Introduction to Land Pattern Design
Land pattern design is a crucial aspect of printed circuit board (PCB) design, as it determines the footprint of electronic components on the board. The land pattern refers to the arrangement of copper pads, solder mask openings, and other features that allow components to be soldered onto the PCB. Designing land patterns that meet industry standards is essential for ensuring the reliability, manufacturability, and functionality of electronic devices.
In this article, we will explore the key considerations and best practices for designing land patterns that adhere to industry standards. We will discuss the importance of land pattern design, the various standards and guidelines available, and the steps involved in creating optimal land patterns for different types of components.
The Importance of Land Pattern Design
Proper land pattern design is critical for several reasons:
-
Manufacturability: Well-designed land patterns ensure that components can be easily and accurately placed on the PCB during the assembly process. This reduces the risk of assembly errors and improves the overall manufacturability of the board.
-
Reliability: Correctly sized and spaced land patterns provide a strong mechanical and electrical connection between the component and the PCB. This enhances the reliability of the solder joint and minimizes the risk of component failure due to stress or vibration.
-
Signal Integrity: Appropriate land pattern design helps maintain signal integrity by minimizing parasitic capacitance, inductance, and resistance. This is particularly important for high-speed and high-frequency applications.
-
Thermal Management: Land patterns play a role in dissipating heat generated by components. Properly designed land patterns facilitate efficient heat transfer from the component to the PCB, preventing overheating and ensuring the long-term reliability of the device.
Industry Standards and Guidelines for Land Pattern Design
Several industry standards and guidelines have been developed to assist PCB designers in creating land patterns that meet the requirements of different applications and manufacturing processes. Some of the most widely recognized standards include:
- IPC-7351: Generic Requirements for Surface Mount Design and Land Pattern Standard
- IPC-SM-782: Surface Mount Design and Land Pattern Standard
- IPC-7093: Design and Assembly Process Implementation for Bottom Termination Components
These standards provide detailed specifications for land pattern dimensions, solder mask openings, and other features based on the component package type, size, and pitch. They also offer guidance on design rules, such as minimum clearances and tolerances, to ensure compatibility with standard manufacturing processes.
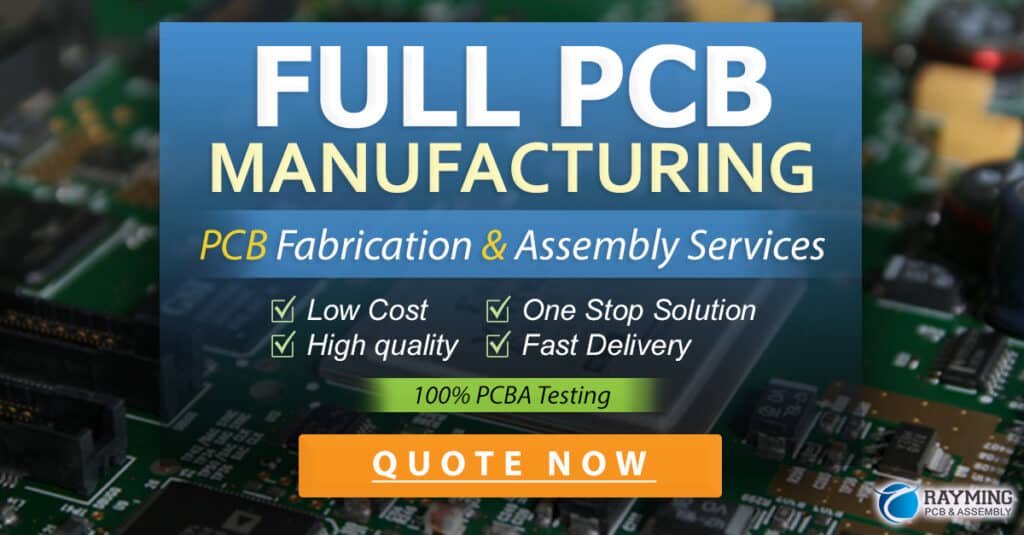
Designing Land Patterns for Different Component Types
The process of designing land patterns varies depending on the type of component being used. Here, we will discuss the key considerations for designing land patterns for some common component types.
