What is Micro-Sectioning?
Micro-sectioning is the process of preparing a small, representative sample of a material to allow detailed microscopic examination of its internal structure. The goal is to create a sample that is:
- Thin enough to allow light to pass through for optical microscopy
- Flat and smooth to eliminate surface defects and topography
- Representative of the bulk material with minimal damage or alteration from preparation
Micro-sectioning typically involves the following main steps:
- Cutting a small sample from the bulk material
- Mounting the sample in a supportive medium
- Grinding the sample to create a flat surface
- Polishing the sample to remove surface defects
- Etching or coating the sample to reveal microstructural features
By carefully controlling each step, a high-quality sample can be produced for microscopic analysis. Micro-sectioning is used on a wide range of materials, including:
- Metals and alloys
- Ceramics and glasses
- Polymers and composites
- Biological tissues and biomaterials
- Electronic and semiconductor materials
The specific techniques and parameters used for micro-sectioning depend on the type of material being examined and the desired analysis. However, the general principles are the same across different materials and applications.
Importance of Micro-Sectioning
Micro-sectioning is a critical tool for understanding the structure, composition, and properties of materials at the microscopic level. By allowing detailed imaging and analysis of the internal features of a sample, micro-sectioning enables researchers to:
- Examine grain structure, phase distributions, and defects in metals and alloys
- Analyze the microstructure and composition of ceramics and glasses
- Characterize the morphology and interfaces in polymers and composites
- Investigate cell and tissue structure in biological samples
- Identify defects and failure modes in electronic devices and components
The insights gained from micro-sectioning are used to develop new materials, optimize manufacturing processes, analyze failures and defects, and advance scientific understanding in many fields. Some key applications of micro-sectioning include:
Application | Description |
---|---|
Material development | Analyzing microstructure to guide alloy design, heat treatment, etc. |
Quality control | Inspecting products for defects, inclusions, proper microstructure |
Failure analysis | Examining fracture surfaces, corrosion, wear, and other failure modes |
Biological research | Studying tissue morphology, cell interactions, implant interfaces |
Electronics reliability | Identifying defects in solder joints, interconnects, device packaging |
Without micro-sectioning, much of this critical knowledge would be impossible to obtain. As materials and devices become increasingly complex and miniaturized, the importance of micro-sectioning continues to grow.
Micro-Sectioning Equipment and Supplies
To perform micro-sectioning, a variety of specialized equipment and supplies are required. While the specific items needed may vary depending on the material and application, a typical micro-sectioning lab will include:
Cutting Equipment
- Precision saws (abrasive, diamond) for initial sectioning of samples
- Wirght saws, EDM, or other tools for smaller, more delicate cuts
Mounting Supplies
- Mounting cups, clips, and molds to hold samples during grinding/polishing
- Mounting media (epoxy, acrylic, etc.) to embed samples
- Curing ovens or lamps to harden mounting media
Grinding and Polishing Machines
- Benchtop grinder/polisher with interchangeable platens
- Semi- or fully-automated systems for high-volume prep
- Vibratory polishers for gentle final polishing
Abrasive Pads, Discs, and Suspensions
- Silicon carbide papers in various grits for grinding
- Diamond films or suspensions for intermediate polishing
- Aluminum oxide or other fine abrasives for final polishing
Microscopes and Imaging Equipment
- Optical microscopes (stereo, compound, inverted)
- Digital cameras and software for image capture and analysis
- Scanning electron microscopes (SEM) for high-resolution imaging
Miscellaneous Supplies
- Cleaning agents (solvents, detergents) and ultrasonic cleaners
- Etching solutions and fume hoods for chemical etching
- Personal protective equipment (gloves, safety glasses, lab coats)
The quality of the micro-sectioning equipment and supplies directly impacts the quality of the prepared samples and resulting analysis. Investing in proper tools and consumables is essential for producing reliable, repeatable results.
