Introduction to Medical Device Manufacturing
The medical device manufacturing industry is a crucial sector that produces a wide range of products, from simple disposable items to complex life-supporting equipment. These devices play a vital role in diagnosing, treating, and preventing various medical conditions, ultimately improving patient outcomes and quality of life. In this article, we will explore four essential processes and components involved in medical device manufacturing: design and development, material selection, manufacturing techniques, and quality control and regulations.
Design and Development
Conceptualization and Ideation
The first step in medical device manufacturing is the conceptualization and ideation phase. This involves identifying a medical need or problem and brainstorming potential solutions. Ideas can come from various sources, such as healthcare professionals, patients, researchers, or engineers. Once an idea is generated, it undergoes a feasibility assessment to determine its viability and potential impact on patient care.
Prototyping and Testing
After the initial concept is developed, the next step is to create a prototype. Prototypes are early versions of the device that allow manufacturers to test and refine the design before moving into full-scale production. Prototypes can be created using various methods, such as 3D printing, CNC machining, or injection molding, depending on the complexity and material requirements of the device.
Once a prototype is created, it undergoes rigorous testing to evaluate its performance, safety, and efficacy. This may include bench testing, animal studies, and eventually, human clinical trials. The testing phase is crucial to identify any potential issues or areas for improvement before the device is submitted for regulatory approval.
Design Optimization and Finalization
Based on the feedback and data collected during the testing phase, the device design is optimized and finalized. This may involve making changes to the device’s shape, size, materials, or functionality to improve its performance and safety. The final design is then documented in detail, including specifications, drawings, and instructions for use, which will be used throughout the manufacturing process and submitted to regulatory bodies for approval.
Material Selection
Biocompatibility and Safety
One of the most critical aspects of medical device manufacturing is material selection. The materials used in medical devices must be biocompatible, meaning they do not cause any adverse reactions or harm to the human body. Biocompatibility is essential to ensure patient safety and prevent complications such as allergic reactions, infections, or toxicity.
The biocompatibility of materials is evaluated through various tests, such as cytotoxicity, sensitization, irritation, and systemic toxicity, as outlined in the ISO 10993 series of standards. These tests assess the material’s interaction with biological systems and help determine its suitability for use in medical devices.
Material Properties and Functionality
In addition to biocompatibility, the materials used in medical devices must also possess the necessary properties and functionality to perform their intended purpose. This may include mechanical properties such as strength, durability, and flexibility, as well as chemical properties such as resistance to corrosion or degradation.
The choice of materials depends on the specific application and requirements of the device. For example, implantable devices may require materials that are resistant to wear and tear, while disposable devices may prioritize cost-effectiveness and ease of manufacturing. Common materials used in medical devices include:
- Metals (e.g., titanium, stainless steel)
- Polymers (e.g., silicone, polyurethane)
- Ceramics (e.g., alumina, zirconia)
- Composites (e.g., carbon fiber reinforced polymers)
Material Sourcing and Quality Control
To ensure the quality and consistency of medical devices, manufacturers must carefully source their materials from reliable suppliers. This involves establishing a robust supply chain management system that includes vendor qualification, material specification, and incoming inspection processes.
Manufacturers must also implement strict quality control measures to verify that the materials meet the required specifications and are free from defects or contamination. This may involve techniques such as visual inspection, dimensional analysis, and material testing (e.g., tensile strength, hardness, chemical composition).
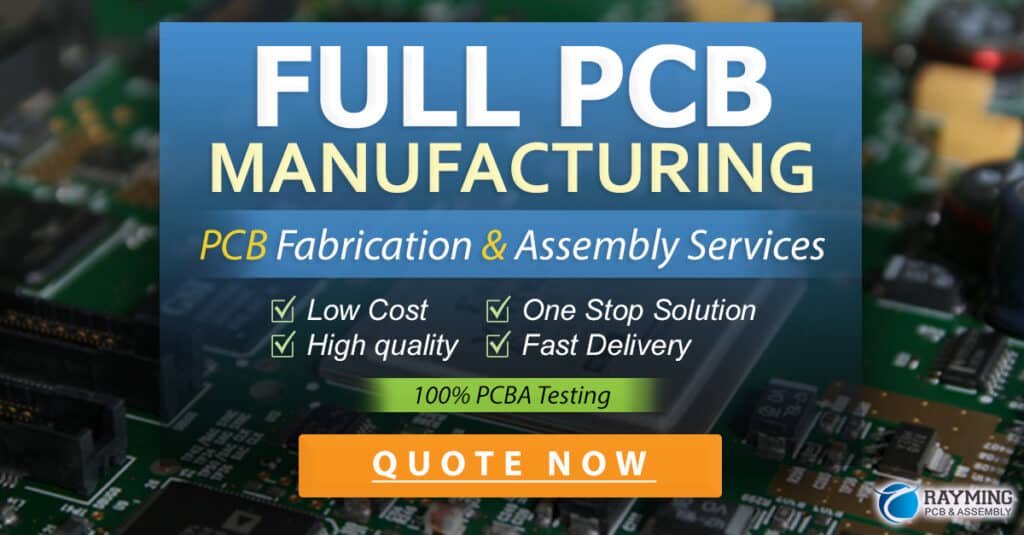
Manufacturing Techniques
Injection Molding
Injection molding is a common manufacturing technique used for producing high volumes of plastic components for medical devices. In this process, molten plastic is injected into a mold cavity under high pressure, where it cools and solidifies into the desired shape. Injection molding is suitable for producing complex geometries with tight tolerances and can be used with a wide range of polymers, including biocompatible materials such as polypropylene, polyethylene, and polycarbonate.
