What is an LED PCB?
An LED PCB, or Light Emitting Diode Printed Circuit Board, is a specialized type of circuit board designed to efficiently power and control LEDs. These boards are essential components in a wide range of applications, from simple indicator lights to complex lighting systems used in automotive, architectural, and entertainment industries.
LEDs have become increasingly popular due to their energy efficiency, long lifespan, and versatility compared to traditional lighting solutions. However, to function properly and reliably, LEDs require precise control over current and heat dissipation. This is where LED PCBs come into play, providing a stable and optimized platform for LEDs to operate.
Key Components of an LED PCB
- Substrate: The foundation of the PCB, typically made from FR-4 or metal-core materials.
- Copper Layers: Conductive paths that carry electrical signals and power to the LEDs.
- Solder Mask: A protective layer that covers the copper traces, preventing short circuits and oxidation.
- Silkscreen: Used for labeling and marking components on the PCB.
- LEDs: The main light-emitting components, available in various colors, sizes, and power ratings.
- Resistors: Used to limit current flow to the LEDs, protecting them from damage.
- Capacitors: Help stabilize the power supply and reduce noise.
- Connectors: Allow the LED PCB to interface with external power sources and control systems.
Benefits of Using LED PCBs
Energy Efficiency
One of the primary advantages of using LED PCBs is their energy efficiency. LEDs consume significantly less power compared to traditional lighting solutions, such as incandescent or fluorescent bulbs. This translates to lower energy costs and a reduced environmental impact.
Long Lifespan
LEDs, when properly controlled by a well-designed PCB, can last for tens of thousands of hours. This extended lifespan minimizes maintenance and replacement costs, making LED PCBs an attractive choice for long-term lighting installations.
Versatility
LED PCBs can be customized to suit a wide range of applications and design requirements. They can be manufactured in various sizes, shapes, and configurations, allowing for integration into diverse products and systems.
Improved Heat Dissipation
Heat management is crucial for the performance and longevity of LEDs. LED PCBs, especially those with metal-core substrates, are designed to efficiently dissipate heat away from the LEDs. This helps maintain optimal operating temperatures, preventing premature failure and ensuring consistent light output.
Types of LED PCBs
Single-Sided LED PCBs
Single-sided LED PCBs have conductive traces on only one side of the substrate. These boards are generally less complex and more affordable than double-sided or multi-layer PCBs. They are suitable for simpler LED applications with fewer components and connections.
Double-Sided LED PCBs
Double-sided LED PCBs feature conductive traces on both sides of the substrate, allowing for higher component density and more complex designs. These boards often incorporate through-hole vias to connect traces on opposite sides.
Multi-Layer LED PCBs
Multi-layer LED PCBs consist of three or more layers of conductive traces, separated by insulating layers. These boards offer the highest level of design flexibility and component density, making them ideal for intricate LED lighting systems with advanced features and control capabilities.
Metal-Core LED PCBs
Metal-core LED PCBs (MCPCBs) are a specialized type of board that uses a metal substrate, typically aluminum, instead of the traditional FR-4 material. The metal core provides excellent thermal conductivity, allowing for efficient heat dissipation from the LEDs. This makes MCPCBs particularly well-suited for high-power LED applications that generate significant amounts of heat.