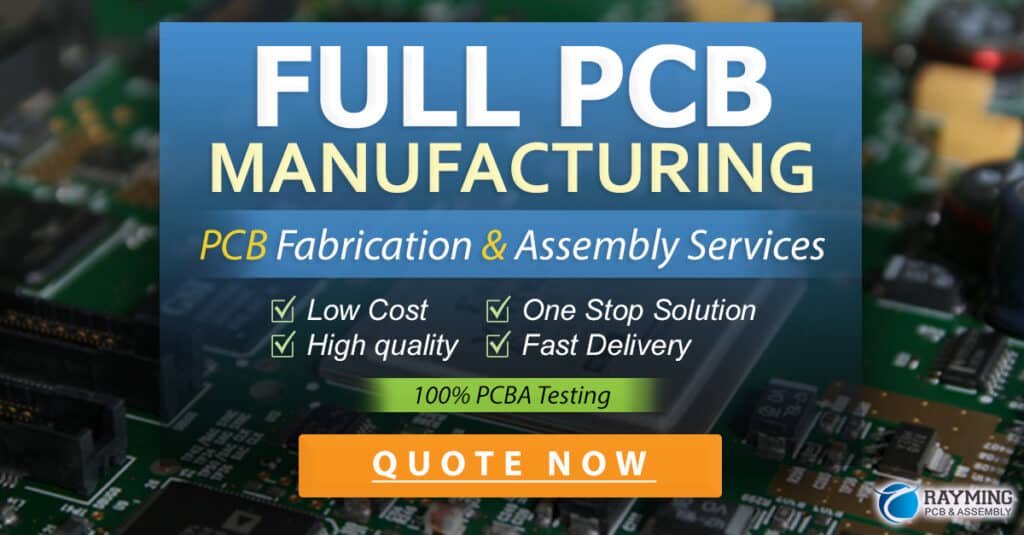
Step-by-Step Micro-Sectioning Procedure
While the exact procedure for micro-sectioning varies based on the material and desired analysis, the general steps are as follows:
1. Sample Cutting
The first step is to cut a small, representative sample from the bulk material. The sample should be:
- Small enough to fit in the mounting cup (typically max. 1-2 inch)
- Oriented to show the desired cross-section or surface
- Cut with minimal damage using appropriate tools (saw, wirght, shears)
Take care to avoid overheating, deforming, or contaminating the sample during cutting. Properly clean and label the sample before proceeding.
2. Mounting
Next, the cut sample is mounted in a supportive medium to allow handling and grinding/polishing. Common mounting methods include:
- Compression mounting with acrylic or other thermoplastic
- Castable mounting with two-part epoxy or polyester
- Wax or adhesive mounting for temporary or delicate samples
Follow the manufacturer’s instructions for mixing, pouring, and curing the mounting media. Ensure the sample is properly oriented and labeled within the mount.
3. Grinding
After mounting, the sample is ground to create a flat, planar surface for polishing. Grinding is typically done with progressively finer abrasive papers, such as:
Abrasive | Grit Size | Purpose |
---|---|---|
Silicon Carbide | 120-320 | Initial planarization |
Silicon Carbide | 400-600 | Intermediate grinding |
Silicon Carbide | 800-1200 | Fine grinding |
Use water as a lubricant and coolant during grinding. Check the sample frequently to monitor progress and maintain flatness. Clean the sample thoroughly between each grit size.
4. Polishing
After grinding, the sample is polished to remove surface defects and produce a mirror-like finish. Polishing is done with progressively finer diamond abrasives and/or oxide suspensions, such as:
Abrasive | Size | Purpose |
---|---|---|
Diamond suspension | 9-6 micron | Rough polishing |
Diamond suspension | 3-1 micron | Intermediate polishing |
Aluminum oxide suspension | 0.05 micron | Final polishing |
Use appropriate polishing cloths and lubricants for each abrasive. Apply gentle pressure and keep the sample moving to avoid creating surface artifacts. Clean thoroughly between steps.
5. Etching or Coating (Optional)
Depending on the material and analysis, the polished sample may be etched or coated to reveal microstructural features. Common methods include:
- Chemical etching with acids, bases, or other reagents
- Electrochemical etching with applied voltage in a conductive solution
- Coating with thin films of carbon, gold, or other materials for SEM
Follow established protocols for the specific material and etchant/coating. Take appropriate safety precautions when handling hazardous chemicals.
6. Microscopic Examination
Finally, the prepared sample is examined under a microscope to analyze the microstructure and properties of interest. This may involve:
- Optical microscopy to image grain structure, phase distributions, etc.
- SEM to characterize fine-scale features, chemical composition, etc.
- Quantitative image analysis to measure grain size, porosity, etc.
Capture representative images and data from multiple fields of view. Use appropriate magnifications and imaging modes for the features of interest.
By carefully following this procedure, a high-quality micro-sectioned sample can be prepared for detailed microscopic analysis. Properly document each step and note any deviations or observations for future reference.
Challenges and Best Practices in Micro-Sectioning
While micro-sectioning is a powerful technique, it also presents several challenges that must be carefully managed to ensure reliable results. Some common issues include:
-
Induced artifacts: Improper sectioning, grinding, or polishing can create surface deformation, cracks, pitting, or other artifacts that obscure the true microstructure. Use gentle, controlled techniques and check samples frequently.
-
Contamination: Samples can be easily contaminated by debris, fluids, or residues from preparation. Maintain a clean work area, use fresh consumables, and thoroughly clean samples between steps.
-
Non-representative samples: If samples are not properly selected or oriented, they may not accurately represent the bulk material. Carefully plan the sectioning to capture the desired features and take multiple samples if needed.
-
Safety hazards: Micro-sectioning involves hazardous equipment and chemicals that can cause injuries or illness if mishandled. Wear appropriate personal protective equipment, read safety data sheets, and follow proper protocols.
