Introduction to Transmission Line Design
Transmission lines are essential components in high-frequency electronic circuits, enabling the efficient transmission of electromagnetic waves. Various types of transmission lines are used in modern electronic systems, each with its unique characteristics and design considerations. In this article, we will explore the design principles and applications of four commonly used transmission lines: microstrip, stripline, coplanar waveguide (CPW), and substrate integrated waveguide (SIW).
Table of Contents
- Microstrip Design
- Stripline Design
- Coplanar Waveguide (CPW) Design
- Substrate Integrated Waveguide (SIW) Design
- Comparison of Transmission Line Types
- Applications of Transmission Lines
- Frequently Asked Questions (FAQ)
Microstrip Design
Microstrip is one of the most widely used transmission line structures in high-frequency electronic circuits. It consists of a conducting strip separated from a ground plane by a dielectric substrate. The simplicity of its structure and ease of fabrication make it a popular choice for many applications.
Microstrip Structure and Characteristics
The microstrip structure comprises three main components:
1. Conducting strip: A narrow, flat conductor that carries the signal.
2. Dielectric substrate: An insulating material that separates the conducting strip from the ground plane.
3. Ground plane: A conducting layer that serves as a reference for the signal.
The characteristic impedance and effective permittivity of a microstrip line depend on the width of the conducting strip (W), the thickness of the dielectric substrate (H), and the relative permittivity of the substrate material (εr).
Microstrip Design Equations
To design a microstrip line with a desired characteristic impedance (Z0), the following equations can be used:
For W/H ≤ 1:
Z0 = (60 / √εe) * ln(8H / W + 0.25W / H)
For W/H ≥ 1:
Z0 = (120π / √εe) / [W/H + 1.393 + 0.667 ln(W/H + 1.444)]
Where:
– εe = (εr + 1) / 2 + [(εr – 1) / 2] * [1 + 12H / W]^(-0.5)
Microstrip Discontinuities and Compensation
Microstrip lines may experience discontinuities due to bends, junctions, and transitions. These discontinuities can cause reflections and degrade the performance of the circuit. To minimize the impact of discontinuities, various compensation techniques can be employed, such as:
– Mitered bends
– Tapered transitions
– Impedance matching networks
Stripline Design
Stripline is another popular transmission line structure that offers several advantages over microstrip, including better isolation and reduced radiation losses. In a stripline, the conducting strip is sandwiched between two ground planes and surrounded by a dielectric substrate.
Stripline Structure and Characteristics
The stripline structure consists of the following components:
1. Conducting strip: A flat conductor that carries the signal, located between two ground planes.
2. Dielectric substrate: An insulating material that surrounds the conducting strip and separates it from the ground planes.
3. Ground planes: Two conducting layers, one above and one below the dielectric substrate, that serve as references for the signal.
The characteristic impedance of a stripline depends on the width of the conducting strip (W), the thickness of the dielectric substrate (H), and the relative permittivity of the substrate material (εr).
Stripline Design Equations
To design a stripline with a desired characteristic impedance (Z0), the following equations can be used:
For 0.35 ≤ W/H ≤ 2:
Z0 = (60 / √εr) * ln(4H / 0.67πW)
For W/H < 0.35:
Z0 = (30π / √εr) / [0.441 + 0.082(W/H) - 0.39(W/H)^2 + 0.45(W/H)^3]
Stripline Discontinuities and Compensation
Like microstrip, stripline may experience discontinuities due to bends, junctions, and transitions. To minimize the impact of discontinuities, similar compensation techniques can be used, such as:
– Mitered bends
– Tapered transitions
– Impedance matching networks
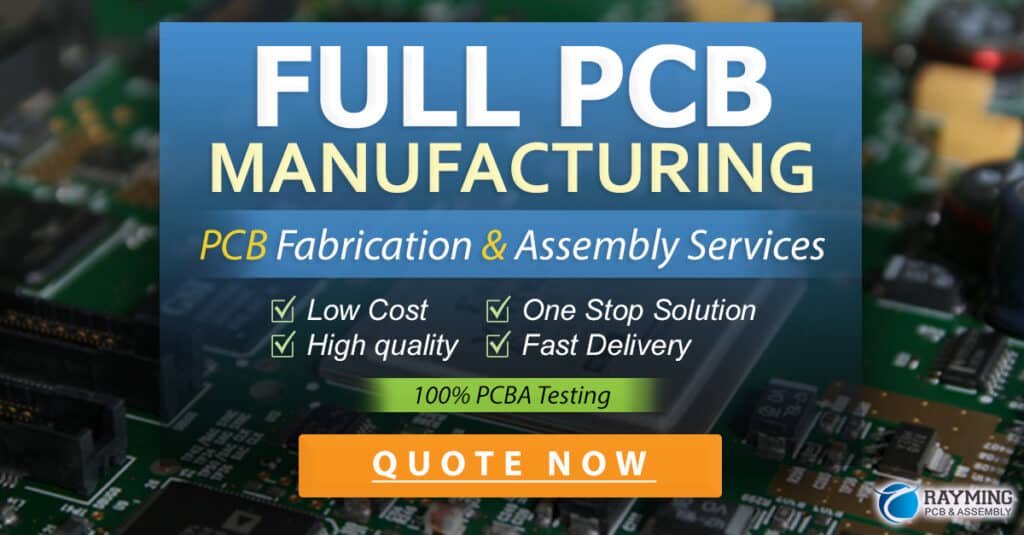
Coplanar Waveguide (CPW) Design
Coplanar waveguide (CPW) is a transmission line structure that offers several advantages, including ease of integration with active devices and low dispersion. In a CPW, the conducting strip and ground planes are located on the same side of the dielectric substrate.