Surface Mount Devices (SMDs)
SMDs are the most widely used type of component in modern PCB design. They are available in a variety of package types, such as chip resistors, chip capacitors, QFPs, and BGAs. When designing land patterns for SMDs, consider the following factors:
-
Package dimensions: Use the component manufacturer’s datasheet to determine the exact dimensions of the package, including the length, width, and height.
-
Pad size and spacing: Follow the recommendations provided in the relevant industry standard (e.g., IPC-7351) for pad size and spacing based on the package type and size.
-
Solder mask opening: Ensure that the solder mask opening is slightly larger than the copper pad to allow for proper solder wetting and to accommodate manufacturing tolerances.
-
Placement orientation: Consider the placement orientation of the component to minimize the impact of tombstoning and other assembly defects.
Through-Hole Components
Through-hole components, such as connectors and large capacitors, require land patterns with holes drilled through the PCB. When designing land patterns for through-hole components, keep the following points in mind:
-
Hole size: Select the appropriate hole size based on the component lead diameter and the PCB thickness. The hole should be large enough to allow for easy insertion of the lead but not so large that it compromises the mechanical strength of the solder joint.
-
Pad size: The pad size should be sufficient to provide a strong mechanical and electrical connection between the component lead and the PCB. Follow the guidelines provided in the relevant industry standard (e.g., IPC-7251) for pad size recommendations.
-
Pad shape: Circular pads are the most common choice for through-hole components, but other shapes, such as oval or rectangular pads, may be used in certain situations.
-
Solder mask opening: As with SMDs, ensure that the solder mask opening is slightly larger than the copper pad to allow for proper solder wetting and to accommodate manufacturing tolerances.
Ball Grid Arrays (BGAs)
BGAs are high-density package types that use an array of solder balls to connect the component to the PCB. Designing land patterns for BGAs requires careful consideration of the following factors:
-
Ball pitch and diameter: Use the component manufacturer’s datasheet to determine the pitch (distance between the centers of adjacent balls) and the diameter of the solder balls.
-
Pad size and spacing: Follow the recommendations provided in the relevant industry standard (e.g., IPC-7095) for pad size and spacing based on the ball pitch and diameter.
-
Solder mask opening: For BGAs, the solder mask opening is typically designed to be smaller than the copper pad to prevent solder bridging between adjacent balls.
-
Via placement: In some cases, vias may be placed within the BGA land pattern to route signals or to provide thermal relief. Follow the guidelines provided in the industry standards for via placement and design.
Design Tools and Automation
Designing land patterns manually can be a time-consuming and error-prone process, especially for complex designs with a large number of components. Fortunately, modern PCB design software tools offer features that can automate and streamline the land pattern design process. Some of these features include:
-
Land pattern libraries: Most PCB design tools include libraries of pre-defined land patterns for common component types and packages. These libraries are often based on industry standards and can be easily customized to meet specific requirements.
-
Footprint wizards: Some design tools offer footprint wizards that guide users through the process of creating custom land patterns step-by-step, ensuring that all necessary parameters are specified and that the resulting land pattern meets industry standards.
-
Design rule checks (DRC): DRC tools can automatically verify that land patterns meet the specified design rules, such as minimum clearances and solder mask openings, helping to catch errors early in the design process.
By leveraging these tools and automation features, PCB designers can create accurate, standards-compliant land patterns more efficiently, reducing design time and minimizing the risk of errors.
Best Practices for Land Pattern Design
In addition to following industry standards and guidelines, there are several best practices that PCB designers should keep in mind when creating land patterns:
-
Use consistent naming conventions: Establish a clear and consistent naming convention for land patterns to make them easier to identify and manage within the design tool and throughout the design process.
-
Consider manufacturing tolerances: When specifying land pattern dimensions, account for the tolerances of the manufacturing process to ensure that the final PCB can be reliably manufactured and assembled.
