What is Metallization?
Metallization is the process of coating a non-metallic substrate with a thin layer of metal. This is done to impart specific properties to the substrate material, such as conductivity, reflectivity, abrasion resistance, corrosion resistance, and altered appearance. The metallization process involves depositing a thin film of metal onto the surface of another material, such as plastic, ceramic, glass, or even other metals.
Metallization is used in various industries for a wide range of applications. Some common examples include:
- Electronic components: Metallization is used to create conductive pathways on printed circuit boards (PCBs) and integrated circuits (ICs).
- Automotive parts: Metallized plastic parts are used for decorative and functional purposes, such as chrome-plated trim pieces and reflective headlight housings.
- Packaging: Metallized films are used for food packaging to provide a barrier against moisture, oxygen, and light.
- Aerospace components: Metallization is used to create thermal barriers and reflective coatings on satellite components and spacecraft.
Types of Metallization Processes
There are several methods used for metallization, each with its own advantages and limitations. The choice of the metallization process depends on factors such as the substrate material, desired metal coating, required adhesion, and production scale. Some of the most common metallization processes include:
Physical Vapor Deposition (PVD)
PVD is a vacuum deposition process where the metal is vaporized and then condensed onto the substrate surface. There are two main types of PVD:
-
Evaporation: In this process, the metal is heated until it evaporates, and the vapors are then deposited onto the substrate. This can be done using resistive heating, electron beam evaporation, or laser evaporation.
-
Sputtering: In this process, a high-energy plasma is used to bombard a metal target, causing atoms to be ejected and deposited onto the substrate. Sputtering can be done using direct current (DC), radio frequency (RF), or magnetron sputtering.
PVD is widely used in the electronics industry for creating thin, uniform metal coatings on various substrates. It offers excellent control over the coating thickness and can be used to deposit a wide range of metals, including aluminum, gold, silver, and titanium.
Chemical Vapor Deposition (CVD)
CVD is a process where a volatile metal compound (precursor) is introduced into a reaction chamber and then decomposed or reacted to form a metal coating on the substrate. The process involves the following steps:
- The precursor is vaporized and transported into the reaction chamber.
- The precursor reacts or decomposes on the heated substrate surface, forming a metal coating.
- Gaseous byproducts are removed from the chamber.
CVD can be used to deposit a wide range of metals and metal compounds, such as tungsten, titanium nitride, and silicon carbide. It offers excellent coating uniformity and can be used to coat complex-shaped parts. However, CVD requires high temperatures and can be more expensive than other metallization processes.
Electroplating
Electroplating is a process where a metal coating is deposited onto a substrate by passing an electric current through an electrolyte solution containing dissolved metal ions. The substrate to be coated serves as the cathode, while a metal electrode serves as the anode. When an electric current is applied, metal ions from the solution are reduced and deposited onto the cathode surface.
Electroplating is widely used for decorative and functional coatings, such as chrome plating, nickel plating, and gold plating. It offers good coating adhesion and can be used to deposit relatively thick coatings (up to several millimeters). However, electroplating requires a conductive substrate and can be limited by the shape and size of the parts that can be coated.
Electroless Plating
Electroless plating is a chemical reduction process where a metal coating is deposited onto a substrate without the use of an external electric current. The process involves immersing the substrate in a plating solution containing a metal salt, a reducing agent, and a catalyst. The reducing agent reacts with the metal ions in the solution, causing them to be reduced and deposited onto the substrate surface.
Electroless plating is commonly used for depositing nickel, copper, and gold coatings on various substrates, including plastics, ceramics, and other non-conductive materials. It offers excellent coating uniformity and can be used to coat complex-shaped parts. However, electroless plating can be more expensive than electroplating and may require careful control of the plating solution chemistry.
Factors Affecting the Metallization Process
Several factors can influence the quality and performance of the metallized coating, including:
Substrate Preparation
Proper substrate preparation is crucial for achieving good coating adhesion and uniformity. This typically involves cleaning the substrate surface to remove contaminants, such as oils, dirt, and oxides. Some common substrate preparation methods include:
- Solvent cleaning: Using organic solvents to dissolve and remove surface contaminants.