Extrusion
Extrusion is another manufacturing technique used for producing continuous profiles or tubing for medical devices. In this process, raw material (usually a polymer) is melted and forced through a die of the desired cross-section. The extruded profile is then cooled and solidified, and can be cut to the required length. Extrusion is commonly used for producing catheters, tubing, and other elongated components.
CNC Machining
CNC (Computer Numerical Control) machining is a subtractive manufacturing technique that involves using computer-controlled machines to remove material from a solid block or blank to create the desired shape. CNC machining is suitable for producing high-precision components with complex geometries, and can be used with a wide range of materials, including metals, polymers, and ceramics. This technique is often used for producing surgical instruments, implants, and other critical components.
3D Printing
3D printing, also known as additive manufacturing, is a rapidly growing technology in the medical device industry. This technique involves building up a component layer by layer using a digital model, allowing for the creation of complex geometries and customized devices. 3D printing is particularly useful for producing patient-specific implants, surgical guides, and anatomical models. Various 3D printing technologies are available, such as fused deposition modeling (FDM), stereolithography (SLA), and selective laser sintering (SLS), each with its own advantages and limitations.
Manufacturing Technique | Advantages | Disadvantages |
---|---|---|
Injection Molding | – High volume production – Complex geometries – Wide range of materials |
– High initial tooling costs – Limited design flexibility |
Extrusion | – Continuous profiles – Suitable for tubing and catheters |
– Limited cross-sectional complexity – Material limitations |
CNC Machining | – High precision – Complex geometries – Wide range of materials |
– Slower than other techniques – Material waste |
3D Printing | – Complex geometries – Customization – Rapid prototyping |
– Limited material options – Lower precision than CNC machining |
Quality Control and Regulations
Quality Management Systems
Quality control is a critical aspect of medical device manufacturing to ensure that devices are safe, effective, and meet the required specifications. Manufacturers must implement a robust quality management system (QMS) that complies with the relevant standards and regulations, such as ISO 13485 and FDA 21 CFR Part 820.
A QMS encompasses various processes and procedures, including:
- Design controls
- Document and record management
- Supplier management
- Production and process controls
- Inspection and testing
- Nonconformance and corrective action
- Post-market surveillance
By implementing a comprehensive QMS, manufacturers can consistently produce high-quality devices, minimize the risk of defects or failures, and ensure compliance with regulatory requirements.
Regulatory Compliance
Medical devices are heavily regulated to ensure patient safety and efficacy. Manufacturers must comply with the regulations set by the relevant authorities in the markets where they intend to sell their devices. In the United States, the Food and Drug Administration (FDA) is responsible for regulating medical devices, while in the European Union, devices must conform to the Medical Device Regulation (MDR).
The regulatory process typically involves the following steps:
- Classification of the device based on its risk level (e.g., Class I, II, or III in the US)
- Preparation of a regulatory submission, including technical documentation and clinical evidence
- Submission to the relevant regulatory authority for review and approval
- Post-market surveillance and reporting of adverse events
Manufacturers must also comply with additional requirements, such as labeling, packaging, and storage, to ensure that devices are used safely and effectively by healthcare professionals and patients.
Frequently Asked Questions (FAQ)
1. What is the difference between a medical device and a pharmaceutical product?
Medical devices are physical items that are used to diagnose, treat, or prevent medical conditions, while pharmaceutical products are drugs or medications that are administered to patients for therapeutic purposes. Medical devices may be used in conjunction with pharmaceuticals, but they have distinct regulatory pathways and manufacturing processes.
2. How long does it take to bring a new medical device to market?
The time required to bring a new medical device to market can vary significantly depending on the complexity of the device, the regulatory requirements, and the development and testing process. On average, it can take anywhere from 3 to 7 years from initial concept to market launch, with some complex devices taking even longer.
3. What are the most common materials used in medical devices?
The most common materials used in medical devices include:
- Metals: titanium, stainless steel, cobalt-chrome alloys
- Polymers: silicone, polyurethane, polyethylene, polypropylene
- Ceramics: alumina, zirconia, hydroxyapatite
- Composites: carbon fiber reinforced polymers, metal-matrix composites
The choice of material depends on the specific application, biocompatibility requirements, and desired properties of the device.
4. What is the role of risk management in medical device manufacturing?
Risk management is a critical aspect of medical device manufacturing that involves identifying, analyzing, and mitigating potential risks associated with the device. This includes risks related to design, manufacturing, use, and disposal of the device. Manufacturers must conduct a thorough risk assessment and implement appropriate controls to minimize the risk of harm to patients and users. Risk management is an ongoing process throughout the device lifecycle and is a key component of a quality management system.
5. How do manufacturers ensure the sterility of medical devices?
Sterility is a critical requirement for many medical devices, particularly those that come into contact with the patient’s body or are used in surgical procedures. Manufacturers ensure the sterility of devices through various methods, including:
- Sterilization processes: such as steam sterilization, ethylene oxide (EtO) sterilization, or radiation sterilization
- Aseptic processing: manufacturing devices in a controlled, sterile environment
- Packaging: using sterile barrier packaging to maintain sterility until use
Manufacturers must validate their sterilization processes and conduct regular monitoring and testing to ensure that devices meet the required sterility assurance level (SAL).
Conclusion
Medical device manufacturing is a complex and highly regulated industry that plays a crucial role in improving patient outcomes and quality of life. The four key processes and components discussed in this article – design and development, material selection, manufacturing techniques, and quality control and regulations – are essential for producing safe, effective, and high-quality medical devices.
As the demand for innovative and personalized medical devices continues to grow, manufacturers must stay up-to-date with the latest technologies, materials, and regulatory requirements. By adopting a patient-centric approach and prioritizing quality and safety throughout the manufacturing process, medical device companies can continue to drive advancements in healthcare and make a positive impact on patients’ lives.
No responses yet