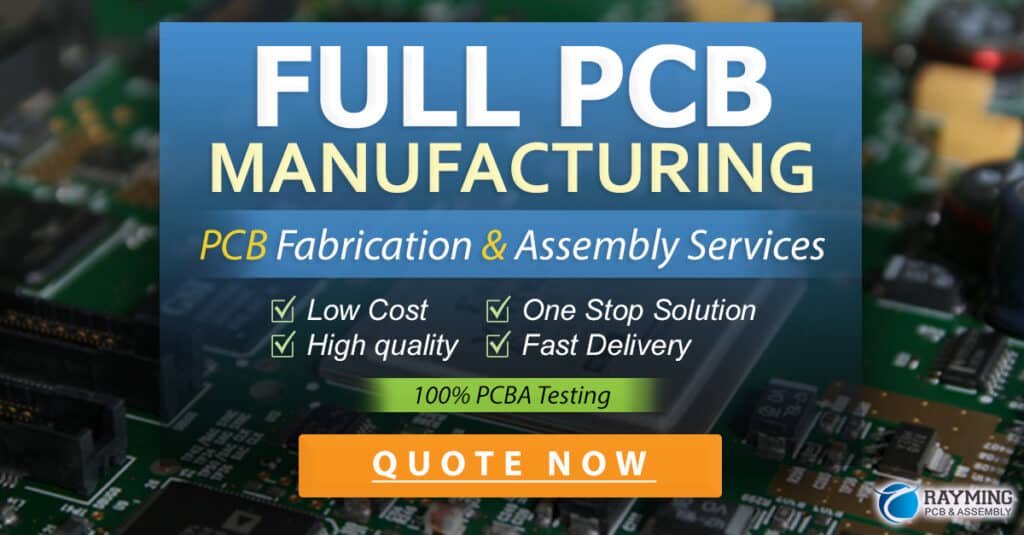
Designing LED PCBs
Designing an effective LED PCB involves several key considerations to ensure optimal performance, reliability, and cost-efficiency.
Schematic Design
The first step in designing an LED PCB is creating a schematic diagram that outlines the electrical connections between components. This includes specifying the LEDs, resistors, capacitors, and any additional control or power management circuitry.
PCB Layout
Once the schematic is finalized, the next step is to create the physical layout of the PCB. This involves arranging the components and routing the conductive traces to minimize signal interference, ensure proper grounding, and optimize thermal management.
Some key factors to consider during PCB layout include:
- Component placement for optimal heat dissipation
- Trace width and thickness to handle the required current
- Proper spacing between traces to prevent short circuits
- Ground planes and thermal vias for improved thermal performance
- Minimizing trace lengths to reduce voltage drop and signal degradation
Thermal Management
Effective thermal management is critical for LED PCBs, as excessive heat can degrade LED performance and shorten their lifespan. Designers must carefully consider the thermal properties of the PCB substrate, the placement of LEDs and other heat-generating components, and the use of thermal vias and heatsinks to dissipate heat.
Power Management
LEDs require constant current to maintain consistent brightness and color. LED PCBs must incorporate power management circuitry, such as current-limiting resistors or constant current drivers, to ensure the LEDs receive the proper current levels.
Design for Manufacturing (DFM)
To ensure the LED PCB can be efficiently and reliably manufactured, designers must adhere to DFM guidelines. This includes considerations such as minimum trace widths and spacing, hole sizes, and component placement tolerances.
Manufacturing LED PCBs
The manufacturing process for LED PCBs involves several key steps to ensure high-quality and reliable boards.
PCB Fabrication
PCB fabrication begins with the creation of the substrate, typically using FR-4 or metal-core materials. Copper layers are then laminated onto the substrate, and the conductive traces are formed through a process of etching or milling.
Next, the solder mask and silkscreen layers are applied to protect the traces and provide labeling for components.
Finally, any necessary holes or vias are drilled, and the PCB is cut to its final shape.
Component Assembly
Once the PCB is fabricated, the components, including LEDs, resistors, capacitors, and connectors, are soldered onto the board. This can be done through manual hand soldering for small-scale production or automated pick-and-place machines for larger volumes.
Testing and Quality Control
After assembly, LED PCBs undergo rigorous testing to ensure proper functionality and reliability. This may include:
- Visual inspection for defects or misaligned components
- Electrical testing to verify proper current flow and voltage levels
- Functional testing to ensure the LEDs illuminate as intended
- Thermal testing to confirm adequate heat dissipation
- Accelerated aging tests to assess long-term reliability
Boards that pass these quality control measures are then packaged and shipped to the end-user or integrated into the final product.
