What is LGA packaging?
LGA (Land Grid Array) is a type of surface-mount packaging used for integrated circuits (ICs). In an LGA package, the IC is mounted on a substrate with an array of flat contact pads or “lands” that connect to the printed circuit board (PCB). LGA packages offer several advantages over other IC packaging types like pin grid array (PGA) and ball grid array (BGA):
- Lower profile and smaller footprint
- Better thermal and electrical performance
- Greater reliability and durability
- Flexibility in PCB mounting and interconnection
LGA packages are widely used in applications that require high density, high performance, and high reliability, such as:
- Mobile devices (smartphones, tablets, laptops)
- Telecommunications equipment
- Automotive electronics
- Industrial control systems
- Medical devices
- Military and aerospace systems
How Does LGA Packaging Work?
An LGA package consists of several key components:
- The IC die, which contains the integrated circuit
- The substrate, which is a thin PCB-like material with conductive traces
- The lands, which are flat contact pads on the bottom of the substrate
- The solder mask, which is a protective coating over the traces with openings for the lands
The IC die is attached to the top of the substrate, typically using epoxy adhesive. Wire bonds are then used to connect the die pads to the substrate traces. The lands on the bottom of the substrate are arranged in a grid pattern, with a specific pitch (distance between lands).
To mount an LGA package to a PCB, a matching pad pattern is designed on the board. Solder paste is applied to the PCB pads, and the package is placed on top using a pick-and-place machine. The assembly then goes through a reflow oven, which melts the solder and forms the electrical and mechanical connections between the lands and pads.
LGA vs. BGA and PGA
LGA packages differ from other common IC package types in the following ways:
Package | Interconnect | Profile | Pitch | Thermal Performance |
---|---|---|---|---|
LGA | Flat contact pads | Low | Fine (0.5-1.27mm) | Good |
BGA | Solder balls | Medium | Coarse (1.0-1.5mm) | Excellent |
PGA | Metal pins | High | Coarse (2.54mm) | Poor |
LGA offers a balance of benefits compared to BGA and PGA:
- Lower standoff height than BGA for slimmer designs
- Finer pitch than PGA for greater connection density
- More reliable solder joints than BGA
- Easier PCB mounting and inspection than PGA
- Better thermal dissipation than PGA
However, LGA packages also have some limitations:
- Require precise control of flatness and coplanarity
- Need specialized handling and test equipment
- Limited to relatively low pin counts (<1000)
- Not suitable for high power devices
LGA Package Design Considerations
To achieve optimal performance and reliability with LGA packaging, several design factors must be considered:
Land Pattern Design
- Land size, shape, and pitch
- Solder mask opening size
- Pad finish (ENIG, OSP, etc.)
- Trace routing and impedance control
Substrate Material Selection
- Coefficient of thermal expansion (CTE)
- Dielectric constant (Dk) and dissipation factor (Df)
- Thermal conductivity
- Mechanical strength and stiffness
Solder Paste Printing
- Stencil thickness and aperture size
- Paste type and metal content
- Print parameters (speed, pressure, separation)
- Inspection and measurement
Reflow Profile Optimization
- Peak temperature and time above liquidus (TAL)
- Ramp rates and soak times
- Cooling rate and total cycle time
- Oven type (IR, convection, vapor phase)
PCB Design Guidelines
- Via placement and size
- Copper weight and thickness
- Surface finish and solder mask
- Component placement and orientation
By carefully optimizing these design parameters, engineers can achieve high-yield, high-reliability LGA assemblies that meet the demands of modern electronic products.
