Introduction to Thermocouple Converters
A thermocouple is a widely used temperature sensing device that consists of two dissimilar metals joined together at one end, creating a junction. When the junction is exposed to a temperature gradient, it generates a small voltage that is proportional to the temperature difference between the junction and the reference point (usually the cold junction). However, this voltage is typically very small and requires amplification and conversion to a digital format for accurate temperature measurement. This is where thermocouple converters, such as the MAX31856, come into play.
What is a Thermocouple Converter?
A thermocouple converter is an electronic device that converts the small analog voltage generated by a thermocouple into a digital signal that can be easily read and processed by a microcontroller or other digital systems. These converters often include features such as cold-junction compensation, linearization, and noise filtering to ensure accurate and stable temperature measurements.
Importance of Thermocouple Converters
Thermocouple converters play a crucial role in various applications where precise temperature monitoring is essential, such as:
- Industrial process control
- HVAC systems
- Automotive engineering
- Medical equipment
- Scientific research
By providing a reliable and efficient means of converting thermocouple signals into digital data, these converters enable accurate temperature measurements and control in diverse settings.
MAX31856: A High-Performance Thermocouple Converter
The MAX31856 is a high-precision thermocouple-to-digital converter designed by Maxim Integrated. It offers a complete solution for thermocouple temperature measurement, combining cold-junction compensation, linearization, and high-resolution analog-to-digital conversion in a single chip.
Key Features of the MAX31856
-
Supports multiple thermocouple types: The MAX31856 is compatible with a wide range of thermocouple types, including K, J, N, R, S, T, E, and B, making it versatile for various applications.
-
High-resolution ADC: With a 19-bit ADC, the MAX31856 provides a resolution of 0.0078°C (14 bits) for temperatures ranging from -210°C to +1800°C, ensuring highly accurate temperature measurements.
-
Cold-junction compensation: The converter includes an internal temperature sensor for cold-junction compensation, eliminating the need for an external sensor and simplifying the design process.
-
Linearization: The MAX31856 automatically linearizes the thermocouple output, reducing the computational burden on the host microcontroller and improving overall system performance.
-
Fault detection: The converter offers open-circuit and short-circuit fault detection, enhancing system reliability and safety.
-
SPI compatible: The MAX31856 communicates with the host microcontroller using a simple SPI interface, making it easy to integrate into various embedded systems.
Thermocouple Types and Temperature Ranges
The MAX31856 supports the following thermocouple types and their corresponding temperature ranges:
Thermocouple Type | Temperature Range (°C) |
---|---|
K | -270 to +1372 |
J | -210 to +1200 |
N | -270 to +1300 |
R | -50 to +1768 |
S | -50 to +1768 |
T | -270 to +400 |
E | -270 to +1000 |
B | +250 to +1820 |
Block Diagram and Pin Description
Here is a simplified block diagram of the MAX31856:
+-------+
| |
Thermocouple---+ |
| | |
| | MAX31856
| | |
| | |
| | |
| | |
| | |
| | |
| | |
| | |
+---+---+
|
|
|
|
|
|
|
SPI Interface
The MAX31856 has the following pin configuration:
Pin | Name | Description |
---|---|---|
1 | GND | Ground |
2 | VCC | Supply voltage (3.0V to 3.6V) |
3 | T- | Thermocouple negative input |
4 | T+ | Thermocouple positive input |
5 | DNC | Do not connect |
6 | DRDY | Data ready output (active low) |
7 | CS | Chip select input (active low) |
8 | SDI | Serial data input |
9 | SDO | Serial data output |
10 | SCK | Serial clock input |
11 | FAULT | Fault output (active low) |
12 | DNC | Do not connect |
13 | DNC | Do not connect |
14 | DNC | Do not connect |
Interfacing the MAX31856 with a Microcontroller
To use the MAX31856 in an embedded system, you need to interface it with a microcontroller using the SPI protocol. Here’s a step-by-step guide on how to set up the communication between the MAX31856 and a microcontroller:
- Hardware Connections:
- Connect the VCC pin to a 3.3V power supply.