To avoid these challenges and produce the best possible micro-sectioned samples, consider the following best practices:
- Start with a clear plan for the desired analysis and sample requirements
- Select appropriate equipment and supplies for the specific material and application
- Follow established protocols and manufacturer’s instructions for each step
- Maintain detailed documentation and labeling of samples throughout the process
- Check samples frequently during preparation to catch any issues early
- Validate results with multiple samples, imaging techniques, and/or operators
- Continuously improve the process based on feedback and quality control measures
By implementing these best practices and staying up to date with the latest techniques and standards, micro-sectioning can provide invaluable insights into the microscopic world of materials.
Frequently Asked Questions
What is the purpose of mounting samples for micro-sectioning?
Mounting serves several important functions in micro-sectioning:
- It provides a uniform, stable base to hold the sample during grinding and polishing
- It protects delicate or friable samples from cracking or crumbling during preparation
- It allows multiple small samples to be prepared together in a single mount
- It facilitates handling, labeling, and storage of prepared samples
Without proper mounting, it would be very difficult to create flat, polished surfaces on small, irregular samples. The mounting medium also provides a clear, contrasting background for imaging.
Can micro-sectioning be used on non-conductive materials?
Yes, micro-sectioning is commonly used on non-conductive materials such as ceramics, polymers, and composites. However, these materials may require additional preparation steps compared to conductive samples, such as:
- Using special abrasives and polishing media that are less likely to cause surface damage
- Applying conductive coatings (carbon, gold, etc.) to allow imaging in electron microscopes
- Adjusting grinding and polishing parameters (speed, pressure, time) to account for different material properties
In some cases, non-conductive materials may also be more prone to certain artifacts such as smearing, pullout, or charging effects during imaging. Proper sample preparation and imaging techniques are essential to overcome these challenges.
How long does micro-sectioning take?
The time required for micro-sectioning varies widely depending on several factors, such as:
- The size, hardness, and complexity of the sample material
- The desired surface finish and level of detail for analysis
- The specific preparation methods and equipment used
- The skill and experience of the operator
A simple, routine sample (e.g. a small metal coupon) may take less than an hour to fully prepare, while a complex or challenging sample (e.g. a composite with multiple phases) may take several hours or even days. In general, each step of the process (cutting, mounting, grinding, polishing) may take anywhere from a few minutes to an hour or more. Automated equipment and batch processing can help increase throughput for larger sample volumes.
What kind of features can be seen in micro-sectioned samples?
Micro-sectioned samples can reveal a wide range of microstructural features depending on the material and preparation methods, such as:
- Grain size, shape, and orientation in polycrystalline materials
- Phase distributions and morphologies in multi-phase materials
- Porosity, voids, and inclusions within the material
- Cracks, delaminations, and other defects
- Interfaces between different materials or phases
- Surface coatings, layers, and treatments
- Segregation, precipitation, and other chemical inhomogeneities
The specific features that can be observed depend on the resolution and contrast of the imaging technique used (optical microscopy, SEM, etc.), as well as any etching or staining treatments applied. With proper preparation and imaging, micro-sectioned samples can provide detailed insights into the structure and properties of materials at the microscopic scale.
How do I choose the right abrasives and polishing media for my sample?
Selecting the appropriate abrasives and polishing media is critical for achieving the desired surface finish and avoiding damage to the sample. The main factors to consider are:
- The hardness and fracture toughness of the sample material
- The desired surface roughness and level of detail for analysis
- The chemical compatibility of the sample with the abrasive/media
- The required preparation time and cost
In general, harder, more brittle materials require finer, less aggressive abrasives and gentler preparation methods to avoid fracture and surface damage. Softer, more ductile materials can tolerate coarser abrasives and higher preparation forces.
For most materials, a sequence of progressively finer abrasives is used, starting with coarse grinding (100-400 grit) and progressing to fine polishing (0.05 micron or less). The specific abrasive types (silicon carbide, diamond, alumina, etc.) and polishing surfaces (cloths, pads, films, etc.) are selected based on the sample material and desired finish.
Many equipment manufacturers and consumable suppliers provide detailed guides and recommendations for abrasive/media selection based on the sample material and application. Consulting with experts and conducting pilot studies can also help optimize the preparation process for specific materials and analyses.
In summary, micro-sectioning is a vital tool for unlocking the secrets of materials at the microscopic level. By carefully cutting, mounting, grinding, and polishing representative samples, researchers can reveal the intricate structures and properties that govern material behavior and performance. While micro-sectioning requires specialized equipment, skillful techniques, and attention to detail, the insights it provides are essential for advancing scientific understanding and solving real-world problems across a wide range of fields. As materials continue to evolve and push the boundaries of performance, micro-sectioning will undoubtedly remain an indispensable technique for exploring the frontiers of the microscopic world.
No responses yet