Introduction to Microwave PCB Laminates
In the world of high-frequency electronics, microwave printed circuit board (PCB) laminates play a crucial role in ensuring stable performance and reliability in demanding applications. These specialized materials are designed to minimize signal loss, maintain integrity, and withstand the rigors of high-power microwave systems. This article delves into the intricacies of microwave PCB laminates, exploring their unique properties, advantages, and applications in various industries.
What are Microwave PCB Laminates?
Microwave PCB laminates are substrate materials specifically engineered for use in high-frequency electronic circuits operating in the microwave range, typically from 300 MHz to 300 GHz. These laminates exhibit exceptional electrical and mechanical properties, making them ideal for applications that demand stable performance, low signal loss, and high power handling capabilities.
Key Properties of Microwave PCB Laminates
To understand the significance of microwave PCB laminates, it’s essential to grasp their key properties:
-
Dielectric Constant (Dk): The dielectric constant represents the material’s ability to store electrical energy. Microwave PCB laminates typically have a low and stable dielectric constant, minimizing signal distortion and ensuring consistent performance across a wide frequency range.
-
Dissipation Factor (Df): Also known as the loss tangent, the dissipation factor measures the amount of energy lost as heat when an electrical signal passes through the material. Low dissipation factors are crucial for minimizing signal attenuation and maintaining signal integrity in microwave applications.
-
Thermal Stability: Microwave PCB laminates must maintain their electrical and mechanical properties over a wide temperature range. High thermal stability ensures reliable performance in demanding environments, such as aerospace and defense systems.
-
Mechanical Strength: The ability to withstand physical stress and maintain dimensional stability is essential for microwave PCB laminates. These materials should exhibit high flexural and tensile strength, as well as resistance to warping and twisting.
Popular Microwave PCB Laminate Materials
Several materials have emerged as popular choices for microwave PCB laminates due to their exceptional properties and performance. Let’s explore some of the most widely used options:
PTFE (Polytetrafluoroethylene)
PTFE, commonly known by its trade name Teflon, is a fluoropolymer with excellent electrical and thermal properties. It offers a low dielectric constant (2.1), low dissipation factor (0.0002), and high thermal stability. PTFE laminates are commonly used in applications such as radar systems, satellite communications, and high-speed digital circuits.
Rogers Corporation Laminates
Rogers Corporation is a leading manufacturer of high-performance microwave PCB laminates. Some of their popular products include:
-
RO4000 Series: These hydrocarbon ceramic laminates offer a low dielectric constant (3.3-3.7), low dissipation factor (0.0027-0.0037), and excellent thermal stability. They are suitable for applications such as wireless infrastructure, automotive radar, and aerospace systems.
-
RT/duroid Series: RT/duroid laminates are PTFE-based materials with low dielectric constant (2.2-2.9), low dissipation factor (0.0009-0.0022), and high thermal stability. They are widely used in military and commercial radar, satellite communications, and high-speed digital circuits.
Isola Group Laminates
Isola Group offers a range of microwave PCB laminates designed for high-frequency applications:
-
I-Tera MT40: This low-loss laminate features a dielectric constant of 3.45 and a dissipation factor of 0.0031 at 10 GHz. It offers excellent thermal stability and is suitable for applications such as 5G infrastructure, automotive radar, and aerospace systems.
-
TerraGreen: TerraGreen is an environmentally friendly halogen-free laminate with a dielectric constant of 3.4 and a dissipation factor of 0.0027 at 10 GHz. It is designed for high-speed digital and RF applications, offering excellent signal integrity and thermal performance.
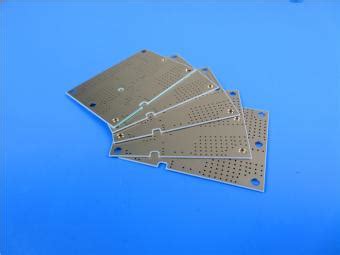
Applications of Microwave PCB Laminates
Microwave PCB laminates find extensive use in various industries and applications that require stable, low-loss performance at high frequencies. Some of the key application areas include:
Telecommunications
In the telecommunications industry, microwave PCB laminates are essential for the development of high-speed wireless networks, such as 5G infrastructure. These materials enable the design of compact, efficient, and reliable microwave components, including antennas, filters, and power amplifiers.
Aerospace and Defense
Aerospace and defense applications demand the highest level of performance and reliability from microwave PCB laminates. These materials are used in radar systems, satellite communications, avionics, and electronic warfare systems. The stability and low-loss properties of microwave PCB laminates ensure accurate signal transmission and reception, even in harsh environments.
Automotive
With the increasing adoption of advanced driver assistance systems (ADAS) and autonomous vehicles, microwave PCB laminates have become crucial in automotive applications. These materials are used in automotive radar systems, enabling features such as collision avoidance, adaptive cruise control, and blind-spot detection. The low dielectric constant and low dissipation factor of microwave PCB laminates ensure reliable and precise radar performance.