- Connect the GND pin to the ground of the system.
- Connect the T+ and T- pins to the thermocouple leads.
- Connect the CS, SDI, SDO, and SCK pins to the corresponding SPI pins on the microcontroller.
-
Optional: Connect the DRDY and FAULT pins to GPIO pins on the microcontroller for additional functionality.
-
SPI Configuration:
-
Set up the SPI peripheral on the microcontroller with the following parameters:
- Mode: 1 (CPOL = 0, CPHA = 1)
- Bit order: MSB first
- Clock frequency: Up to 5 MHz
- Data size: 8 bits
-
Initialization:
- Pull the CS pin high to deselect the MAX31856.
- Send the configuration register write command (0x80) followed by the desired configuration value to set up the thermocouple type, averaging mode, and other parameters.
-
Pull the CS pin low to select the MAX31856 for communication.
-
Temperature Reading:
- Send the temperature register read command (0x00) to retrieve the temperature data.
- Read 4 bytes of data from the SDO pin, which represent the 19-bit signed temperature value and the fault status.
-
Convert the received data into a temperature value according to the selected thermocouple type and the MAX31856’s data format.
-
Fault Handling:
- Check the fault status byte for any thermocouple faults (open circuit, short to ground, or short to VCC).
- Take appropriate actions based on the fault status, such as triggering an alarm or initiating a safety shutdown.
Example Code (Arduino)
Here’s an example Arduino sketch that demonstrates how to interface the MAX31856 with an Arduino board and read the temperature:
#include <SPI.h>
const int CS_PIN = 10;
const int DRDY_PIN = 9;
const int FAULT_PIN = 8;
void setup() {
Serial.begin(9600);
SPI.begin();
pinMode(CS_PIN, OUTPUT);
pinMode(DRDY_PIN, INPUT);
pinMode(FAULT_PIN, INPUT);
// Initialize the MAX31856
digitalWrite(CS_PIN, HIGH);
SPI.beginTransaction(SPISettings(5000000, MSBFIRST, SPI_MODE1));
digitalWrite(CS_PIN, LOW);
SPI.transfer(0x80); // Configuration register write command
SPI.transfer(0x03); // Thermocouple type K, averaging enabled
digitalWrite(CS_PIN, HIGH);
SPI.endTransaction();
}
void loop() {
if (digitalRead(DRDY_PIN) == LOW) {
SPI.beginTransaction(SPISettings(5000000, MSBFIRST, SPI_MODE1));
digitalWrite(CS_PIN, LOW);
SPI.transfer(0x00); // Temperature register read command
uint8_t data[4];
for (int i = 0; i < 4; i++) {
data[i] = SPI.transfer(0x00);
}
digitalWrite(CS_PIN, HIGH);
SPI.endTransaction();
int16_t temperature = (data[0] << 8) | data[1];
float temp_celsius = temperature * 0.0078125;
Serial.print("Temperature: ");
Serial.print(temp_celsius);
Serial.println(" °C");
if (digitalRead(FAULT_PIN) == LOW) {
Serial.println("Thermocouple fault detected!");
}
}
delay(500);
}
This example sketch assumes that the MAX31856 is connected to the Arduino’s SPI pins (MOSI, MISO, and SCK) and that the CS, DRDY, and FAULT pins are connected to digital pins 10, 9, and 8, respectively. The sketch initializes the MAX31856 for thermocouple type K and enables averaging. In the main loop, it checks the DRDY pin to determine if new temperature data is available, reads the data using the SPI interface, converts it to a temperature value in degrees Celsius, and prints the result to the serial monitor. It also checks the FAULT pin to detect any thermocouple faults and prints a warning message if a fault is detected.
