What is Solder?
Solder is a metal alloy that is used to create a permanent bond between two or more metal surfaces. It is typically composed of tin (Sn) and lead (Pb) in varying proportions, along with small amounts of other elements such as silver (Ag), copper (Cu), or bismuth (Bi) to improve its properties. The most common lead-based solder alloy is Sn63Pb37, which contains 63% tin and 37% lead by weight.
Properties of an Ideal Solder
An ideal solder should possess the following properties:
1. Low melting point
2. Good wetting ability
3. Strong bond strength
4. Good electrical conductivity
5. Resistance to corrosion and oxidation
6. Ease of use and processing
7. Affordable cost
Lead Solder: Advantages and Disadvantages
Lead-based solder alloys have been the standard in the electronics industry for many decades due to their excellent properties and ease of use. However, the use of lead in solder has come under scrutiny due to its potential health and environmental hazards.
Advantages of Lead Solder
- Low melting point (183°C for Sn63Pb37)
- Excellent wetting properties
- Strong bond strength
- Good electrical conductivity
- Easy to use and process
- Relatively low cost
Disadvantages of Lead Solder
- Health hazards associated with lead exposure
- Environmental concerns due to lead contamination
- Disposal and recycling challenges
- Regulatory restrictions on the use of lead
Lead-Free Solder: Advantages and Disadvantages
In response to the growing concerns about lead, the electronics industry has been developing and adopting lead-free solder alternatives. The most common lead-free solder alloys are based on tin (Sn), silver (Ag), and copper (Cu), with varying compositions to achieve desired properties.
Advantages of Lead-Free Solder
- Reduced health and environmental hazards
- Compliance with regulatory requirements (e.g., RoHS, WEEE)
- Improved mechanical strength and reliability in some applications
- Better compatibility with certain surface finishes (e.g., immersion silver)
Disadvantages of Lead-Free Solder
- Higher melting point (217-227°C for Sn-Ag-Cu alloys)
- Poorer wetting properties compared to lead solder
- Increased risk of tin whisker growth
- Higher cost due to the use of silver and other alloying elements
- More complex processing requirements (e.g., higher soldering temperatures, stricter process control)
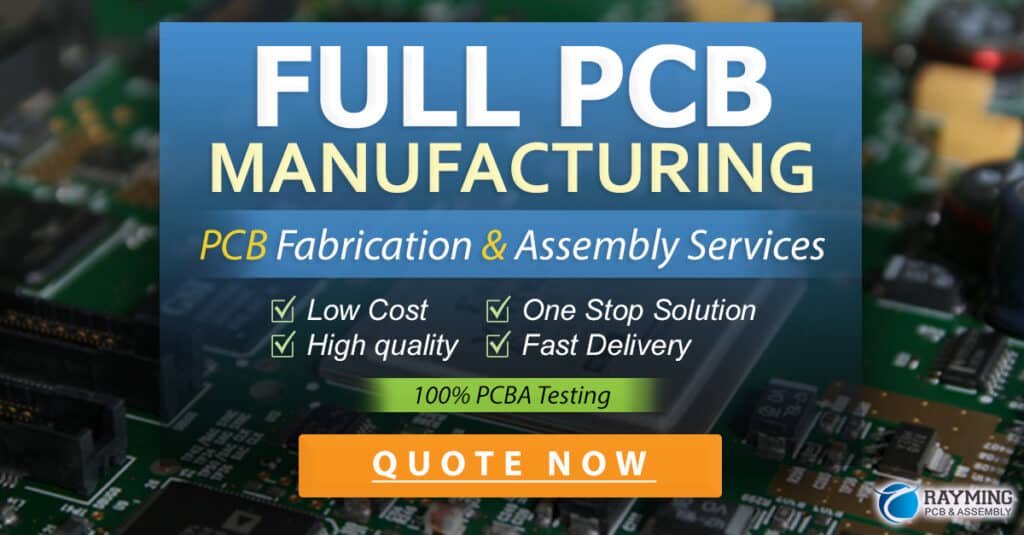
Comparison of Lead and Lead-Free Solder Properties
To better understand the differences between lead and lead-free solder, let’s compare their key properties:
Property | Lead Solder (Sn63Pb37) | Lead-Free Solder (Sn-Ag-Cu) |
---|---|---|
Melting Point | 183°C | 217-227°C |
Wetting Ability | Excellent | Good |
Bond Strength | Strong | Strong to Very Strong |
Electrical Conductivity | Good | Good |
Corrosion Resistance | Good | Good to Excellent |
Processing Complexity | Low | Moderate to High |
Cost | Low | Moderate to High |
As evident from the table, lead-free solder alloys have some advantages over lead solder in terms of mechanical strength, corrosion resistance, and environmental friendliness. However, they also have some drawbacks, such as higher melting points, poorer wetting properties, and increased processing complexity.
Tin Whisker Growth: A Concern with Lead-Free Solder
One of the major concerns associated with lead-free solder is the increased risk of tin whisker growth. Tin whiskers are thin, needle-like structures that can grow spontaneously from tin-rich surfaces, particularly in the presence of compressive stress and certain environmental conditions (e.g., temperature fluctuations, humidity).