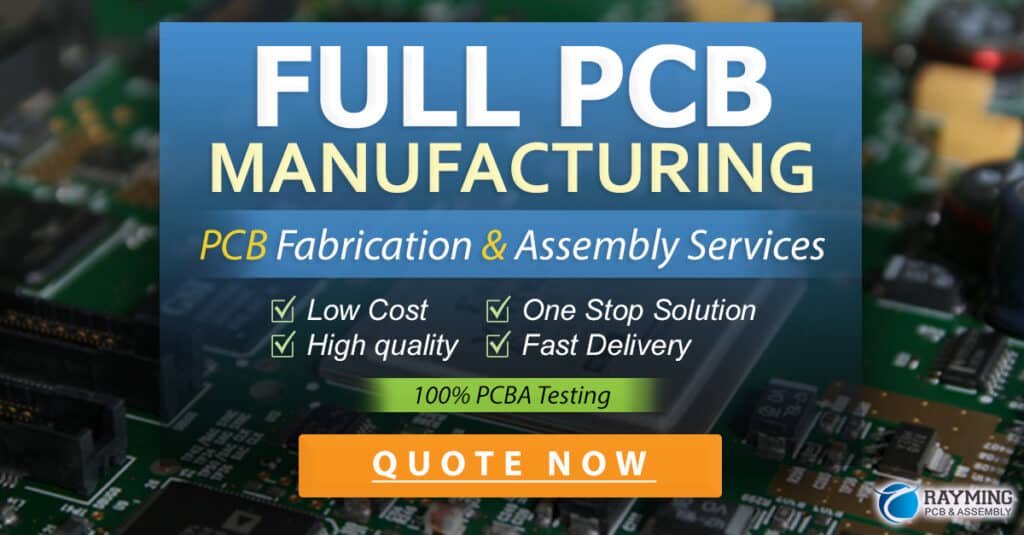
LGA Package Testing and Qualification
To ensure the quality and reliability of LGA packages, a rigorous testing and qualification process is required. This typically involves several types of tests:
Electrical Tests
- Continuity and isolation
- Signal integrity and propagation delay
- Electromagnetic compatibility (EMC)
- Electrostatic discharge (ESD) sensitivity
Mechanical Tests
- Solderability and wettability
- Shear and pull strength
- Bend and twist resistance
- Vibration and shock
Environmental Tests
- Thermal cycling and shock
- Temperature and humidity aging
- Salt spray and corrosion resistance
- Flammability and outgassing
Optical Inspection
- X-ray for joint and void detection
- Scanning acoustic microscopy (SAM) for delamination
- Confocal and electron microscopy for surface analysis
- Automated optical inspection (AOI) for dimensional measurements
The test results are used to validate the package design, assembly process, and long-term reliability under the expected use conditions. Industry standards such as IPC/JEDEC J-STD-020 and MIL-STD-810 provide guidance on test methods and acceptance criteria for LGA packages.
Future Trends in LGA Packaging
As electronic devices continue to become smaller, faster, and more complex, LGA packaging technology is evolving to meet the new challenges. Some of the key trends and innovations in LGA packaging include:
Finer Pitch and Higher Density
- Decreasing land size and spacing below 0.5mm
- Increasing pin counts above 1000
- Using multi-row and staggered land patterns
Thinner and Lighter Substrates
- Adopting low-CTE materials like coreless and glass-reinforced laminates
- Reducing substrate thickness below 0.3mm
- Integrating embedded passives and actives
Advanced Interconnect Technologies
- Implementing copper pillar bumps and micro-springs
- Exploring novel materials like anisotropic conductive adhesives
- Developing hybrid bonding methods for heterogeneous integration
3D and Modular Packaging
- Stacking multiple LGA packages vertically
- Creating package-on-package (PoP) and system-in-package (SiP) modules
- Incorporating through-silicon vias (TSVs) for vertical interconnects
By pushing the limits of LGA packaging technology, designers can enable a new generation of miniaturized, high-performance electronic products that meet the ever-increasing demands of the market.
Frequently Asked Questions (FAQ)
1. What is the main difference between LGA and BGA packages?
The main difference is in the interconnect structure. LGA packages have flat contact pads called lands, while BGA packages have spherical solder balls. LGA offers a lower profile and finer pitch than BGA, but requires more precise control of PCB flatness and coplanarity.
2. Can LGA packages be reworked or repaired?
Yes, LGA packages can be reworked using specialized heating and removal tools. However, the process is more challenging than for BGA due to the lack of self-alignment and the risk of damaging the lands or substrate. Proper care and expertise are required for successful LGA rework.
3. What is the maximum pin count for LGA packages?
Currently, most LGA packages have less than 1000 pins due to the limitations of substrate size and land pitch. However, advances in packaging technology are enabling higher pin counts, with some designs exceeding 2000 pins using multi-row or staggered land patterns.
4. How does the thermal performance of LGA compare to other package types?
LGA packages offer better thermal performance than PGA due to the larger contact area between the lands and PCB pads, which allows for more efficient heat transfer. However, BGA packages still provide the best thermal performance due to the thermal conductivity of the solder balls.
5. What are some common applications for LGA packages?
LGA packages are widely used in mobile devices, telecommunications equipment, automotive electronics, industrial control systems, medical devices, and military/aerospace applications. They are particularly well-suited for high-density, high-performance, and high-reliability applications that require a low profile and fine pitch.
No responses yet