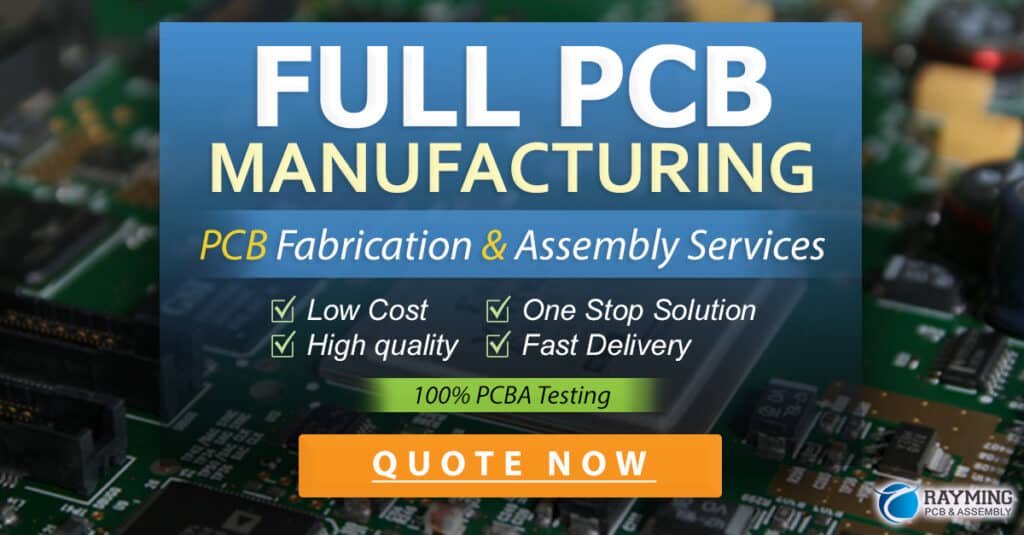
Advanced Features of the MAX31856
In addition to its core functionalities, the MAX31856 offers several advanced features that enhance its performance and usability:
Averaging
The MAX31856 provides an averaging function that helps to reduce noise and improve the stability of temperature measurements. This feature is particularly useful in environments with high levels of electromagnetic interference (EMI) or when measuring temperatures that fluctuate rapidly. The converter supports four averaging modes:
- 1 sample (no averaging)
- 2 samples
- 4 samples
- 8 samples
By enabling averaging, the MAX31856 automatically takes multiple temperature readings and calculates the average value, resulting in a more stable and accurate measurement.
Fault Detection
The MAX31856 includes built-in fault detection capabilities that help to ensure the integrity of the thermocouple and the temperature measurement system. The converter can detect the following fault conditions:
- Open circuit: Indicates a broken or disconnected thermocouple.
- Short to ground: Indicates a short circuit between the thermocouple leads and ground.
- Short to VCC: Indicates a short circuit between the thermocouple leads and the power supply voltage.
When a fault is detected, the MAX31856 sets the corresponding bits in the fault status register and pulls the FAULT pin low, alerting the host microcontroller to take appropriate action, such as triggering an alarm or initiating a safety shutdown procedure.
Cold-Junction Compensation
Cold-junction compensation (CJC) is a crucial feature in thermocouple temperature measurement systems. The MAX31856 includes an internal temperature sensor that measures the temperature at the cold junction (the point where the thermocouple connects to the converter). By combining the cold-junction temperature with the thermocouple voltage, the MAX31856 can accurately calculate the temperature at the thermocouple tip, compensating for any temperature differences between the cold junction and the reference point.
The MAX31856’s internal CJC sensor has a resolution of 0.0625°C and an accuracy of ±1°C (typical) from -20°C to +85°C, ensuring reliable cold-junction compensation across a wide temperature range.
Linearization
Thermocouples exhibit a non-linear relationship between voltage and temperature, which can lead to measurement errors if not properly compensated. The MAX31856 implements a linearization algorithm that automatically corrects for the non-linearity of the thermocouple, providing a more accurate temperature reading.
The linearization algorithm is based on the National Institute of Standards and Technology (NIST) ITS-90 thermocouple tables, which define the voltage-to-temperature conversion curves for various thermocouple types. By using these tables, the MAX31856 can accurately convert the thermocouple voltage to a temperature value, eliminating the need for the host microcontroller to perform complex linearization calculations.