- Mechanical cleaning: Using abrasive methods, such as sanding or blasting, to remove surface layers and roughen the substrate.
- Chemical etching: Using acids or alkalis to chemically modify the substrate surface and improve coating adhesion.
Coating Thickness
The thickness of the metal coating can affect its properties, such as conductivity, reflectivity, and durability. Coating thickness can be controlled by adjusting process parameters, such as deposition rate, time, and temperature. In general, thicker coatings provide better protection and durability, but may also be more expensive and prone to cracking or delamination.
Coating Adhesion
Coating adhesion refers to the strength of the bond between the metal coating and the substrate. Poor adhesion can lead to coating delamination, peeling, or blistering. Factors that can affect coating adhesion include:
- Substrate surface roughness: A rougher surface can provide better mechanical interlocking and improve adhesion.
- Substrate cleanliness: Contaminants on the substrate surface can interfere with the bonding process and reduce adhesion.
- Coating-substrate compatibility: The chemical and physical properties of the coating and substrate should be compatible to ensure good adhesion.
Process Parameters
The specific process parameters used during metallization can significantly affect the quality and performance of the resulting coating. Some key process parameters include:
- Deposition rate: The rate at which the metal is deposited onto the substrate can affect the coating thickness, uniformity, and microstructure.
- Substrate temperature: Higher substrate temperatures can promote better coating adhesion and density, but may also cause substrate degradation or distortion.
- Chamber pressure: The pressure inside the deposition chamber can influence the coating density, stress, and contamination levels.
- Gas composition: The type and composition of the gases used in the process can affect the coating chemistry, microstructure, and stress levels.
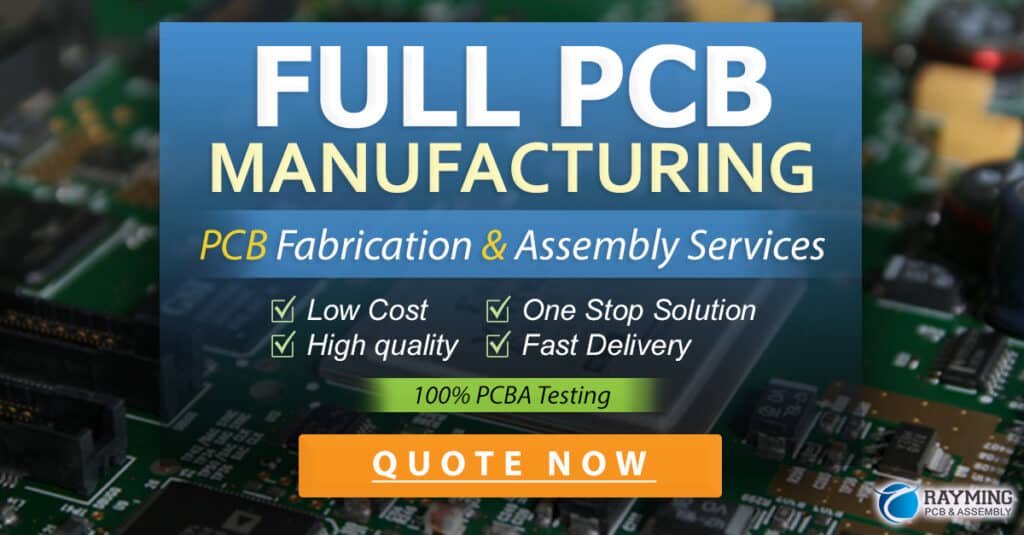
Characterization and Testing of Metallized Coatings
After metallization, it is important to characterize and test the resulting coating to ensure that it meets the desired specifications and performance requirements. Some common characterization and testing methods include:
Thickness Measurement
Coating thickness can be measured using various techniques, such as:
- Cross-sectional microscopy: Cutting a cross-section of the coated sample and measuring the thickness using an optical or electron microscope.
- X-ray fluorescence (XRF): Measuring the intensity of X-rays emitted by the coating when exposed to a primary X-ray source.
- Eddy current testing: Measuring changes in the electrical impedance of a probe coil when placed near the coated surface.
