What Are Medical PCBs?
Medical PCBs are printed circuit boards designed and manufactured specifically for use in medical devices and equipment. These PCBs must meet stringent quality and reliability standards to ensure the safety and effectiveness of the medical devices they power. Medical PCBs are used in a wide range of applications, including:
- Diagnostic imaging equipment (X-ray, MRI, CT scanners)
- Patient monitoring systems
- Surgical instruments
- Implantable devices (pacemakers, neurostimulators)
- Medical wearables
- Lab automation equipment
Key Characteristics of Medical PCBs
Medical PCBs have unique characteristics that set them apart from standard PCBs used in other industries. These characteristics include:
- High reliability: Medical PCBs must function flawlessly to ensure patient safety and accurate diagnoses.
- Strict quality control: Manufacturers must adhere to rigorous quality control processes to meet regulatory requirements.
- Miniaturization: Many medical devices require compact and lightweight PCBs to fit within small form factors.
- Biocompatibility: PCBs used in implantable devices must be made from biocompatible materials to prevent adverse reactions.
- Long product lifecycles: Medical devices often have longer lifecycles than consumer electronics, requiring PCBs with extended durability and availability.
The Role of Medical PCB Manufacturers
Medical PCB manufacturers are responsible for designing, fabricating, and assembling PCBs that meet the specific requirements of medical devices. Their primary goals are to ensure the quality, reliability, and compliance of the PCBs they produce.
Design and Engineering Support
Many medical PCB manufacturers offer design and engineering support to help clients develop PCBs that meet their specific needs. This support may include:
- Schematic and layout design assistance
- Component selection and optimization
- Signal integrity analysis
- Thermal management solutions
- Prototype development and testing
PCB Fabrication
Once the PCB design is finalized, medical PCB manufacturers begin the fabrication process. This involves creating the bare PCB using a combination of processes, such as:
- Material selection (e.g., FR-4, polyimide, ceramic)
- Copper cladding
- Photolithography
- Etching
- Drilling
- Plating
- Solder mask and silkscreen application
Medical PCB manufacturers must maintain strict control over the fabrication process to ensure consistency and quality.
PCB Assembly
After fabrication, the bare PCBs are populated with electronic components through the assembly process. Medical PCB manufacturers typically offer both through-hole and surface-mount assembly services. The assembly process includes:
- Solder paste application
- Component placement
- Reflow soldering
- Wave soldering (for through-hole components)
- Inspection and testing
Quality Control and Testing
To ensure the reliability and safety of medical PCBs, manufacturers employ rigorous quality control and testing procedures. These may include:
- Automated optical inspection (AOI)
- X-ray inspection
- In-circuit testing (ICT)
- Functional testing
- Environmental testing (e.g., temperature, humidity, vibration)
- Burn-in testing
Medical PCB manufacturers must also maintain detailed documentation and traceability records to comply with regulatory requirements.
Challenges Faced by Medical PCB Manufacturers
Medical PCB manufacturers face several unique challenges due to the stringent requirements and regulations governing the medical device industry.
Regulatory Compliance
Medical PCB manufacturers must comply with various regulations and standards to ensure the safety and effectiveness of their products. Some of the key regulations include:
- FDA 21 CFR Part 820 (Quality System Regulation)
- ISO 13485 (Medical devices – Quality management systems)
- IEC 60601-1 (Medical electrical equipment – General requirements for basic safety and essential performance)
- RoHS (Restriction of Hazardous Substances)
Compliance with these regulations requires extensive documentation, process validation, and ongoing monitoring.
Supply Chain Management
Medical PCB manufacturers must manage a complex supply chain to ensure the availability and quality of components used in their products. This can be challenging due to:
- Long lead times for specialized components
- Obsolescence risk for older components
- Counterfeit part prevention
- Traceability requirements
Effective supply chain management is crucial for meeting production deadlines and maintaining product quality.
Rapid Technological Advancements
The medical device industry is constantly evolving, with new technologies and treatments emerging at a rapid pace. Medical PCB manufacturers must stay up-to-date with these advancements to remain competitive and meet changing customer needs. This may require investments in new equipment, materials, and employee training.
Cost Pressures
While medical devices command higher prices than consumer electronics, medical PCB manufacturers still face pressure to control costs and remain competitive. This can be challenging given the additional expenses associated with regulatory compliance, quality control, and specialized materials.