Tin whiskers can cause short circuits, intermittent failures, and other reliability issues in electronic devices. The risk of tin whisker growth is higher in lead-free solder alloys due to the higher tin content and the absence of lead, which acts as a whisker growth inhibitor.
To mitigate the risk of tin whisker growth, various strategies have been developed, such as:
1. Using tin alloys with whisker-inhibiting elements (e.g., bismuth, indium, germanium)
2. Applying conformal coatings or encapsulants to protect the solder joints
3. Implementing stricter process controls and quality assurance measures
4. Conducting accelerated life testing and monitoring for tin whisker growth
Regulatory Requirements for Lead-Free Solder
The transition to lead-free solder in the electronics industry has been largely driven by regulatory requirements aimed at reducing the environmental impact of electronic waste. Two of the most significant regulations are the Restriction of Hazardous Substances (RoHS) Directive and the Waste Electrical and Electronic Equipment (WEEE) Directive, both implemented by the European Union.
RoHS Directive
The RoHS Directive, first introduced in 2003 and updated in 2011 (RoHS 2), restricts the use of six hazardous substances in electrical and electronic equipment, including lead. Under RoHS, the maximum allowable concentration of lead in homogeneous materials is 0.1% by weight, with some exemptions for specific applications.
WEEE Directive
The WEEE Directive, implemented in 2003 and revised in 2012, aims to promote the collection, recycling, and recovery of waste electrical and electronic equipment. It sets targets for the recovery and recycling of electronic waste and requires manufacturers to provide information on the content of hazardous substances in their products.
Many other countries and regions have adopted similar regulations, such as China RoHS, Korea RoHS, and California RoHS, further driving the global transition to lead-free solder.
Implementing Lead-Free Soldering in Electronics Manufacturing
Transitioning from lead to lead-free solder in electronics manufacturing requires careful planning, process optimization, and quality control. Some key considerations for implementing lead-free soldering include:
- Selecting the appropriate lead-free solder alloy based on the application requirements and compatibility with the components and surface finishes
- Adjusting the soldering process parameters, such as temperature profiles, dwell times, and cooling rates, to accommodate the higher melting points and different wetting behavior of lead-free solder
- Updating the manufacturing equipment and tools to handle lead-free solder, such as using compatible solder pots, tips, and fluxes
- Providing training and guidance to the manufacturing personnel on lead-free soldering techniques and best practices
- Implementing strict process controls and quality assurance measures to ensure the reliability and performance of lead-free solder joints
- Conducting thorough testing and validation of lead-free soldered assemblies, including accelerated life testing, environmental stress testing, and tin whisker growth monitoring
Frequently Asked Questions (FAQ)
1. Is lead-free solder as reliable as lead solder?
When properly implemented and controlled, lead-free solder can provide reliable and robust solder joints. However, due to the different properties and processing requirements of lead-free solder alloys, achieving the same level of reliability as lead solder may require more stringent process controls and quality assurance measures.
2. Can lead-free solder be used for all electronics applications?
Lead-free solder can be used for most electronics applications, but there are some exceptions where lead solder may still be necessary or preferred. For example, certain high-reliability applications, such as aerospace, military, or medical devices, may require the use of lead solder due to its proven reliability and the critical nature of the application.
3. How can I identify lead-free solder joints?
Lead-free solder joints typically have a duller, more matte appearance compared to the shiny, silvery appearance of lead solder joints. Additionally, lead-free solder joints may have a slightly different shape due to the different wetting behavior of lead-free solder alloys. However, the most reliable way to identify lead-free solder is through proper labeling and documentation of the soldering process and materials used.
4. Are there any health risks associated with lead-free solder?
While lead-free solder eliminates the health risks associated with lead exposure, some lead-free solder alloys may contain other elements that can pose health hazards if not handled properly. For example, some lead-free solder alloys contain silver, which can cause skin irritation or allergic reactions in some individuals. It is important to follow proper safety guidelines and use appropriate personal protective equipment when handling any type of solder.
5. How can I dispose of lead-free solder waste?
Lead-free solder waste should be disposed of in accordance with local, state, and federal regulations. In most cases, lead-free solder waste can be recycled through approved electronic waste recycling facilities. It is important to segregate lead-free solder waste from other types of waste and to properly label and store it to prevent contamination and ensure safe handling and disposal.
Conclusion
The transition from lead to lead-free solder in the electronics industry has been driven by growing concerns about the health and environmental impacts of lead, as well as regulatory requirements such as the RoHS and WEEE Directives. While lead-free solder alloys offer some advantages, such as reduced health and environmental hazards and improved mechanical strength in some applications, they also present challenges, such as higher melting points, poorer wetting properties, and increased risk of tin whisker growth.
Implementing lead-free soldering in electronics manufacturing requires careful planning, process optimization, and quality control to ensure the reliability and performance of lead-free solder joints. As the industry continues to evolve and new lead-free solder alloys and processing techniques are developed, it is crucial for manufacturers to stay informed and adapt their practices accordingly.
In conclusion, while lead-free solder may not be a perfect replacement for lead solder in all applications, it is a necessary and important step towards reducing the environmental and health impacts of electronics manufacturing. By understanding the properties, advantages, and challenges of lead-free solder and implementing best practices for lead-free soldering, manufacturers can ensure the production of reliable, high-quality, and environmentally friendly electronic products.
No responses yet