Adhesion Testing
Coating adhesion can be evaluated using various methods, such as:
- Tape test: Applying and removing a piece of adhesive tape from the coated surface and visually inspecting for coating removal.
- Scratch test: Drawing a stylus or needle across the coated surface under increasing load and measuring the critical load at which coating failure occurs.
- Pull-off test: Bonding a dolly or stud to the coated surface and measuring the force required to pull it off.
Surface Roughness Measurement
Surface roughness can be measured using techniques such as:
- Stylus profilometry: Drawing a diamond-tipped stylus across the surface and measuring the vertical displacement.
- Optical profilometry: Using interferometry or confocal microscopy to measure surface height variations.
- Atomic force microscopy (AFM): Using a sharp probe to scan the surface and measure topography at the nanoscale.
Electrical Resistance Measurement
For conductive coatings, electrical resistance can be measured using a four-point probe or a sheet resistance meter. This involves applying a known current through the coating and measuring the resulting voltage drop.
Corrosion Testing
Corrosion resistance of metallized coatings can be evaluated using various methods, such as:
- Salt spray testing: Exposing the coated sample to a salt spray environment and monitoring for corrosion or coating degradation.
- Electrochemical impedance spectroscopy (EIS): Measuring the impedance of the coating-substrate system when exposed to an electrolyte solution.
- Potentiodynamic polarization: Measuring the current-voltage response of the coated sample in an electrolyte solution to determine corrosion rates and coating breakdown potential.
Applications of Metallized Coatings
Metallized coatings find use in a wide range of industries and applications, some of which are highlighted below:
Electronics Industry
In the electronics industry, metallization is used for creating conductive pathways, contacts, and interconnects on semiconductor devices and printed circuit boards. Some common applications include:
- Integrated circuits: Metallization is used to create conductive lines and vias that connect different components on a chip.
- PCBs: Copper metallization is used to create conductive traces and pads on the board surface.
- SMD components: Metallization is used to create solderable contacts on surface-mount devices, such as resistors and capacitors.
Automotive Industry
Metallized coatings are used in the automotive industry for both decorative and functional purposes. Some examples include:
- Chrome-plated trim: Electroplated chrome is used for decorative trim pieces, such as grilles, bumpers, and wheel covers.
- Reflective coatings: Metallized coatings are used on headlights and taillights to provide reflectivity and improve visibility.
- Corrosion protection: Metallized coatings, such as zinc and nickel, are used to protect steel parts from corrosion.
Aerospace Industry
In the aerospace industry, metallized coatings are used for thermal management, radiation shielding, and surface protection. Some applications include:
- Thermal control coatings: Metallized coatings, such as gold and silver, are used on satellite components to reflect solar radiation and maintain temperature stability.
- EMI shielding: Metallized coatings are used to shield electronic components from electromagnetic interference.
- Erosion protection: Metallized coatings, such as titanium nitride, are used to protect components from erosion caused by high-speed airflow or particle impact.
Packaging Industry
Metallized films and foils are widely used in the packaging industry for food and pharmaceutical products. Some benefits include:
- Barrier properties: Metallized films provide a barrier against moisture, oxygen, and light, extending product shelf life.
- Aesthetics: Metallized films can provide a glossy, metallic appearance that enhances product visibility and appeal.
- Cost-effectiveness: Metallized films are often less expensive than traditional metal foils while providing similar barrier properties.
Challenges and Future Trends in Metallization
Despite the wide-ranging applications and benefits of metallization, there are still some challenges and opportunities for further development. Some of these include:
Environmental Concerns
Many metallization processes involve the use of hazardous chemicals and generate waste products that can be harmful to the environment. There is a growing need for more sustainable and eco-friendly metallization methods, such as using non-toxic precursors and reducing energy consumption.
Miniaturization and High-Aspect-Ratio Coatings
As electronic devices continue to shrink in size, there is a need for metallization processes that can create ultra-thin, conformal coatings on high-aspect-ratio structures. This requires the development of advanced deposition techniques, such as atomic layer deposition (ALD) and focused ion beam (FIB) deposition.