Medical Electronics
Microwave PCB laminates are also finding applications in medical electronics, particularly in devices that utilize high-frequency signals. Examples include medical imaging systems, such as MRI and CT scanners, as well as microwave ablation devices for cancer treatment. The stability and low-loss properties of these laminates ensure accurate and reliable performance in these critical medical applications.
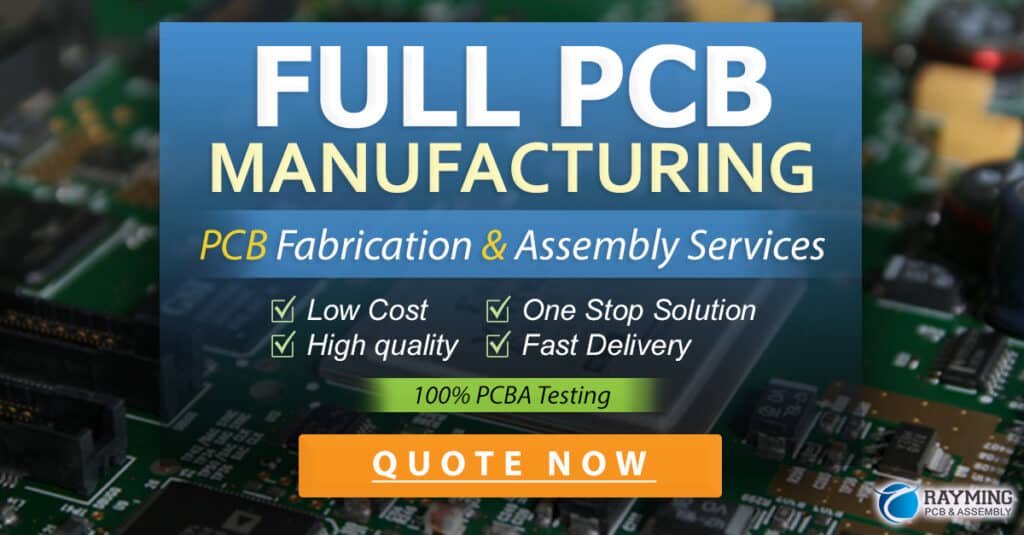
Choosing the Right Microwave PCB Laminate
Selecting the appropriate microwave PCB laminate for a specific application requires careful consideration of several factors:
-
Frequency Range: The operating frequency range of the application determines the required dielectric constant and dissipation factor of the laminate. Higher frequencies typically demand lower dielectric constants and dissipation factors to minimize signal loss.
-
Power Handling: The laminate’s ability to withstand high power levels is crucial in applications such as radar systems and power amplifiers. Materials with high thermal conductivity and thermal stability are preferred for high-power applications.
-
Environmental Conditions: The operating environment of the application, including temperature range, humidity, and exposure to chemicals, should be considered when choosing a microwave PCB laminate. Materials with high thermal stability and chemical resistance are essential for harsh environments.
-
Manufacturing Process: The ease of manufacturing and processing the laminate should be taken into account. Some materials, such as PTFE, require specialized processing techniques, which can increase production costs and lead times.
-
Cost: The cost of the laminate is an important factor, especially for high-volume production. A balance between performance and cost should be achieved based on the specific requirements of the application.
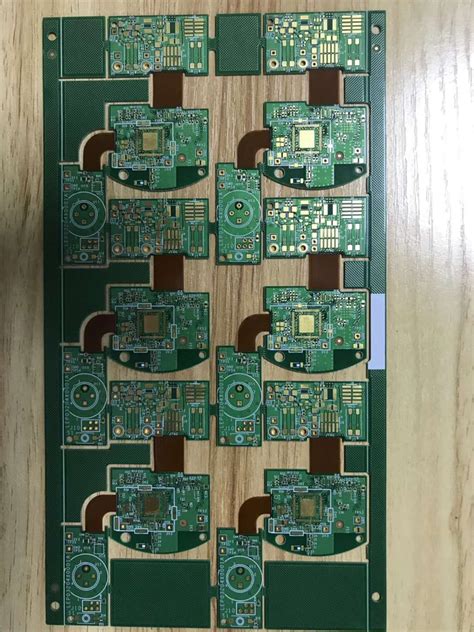
Comparison of Microwave PCB Laminates
To aid in the selection process, the following table provides a comparison of some popular microwave PCB laminates:
Laminate | Dielectric Constant (Dk) | Dissipation Factor (Df) | Thermal Stability | Applications |
---|---|---|---|---|
PTFE | 2.1 | 0.0002 | High | Radar, satellite communications, high-speed digital |
Rogers RO4000 Series | 3.3-3.7 | 0.0027-0.0037 | High | Wireless infrastructure, automotive radar, aerospace |
Rogers RT/duroid | 2.2-2.9 | 0.0009-0.0022 | High | Military and commercial radar, satellite communications |
Isola I-Tera MT40 | 3.45 | 0.0031 (at 10 GHz) | High | 5G infrastructure, automotive radar, aerospace |
Isola TerraGreen | 3.4 | 0.0027 (at 10 GHz) | High | High-speed digital, RF applications |
Fabrication Considerations for Microwave PCB Laminates
When working with microwave PCB laminates, several fabrication considerations should be kept in mind to ensure optimal performance and reliability:
-
Controlled Impedance: Maintaining consistent impedance throughout the PCB is crucial for minimizing signal reflections and distortions. Careful design and manufacturing techniques, such as precise control of trace widths and spacing, are necessary to achieve controlled impedance.
