enable the creation of smaller, more compact electronic devices without sacrificing functionality.
Challenges in HDI PCB Design and Manufacturing
- Design complexity: Designing HDI PCBs requires specialized knowledge and tools to ensure proper signal routing, impedance control, and manufacturing feasibility.
- Manufacturing challenges: The advanced manufacturing techniques used in HDI PCBs, such as laser drilling and sequential lamination, require specialized equipment and expertise, which can increase production costs.
- Testing and inspection: The high density of components and interconnections in HDI PCBs makes testing and inspection more challenging, requiring advanced testing methods and equipment.
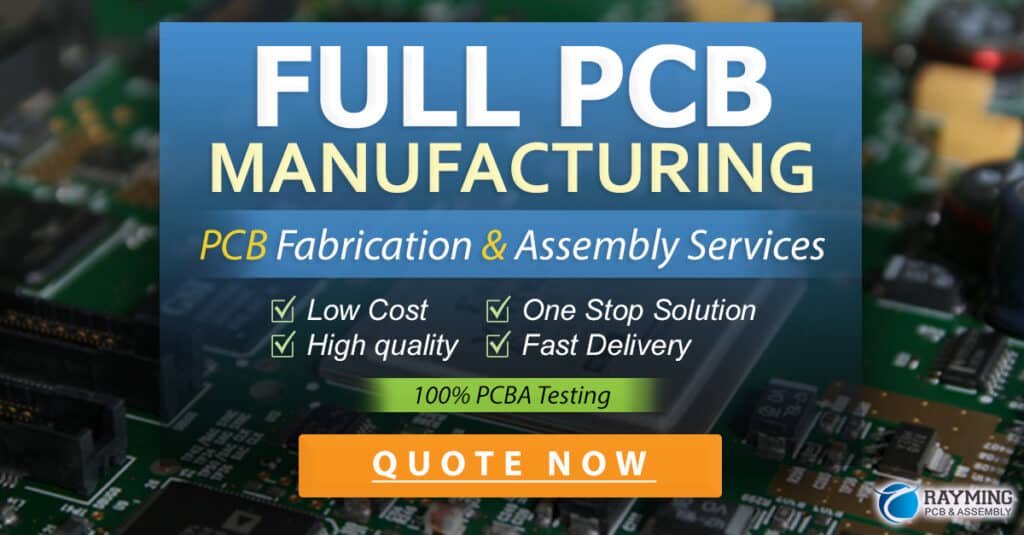
Rigid-Flex PCB Architecture
Overview of Rigid-Flex PCBs
Rigid-flex PCBs combine the benefits of both rigid and flexible PCBs into a single, integrated structure. This architecture consists of rigid PCB sections connected by flexible PCB sections, allowing for three-dimensional packaging and improved mechanical reliability.
Advantages of Rigid-Flex PCBs
- Space savings: Rigid-flex PCBs enable more compact packaging by allowing the PCB to be folded or bent to fit into tight spaces.
- Reduced assembly complexity: By integrating flexible interconnects into the PCB, rigid-flex PCBs eliminate the need for separate cables and connectors, simplifying the assembly process.
- Improved reliability: The flexible sections in rigid-flex PCBs provide stress relief and absorb mechanical shocks, enhancing the overall reliability of the electronic device.
Applications of Rigid-Flex PCBs
Rigid-flex PCBs are widely used in applications where space is limited, and reliability is critical, such as:
- Wearable electronics
- Medical devices
- Aerospace and defense systems
- Automotive electronics
Challenges in Rigid-Flex PCB Design and Manufacturing
- Material selection: Choosing the appropriate materials for the rigid and flexible sections of the PCB is crucial for ensuring the desired mechanical and electrical properties.
- Design complexity: Designing rigid-flex PCBs requires careful consideration of the placement of components, the routing of traces, and the positioning of the flexible sections to ensure proper functionality and reliability.
- Manufacturing challenges: Fabricating rigid-flex PCBs involves specialized processes, such as selective lamination and controlled depth milling, which require advanced equipment and expertise.
Embedded Component PCB Architecture
Overview of Embedded Component PCBs
Embedded component PCBs are a type of PCB architecture where components are embedded within the layers of the PCB, rather than being mounted on the surface. This approach allows for higher component density, improved electrical performance, and better protection of components from environmental factors.
