What is Solder?
Solder is a fusible metal alloy used to create a permanent bond between two or more metal surfaces. It is commonly used in electronics to join components to printed circuit boards (PCBs) and to create electrical connections. Solder typically has a lower melting point than the metals it is joining, allowing it to flow and create a strong bond without damaging the components.
Lead Solder
Lead solder, also known as tin-lead solder, has been the traditional choice for soldering in the electronics industry for decades. It typically consists of a mixture of tin and lead, with the most common composition being 63% tin and 37% lead (Sn63/Pb37).
Advantages of Lead Solder
- Lower melting point: Lead solder has a lower melting point compared to lead-free alternatives, making it easier to work with and requiring less heat to melt.
- Better wetting properties: Lead solder has excellent wetting properties, meaning it flows easily and creates a strong bond with the metal surfaces it is joining.
- Proven reliability: Lead solder has been used in the electronics industry for a long time and has a proven track record of reliability.
Disadvantages of Lead Solder
- Environmental concerns: Lead is a toxic substance that can harm the environment and human health if not disposed of properly.
- Health risks: Exposure to lead can cause serious health problems, especially for children and pregnant women.
- Regulatory restrictions: Many countries have implemented regulations restricting the use of lead in electronics due to environmental and health concerns.
Lead-Free Solder
Lead-free solder is an alternative to traditional lead solder that has gained popularity in recent years. It is made from a combination of tin, silver, and copper, with the most common composition being 96.5% tin, 3% silver, and 0.5% copper (Sn96.5/Ag3.0/Cu0.5 or SAC305).
Advantages of Lead-Free Solder
- Environmentally friendly: Lead-free solder does not contain the toxic metal lead, making it a more environmentally friendly option.
- Compliance with regulations: Using lead-free solder helps companies comply with environmental regulations and avoid potential fines or legal issues.
- Improved mechanical strength: Some lead-free solder alloys have been found to have better mechanical strength compared to lead solder.
Disadvantages of Lead-Free Solder
- Higher melting point: Lead-free solder typically has a higher melting point than lead solder, requiring higher soldering temperatures and potentially causing thermal stress on components.
- Increased cost: Lead-free solder and the associated equipment and training costs can be more expensive than traditional lead soldering.
- Learning curve: Transitioning from lead to lead-free soldering may require additional training and adjustments to soldering techniques.
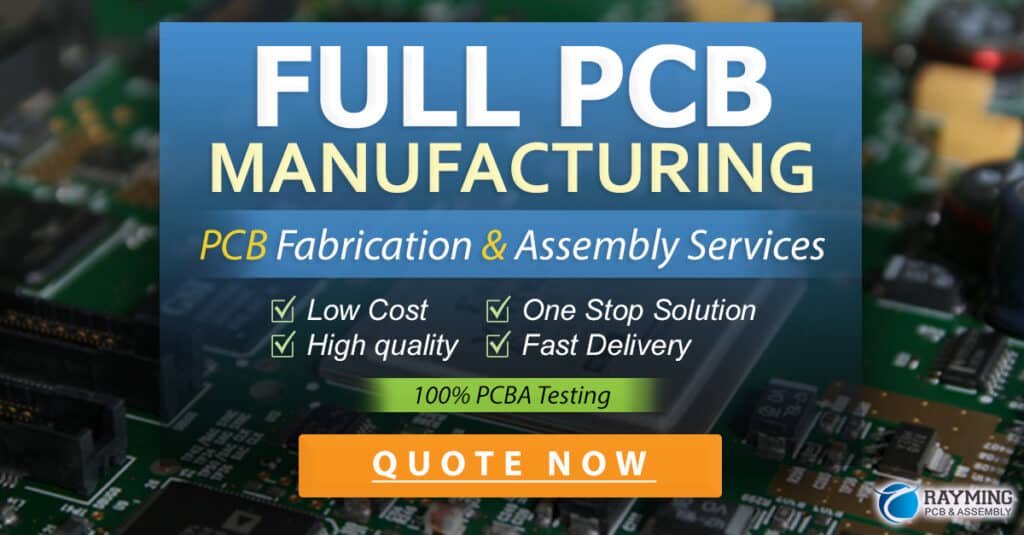
Comparison Table
Property | Lead Solder (Sn63/Pb37) | Lead-Free Solder (SAC305) |
---|---|---|
Composition | 63% Tin, 37% Lead | 96.5% Tin, 3% Silver, 0.5% Copper |
Melting Point | 183°C (361°F) | 217-220°C (423-428°F) |
Wetting Properties | Excellent | Good |
Environmental Impact | High (toxic lead content) | Low (no lead content) |
Regulatory Compliance | Non-compliant in many regions | Compliant with RoHS and other regulations |
Mechanical Strength | Good | Better than lead solder |
Cost | Lower | Higher |
Applications
Both lead and lead-free solders are used in various applications in the electronics industry. However, due to environmental regulations and health concerns, lead-free solder has become the preferred choice for many manufacturers.
Lead Solder Applications
- Older electronic equipment and devices
- Applications where lead is still permitted, such as certain aerospace and military equipment
Lead-Free Solder Applications
- Consumer electronics (smartphones, laptops, tablets, etc.)
- Automotive electronics
- Medical devices
- Telecommunications equipment
- Industrial electronics
Frequently Asked Questions (FAQ)
-
Q: Is lead solder still used in electronics?
A: While lead solder is still used in some specific applications, such as certain aerospace and military equipment, it has largely been replaced by lead-free solder in consumer electronics due to environmental regulations and health concerns. -
Q: Can I mix lead and lead-free solder?
A: Mixing lead and lead-free solder is not recommended, as it can lead to compatibility issues and potentially compromise the reliability of the solder joint. It is best to use either lead or lead-free solder consistently throughout a project. -
Q: What is the most common lead-free solder alloy?
A: The most common lead-free solder alloy is SAC305, which consists of 96.5% tin, 3% silver, and 0.5% copper. -
Q: Do I need special equipment to use lead-free solder?
A: While lead-free soldering can be done with standard soldering equipment, it may require higher soldering temperatures and adjustments to soldering techniques. Some manufacturers may choose to invest in specialized lead-free soldering equipment to ensure optimal results. -
Q: Are there any health risks associated with using lead-free solder?
A: Lead-free solder is generally considered safer than lead solder, as it does not contain the toxic metal lead. However, it is still important to follow proper safety guidelines and work in a well-ventilated area when soldering, as the fumes from any type of solder can be harmful if inhaled in large quantities.
Conclusion
In conclusion, lead-free solder has become the preferred choice for many electronics manufacturers due to environmental regulations and health concerns associated with lead exposure. While lead solder still has its advantages, such as lower melting points and excellent wetting properties, the benefits of lead-free solder, including environmental friendliness and regulatory compliance, have driven its widespread adoption.
When choosing between lead and lead-free solder, it is essential to consider factors such as the specific application, regulatory requirements, and the desired mechanical and electrical properties of the solder joint. By understanding the differences between these two types of solder and their respective advantages and disadvantages, electronics professionals can make informed decisions and ensure the reliability and safety of their soldered connections.
No responses yet