Introduction to Stepper Motors
Stepper motors are a type of brushless DC electric motor that divides a full rotation into a number of equal steps. They are widely used in applications requiring precise positioning and speed control, such as 3D printers, CNC machines, and robotics. Among the various types of stepper motors, the NEMA 17 has gained popularity due to its high torque output and compact size.
What is a NEMA 17 Stepper Motor?
A NEMA 17 stepper motor is a type of stepper motor with a faceplate size of 1.7 inches x 1.7 inches (43.2 mm x 43.2 mm). The “NEMA” stands for National Electrical Manufacturers Association, which standardizes motor dimensions and specifications. NEMA 17 motors are known for their high torque-to-size ratio, making them suitable for a wide range of applications.
Working Principle of Stepper Motors
Stator and Rotor
A stepper motor consists of two main components: the stator and the rotor. The stator is the stationary part of the motor and contains a series of electromagnets arranged in a circular pattern. The rotor, on the other hand, is the moving part of the motor and is made of a permanent magnet or a soft magnetic material with teeth.
Stepping Sequence
The working principle of a stepper motor relies on the precise control of the electromagnetic fields generated by the stator. By energizing the stator coils in a specific sequence, the rotor can be made to rotate in discrete steps. The stepping sequence determines the direction and speed of rotation.
Full-Step Sequence
In a full-step sequence, the motor moves one full step at a time. The stator coils are energized in a specific order, causing the rotor to align with the magnetic fields and rotate by a fixed angle. The step angle depends on the number of poles in the motor and can range from 0.9° to 90°.
Step | Coil A | Coil B | Coil C | Coil D |
---|---|---|---|---|
1 | ON | OFF | OFF | OFF |
2 | OFF | ON | OFF | OFF |
3 | OFF | OFF | ON | OFF |
4 | OFF | OFF | OFF | ON |
Half-Step Sequence
In a half-step sequence, the motor moves half a step at a time, resulting in smoother motion and increased resolution. This is achieved by energizing two adjacent coils simultaneously, creating an intermediate position between full steps.
Step | Coil A | Coil B | Coil C | Coil D |
---|---|---|---|---|
1 | ON | OFF | OFF | OFF |
2 | ON | ON | OFF | OFF |
3 | OFF | ON | OFF | OFF |
4 | OFF | ON | ON | OFF |
5 | OFF | OFF | ON | OFF |
6 | OFF | OFF | ON | ON |
7 | OFF | OFF | OFF | ON |
8 | ON | OFF | OFF | ON |
Microstepping
Microstepping is a technique used to further increase the resolution and smoothness of stepper motor motion. By precisely controlling the current in each stator coil, the motor can achieve intermediate positions between full steps, effectively dividing each step into smaller microsteps.
Microstepping allows for finer positioning and reduced vibration, but it also decreases the available torque output. The number of microsteps per full step can vary, with common values being 2, 4, 8, 16, and 32.
NEMA 17 Stepper Motor Specifications
Physical Dimensions
NEMA 17 stepper motors have a standard faceplate size of 1.7 inches x 1.7 inches (43.2 mm x 43.2 mm). The body length can vary depending on the specific model and manufacturer, ranging from 34 mm to 60 mm or more.
Electrical Specifications
NEMA 17 stepper motors are typically available in various electrical configurations, including:
- Voltage: 12V, 24V, 48V
- Current: 0.5A to 2A per phase
- Resistance: 1.5Ω to 10Ω per phase
- Inductance: 2mH to 10mH per phase
The specific electrical specifications will depend on the motor’s intended application and performance requirements.
Torque Output
One of the key advantages of NEMA 17 stepper motors is their high torque output relative to their size. The holding torque, which is the maximum torque the motor can generate when energized but not rotating, can range from 0.2 N·m to 0.6 N·m or more.
The actual torque output during rotation will depend on factors such as the motor’s speed, load, and driving current. Torque-speed curves provided by the manufacturer can help in selecting the appropriate motor for a given application.