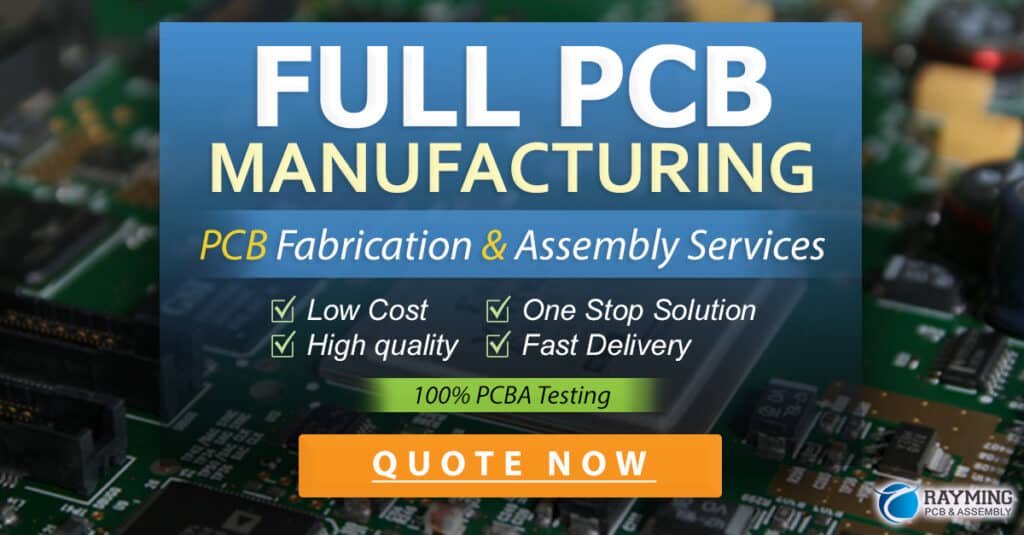
Selecting the Best Medical PCB Manufacturer
Choosing the right medical PCB manufacturer is crucial for the success of your medical device project. Consider the following factors when evaluating potential partners:
Certifications and Compliance
Ensure that the manufacturer holds the necessary certifications and complies with relevant regulations, such as ISO 13485 and FDA 21 CFR Part 820. Request documentation to verify their compliance status.
Experience and Expertise
Look for a manufacturer with extensive experience in producing PCBs for medical devices similar to yours. They should have a deep understanding of the unique requirements and challenges associated with medical PCBs.
Quality Management System
Evaluate the manufacturer’s quality management system (QMS) to ensure that they have robust processes in place for quality control, document control, and continuous improvement. A strong QMS is essential for consistently producing high-quality PCBs.
Technical Capabilities
Consider the manufacturer’s technical capabilities, including their design and engineering support, fabrication and assembly processes, and testing and inspection equipment. They should have the necessary expertise and infrastructure to meet your specific requirements.
Flexibility and Scalability
Choose a manufacturer that can accommodate your production needs, whether you require small prototype runs or large-scale production. They should also be flexible enough to adapt to changes in your design or production schedule.
Communication and Customer Support
Effective communication is key to a successful partnership. Look for a manufacturer that is responsive, transparent, and proactive in their communication. They should also offer reliable customer support to address any issues or concerns that may arise.
Cost and Lead Time
While cost should not be the sole deciding factor, it is essential to consider the manufacturer’s pricing and lead times. Look for a partner that offers competitive pricing without compromising on quality or service. They should also be able to meet your delivery requirements and provide reliable lead time estimates.
Frequently Asked Questions (FAQ)
-
Q: What is the difference between a medical PCB and a standard PCB?
A: Medical PCBs are designed and manufactured to meet the strict quality, reliability, and regulatory requirements of the medical device industry. They often require specialized materials, processes, and testing to ensure patient safety and device performance. -
Q: How long does it typically take to manufacture a medical PCB?
A: The lead time for manufacturing a medical PCB can vary depending on the complexity of the design, the materials used, and the production volume. Prototype runs may take a few weeks, while large-scale production can take several months. It’s essential to discuss lead times with your manufacturer early in the project. -
Q: What certifications should I look for in a medical PCB manufacturer?
A: Key certifications to look for include ISO 13485 (quality management systems for medical devices), FDA 21 CFR Part 820 (quality system regulation), and IPC standards for PCB fabrication and assembly. Additional certifications may be required depending on the specific application and market. -
Q: Can medical PCB manufacturers assist with the design process?
A: Yes, many medical PCB manufacturers offer design and engineering support services to help clients develop PCBs that meet their specific requirements. This can include assistance with schematic and layout design, component selection, signal integrity analysis, and prototype development. -
Q: How can I ensure the security of my intellectual property when working with a medical PCB manufacturer?
A: To protect your intellectual property, choose a manufacturer with a strong track record of integrity and confidentiality. Request a non-disclosure agreement (NDA) before sharing sensitive information, and ensure that the manufacturer has secure data storage and transfer practices in place.
Conclusion
Medical PCB manufacturers play a vital role in the development and production of medical devices. By understanding their functions, challenges, and the key factors to consider when selecting a manufacturer, you can make an informed decision and find the best partner for your medical device project. Remember to prioritize quality, reliability, and compliance, as these are essential for ensuring patient safety and device performance.
When evaluating potential medical PCB manufacturers, consider their certifications, experience, technical capabilities, quality management systems, flexibility, communication, and cost. By choosing the right partner and fostering a strong, collaborative relationship, you can bring your medical device to market with confidence, knowing that your PCBs are of the highest quality and reliability.
No responses yet