Applications of LED PCBs
LED PCBs find use in a wide range of industries and applications, thanks to their versatility, efficiency, and long lifespan.
Automotive Lighting
LED PCBs are increasingly used in automotive lighting applications, such as headlights, taillights, and interior lighting. They offer improved visibility, styling options, and energy efficiency compared to traditional automotive lighting solutions.
Architectural Lighting
In architectural lighting, LED PCBs enable creative and efficient lighting designs for both interior and exterior spaces. They can be used for general illumination, accent lighting, and decorative purposes, while offering significant energy savings and reduced maintenance costs.
Display Backlighting
LED PCBs are commonly used for backlighting LCD displays in devices such as smartphones, tablets, laptops, and televisions. They provide uniform, high-quality illumination while consuming minimal power.
Signage and Advertising
LED PCBs are ideal for illuminated signage and advertising displays, offering bright, eye-catching visuals with low energy consumption and long operating life.
Industrial and Safety Lighting
In industrial settings, LED PCBs provide reliable, efficient lighting for workspaces, equipment, and machinery. They are also used in safety lighting applications, such as emergency exit signs and warning lights.
Future of LED PCBs
As LED technology continues to advance, so too will the capabilities and applications of LED PCBs.
Advancements in LED Efficiency
Ongoing research and development in LED technology are yielding ever-higher levels of efficiency, with lumens per watt (lm/W) ratings consistently improving. This means future LED PCBs will be able to deliver more light output with less power consumption.
Smart Lighting and IoT Integration
The integration of LED PCBs with smart lighting systems and Internet of Things (IoT) technology is growing. This enables features such as remote control, automated dimming and color adjustment, and real-time monitoring of energy consumption. Future LED PCBs may incorporate even more advanced sensors and communication capabilities, allowing for more dynamic and adaptive lighting solutions.
Flexible and Stretchable LED PCBs
The development of flexible and stretchable LED PCBs opens up new possibilities for wearable electronics, conformable lighting, and innovative product designs. These advanced PCBs can be bent, folded, or stretched to fit unique form factors, expanding the potential applications for LED lighting.
FAQ
-
What are the main advantages of using LED PCBs over traditional lighting solutions?
LED PCBs offer several key advantages, including energy efficiency, long lifespan, versatility, and improved heat dissipation. They consume less power, last longer, and can be customized for a wide range of applications. -
What is the difference between single-sided and double-sided LED PCBs?
Single-sided LED PCBs have conductive traces on only one side of the substrate, while double-sided boards have traces on both sides. Double-sided PCBs allow for higher component density and more complex designs. -
Why is thermal management important for LED PCBs?
Proper thermal management is crucial for LED PCBs because excessive heat can degrade LED performance and shorten their lifespan. Efficient heat dissipation helps maintain optimal operating temperatures, ensuring consistent light output and reliability. -
What are metal-core LED PCBs, and when are they used?
Metal-core LED PCBs (MCPCBs) use a metal substrate, typically aluminum, instead of traditional FR-4 material. The metal core provides excellent thermal conductivity, making MCPCBs well-suited for high-power LED applications that generate significant amounts of heat. -
How can LED PCBs be integrated with smart lighting systems and the Internet of Things (IoT)?
LED PCBs can be designed to incorporate sensors, communication modules, and control circuitry that enable integration with smart lighting systems and IoT platforms. This allows for features such as remote control, automated dimming and color adjustment, and real-time monitoring of energy consumption.
In conclusion, LED PCBs are a crucial component in the rapidly growing field of LED lighting. Their energy efficiency, long lifespan, versatility, and thermal management capabilities make them an attractive choice for a wide range of applications. As LED technology continues to advance, the future of LED PCBs looks bright, with opportunities for even greater efficiency, smart lighting integration, and innovative form factors. By understanding the key aspects of LED PCB design, manufacturing, and application, engineers and manufacturers can create cutting-edge lighting solutions that meet the evolving needs of various industries and consumers.
No responses yet