Step Angle and Resolution
NEMA 17 stepper motors are available with different step angles, which determine the number of steps per revolution. Common step angles include:
- 1.8° (200 steps/rev)
- 0.9° (400 steps/rev)
- 7.5° (48 steps/rev)
- 15° (24 steps/rev)
The choice of step angle will depend on the required resolution and positioning accuracy of the application. Higher resolution motors with smaller step angles provide more precise control but may have lower torque output.
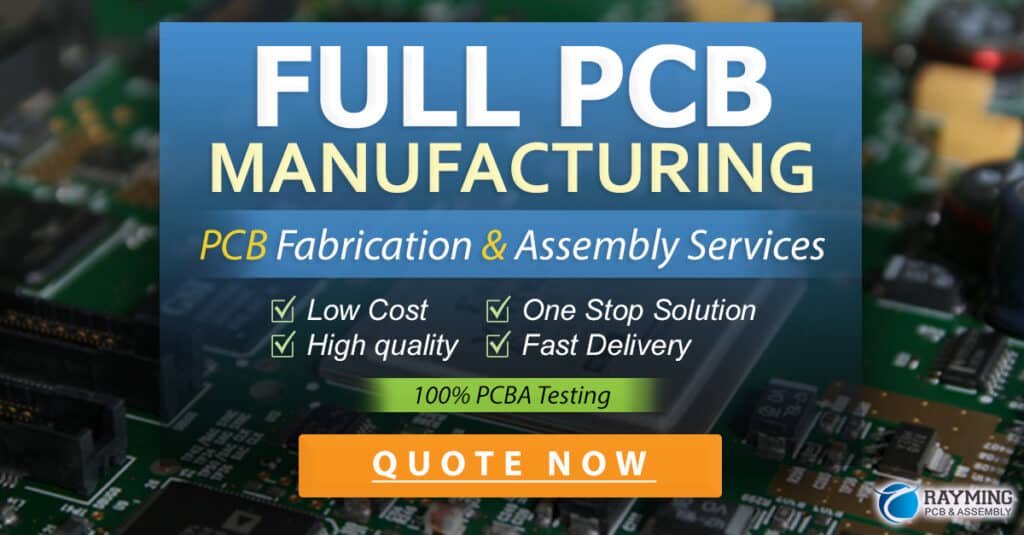
Applications of NEMA 17 Stepper Motors
3D Printing
NEMA 17 stepper motors are widely used in 3D printers to drive the X, Y, and Z axes. Their high torque output and precise positioning capabilities make them suitable for accurately moving the print head and build platform.
CNC Machines
In CNC (Computer Numerical Control) machines, NEMA 17 stepper motors are used to control the motion of the cutting tools and workpiece. They provide the necessary precision and torque for machining operations such as milling, drilling, and routing.
Robotics
NEMA 17 stepper motors are commonly used in robotic applications, such as robotic arms and grippers. Their compact size and high torque output make them suitable for precise positioning and movement control in robotic systems.
Other Applications
NEMA 17 stepper motors find use in various other applications, including:
- Automated dispensing systems
- Surveillance cameras
- Textile machinery
- Medical equipment
- Packaging machinery
Controlling NEMA 17 Stepper Motors
Stepper Motor Drivers
To control a NEMA 17 stepper motor, a stepper motor driver is required. The driver acts as an interface between the motor and the control system, converting the digital control signals into the appropriate sequence of electrical pulses to drive the motor.
Stepper motor drivers can be either unipolar or bipolar, depending on the motor’s winding configuration. They also provide features such as microstepping, current control, and protection against over-current and over-temperature conditions.
Control Systems
NEMA 17 stepper motors can be controlled using various control systems, including:
- Microcontrollers (e.g., Arduino, Raspberry Pi)
- PLC (Programmable Logic Controllers)
- CNC controllers
- Dedicated motion control boards
The control system sends the necessary step and direction signals to the stepper motor driver, which then translates them into the appropriate electrical pulses to drive the motor.