Multifunctional Coatings
There is a growing interest in developing multifunctional metallized coatings that can provide multiple benefits, such as corrosion protection, wear resistance, and self-cleaning properties. This can be achieved through the use of nanocomposite coatings, gradient coatings, and surface functionalization techniques.
Additive Manufacturing
Additive manufacturing, or 3D printing, is a rapidly growing field that enables the creation of complex, customized parts. Metallization can be used in conjunction with additive manufacturing to create functional, metal-coated parts. This requires the development of new materials and processes that are compatible with additive manufacturing techniques.
FAQ
1. What is the difference between PVD and CVD metallization?
PVD (Physical Vapor Deposition) and CVD (Chemical Vapor Deposition) are both methods used for depositing thin metal films onto a substrate. The main differences are:
- PVD involves the physical vaporization and condensation of a metal onto the substrate, while CVD involves the chemical reaction or decomposition of a metal-containing precursor gas.
- PVD is typically done at lower temperatures than CVD, making it more suitable for temperature-sensitive substrates.
- CVD can provide better coating conformality and uniformity on complex-shaped parts than PVD.
- PVD is often faster and less expensive than CVD for depositing simple metal coatings.
2. Can metallization be used on plastic parts?
Yes, metallization can be used to coat plastic parts for various purposes, such as decorative finishes, EMI shielding, and barrier protection. However, the choice of the metallization process and pre-treatment methods depends on the specific plastic material and the desired coating properties. For example:
- ABS and PC/ABS plastics can be electroplated with copper or nickel after a suitable etching and activation process.
- PET and PBT plastics can be metallized using sputtering or evaporation after a plasma or UV treatment to improve coating adhesion.
- PTFE and other fluoropolymers require specialized surface modification techniques, such as sodium naphthalenide etching, before metallization.
3. How does surface roughness affect the metallization process?
Surface roughness can have both positive and negative effects on the metallization process, depending on the specific application and coating requirements. Some effects of surface roughness include:
- Increased surface area: A rougher surface has a higher surface area, which can improve coating adhesion by providing more anchor points for mechanical interlocking. However, it can also lead to higher coating thickness variations and reduced electrical conductivity.
- Shadowing effects: In line-of-sight deposition processes, such as evaporation and sputtering, a rougher surface can cause shadowing effects, where some areas receive less coating than others. This can lead to coating non-uniformity and defects.
- Increased stress: A rougher surface can cause higher residual stress in the coating, which can lead to cracking, delamination, or poor adhesion.
In general, a moderate level of surface roughness (e.g., Ra = 0.1-1 μm) is desirable for most metallization applications, as it provides a good balance between adhesion and coating quality. The optimal surface roughness depends on factors such as the substrate material, coating thickness, and performance requirements.
4. What are some common defects in metallized coatings?
Some common defects that can occur in metallized coatings include:
- Pinholes: Small holes or voids in the coating that can expose the substrate and lead to corrosion or performance issues.
- Blisters: Localized areas where the coating separates from the substrate, often due to poor adhesion or contamination.
- Cracks: Fractures in the coating that can occur due to excessive stress, thermal mismatch, or mechanical damage.
- Peeling: Separation of the coating from the substrate along the interface, often due to poor surface preparation or incompatible materials.
- Nodules: Small, raised bumps on the coating surface that can occur due to contaminants, gas bubbles, or uneven deposition.
- Discoloration: Changes in the coating color or appearance due to oxidation, contamination, or exposure to heat or light.
These defects can be minimized through proper process control, substrate preparation, and post-deposition treatment. Regular inspection and testing can help identify and correct defects before they cause significant performance issues.
5. How can the corrosion resistance of metallized coatings be improved?
The corrosion resistance of metallized coatings can be improved through various methods, such as:
- Choosing the right coating material: Some metals, such as gold, platinum, and titanium, have inherently high corrosion resistance due to their noble character and stable oxide layers. Other metals, such as zinc and cadmium, can provide sacrificial protection to the substrate.
- Increasing the coating thickness: Thicker coatings generally provide better barrier protection against corrosive species. However, excessively thick coatings can also lead to higher stress and reduced adhesion.
- Applying multi-layer coatings: Combining
No responses yet