Introduction to Nickel-Gold surface finish
Nickel-Gold (Ni-Au) surface finish is a popular choice in the electronics industry due to its excellent properties, such as good solderability, corrosion resistance, and electrical conductivity. This surface finish is widely used in various applications, including printed circuit boards (PCBs), connectors, and semiconductor packaging. In recent years, new options for chemical Nickel-Gold surface finish have emerged, offering improved performance and cost-effectiveness.
Advantages of Nickel-Gold surface finish
- Excellent solderability
- High corrosion resistance
- Good electrical conductivity
- Compatibility with various soldering processes
- Suitable for high-reliability applications
Traditional Nickel-Gold surface finish process
The traditional Nickel-Gold surface finish process involves two main steps:
- Electroless nickel plating
- Immersion Gold plating
Electroless nickel plating
Electroless nickel plating is a chemical process that deposits a uniform layer of nickel on the surface of the substrate without the use of an external electrical current. The process involves the following steps:
- Surface preparation: The substrate is cleaned and activated to ensure proper adhesion of the nickel layer.
- Nickel plating: The substrate is immersed in an electroless nickel plating solution, which contains nickel ions, reducing agents, and complexing agents. The nickel ions are reduced to metallic nickel and deposited on the surface of the substrate.
Immersion gold plating
Immersion gold plating is a chemical process that deposits a thin layer of gold on top of the nickel layer. The process involves the following steps:
- Activation: The nickel surface is activated to promote the deposition of gold.
- Gold plating: The substrate is immersed in an immersion gold plating solution, which contains gold ions and a reducing agent. The gold ions are reduced to metallic gold and deposited on the nickel surface through a displacement reaction.
The typical thickness of the nickel layer in a Nickel-Gold surface finish ranges from 3 to 6 μm, while the gold layer thickness is usually between 0.05 and 0.2 μm.
New options for chemical Nickel-Gold surface finish
1. Electroless Nickel Electroless Palladium Immersion Gold (ENEPIG)
ENEPIG is a three-layer surface finish that consists of an electroless nickel layer, an electroless palladium layer, and an immersion gold layer. The addition of the palladium layer between the nickel and gold layers offers several advantages:
- Improved solder joint reliability: The palladium layer acts as a barrier, preventing the formation of brittle intermetallic compounds between the nickel and gold layers during soldering.
- Better Wire Bonding performance: The palladium layer provides a suitable surface for wire bonding, ensuring strong and reliable bonds.
- Enhanced corrosion resistance: The palladium layer further enhances the corrosion resistance of the surface finish.
The typical thickness of the layers in an ENEPIG surface finish are:
Layer | Thickness (μm) |
---|---|
Nickel | 3-6 |
Palladium | 0.05-0.15 |
Gold | 0.05-0.15 |
2. Electroless Nickel Electroless Palladium Autocatalytic Gold (ENEPAG)
ENEPAG is a variation of the ENEPIG surface finish, where the immersion gold layer is replaced by an autocatalytic gold layer. The autocatalytic gold plating process deposits a thicker and more uniform gold layer compared to immersion gold plating. This surface finish offers the following benefits:
- Improved gold layer thickness uniformity: The autocatalytic gold plating process ensures a more consistent gold layer thickness across the surface, reducing the risk of thin spots or voids.
- Better wear resistance: The thicker gold layer provided by the autocatalytic plating process offers better wear resistance, making it suitable for applications with frequent insertions or removals.
- Enhanced wire bonding performance: The thicker and more uniform gold layer improves wire bonding reliability and strength.
The typical thickness of the layers in an ENEPAG surface finish are:
Layer | Thickness (μm) |
---|---|
Nickel | 3-6 |
Palladium | 0.05-0.15 |
Gold | 0.1-0.5 |
3. Electroless Nickel Immersion Gold (ENIG) with organic additives
Recent advancements in electroless nickel plating have led to the development of organic additives that can improve the performance of the ENIG surface finish. These additives, such as nitrogen-containing compounds and sulfur-containing compounds, can modify the properties of the nickel layer, offering the following benefits:
- Enhanced corrosion resistance: The organic additives can improve the corrosion resistance of the nickel layer by forming a protective film on the surface.
- Better thermal stability: The additives can increase the thermal stability of the nickel layer, reducing the risk of intermetallic compound formation during soldering.
- Improved mechanical properties: The modified nickel layer can exhibit better mechanical properties, such as hardness and wear resistance.