Applications of the MAX31856
The MAX31856’s high-precision temperature measurement capabilities, combined with its advanced features and ease of use, make it suitable for a wide range of applications across various industries:
-
Industrial Process Control: In manufacturing and process control applications, accurate temperature monitoring is essential for maintaining product quality and ensuring safe operation. The MAX31856 can be used to measure temperatures in ovens, furnaces, reactors, and other industrial equipment, providing reliable data for process control and optimization.
-
HVAC Systems: Heating, ventilation, and air conditioning (HVAC) systems rely on accurate temperature measurements to maintain comfortable indoor environments and optimize energy efficiency. The MAX31856 can be integrated into HVAC control systems to monitor temperatures in ducts, heat exchangers, and other critical components, enabling precise control and fault detection.
-
Automotive Engineering: Temperature monitoring is crucial in various automotive applications, such as engine management, exhaust gas temperature sensing, and cabin climate control. The MAX31856’s wide temperature range and support for multiple thermocouple types make it suitable for measuring temperatures in harsh automotive environments, contributing to improved engine performance, emissions control, and passenger comfort.
-
Medical Equipment: Medical devices and equipment often require precise temperature monitoring to ensure patient safety and maintain the integrity of biological samples. The MAX31856 can be used in applications such as patient temperature monitoring, laboratory incubators, and cryogenic storage systems, providing accurate and reliable temperature data for critical medical procedures and research.
-
Scientific Research: Temperature is a fundamental parameter in many scientific experiments and studies, from materials science to environmental monitoring. The MAX31856’s high resolution and accuracy make it an ideal choice for scientific instrumentation, enabling researchers to measure temperatures with exceptional precision and gain valuable insights into thermal processes and phenomena.
By leveraging the capabilities of the MAX31856, engineers and scientists can develop more accurate, reliable, and efficient temperature measurement systems, ultimately leading to better process control, enhanced safety, and improved outcomes across a wide range of applications.
FAQ
-
What is the MAX31856?
The MAX31856 is a high-precision thermocouple-to-digital converter designed by Maxim Integrated. It offers a complete solution for thermocouple temperature measurement, combining cold-junction compensation, linearization, and high-resolution analog-to-digital conversion in a single chip. -
What thermocouple types does the MAX31856 support?
The MAX31856 supports a wide range of thermocouple types, including K, J, N, R, S, T, E, and B, making it versatile for various applications. -
How accurate is the MAX31856?
The MAX31856 features a 19-bit ADC that provides a resolution of 0.0078°C (14 bits) for temperatures ranging from -210°C to +1800°C, ensuring highly accurate temperature measurements. The internal cold-junction compensation sensor has an accuracy of ±1°C (typical) from -20°C to +85°C. -
Can the MAX31856 detect thermocouple faults?
Yes, the MAX31856 offers open-circuit and short-circuit fault detection. When a fault is detected, the converter sets the corresponding bits in the fault status register and pulls the FAULT pin low, alerting the host microcontroller to take appropriate action. -
How do I interface the MAX31856 with a microcontroller?
The MAX31856 communicates with the host microcontroller using a simple SPI interface. To set up the communication, you need to connect the MAX31856’s CS, SDI, SDO, and SCK pins to the corresponding SPI pins on the microcontroller. You can then use SPI commands to configure the MAX31856, read temperature data, and check fault status.
Conclusion
The MAX31856 is a powerful and versatile thermocouple-to-digital converter that offers high precision, ease of use, and advanced features for accurate temperature measurement. By combining cold-junction compensation, linearization, and fault detection in a single chip, the MAX31856 simplifies the design of thermocouple-based temperature monitoring systems and ensures reliable performance across a wide range of applications.
With its support for multiple thermocouple types, high-resolution ADC, and SPI interface, the MAX31856 is an ideal choice for engineers an
No responses yet