Introduction to LDI Technology
Laser Direct Imaging (LDI) is a advanced technology used in the manufacturing of printed circuit boards (PCBs). It has revolutionized the PCB fabrication process by providing higher precision, faster production speeds, and improved quality compared to traditional photolithography methods. LDI uses lasers to directly write the PCB patterns onto photoresist-coated copper clad laminates, eliminating the need for physical photomasks.
How LDI Works
The LDI process involves the following key steps:
- Photoresist Coating: The copper clad laminate is coated with a light-sensitive photoresist material.
- Direct Laser Writing: A high-precision laser beam directly writes the PCB pattern onto the photoresist layer. The laser exposes the photoresist in the desired areas, hardening it.
- Development: The unexposed photoresist is removed using a chemical developer solution, leaving behind the hardened photoresist pattern.
- Etching: The exposed copper areas are etched away using a chemical etchant, while the areas protected by the hardened photoresist remain intact.
- Photoresist Stripping: The remaining hardened photoresist is stripped off, revealing the final copper PCB pattern.
Advantages of LDI over Traditional Photolithography
LDI offers several key advantages over traditional photolithography methods in PCB manufacturing:
Higher Precision and Resolution
LDI enables the creation of PCB patterns with much higher precision and resolution compared to photolithography. The laser beam can be focused to a very small spot size, allowing for the creation of fine features and intricate designs. This is particularly important for high-density PCBs used in advanced electronic devices.
Feature | LDI | Photolithography |
---|---|---|
Minimum Line Width | 25 μm | 50 μm |
Minimum Space Width | 25 μm | 50 μm |
Registration Accuracy | ±10 μm | ±25 μm |
Faster Production Speeds
LDI eliminates the need for physical photomasks, which are time-consuming and costly to produce. With LDI, the PCB pattern can be directly written onto the photoresist layer, reducing the overall production time. This leads to faster turnaround times and increased productivity in PCB manufacturing.
Improved Quality and Reliability
LDI produces PCBs with improved quality and reliability compared to photolithography. The direct writing process minimizes the chances of defects and errors associated with physical photomasks. LDI also provides better registration accuracy, ensuring precise alignment of layers in multi-layer PCBs.
Cost Savings
While the initial investment in LDI equipment may be higher than traditional photolithography setup, LDI offers long-term cost savings. The elimination of physical photomasks reduces material costs and eliminates the need for mask maintenance and storage. LDI also reduces the need for rework and scrap, leading to overall cost savings in PCB production.
Applications of LDI in PCB Manufacturing
LDI finds applications in various segments of PCB manufacturing:
High-Density Interconnect (HDI) PCBs
HDI PCBs require fine features and high precision, making LDI an ideal choice for their fabrication. LDI enables the creation of micro-vias, fine pitch traces, and dense interconnects necessary for HDI PCB designs.
Flexible and Rigid-Flex PCBs
LDI is well-suited for the manufacturing of flexible and rigid-flex PCBs. The direct writing process allows for the creation of fine features on flexible substrates, ensuring the reliability and performance of these PCBs in applications such as wearable electronics and automotive systems.
Multilayer PCBs
LDI is extensively used in the fabrication of multilayer PCBs. The high precision and registration accuracy provided by LDI ensure precise alignment of layers, minimizing the chances of misregistration and improving the overall quality of the multilayer PCB stack.
Quick-Turn Prototyping
LDI is an excellent choice for quick-turn prototyping of PCBs. The direct writing process eliminates the need for photomask creation, reducing the lead time for prototype fabrication. This allows for faster iteration and testing of PCB designs.
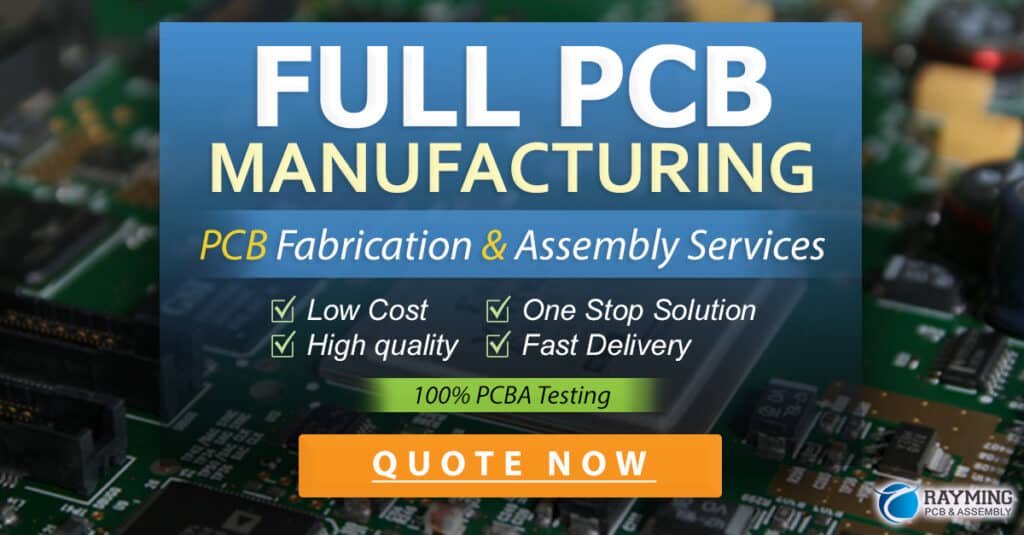
Challenges and Considerations in LDI Implementation
While LDI offers numerous benefits, there are some challenges and considerations to keep in mind when implementing LDI in PCB manufacturing:
Equipment Cost
LDI systems require a significant initial investment compared to traditional photolithography equipment. The high-precision lasers and advanced control systems used in LDI contribute to the higher cost. However, the long-term cost savings and productivity improvements often justify the investment.