The typical thickness of the layers in an ENIG surface finish with organic additives remains the same as the traditional ENIG process:
Layer | Thickness (μm) |
---|---|
Nickel | 3-6 |
Gold | 0.05-0.2 |
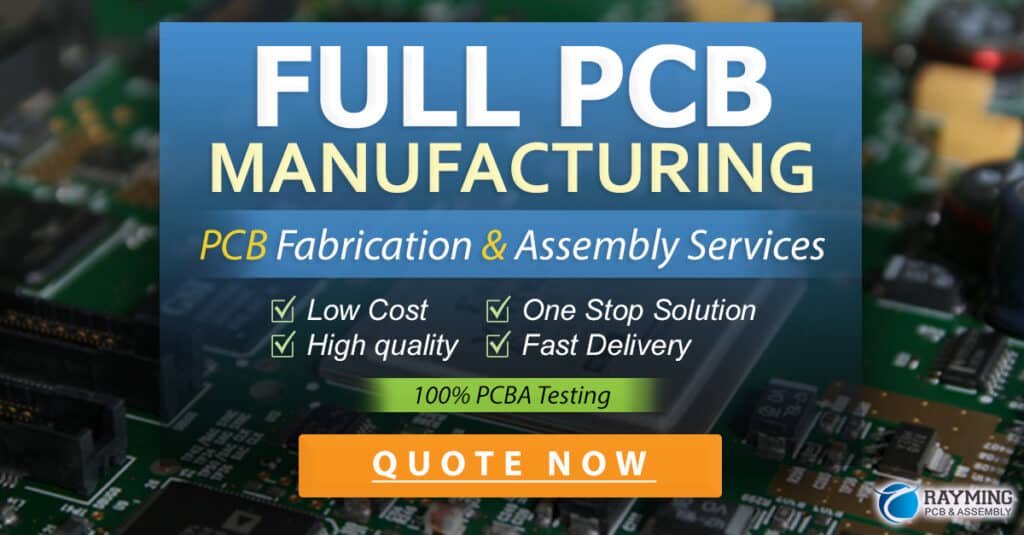
Comparison of Nickel-Gold surface finish options
Surface Finish | Advantages | Disadvantages |
---|---|---|
Traditional ENIG | – Good solderability – Cost-effective |
– Potential for black pad formation – Limited wire bonding performance |
ENEPIG | – Improved solder joint reliability – Better wire bonding performance – Enhanced corrosion resistance |
– Higher cost compared to traditional ENIG – More complex process |
ENEPAG | – Improved gold layer thickness uniformity – Better wear resistance – Enhanced wire bonding performance |
– Higher cost compared to ENEPIG – More complex process |
ENIG with additives | – Enhanced corrosion resistance – Better thermal stability – Improved mechanical properties |
– Potential for increased process complexity – Limited long-term performance data |
Applications of Nickel-Gold surface finish
Nickel-Gold surface finish is widely used in various industries and applications, including:
- Consumer electronics: Smartphones, tablets, laptops, and wearable devices.
- Automotive electronics: Engine control units, sensors, and infotainment systems.
- Aerospace and defense: Avionics, radar systems, and satellite communication devices.
- Medical devices: Implantable devices, diagnostic equipment, and surgical instruments.
- Industrial electronics: Process control systems, automation equipment, and power electronics.
Future trends in Nickel-Gold surface finish
As the electronics industry continues to evolve, new trends and developments in Nickel-Gold surface finish are expected to emerge:
- Thinner gold layers: The trend towards miniaturization and cost reduction may lead to the development of surface finishes with thinner gold layers while maintaining the required performance.
- New additives and formulations: Research into new organic additives and plating solution formulations may result in further improvements in the properties and performance of Nickel-Gold surface finishes.
- Environmentally friendly processes: The development of more environmentally friendly plating processes, such as those with reduced water and energy consumption, may become increasingly important.
- Integration with advanced packaging technologies: As advanced packaging technologies, such as 2.5D and 3D packaging, gain popularity, Nickel-Gold surface finishes may need to adapt to meet the specific requirements of these technologies.
Frequently Asked Questions (FAQ)
- What is the purpose of the nickel layer in a Nickel-Gold surface finish?
-
The nickel layer serves as a barrier to prevent copper diffusion from the substrate into the gold layer. It also provides a smooth and uniform surface for the deposition of the gold layer.
-
How does the gold layer thickness affect the performance of a Nickel-Gold surface finish?
-
The gold layer thickness can affect the solderability, wire bonding performance, and wear resistance of the surface finish. Thicker gold layers generally provide better performance but also increase the cost.
-
What are the main differences between ENIG and ENEPIG surface finishes?
-
ENEPIG has an additional electroless palladium layer between the nickel and gold layers, which improves solder joint reliability, wire bonding performance, and corrosion resistance compared to traditional ENIG.
-
Can Nickel-Gold surface finishes be used for high-frequency applications?
-
Yes, Nickel-Gold surface finishes are suitable for high-frequency applications due to their good electrical conductivity and low signal loss. However, the specific requirements of the application should be considered when selecting the appropriate surface finish.
-
How can the formation of black pad be prevented in ENIG surface finishes?
- The formation of black pad in ENIG surface finishes can be prevented by optimizing the plating process parameters, such as the composition of the plating solutions, the plating temperature, and the plating time. The use of organic additives in the nickel plating solution can also help reduce the risk of black pad formation.
Conclusion
Chemical Nickel-Gold surface finish continues to be a popular choice in the electronics industry due to its excellent properties and versatility. The development of new options, such as ENEPIG, ENEPAG, and ENIG with organic additives, has expanded the range of applications and performance characteristics available. As the electronics industry advances, further innovations in Nickel-Gold surface finish are expected to emerge, addressing the evolving needs of various applications and technologies.
No responses yet