Types of Embedded Components
Various types of components can be embedded in PCBs, including:
- Passive components: Resistors, capacitors, and inductors
- Active components: Integrated circuits (ICs) and semiconductors
- Optical components: Fiber optic cables and waveguides
Benefits of Embedded Component PCBs
- Increased density: Embedding components within the PCB layers frees up surface space, allowing for higher component density and smaller board sizes.
- Improved electrical performance: Embedding components reduces the distance between components and interconnects, minimizing signal distortion and improving overall electrical performance.
- Enhanced reliability: Embedded components are protected from external factors such as mechanical stress, moisture, and temperature fluctuations, leading to improved reliability.
Challenges in Embedded Component PCB Design and Manufacturing
- Design complexity: Designing embedded component PCBs requires careful consideration of component placement, layer stack-up, and thermal management to ensure proper functionality and reliability.
- Manufacturing challenges: Embedding components within the PCB layers requires specialized manufacturing processes, such as cavity formation and component placement, which can increase production costs and lead times.
- Repair and rework: Repairing or replacing embedded components can be difficult or impossible, requiring the replacement of the entire PCB in case of component failure.
Future Trends in PCB Architectures
3D PCB Architecture
3D PCB architecture involves the vertical stacking of multiple PCB layers to create a three-dimensional structure. This approach enables even higher component density and more compact packaging compared to traditional 2D PCBs. 3D PCBs can be created using various techniques, such as through-silicon vias (TSVs) or stacked die packaging.
Organic and Printed Electronics
Organic and printed electronics involve the use of conductive inks and organic materials to create PCBs and electronic components. This emerging technology offers the potential for low-cost, flexible, and environmentally friendly PCB manufacturing. Organic and printed electronics can be used in applications such as wearable devices, smart packaging, and disposable sensors.
Artificial Intelligence in PCB Design
Artificial intelligence (AI) and machine learning (ML) techniques are being increasingly applied to PCB design to optimize layout, component placement, and signal routing. AI-driven PCB design tools can analyze vast amounts of design data, identify potential issues, and suggest improvements, leading to faster design cycles and more reliable PCBs.
Frequently Asked Questions (FAQ)
- What is the difference between a multilayer PCB and an HDI PCB?
-
Multilayer PCBs consist of multiple layers of conductive material separated by insulating layers, allowing for higher density and more complex circuits compared to single or double-layer PCBs. HDI (High Density Interconnect) PCBs are a type of multilayer PCB that utilizes advanced design and manufacturing techniques, such as microvias and sequential lamination, to achieve even higher component and interconnection densities.
-
What are the benefits of using rigid-flex PCBs?
-
Rigid-flex PCBs offer several benefits, including space savings, reduced assembly complexity, and improved reliability. By combining rigid and flexible sections in a single PCB, rigid-flex PCBs enable more compact packaging, eliminate the need for separate cables and connectors, and provide stress relief and shock absorption.
-
What types of components can be embedded in PCBs?
-
Various types of components can be embedded in PCBs, including passive components (resistors, capacitors, inductors), active components (integrated circuits and semiconductors), and optical components (fiber optic cables and waveguides).
-
What challenges are associated with embedded component PCB design and manufacturing?
-
Designing embedded component PCBs requires careful consideration of component placement, layer stack-up, and thermal management. Manufacturing embedded component PCBs involves specialized processes, such as cavity formation and component placement, which can increase production costs and lead times. Additionally, repairing or replacing embedded components can be difficult or impossible.
-
How can artificial intelligence (AI) be applied to PCB design?
- AI and machine learning techniques can be used to optimize PCB layout, component placement, and signal routing. AI-driven PCB design tools can analyze vast amounts of design data, identify potential issues, and suggest improvements, leading to faster design cycles and more reliable PCBs.
Conclusion
As electronic devices continue to become more compact, powerful, and sophisticated, the demand for high-density PCB construction will only increase. New PCB architectures, such as multilayer PCBs, HDI PCBs, rigid-flex PCBs, and embedded component PCBs, offer various advantages in terms of density, electrical performance, and reliability. However, these advanced architectures also present design and manufacturing challenges that require specialized knowledge and tools to overcome.
Looking to the future, emerging technologies such as 3D PCB architecture, organic and printed electronics, and AI-driven PCB design will shape the landscape of PCB manufacturing. As these technologies mature, they will enable even higher levels of miniaturization, functionality, and cost-effectiveness in electronic devices.
By staying up-to-date with the latest developments in PCB architectures and technologies, electronics manufacturers can position themselves to meet the ever-increasing demands of the market and create innovative, high-performance products that push the boundaries of what is possible.
No responses yet