CPW Structure and Characteristics
The CPW structure consists of the following components:
1. Conducting strip: A flat conductor that carries the signal, located between two ground planes on the same side of the substrate.
2. Ground planes: Two conducting layers, one on each side of the conducting strip, that serve as references for the signal.
3. Dielectric substrate: An insulating material that supports the conducting strip and ground planes.
The characteristic impedance of a CPW depends on the width of the conducting strip (W), the gap between the conducting strip and ground planes (G), and the relative permittivity of the substrate material (εr).
CPW Design Equations
To design a CPW with a desired characteristic impedance (Z0), the following equations can be used:
Z0 = (30π / √εe) * K(k') / K(k)
Where:
– k = W / (W + 2G)
– k’ = √(1 – k^2)
– K(k) and K(k’) are complete elliptic integrals of the first kind
– εe = (εr + 1) / 2
CPW Discontinuities and Compensation
CPW may experience discontinuities due to bends, junctions, and transitions. To minimize the impact of discontinuities, various compensation techniques can be employed, such as:
– Air bridges
– Tapered transitions
– Impedance matching networks
Substrate Integrated Waveguide (SIW) Design
Substrate integrated waveguide (SIW) is a relatively new transmission line structure that combines the advantages of traditional waveguides and planar transmission lines. SIW is formed by creating two rows of periodic metallic vias in a dielectric substrate, which act as the sidewalls of the waveguide.
SIW Structure and Characteristics
The SIW structure consists of the following components:
1. Dielectric substrate: An insulating material that forms the body of the waveguide.
2. Metallic vias: Two rows of periodic metallic vias that act as the sidewalls of the waveguide.
3. Conducting layers: Two conducting layers, one on the top and one on the bottom of the substrate, that serve as the top and bottom walls of the waveguide.
The characteristic impedance and cutoff frequency of an SIW depend on the width of the waveguide (W), the diameter of the metallic vias (D), the spacing between the vias (S), and the relative permittivity of the substrate material (εr).
SIW Design Equations
To design an SIW with a desired cutoff frequency (fc), the following equation can be used:
fc = c / (2W√εr)
Where:
– c is the speed of light in vacuum
– W is the width of the waveguide
– εr is the relative permittivity of the substrate material
The diameter of the metallic vias (D) and the spacing between the vias (S) should be chosen such that:
D < λ0 / 5
S ≤ 2D
Where λ0 is the free-space wavelength at the operating frequency.
SIW Transitions and Integration
To integrate SIW with other planar transmission lines, such as microstrip or CPW, suitable transitions must be designed. Various transition structures can be used, including:
– Tapered microstrip-to-SIW transitions
– CPW-to-SIW transitions
– Aperture-coupled transitions
Comparison of Transmission Line Types
The choice of transmission line type depends on various factors, such as the operating frequency, substrate material, circuit complexity, and performance requirements. The following table summarizes the key characteristics of microstrip, stripline, CPW, and SIW:
Transmission Line Type | Advantages | Disadvantages |
---|---|---|
Microstrip | – Simple structure – Easy to fabricate – Low cost |
– Higher radiation losses – Lower isolation |
Stripline | – Better isolation – Reduced radiation losses |
– More complex structure – Higher fabrication cost |
CPW | – Ease of integration with active devices – Low dispersion |
– Higher losses at high frequencies |
SIW | – Low loss – High power handling – Good isolation |
– Larger size compared to planar transmission lines |
Applications of Transmission Lines
Transmission lines find applications in various high-frequency electronic systems, such as:
– Microwave and millimeter-wave circuits
– Antennas and antenna arrays
– Filters and couplers
– Wireless communication systems
– Radar and sensing systems
– High-speed digital circuits
The choice of transmission line type depends on the specific requirements of the application, such as operating frequency, bandwidth, loss, and integration with other components.
Frequently Asked Questions (FAQ)
- What is the main difference between microstrip and stripline?
-
The main difference between microstrip and stripline is that in microstrip, the conducting strip is separated from a single ground plane by a dielectric substrate, while in stripline, the conducting strip is sandwiched between two ground planes and surrounded by a dielectric substrate. Stripline offers better isolation and reduced radiation losses compared to microstrip.
-
What are the advantages of using CPW over microstrip?
-
CPW offers several advantages over microstrip, including ease of integration with active devices and low dispersion. CPW also allows for easier implementation of series and shunt elements, as both ground planes are on the same side of the substrate.
-
When should I consider using SIW instead of planar transmission lines?
-
SIW should be considered when low loss, high power handling, and good isolation are required, especially at higher frequencies. SIW combines the advantages of traditional waveguides and planar transmission lines, making it suitable for applications such as antennas, filters, and high-frequency circuits.
-
How can I minimize the impact of discontinuities in transmission lines?
-
To minimize the impact of discontinuities in transmission lines, various compensation techniques can be employed, such as mitered bends, tapered transitions, impedance matching networks, and air bridges. The specific technique depends on the type of transmission line and the nature of the discontinuity.
-
What factors should I consider when choosing a substrate material for transmission line design?
- When choosing a substrate material for transmission line design, several factors should be considered, including the relative permittivity (εr), loss tangent (tan δ), thermal stability, and mechanical properties. The substrate material should be selected based on the operating frequency, desired characteristic impedance, and the specific application requirements.
In conclusion, understanding the design principles and characteristics of different transmission line types is crucial for developing high-performance high-frequency electronic circuits. By selecting the appropriate transmission line structure and applying proper design techniques, engineers can optimize signal integrity, minimize losses, and ensure reliable operation of their systems.
No responses yet