Operator Training
Operating LDI equipment requires specialized skills and knowledge. Operators need to be trained in the setup, calibration, and maintenance of LDI systems. Proper training is essential to ensure optimal performance and avoid errors in the PCB fabrication process.
Photoresist Compatibility
Not all photoresist materials are compatible with LDI. The photoresist must have the appropriate sensitivity and resolution to work effectively with the laser wavelength used in LDI. Selecting the right photoresist and optimizing the process parameters are crucial for achieving the desired PCB quality.
Data Preparation
LDI requires accurate and optimized PCB design data. The design files must be properly prepared and verified to ensure smooth LDI processing. This includes checking for design rule violations, ensuring proper layer alignment, and generating the appropriate laser data files.
Future Trends and Developments in LDI
LDI technology continues to evolve and improve, driven by the increasing demands of the electronics industry. Some of the future trends and developments in LDI include:
Higher Resolution and Finer Features
As electronic devices become more compact and complex, there is a constant push for higher resolution and finer features in PCBs. LDI system manufacturers are developing lasers with smaller spot sizes and improved focusing capabilities to enable the creation of even finer PCB features.
Faster Laser Scanning Speeds
Faster laser scanning speeds are being achieved through advancements in laser technology and control systems. Higher scanning speeds translate to faster PCB production rates, further improving productivity in PCB manufacturing.
Integration with Other Manufacturing Processes
LDI is being integrated with other advanced manufacturing processes, such as additive manufacturing and 3D printing, to create innovative PCB structures and functionalities. This integration opens up new possibilities for PCB design and fabrication.
Environmentally Friendly Processes
There is a growing focus on developing environmentally friendly PCB manufacturing processes. LDI can contribute to this effort by reducing the use of chemicals and waste generation associated with traditional photolithography methods.
Frequently Asked Questions (FAQ)
-
Q: What is the minimum feature size achievable with LDI?
A: LDI can achieve minimum feature sizes as small as 25 μm, enabling the creation of high-density PCBs with fine pitch traces and micro-vias. -
Q: Can LDI be used for both rigid and flexible PCBs?
A: Yes, LDI is suitable for both rigid and flexible PCB fabrication. It can handle a variety of substrate materials, including FR-4, polyimide, and flexible laminates. -
Q: Is LDI faster than traditional photolithography?
A: Yes, LDI is generally faster than traditional photolithography. By eliminating the need for physical photomasks, LDI reduces the overall production time and improves productivity. -
Q: What are the key advantages of LDI over photolithography?
A: LDI offers several advantages, including higher precision and resolution, faster production speeds, improved quality and reliability, and cost savings through the elimination of physical photomasks. -
Q: What factors should be considered when implementing LDI in PCB manufacturing?
A: When implementing LDI, factors such as equipment cost, operator training, photoresist compatibility, and data preparation should be carefully considered to ensure successful adoption and optimal results.
Conclusion
Laser Direct Imaging (LDI) has emerged as a game-changing technology in PCB manufacturing, offering numerous benefits over traditional photolithography methods. With its high precision, faster production speeds, improved quality, and cost savings, LDI has become the preferred choice for fabricating high-density PCBs, flexible and rigid-flex PCBs, and multilayer PCBs.
As the electronics industry continues to evolve and demand more advanced PCB features, LDI technology will play a crucial role in meeting these requirements. Ongoing developments in laser technology, integration with other manufacturing processes, and a focus on environmentally friendly practices will shape the future of LDI in PCB manufacturing.
By embracing LDI technology, PCB manufacturers can enhance their capabilities, improve efficiency, and deliver high-quality PCBs to meet the ever-increasing demands of the electronics market.
No responses yet