-
Optimize for assembly: Design land patterns with the assembly process in mind, considering factors such as component orientation, solder paste application, and reflow profile to minimize the risk of assembly defects.
-
Document and communicate: Clearly document the land pattern design parameters and any deviations from industry standards, and communicate this information to the manufacturing and assembly teams to ensure that everyone involved in the process is working from the same set of specifications.
By following these best practices and staying up-to-date with the latest industry standards and guidelines, PCB designers can create land patterns that are reliable, manufacturable, and optimized for the specific requirements of their designs.
Frequently Asked Questions (FAQ)
-
Q: What is the difference between a land pattern and a footprint?
A: In PCB design, the terms “land pattern” and “footprint” are often used interchangeably. However, strictly speaking, a land pattern refers to the arrangement of copper pads, solder mask openings, and other features on the PCB that allow a component to be soldered, while a footprint includes the land pattern as well as additional information such as the component outline, silkscreen markings, and keepout areas. -
Q: How do I choose the appropriate industry standard for my land pattern design?
A: The choice of industry standard depends on the specific requirements of your design, such as the component types being used, the manufacturing process, and the end-use application. In general, IPC-7351 is a good starting point for most surface mount designs, while IPC-SM-782 provides additional guidance for specific component types. For through-hole components, IPC-7251 is the most widely used standard. -
Q: Can I deviate from industry standards when designing land patterns?
A: While it is generally recommended to follow industry standards to ensure compatibility with standard manufacturing processes and to minimize the risk of assembly defects, there may be situations where deviations are necessary to meet specific design requirements. In such cases, it is important to clearly document and communicate any deviations to the manufacturing and assembly teams to ensure that they are properly accounted for in the production process. -
Q: How do I ensure that my land patterns are compatible with the manufacturing process?
A: To ensure compatibility with the manufacturing process, it is important to consider factors such as the capabilities and tolerances of the PCB fabrication and assembly equipment, the solder paste and reflow profile being used, and any specific requirements or limitations of the manufacturing facility. Communicating with the manufacturing team early in the design process and involving them in design reviews can help identify and address any potential manufacturability issues. -
Q: What are some common mistakes to avoid when designing land patterns?
A: Some common mistakes to avoid when designing land patterns include: - Failing to account for manufacturing tolerances, leading to issues with component placement and solderability
- Using incorrect or outdated component package dimensions, resulting in land patterns that do not match the actual component
- Neglecting to consider the assembly process, such as component orientation and solder paste application, leading to assembly defects
- Not properly documenting or communicating deviations from industry standards, causing confusion and potential issues in the manufacturing process
By being aware of these common pitfalls and taking steps to avoid them, PCB designers can create land patterns that are more robust, reliable, and manufacturable.
Conclusion
Land pattern design is a critical aspect of PCB design that directly impacts the reliability, manufacturability, and functionality of electronic devices. By understanding the importance of land pattern design, following industry standards and guidelines, and leveraging modern design tools and automation features, PCB designers can create land patterns that meet the specific requirements of their designs while ensuring compatibility with standard manufacturing processes.
As the electronics industry continues to evolve, with new component types and packaging technologies being introduced, it is essential for PCB designers to stay up-to-date with the latest industry standards and best practices for land pattern design. By doing so, they can create designs that are optimized for performance, reliability, and manufacturability, ultimately contributing to the success of their products in the marketplace.
Component Type | Key Considerations | Relevant Industry Standards |
---|---|---|
Surface Mount Devices (SMDs) | – Package dimensions – Pad size and spacing – Solder mask opening – Placement orientation |
– IPC-7351 – IPC-SM-782 |
Through-Hole Components | – Hole size – Pad size – Pad shape – Solder mask opening |
– IPC-7251 |
Ball Grid Arrays (BGAs) | – Ball pitch and diameter – Pad size and spacing – Solder mask opening – Via placement |
– IPC-7095 |
By addressing these key considerations and adhering to the relevant industry standards, PCB designers can create land patterns that are optimized for each component type and that meet the requirements of the manufacturing process.
No responses yet