Software and Programming
Controlling NEMA 17 stepper motors often involves writing software or firmware to generate the desired motion profiles and control sequences. Programming languages such as C, C++, and Python are commonly used for this purpose.
There are also various libraries and frameworks available that simplify the process of controlling stepper motors, such as:
- AccelStepper (Arduino)
- GPIO Zero (Raspberry Pi)
- GRBL (CNC control)
- Marlin (3D printer firmware)
These libraries provide high-level functions for setting motor speed, acceleration, and position, as well as handling complex motion profiles and synchronization between multiple motors.
Advantages and Disadvantages of NEMA 17 Stepper Motors
Advantages
- High torque output relative to size
- Precise positioning and speed control
- Open-loop operation (no feedback required)
- Low cost compared to servo motors
- Wide availability and standardized dimensions
Disadvantages
- Limited speed range (typically below 1000 RPM)
- Reduced torque at higher speeds
- Potential for resonance and vibration
- Power inefficiency compared to brushless DC motors
- Requires a stepper motor driver for operation
Frequently Asked Questions (FAQ)
1. What is the difference between a NEMA 17 and a NEMA 23 stepper motor?
The main difference between a NEMA 17 and a NEMA 23 stepper motor is the size. NEMA 23 motors have a larger faceplate size of 2.3 inches x 2.3 inches (58.4 mm x 58.4 mm) compared to the 1.7 inches x 1.7 inches (43.2 mm x 43.2 mm) of a NEMA 17 motor. NEMA 23 motors also typically have higher torque output and current ratings.
2. Can a NEMA 17 stepper motor be used with a belt drive system?
Yes, NEMA 17 stepper motors can be used with belt drive systems. In fact, belt drives are commonly used in applications such as 3D printers and CNC machines to transmit the motor’s motion to the linear axes. The motor is coupled to a pulley, which drives a belt connected to the linear motion components.
3. How do I choose the right NEMA 17 stepper motor for my application?
When selecting a NEMA 17 stepper motor for your application, consider the following factors:
- Torque requirements
- Speed range
- Step angle and resolution
- Voltage and current ratings
- Physical dimensions and mounting options
- Compatibility with the stepper motor driver and control system
It’s also important to refer to the motor’s datasheet and torque-speed curves to ensure that it meets the specific requirements of your application.
4. Can I use a NEMA 17 stepper motor without a driver?
No, a NEMA 17 stepper motor cannot be used without a stepper motor driver. The driver is responsible for converting the digital control signals into the appropriate sequence of electrical pulses to energize the motor’s coils. Attempting to connect a NEMA 17 motor directly to a power supply or control system can damage the motor and the control electronics.
5. How do I reduce the noise and vibration of a NEMA 17 stepper motor?
To reduce the noise and vibration of a NEMA 17 stepper motor, consider the following techniques:
- Use microstepping to smooth out the motor’s motion
- Ensure proper mechanical mounting and alignment
- Use damping materials or vibration isolation mounts
- Adjust the motor’s current and voltage settings
- Implement acceleration and deceleration ramps in the motion profile
- Use a motor with a higher resolution (smaller step angle)
Additionally, operating the motor at speeds that avoid its resonant frequencies can help minimize vibration and noise.
Conclusion
NEMA 17 stepper motors are versatile and widely used in applications requiring precise positioning and speed control. Their high torque output, compact size, and standardized dimensions make them a popular choice for 3D printers, CNC machines, robotics, and various other automation systems.
Understanding the working principle, specifications, and control methods of NEMA 17 stepper motors is essential for selecting the appropriate motor and implementing it effectively in your application. By considering factors such as torque requirements, speed range, and compatibility with the control system, you can ensure optimal performance and reliability.
As technology advances, NEMA 17 stepper motors continue to find new applications and play a crucial role in the world of motion control and automation. With their precision, durability, and affordability, these motors are likely to remain a key component in a wide range of industries and projects.
No responses yet