-
Via Hole Plating: In high-frequency PCBs, via holes can introduce significant signal loss and reflections. Proper via hole plating techniques, such as copper filling or conductive polymer filling, can help mitigate these issues and improve signal integrity.
-
Surface Finish: The choice of surface finish can impact the performance of microwave PCBs. Low-loss surface finishes, such as immersion silver or electroless nickel/immersion gold (ENIG), are preferred for high-frequency applications.
-
Laminate Thickness: The thickness of the laminate should be carefully selected based on the desired electrical performance and mechanical requirements. Thinner laminates are often used for high-frequency applications to minimize dielectric losses and improve signal propagation.
-
copper roughness: The roughness of the copper surface can affect signal integrity at high frequencies. Smooth copper surfaces are preferable for microwave applications to reduce Skin Effect losses and improve signal transmission.
Future Trends in Microwave PCB Laminates
As the demand for high-frequency electronics continues to grow, advancements in microwave PCB laminate technology are expected to keep pace. Some of the future trends in this field include:
-
Ultra-Low-Loss Materials: The development of new materials with even lower dielectric constants and dissipation factors will enable the design of high-performance microwave systems operating at higher frequencies and with reduced signal loss.
-
3D Printing: Additive manufacturing techniques, such as 3D printing, are being explored for the fabrication of microwave PCBs. These methods offer the potential for more complex geometries, reduced manufacturing time, and customization of dielectric properties.
-
Integration with Advanced Packaging: The integration of microwave PCB laminates with advanced packaging technologies, such as system-in-package (SiP) and wafer-level packaging (WLP), will enable the development of compact, high-performance microwave modules for various applications.
-
Environmentally Friendly Materials: The increasing focus on sustainability is driving the development of environmentally friendly microwave PCB laminates. Halogen-free and low-toxicity materials are being explored to reduce the environmental impact of electronic waste.
Frequently Asked Questions (FAQ)
- What is the difference between the dielectric constant (Dk) and dissipation factor (Df)?
The dielectric constant (Dk) represents the material’s ability to store electrical energy, while the dissipation factor (Df) measures the amount of energy lost as heat when an electrical signal passes through the material. A low Dk is desirable for minimizing signal distortion, and a low Df is essential for reducing signal loss.
- Can microwave PCB laminates be used for low-frequency applications?
While microwave PCB laminates are specifically designed for high-frequency applications, they can also be used for low-frequency applications. However, the superior electrical properties of these materials may not be fully utilized at lower frequencies, and their higher cost compared to standard PCB laminates may not be justified.
- What is the typical operating frequency range for microwave PCB laminates?
Microwave PCB laminates are designed to operate in the microwave frequency range, typically from 300 MHz to 300 GHz. However, the specific frequency range may vary depending on the material properties and application requirements.
- How does the choice of microwave PCB laminate affect signal integrity?
The choice of microwave PCB laminate directly impacts signal integrity. Materials with low dielectric constants and dissipation factors minimize signal distortion and loss, ensuring accurate signal transmission and reception. Additionally, the thermal stability and mechanical properties of the laminate contribute to maintaining signal integrity under various operating conditions.
- Are microwave PCB laminates more expensive than standard PCB laminates?
Yes, microwave PCB laminates are generally more expensive than standard PCB laminates due to their specialized properties and the advanced manufacturing processes required. The higher cost is justified by the superior performance and reliability offered by these materials in high-frequency applications.
Conclusion
Microwave PCB laminates are essential materials for the design and fabrication of high-frequency electronic systems. Their unique properties, including low dielectric constants, low dissipation factors, and high thermal stability, enable stable and reliable performance in demanding applications such as telecommunications, aerospace, defense, automotive, and medical electronics.
When selecting a microwave PCB laminate, careful consideration should be given to factors such as the operating frequency range, power handling requirements, environmental conditions, manufacturing process, and cost. Popular laminate materials, such as PTFE and products from Rogers Corporation and Isola Group, offer a range of options to meet the specific needs of various applications.
As the demand for high-frequency electronics continues to grow, advancements in microwave PCB laminate technology are expected to drive the development of ultra-low-loss materials, innovative fabrication techniques, and integration with advanced packaging solutions. Additionally, the increasing focus on sustainability will likely lead to the development of more environmentally friendly laminate materials.
By understanding the properties, advantages, and applications of microwave PCB laminates, engineers and designers can make informed decisions when selecting materials for their high-frequency projects. The continued evolution of these specialized laminates will play a crucial role in enabling the next generation of microwave systems, pushing the boundaries of performance and reliability in an increasingly connected world.
No responses yet